Добавлен: 11.01.2024
Просмотров: 131
Скачиваний: 3
ВНИМАНИЕ! Если данный файл нарушает Ваши авторские права, то обязательно сообщите нам.
Первичный алюминий марки АК7 Требования к марке первичного алюминия устанавливает ГОСТ 11069-2001. Первичным алюминием называют алюминий, который получают непосредственно из ископаемого сырья – бокситов.
Первичный алюминий производят:
- в жидком виде;
- виде чушек, слитков, катанки, ленты.
Таблица 6- Химический состав алюминия АК7 согласно ГОСТ 11069 – 2001
Fe | Si | Mn | Ti | Al | Cu | Mg | Zn | Ga | Примесей | |
До 0.16 | до 0.15 | до 0.03 | до 0.01 | 99.7 | до 0.01 | до 0.02 | до 0.04 | до 0.03 | 0.02 |
Магний первичный марки МГ95 для производства сплавов, магниетермических процессов, десульфурации чугуна в качестве химического реагента и других целей.
Таблица 7- Химический состав МГ95 материала (ГОСТ 804 - 93)
Fe | Si | Mn | Ni | Al | Cu | Pb | Mg | Zn | Sn | Cl | Na | Примесей |
до 0.003 | до 0.004 | до 0.01 | до 0.001 | до 0.01 | до 0.003 | до 0.005 | 99.95 | до 0.01 | до 0.005 | до 0.005 | до 0.004 | прочие, каждая 0.01; всего 0.05 |
4.ВЫБОР ПЛАВИЛЬНОГО АГРЕГАТА И ЕГО ХАРАКТЕРИСТИКА
Электропечи сопротивления применяют на многих заводах, где производство алюминиевых сплавов приобрело достаточно широкие масштабы.
Основными технологическими преимуществами, способствующими широкому распространению этих печей, являются:
– значительное снижение угара по сравнению с печами с нефтяным или газовым обогревом;
– высокая производительность, обусловливаемая большой емкостью и мощностью;
– высокий коэффициент полезного действия (60–70 %);
– незначительное поглощение газов расплавом;
– сравнительно невысокий расход электроэнергии (450–500 квт · ч/Т);
– простота конструкции;
– облегчение условий труда рабочих;
– возможность легкой регулировки температур.
Электропечи сопротивления имеют различную емкость – от 0,5 т до 20т, благодаря чему их можно применять при различных масштабах производства.
Печи типа САТ чаще всего используются в качестве плавильных и раздаточных печей при кокильном литье. Производительность печей типа САК колеблется от 50 до 75 кг/ч. Расход электроэнергии на одну тонну алюминиевого сплава составляет 600–650 кВт·ч
Возможность создания в электропечи сухой воздушной атмосферы, от которой расплав отделен не повреждаемой окисной пленкой, служит хорошим условием предотвращения газонасыщения и окисления расплава. Следует, однако, иметь в виду влагу, присутствующую в кладке печи, или заносимую металлом шихты.
Небольшое количество водяного пара в атмосфере печи или ее кладки вызывает значительное насыщение расплава водородом. Новая кладка печи, несмотря на предварительную просушку и нагрев, долго служит источником насыщения расплава водородом и дополнительного насыщения его окисью алюминия (карбиды, корунды и прочие включения в сплавах).
В электропечах сопротивления не рекомендуется проводить плавку под флюсом из-за опасности разрушения нагревательных элементов. Поэтому они предназначены для плавки чистой высококачественной шихты: свежих чушковых металлов с добавкой лигатур, крупных очищенных отходов и чушковых вторичных сплавов. Электропечи не пригодны для переработки стружки и других мелких отходов.
Электропечи САТ-0,25 (рис.2) предназначены для переплава и перегрева алюминия и его сплавов, поддержания температуры расплавленного металла перед разливкой в формы. Они используются для плавки небольших количеств (до 250 кг) алюминиевых сплавов. Электропечь представляет собой теплоизолированную шахтную камеру, выполненную из листового проката, внутри которой установлен графитовый тигель на подставке из огнеупорной нержавеющей стали.
Футеровка многослойная – первый слой огнеупорный кирпич, второй теплоизоляционный волокнистый материал.
Три зигзагообразных нагревателя соединены в звезду и закреплены на огнеупорной кладке с помощью жаропрочных штырей. Снизу камеры предусмотрено отверстие для аварийного слива расплава. Сверху проем электропечи перекрывается двумя теплоизолированными крышками.
Для регулирования температуры в шахте печи и расплава в тигле, установлены две термопары. Управление тепловым режим электропечи осуществляется шкафом управления (рис3), в котором установлен теристорный регулятор мощности и двухканальный прибор регулирования температуры в шахте и расплаве.
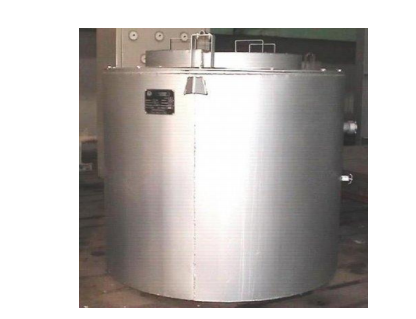
Рисунок 2- Внешний вид электропечи САТ-0,25
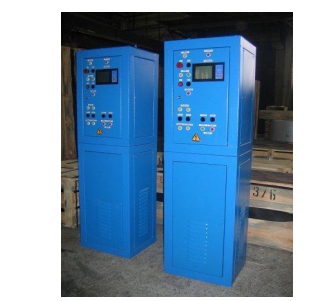
Рисунок 3 – Внешний вид шкафа управления электропечи САТ-0,25
Таблица 8- Основные технические характеристики печи САТ-0,25
№ | Наименование параметра | САТ-0,25 |
1 | Установленная мощность, кВт | 50 |
2 | Номинальная температура расплава, С | 750 |
3 | Номинальное напряжение, В: - питающей цепи; - цепей управления; - на нагревателях | 380 220 155 |
4 | Число фаз | 3 |
5 | Чистота тока, Гц | 50 |
6 | Емкость тигля ( по алюминию),тн | 0,25 |
7 | Размеры тигля (наружные), мм: - диаметр - глубина | 520 685 |
8 | Номинальная потребляемая мощность | 42 |
9 | Мощность холостого хода | 7 |
10 | Скорость плавки при плавлении и перегреве | 0,125 |
11 | Удельный расход электроэнергии (при расплавлении и перегреве до 750 ° С), кВт*ч/т | 336 |
12 | Время разогрева электропечи до установившегося режима, час | 2,5 |
13 | Масса электропечи, кг | 1100 |
14 | Масса футеровки, кг | 400 |
15 | Масса шкафа управления, кг | 118 |
5.РАСЧЕТ ШИХТОВЫХ МАТЕРИАЛОВ
В качестве шихты используем:
1.Первичный Al марки Al(АК7) ( Al -89.9%)
2.Кремний марки Кр1(Si-98%)
3. Магний первичный марки Мг95(Mg-0.3%)
Таблица 9- Угар основных элементов сплава АК7ч
Элементы | Al | Si | Mg |
Угар, % | 1,5 | 1 | 1 |
Расчет:
1.Угар по компонентам в кг составит:
Al = 93,90*1,5/100 = 1,40кг;
Si = 7,07*1/100 = 0,070кг;
Мg = 0,30*1/100 = 0,003кг;
2.Определяем состав металлической завалки:
алюминия (92,7× 100)/(100-1,5) = 93,90 кг;
кремния (7× 100)/(100-1) = 7,07 кг;
магний (0,3× 100)/(100- 1) = 0,30кг;
Определяем суммарное количество компонентов
93,90+7,07+0,30=101,27 кг
6.РАЗРАБОТКА ТЕХНОЛОГИИ ПРИГОТОВЛЕНИЯ СПЛАВА
Для получения сплава АК7ч обычно рекомендуется следующая технология. Шихтовые материалы перед загрузкой тщательно очищают от загрязнений и подогревают до 100 … 150 °С для удаления с их поверхности влаги.
Плавка алюминиево-кремнистых сплавов . Лучше всего вести плавку в индукционных печах высокой или промышленной частоты и в электрических печах сопротивления. В качестве шихтовых материалов применяют чушковые силумины, первичный алюминий и оборотный металл (до 50 % от массы шихты).
Плавку осуществляют в следующей последовательности. Печь или тигель нагревают до температуры 600-700 °С, загружают в них подогретые чушки силумина и предварительно очищенный в барабане оборотный сплав. После расплавления металл перегревают до 720-730°С, рафинируют хлористым цинком (0,1 % от массы шихты) и производят его модифицирование.
Рафинирование осуществляют путем погружения навески хлористого цинка на дно тигля с помощью «колокольчика», который медленно водят по дну тигля до полного прекращения выделения пузырьков газа. Модифицирование смесью хлористых и фтористых солей калия и натрия производят путем покрытия ими очищенной от шлака поверхности сплава и выдержки в течение 12…14 мин.
Затем соли рубят и замешивают в сплав в течение 2 мин, после чего модификатор снимают с поверхности сплава. При использовании универсальных флюсов операции рафинирования и модифицирования совмещают.
Плавка алюминиевых сплавов, содержащих магний. Во избежание насыщения сплава вредными примесями (железом и кремнием) − плавка ведется только в графитовых тиглях.
Вспомогательный инструмент (счищалка, колокольчики и др.) также изготовляется из графита или титана. В качестве шихтовых материалов применяют первичный алюминий высокой чистоты, магний и лигатуры алюминиево-бериллиевую, алюминиево-титановую, алюминиево-циркониевую и оборотный сплав соответствующей марки (до 50…60 % от массы всей шихты).
После нагрева тигля до температуры 600 °С. загружают чушки первичного алюминия и алюминиево-бериллиевую лигатуру. При температуре сплава 670-700 °С вводят лигатуры алюминий-титан и алюминий-цирконий и после полного растворения всех лигатур с помощью графитового колокольчика вводят магний. При этом необходимо следить, чтобы магний все время был погружен в сплав. После ввода магния сплав рафинируют. Затем с поверхности ванны снимают шлак, сплав тщательно перемешивают и опять снимают шлак, после чего производят разливку. На протяжении всей плавки не допускается перегрев сплава свыше 750 °С.
6.РАСЧЕТ КОЛИЧЕСТВА ТЕПЛОТЫ
Количество теплоты является энергетической характеристикой процесса теплообмена и определяется количеством энергии, которое получает или отдает система в процессе теплообмена.
Теплота – функция процесса, т.е. количество сообщенной телу теплоты зависит не только от начального и конечного состояния тела, но также от вида процесса. Элементарное количество теплоты определяется как :
dQ = C*dT, (1)
где С- теплоемкость тела в рассматриваемом процессе,
dT- малое изменение температуры тела.
Под теплотой плавления понимают количество теплоты, которое необходимо сообщить твердому кристаллическому веществу при постоянном давлении, чтобы полностью перевести его в жидкое состояние.
Количество полезного тепла, затрачиваемого на нагрев, расплавление и перегрев расплава до заданной температуры, кДж:
Qобщ. = Qраз + Qпл + Qпер(2)
Количество тепла, необходимое для разогрева сплава до температуры плавления, кДж:
Qраз = ств m(tпл - t0), (3)
где, ств – средняя теплоемкость твердого металла, Дж/(кг*0С);
m – масса металла, кг; m=1000кг;
tпл – температура плавления, tпл= 6000С;
t0 – начальная температура сплава; t0 = 200С;
ств =[(6/АMg)*0,3+(6/ASi)*7+(6/AAl)*92,7]*1000 = (6/24,30)*0,3]+(6/26,09)*7+(6/26,98)*0,92] *1000 =567 ккал/(кг*0С)
ств = 4,18*567= 2370,06Дж/(кг*0С)
Qраз= ств m(tпл - t0) = 2370,06*1000*(600-20) = 137463кДж
Количество тепла, затрачиваемого на расплавление металла, кДж