Файл: Диссертация удк 622. 692 053048. 34 Студент Группа фио подпись.docx
Добавлен: 12.01.2024
Просмотров: 252
Скачиваний: 3
ВНИМАНИЕ! Если данный файл нарушает Ваши авторские права, то обязательно сообщите нам.
СОДЕРЖАНИЕ
Определения, обозначения, сокращения, нормативные ссылки
Отсутствие или недостаток естественного света.
Отклонение параметров климата.
Механические травмы при основных видах работ.
Отсутствие или недостаток естественного света.
Отклонение параметров климата.
Механические травмы при основных видах работ.
Обоснование мероприятий по защите окружающей среды
Правовые и организационные вопросы обеспечения безопасности
-
optimization of the level of reliability of pipeline systems [4].
Economic and mathematical models of pipeline reliability are often used.
Despite the positive examples in ensuring pipeline reliability, pipelines accidents caused by various reasons still occur. Oil spills during accidents have a harmful effect on soils, surface and groundwater, on the plant and animal world. Therefore, oil pipelines are objects of high environmental risk. Each accident draws attention of the public, state bodies, mass media. The cost to eliminate the consequences is high and, obviously, will grow in the future. That is why, it is extremely important to minimize the likelihood of emergencies and their consequences.
Pipeline damage is caused by two groups of factors. The first group is associated with a reduction in the bearing capacity of the pipeline, the second - with the increase in pressures and load.
The reduction in the carrying capacity of the pipeline is due to the presence of defects in the wall of the pipes and the aging of the metal. Defects of pipes are usually divided into four groups: metallurgical, technological, construction and operation. Defects of metallurgical origin occur in metal smelting, sheet rolling and welding of pipes and pipelines. These defects include nonmetallic inclusions (sulphides, oxides, nitrides, etc.), fissures, burns, stratification, etc. Technological defects are formed during the manufacture of sheet material and pipes. These defects include shells, Sunsets, burns, edge misalignments, dents, cracks in the seam and the weld zone, defects in welds, deviation of the geometric dimensions of the weld, as well as burrs, longitudinal risks, grooves on the outer surface, scratches most characteristic
for seamless trusses Ub. During construction and repair, defects of mechanical damage are formed, and in pipline operation – defects associated with corrosion (solid corrosion, corrosive ulcers, pitting and intergranular corrosion). Mechanical damages of the pipe wall are scratches, risks, dents, corrugations, etc. [3].
| | | | | Приложение А | Лист |
| | | | | 104 | |
Изм. | Лист | № докум. | Подпись | Дата |
Factors of the second group appear in the operation of the existing pipeline. In the course of pipeline operation, there are a number of power factors. These include internal pressure, stress caused by the temperature of the transported oil and the

Any discrepancy between the controlled parameter of the material quality and products to regulated norms can be considered as a defect. The need to ensure the reliability and safety of oil pipelines requires the timely elimination of these defects [3].
Underground steel pipelines are prone to corrosion. Underground pipelines can corrode under the influence of soil, stray currents and alternating current electrified transportation. Pipeline corrosion is a difficult problem related to the pipeline reliability and safety.
The results of the failure analysis indicate that one of the main causes of damage to underground pipelines is the impact of external forces, resulting in the formation of surface dents, cracks, cracks in dents, ruptures in welds and along the body of the pipe. External loads acting on the underground pipelines include any possible loads caused by various works near the pipeline, heavy traffic, landslides, earthquakes, explosions, etc. The most common damage is caused by repair or construction work in the immediate vicinity of the existing pipeline; they are among the potentially most dangerous ones [3]. More than 5% of accidents from the total number of
accidents take place due to external impacts on domestic pipelines.
The failure analysis of the pipeline indicates that the share of failures caused by the infringement of pipeline operation and maintenance norms ranges from2 to 7
%. This includes failures caused by the fault of operating personnel in connection with the violation of terms of maintenance and repairs, improper maintenance and repair of oil pipelines, etc. The external loads include hydraulic impact. Hydraulic impact, as a rule, occurs due to the improper pipeline operation, and presents a great danger to oil pipelines.
| | | | | Приложение А | Лист |
| | | | | 105 | |
Изм. | Лист | № докум. | Подпись | Дата |
The pipeline damage caused by failures due to operational reasons varies greatly. The large-scale damage is associated with oil pipeline disruptions due to
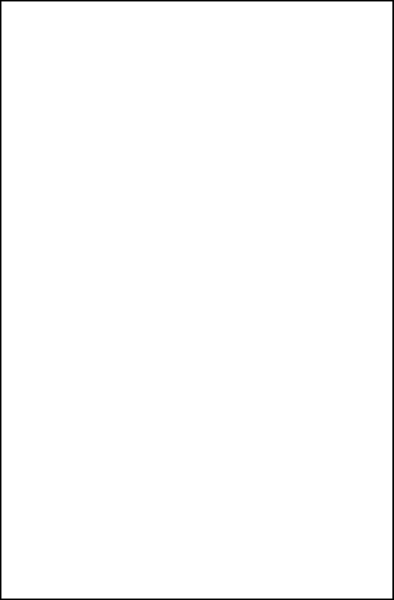
The main operating loads and impacts are internal product pressure in the pipeline and a temperature difference (difference between the temperatures of the metal pipe during installation and in service). In accordance with the rules of technical operation, during normal operation of the pipelines the internal pressure does not change significantly. There are quite effective methods to select materials, equipment and designs of oil pipelines subjected to internal pressure. The issue concerning temperature differential is more complicated. The influence of this parameter on the stress-strain state (SSS) of the pipeline depends on many factors.
The change in the temperature of the transported oil or oil product has a great influence on the strength of the pipeline. Thus, for example, when the metal temperature of the pipe decreases by 1 ° C, the tensile longitudinal stresses in the metal of the pipes increase by 2.5 MPa. When large longitudinal compressive forces occur in the pipeline, the conditions for the deformation of the pipe material change, the longitudinal-transverse bends of the pipeline in the ground are altered, and sometimes the backfilling breaks down and a complete loss of longitudinal stability of the pipeline occurs, accompanied by a sharp increase in deflections and collapse of the pipes.
Longitudinal forces change the working conditions of the pipe material, located in a complex stress state, which contributes to developing new and growing old cracks, therefore, it is expected that the bearing capacity of the pipeline is reduced. The research on strength of pipelines in conditions of compressive forces shows that longitudinal forces affect the bearing capacity of the pipeline in all stages of destruction: the formation of the fractures, the development of plastic deformation (when the viscous destruction) and crack propagation (by brittle fracture).
| | | | | Приложение А | Лист |
| | | | | 106 | |
Изм. | Лист | № докум. | Подпись | Дата |
The level and nature of the changes in the stress-strain state basically depend on reliable and safe operation of pipelines [3]. Excessively high stresses acting on the pipeline, as well as reducing the bearing capacity of the structure, lead to damage and
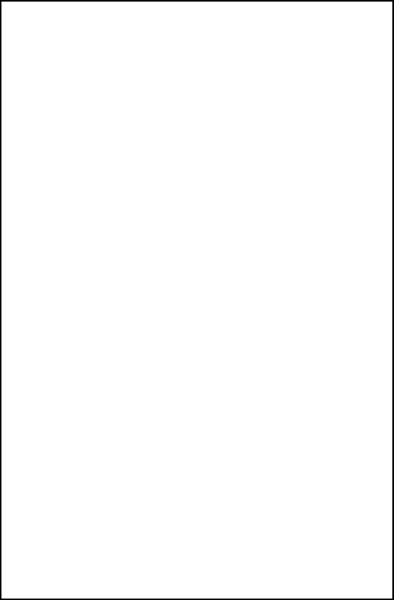
The studies carried out by a number of authors show that during the long (20 years or more) operation of oil pipelines, the characteristics of the metal of the pipes change (in the direction of deterioration). Mechanical tests of pipe samples cut from the dismantled pipes revealed that during long operation of 17GS, 14HGS, 19G steels, the plastic properties of steel are significantly reduced [3]. Metal in the process of long-term operation embrittles, the toughness significantly reduces (for steel 19G, the parameter decreases by half). As the operating pressure increases, the diameter of the pipes increases, the service life of the pipeline increases, the metal becomes more prone to embrittlement. Such fractures can occur even at normal values of circumferential stresses, which are 30-50% of the yield point, i.e. in the obviously elastic area of the metal pipeline.
In addition, the change in pipe metal temperature leads to the following phenomenon. When the temperature changes in the underground pipeline, there is shear stress at the contact of pipeline with soil. This leads to damage to the insulation of the pipeline. As a result of breaking the protective coating, the exposed sections of the pipeline become subjected to corrosion.
| | | | | Приложение А | Лист |
| | | | | 107 | |
Изм. | Лист | № докум. | Подпись | Дата |
The bends, loops, pipeline units are the pipeline sections that are subjected to the most intensive loads. Bypass, pump stations and heating devices, onshore oil pipeline units are also intensively stressed. [3]. The analysis of accidents occurring on oil pipelines shows that in a number of accidents are caused by the insufficient reliability of tees, receiving and launching pig traps. The cause of damage is most often a combination of insufficient strength of tee connections and excessive (due to temperature fluctuations and uneven sediment) stresses in ground units.