Файл: Конспект лекций по учебной дисциплине Материаловедение.doc
ВУЗ: Не указан
Категория: Не указан
Дисциплина: Не указана
Добавлен: 01.12.2023
Просмотров: 712
Скачиваний: 3
ВНИМАНИЕ! Если данный файл нарушает Ваши авторские права, то обязательно сообщите нам.
механический кривошипный штамповочный пресс, имеющий разъемную матрицу, одна часть которой является подвижной – зажимной.
Кроме главного деформирующего ползуна, имеется ползун, движение которого перпендикулярно движению главного.
Горизонтально-ковочные машины выбираются по номинальному усилию, которое составляет 1…31,5 МН.
Схема горячей объемной штамповки на горизонтально-ковочной машине показана на рис. 14.4.
Рис. 14.4. Схема горячей объемной штамповки на горизонтально-ковочной машине
Штамп состоит из трех частей: неподвижной матрицы 3, подвижной матрицы 5 и пуансона 1, размыкающихся в двух взаимно перпендикулярных плоскостях. Пруток 4 с нагретым участком на его конце закладывают в неподвижную матрицу. Положение конца прутка определяется упором 2. При включении машины подвижная матрица 5 прижимает пруток к неподвижной матрице, упор автоматически отходит в сторону, и только после этого пуансон 1 соприкасается с выступающей частью прутка и деформирует ее. Металл при этом заполняет формующую полость, расположенную впереди зажимной части. Формующая полость может находиться только в матрице, только в пуансоне, а также в матрице и пуансоне.
После окончания деформирования пуансон движется в обратном направлении, выходя из полости матрицы. Матрицы разжимаются, деформированную заготовку вынимают или она выпадает из них.
Штамповка выполняется за несколько переходов в отдельных ручьях, оси которых расположены одна над другой. Каждый переход осуществляется за один рабочий ход ползуна. Осуществляются операции: высадка, прошивка, пробивка. За один переход можно высадить выступающий из зажимной части матрицы конец прутка только в том случае, если его длина не превышает трех диаметров. При большей длине возможен изгиб заготовки, поэтому предварительно необходимо произвести набор металла. Набор металла осуществляется в полости пуансона, которой придают коническую форму.
В качестве исходной заготовки используют пруток круглого или квадратного сечения, трубный прокат. Штампуют поковки: стержни с утолщениями и глухими отверстиями, кольца, трубчатые детали со сквозными и глухими отверстиями.
Так как штамп состоит из трех частей , то напуски на поковки и штамповочные уклоны малы или отсутствуют.
К недостаткам горизонтально-ковочных машин следует отнести их малую универсальность и высокую стоимость.
Ротационные способы изготовления поковок
В основе этих способов лежит процесс ротационного обжатия при вращении инструмента или заготовки. При обкатывании инструментом заготовки очаг деформации имеет локальный характер и постоянно перемещается по заготовке, вследствие чего усилие, действующее на инструмент, меньше чем при штамповке. Это позволяет изготовлять поковки большой массы (заготовка вагонных осей) с большой точностью, так как упругие деформации при меньших усилиях меньше.
Штамповка на ковочных вальцах напоминает продольную прокатку, на двух валках закрепляют секторные штампы, имеющие соответствующие ручьи (рис. 14. 5.а).
Рис.14.5. Схемы действия ковочных вальцов (а), ротационно-ковочной машины (б), станов поперечно-клиновой прокатки (в); раскатки (г)
Нагретую заготовку 1 подают до упора 2, когда секторные штампы 3 расходятся. При повороте валков происходит захват заготовки и обжатие ее по форме полости; одновременно с обжатием заготовка выталкивается в сторону подачи.
На вальцах изготовляют поковки типа звеньев цепей, рычагов, гаечных ключей и т.п., а также осуществляют фасонирование заготовок. Исходное сечение заготовки принимают равным максимальному сечению поковки, так как при вальцовке происходит главным образом протяжка.
Штамповка на ротационно-ковочных машинах подобна операции протяжки и заключается в местном обжатии заготовки по периметру (рис. 14.5.б). Заготовку 1 в виде прутка или трубы помещают в отверстие между бойками 5 машины, находящимися в шпинделе 4. Бойки могут свободно скользить в радиально расположенных пазах шпинделя. При вращении шпинделя ролики 3, помещенные в обойме 2, толкают бойки 5, которые наносят удары по заготовке. В исходное положение бойки возвращаются под действием центробежных сил. В машинах этого типа получают поковки, имеющие форму тел вращения. Существуют машины, у которых вместо шпинделя с бойками вращается обойма с роликами; в этом случае для возвратного движения ползунов служат пружины. В таких машинах получают поковки квадратного, прямоугольного и других сечений.
Поперечно-клиновой прокаткой (рис.14.5.в) получают заготовки валов и осей с резкими ступенчатыми переходами диаметром от 12 до 120 мм. Деформирование может осуществляться инструментом в виде двух валков, валка и сегмента или двух плоских плит. Плоско-клиновой инструмент наиболее прост и обеспечивает получение валов сложной конфигурации с высокой точностью. Заготовка 2 из круглого прокатанного прутка после нагрева автоматически перемещается в рабочую зону клиньев 1 в их исходном положении. Клиновой инструмент, закрепленный в подвижной салазке станка, совершает прямолинейное движение. Заготовка прокатывается между двумя клиновыми плитами.
Раскатка кольцевых заготовок на раскатных станах получила особенно большое распространение при производстве колец подшипников. Схема процесса показана на рис. 14.5.г. Заготовка 1 представляет собой кольцо с меньшим диаметром и большей толщиной стенки, чем у поковки. Заготовки получают штамповкой на молотах или горизонтально-ковочных машинах. При подведении к заготовке 1, надетой на валок 2, быстро вращающегося валка 3 заготовка и валок 2 начинают вращаться. При дальнейшем сближении валков 2 и 3 увеличивается наружный диаметр заготовки за счет уменьшения толщины и происходит ее контакт с направляющим роликом 4, обеспечивающим получение правильной кольцевой формы поковки. После касания поковкой контрольного ролика 5 раскатка прекращается.
Раскаткой получают поковки колец с поперечными сечениями различной формы наружным диаметром 70…700 мм и шириной 20…180 мм.
Штамповка жидкого металла
Штамповка жидкого металла является одним из прогрессивных технологических процессов, позволяющих получать плотные заготовки с уменьшенными пропусками на механическую обработку, с высокими физико-механическими и эксплуатационными свойствами.
Технологический процесс штамповки жидкого металла объединяет в себе процессы литья и горячей объемной штамповки.
Процесс заключается в том, что расплав, залитый в матрицу пресс-формы, уплотняют пуансоном, закрепленным на ползуне гидравлического пресса, до окончания затвердевания.
Сопряжение пуансона и матрицы образует закрытую фасонную полость. Наружные контуры заготовки получают разъемной формой, если деталь имеет наружные выступы, или неразъемной формой – при отсутствии выступов. Внутренние полости образуются внедрением пуансона в жидкий металл.
После извлечения из пресс-формы заготовку подвергают различным видам обработки или используют без последующей обработки.
Под действием высокого давления и быстрого охлаждения газы, растворенные в расплаве, остаются в твердом растворе. Все усадочные пустоты заполняются незатвердевшим расплавом, в результате чего заготовки получаются плотными, с мелкокристаллическим строением, что позволяет изготавливать детали, работающие под гидравлическим давлением.
Этим способом можно получить сложные заготовки с различными фасонными приливами на наружной поверхности, значительно выходящими за пределы основных габаритных размеров детали. В заготовках могут быть получены отверстия, расположенные не только вдоль движения пуансона, но и в перпендикулярном направлении.
Возможно запрессовывать в заготовки металлическую и неметаллическую арматуру.
Процесс используется для получения фасонных заготовок из чистых металлов и сплавов на основе магния, алюминия, меди, цинка, а также из черных металлов.
ЛЕКЦИЯ
Холодная штамповка
Холодная штамповка производится в штампах без нагрева заготовок и сопровождается деформационным упрочнением металла.
Холодная штамповка является одним из наиболее прогрессивных методов получения высококачественных заготовок небольших и точных из стали и цветных металлов. Она обеспечивает достаточно высокую точность и малую шероховатость поверхности при малых отходах металла и низкой трудоемкости и себестоимости изготовления изделий. Возможность осуществления холодной штамповки и качество заготовок определяются качеством исходного материала. Большое значение имеет подготовка поверхности заготовок: удаление окалины, загрязнений и поверхностных дефектов.
Процессы холодной штамповки часто выполняют за несколько технологических переходов, постепенно приближая форму и размеры заготовок к форме и размерам готовых изделий и осуществляя промежуточный отжиг для снятия наклепа и восстановления пластических свойств металла. В зависимости от характера деформирования и конструкции штампов холодную штамповку делят на объемную и листовую.
Объемная холодная штамповка
Холодную объемную штамповку выполняют на прессах или специальных холодноштамповочных автоматах. Основными ее разновидностями являются: высадка, выдавливание, объемная формовка, чеканка.
Высадка – образование на заготовке местных утолщений требуемой формы в результате осадки ее конца (рис. 15.1).
Рис.15.1. Схема высадки
Заготовкой обычно служит холоднотянутый материал в виде проволоки или прутка из черных или цветных металлов. Высадкой изготавливают стандартные и специальные крепежные изделия, кулачки, валы-шестерни, детали электронной аппаратуры, электрические контакты и т.д.
Длина высаживаемой части рассчитывается с учетом объема требуемого утолщения по формуле: .
Расчет числа переходов производится в основном по соотношению длины высаживаемой части и диаметра заготовки , которое характеризует устойчивость к продольному изгибу. При используют один переход, при – два перехода, при – три перехода. При большом количестве переходов происходит упрочнение металла, поэтому требуется отжиг.
Последовательность переходов изготовления деталей показана на рис. 15.2.: за три перехода (рис. 15.2.а); за пять переходов (рис. 15.2.б).
Рис.15.2. Последовательность переходов изготовления детали
Высадка осуществляется на прессах, горизонтально-ковочных машинах, автоматических линиях, оснащенных холодновысадочными пресс-автоматами.
Выдавливание – формообразование сплошных или полых изделий, благодаря пластическому течению металла из замкнутого объема через отверстия соответствующей формы.
Особенностью процесса является образование в очаге деформации схемы трехосного неравномерного сжатия, повышающего технологическую пластичность материала.
Различают прямое, обратное, боковое и комбинированное выдавливание (рис. 15.3).
При прямом выдавливании металл течет из матрицы 2 в направлении, совпадающем с направлением движения пуансона 1 (рис.15.3.а, 15.3.б). Этим способом можно получить детали типа стержня с утолщением, трубки с фланцем, стакана с фланцем.
При обратном выдавливании металл течет в направлении, противоположном направлению движения пуансона, в кольцевой зазор между пуансоном и матрицей для получения полых деталей с дном (рис. 15.3.в) или в полый пуансон для получения деталей типа стержня с фланцем (рис. 15.3.г).
Кроме главного деформирующего ползуна, имеется ползун, движение которого перпендикулярно движению главного.
Горизонтально-ковочные машины выбираются по номинальному усилию, которое составляет 1…31,5 МН.
Схема горячей объемной штамповки на горизонтально-ковочной машине показана на рис. 14.4.
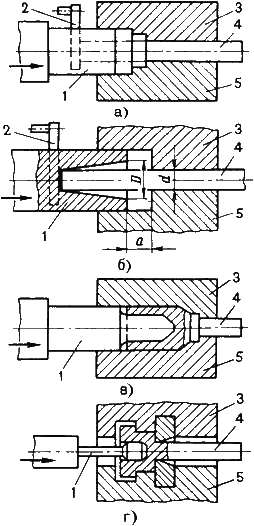
Рис. 14.4. Схема горячей объемной штамповки на горизонтально-ковочной машине
Штамп состоит из трех частей: неподвижной матрицы 3, подвижной матрицы 5 и пуансона 1, размыкающихся в двух взаимно перпендикулярных плоскостях. Пруток 4 с нагретым участком на его конце закладывают в неподвижную матрицу. Положение конца прутка определяется упором 2. При включении машины подвижная матрица 5 прижимает пруток к неподвижной матрице, упор автоматически отходит в сторону, и только после этого пуансон 1 соприкасается с выступающей частью прутка и деформирует ее. Металл при этом заполняет формующую полость, расположенную впереди зажимной части. Формующая полость может находиться только в матрице, только в пуансоне, а также в матрице и пуансоне.
После окончания деформирования пуансон движется в обратном направлении, выходя из полости матрицы. Матрицы разжимаются, деформированную заготовку вынимают или она выпадает из них.
Штамповка выполняется за несколько переходов в отдельных ручьях, оси которых расположены одна над другой. Каждый переход осуществляется за один рабочий ход ползуна. Осуществляются операции: высадка, прошивка, пробивка. За один переход можно высадить выступающий из зажимной части матрицы конец прутка только в том случае, если его длина не превышает трех диаметров. При большей длине возможен изгиб заготовки, поэтому предварительно необходимо произвести набор металла. Набор металла осуществляется в полости пуансона, которой придают коническую форму.
В качестве исходной заготовки используют пруток круглого или квадратного сечения, трубный прокат. Штампуют поковки: стержни с утолщениями и глухими отверстиями, кольца, трубчатые детали со сквозными и глухими отверстиями.
Так как штамп состоит из трех частей , то напуски на поковки и штамповочные уклоны малы или отсутствуют.
К недостаткам горизонтально-ковочных машин следует отнести их малую универсальность и высокую стоимость.
Ротационные способы изготовления поковок
В основе этих способов лежит процесс ротационного обжатия при вращении инструмента или заготовки. При обкатывании инструментом заготовки очаг деформации имеет локальный характер и постоянно перемещается по заготовке, вследствие чего усилие, действующее на инструмент, меньше чем при штамповке. Это позволяет изготовлять поковки большой массы (заготовка вагонных осей) с большой точностью, так как упругие деформации при меньших усилиях меньше.
Штамповка на ковочных вальцах напоминает продольную прокатку, на двух валках закрепляют секторные штампы, имеющие соответствующие ручьи (рис. 14. 5.а).
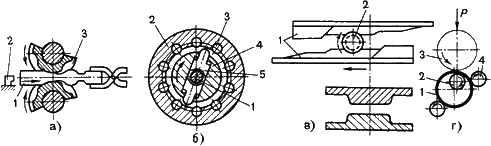
Рис.14.5. Схемы действия ковочных вальцов (а), ротационно-ковочной машины (б), станов поперечно-клиновой прокатки (в); раскатки (г)
Нагретую заготовку 1 подают до упора 2, когда секторные штампы 3 расходятся. При повороте валков происходит захват заготовки и обжатие ее по форме полости; одновременно с обжатием заготовка выталкивается в сторону подачи.
На вальцах изготовляют поковки типа звеньев цепей, рычагов, гаечных ключей и т.п., а также осуществляют фасонирование заготовок. Исходное сечение заготовки принимают равным максимальному сечению поковки, так как при вальцовке происходит главным образом протяжка.
Штамповка на ротационно-ковочных машинах подобна операции протяжки и заключается в местном обжатии заготовки по периметру (рис. 14.5.б). Заготовку 1 в виде прутка или трубы помещают в отверстие между бойками 5 машины, находящимися в шпинделе 4. Бойки могут свободно скользить в радиально расположенных пазах шпинделя. При вращении шпинделя ролики 3, помещенные в обойме 2, толкают бойки 5, которые наносят удары по заготовке. В исходное положение бойки возвращаются под действием центробежных сил. В машинах этого типа получают поковки, имеющие форму тел вращения. Существуют машины, у которых вместо шпинделя с бойками вращается обойма с роликами; в этом случае для возвратного движения ползунов служат пружины. В таких машинах получают поковки квадратного, прямоугольного и других сечений.
Поперечно-клиновой прокаткой (рис.14.5.в) получают заготовки валов и осей с резкими ступенчатыми переходами диаметром от 12 до 120 мм. Деформирование может осуществляться инструментом в виде двух валков, валка и сегмента или двух плоских плит. Плоско-клиновой инструмент наиболее прост и обеспечивает получение валов сложной конфигурации с высокой точностью. Заготовка 2 из круглого прокатанного прутка после нагрева автоматически перемещается в рабочую зону клиньев 1 в их исходном положении. Клиновой инструмент, закрепленный в подвижной салазке станка, совершает прямолинейное движение. Заготовка прокатывается между двумя клиновыми плитами.
Раскатка кольцевых заготовок на раскатных станах получила особенно большое распространение при производстве колец подшипников. Схема процесса показана на рис. 14.5.г. Заготовка 1 представляет собой кольцо с меньшим диаметром и большей толщиной стенки, чем у поковки. Заготовки получают штамповкой на молотах или горизонтально-ковочных машинах. При подведении к заготовке 1, надетой на валок 2, быстро вращающегося валка 3 заготовка и валок 2 начинают вращаться. При дальнейшем сближении валков 2 и 3 увеличивается наружный диаметр заготовки за счет уменьшения толщины и происходит ее контакт с направляющим роликом 4, обеспечивающим получение правильной кольцевой формы поковки. После касания поковкой контрольного ролика 5 раскатка прекращается.
Раскаткой получают поковки колец с поперечными сечениями различной формы наружным диаметром 70…700 мм и шириной 20…180 мм.
Штамповка жидкого металла
Штамповка жидкого металла является одним из прогрессивных технологических процессов, позволяющих получать плотные заготовки с уменьшенными пропусками на механическую обработку, с высокими физико-механическими и эксплуатационными свойствами.
Технологический процесс штамповки жидкого металла объединяет в себе процессы литья и горячей объемной штамповки.
Процесс заключается в том, что расплав, залитый в матрицу пресс-формы, уплотняют пуансоном, закрепленным на ползуне гидравлического пресса, до окончания затвердевания.
Сопряжение пуансона и матрицы образует закрытую фасонную полость. Наружные контуры заготовки получают разъемной формой, если деталь имеет наружные выступы, или неразъемной формой – при отсутствии выступов. Внутренние полости образуются внедрением пуансона в жидкий металл.
После извлечения из пресс-формы заготовку подвергают различным видам обработки или используют без последующей обработки.
Под действием высокого давления и быстрого охлаждения газы, растворенные в расплаве, остаются в твердом растворе. Все усадочные пустоты заполняются незатвердевшим расплавом, в результате чего заготовки получаются плотными, с мелкокристаллическим строением, что позволяет изготавливать детали, работающие под гидравлическим давлением.
Этим способом можно получить сложные заготовки с различными фасонными приливами на наружной поверхности, значительно выходящими за пределы основных габаритных размеров детали. В заготовках могут быть получены отверстия, расположенные не только вдоль движения пуансона, но и в перпендикулярном направлении.
Возможно запрессовывать в заготовки металлическую и неметаллическую арматуру.
Процесс используется для получения фасонных заготовок из чистых металлов и сплавов на основе магния, алюминия, меди, цинка, а также из черных металлов.
ЛЕКЦИЯ
Холодная штамповка
Холодная штамповка производится в штампах без нагрева заготовок и сопровождается деформационным упрочнением металла.
Холодная штамповка является одним из наиболее прогрессивных методов получения высококачественных заготовок небольших и точных из стали и цветных металлов. Она обеспечивает достаточно высокую точность и малую шероховатость поверхности при малых отходах металла и низкой трудоемкости и себестоимости изготовления изделий. Возможность осуществления холодной штамповки и качество заготовок определяются качеством исходного материала. Большое значение имеет подготовка поверхности заготовок: удаление окалины, загрязнений и поверхностных дефектов.
Процессы холодной штамповки часто выполняют за несколько технологических переходов, постепенно приближая форму и размеры заготовок к форме и размерам готовых изделий и осуществляя промежуточный отжиг для снятия наклепа и восстановления пластических свойств металла. В зависимости от характера деформирования и конструкции штампов холодную штамповку делят на объемную и листовую.
Объемная холодная штамповка
Холодную объемную штамповку выполняют на прессах или специальных холодноштамповочных автоматах. Основными ее разновидностями являются: высадка, выдавливание, объемная формовка, чеканка.
Высадка – образование на заготовке местных утолщений требуемой формы в результате осадки ее конца (рис. 15.1).
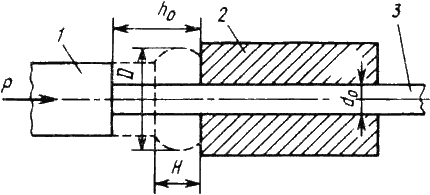
Рис.15.1. Схема высадки
Заготовкой обычно служит холоднотянутый материал в виде проволоки или прутка из черных или цветных металлов. Высадкой изготавливают стандартные и специальные крепежные изделия, кулачки, валы-шестерни, детали электронной аппаратуры, электрические контакты и т.д.
Длина высаживаемой части рассчитывается с учетом объема требуемого утолщения по формуле: .
Расчет числа переходов производится в основном по соотношению длины высаживаемой части и диаметра заготовки , которое характеризует устойчивость к продольному изгибу. При используют один переход, при – два перехода, при – три перехода. При большом количестве переходов происходит упрочнение металла, поэтому требуется отжиг.
Последовательность переходов изготовления деталей показана на рис. 15.2.: за три перехода (рис. 15.2.а); за пять переходов (рис. 15.2.б).
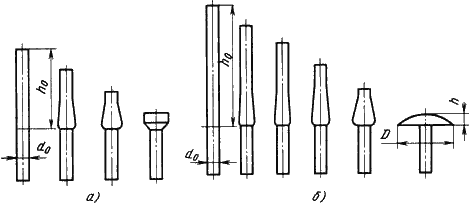
Рис.15.2. Последовательность переходов изготовления детали
Высадка осуществляется на прессах, горизонтально-ковочных машинах, автоматических линиях, оснащенных холодновысадочными пресс-автоматами.
Выдавливание – формообразование сплошных или полых изделий, благодаря пластическому течению металла из замкнутого объема через отверстия соответствующей формы.
Особенностью процесса является образование в очаге деформации схемы трехосного неравномерного сжатия, повышающего технологическую пластичность материала.
Различают прямое, обратное, боковое и комбинированное выдавливание (рис. 15.3).
При прямом выдавливании металл течет из матрицы 2 в направлении, совпадающем с направлением движения пуансона 1 (рис.15.3.а, 15.3.б). Этим способом можно получить детали типа стержня с утолщением, трубки с фланцем, стакана с фланцем.
При обратном выдавливании металл течет в направлении, противоположном направлению движения пуансона, в кольцевой зазор между пуансоном и матрицей для получения полых деталей с дном (рис. 15.3.в) или в полый пуансон для получения деталей типа стержня с фланцем (рис. 15.3.г).