Файл: 1. 2 Основные виды металлорежущих станков 8 6 Требования к электрооборудованию 14.docx
Добавлен: 06.11.2023
Просмотров: 184
Скачиваний: 4
ВНИМАНИЕ! Если данный файл нарушает Ваши авторские права, то обязательно сообщите нам.
У большей части специальных станков частота (скорость) вращения шпинделя неизменна.
Привод с шестеренной коробкой скоростей в настоящее время является наиболее распространенным типом привода главного движения в металлорежущих станках.
Их достоинством являются компактность, удобство в управлении и надежность в работе.
Недостатки приводов с шестеренными коробками скоростей заключаются в невозможности бесступенчатого регулирования скорости, а также в сравнительно низком к. п. д. на высоких частотах вращения в случае широкого диапазона регулирования.
1.3 Классификация
Станки классифицируются по множеству признаков:
По классу точности металлорежущие станки классифицируются на пять классов:
-
(Н) Нормальной точности -
(П) Повышенной точности -
(В) Высокой точности -
(А) Особо высокой точности -
(С) Особо точные станки (прецизионные) с погрешностью 1 мкм.
Классификация металлорежущих станков по массе:
-
лёгкие (< 1 т) -
средние (1-10 т) -
тяжёлые (>10 т) -
уникальные (>100 т)
Классификация металлорежущих станков по степени автоматизации:
-
ручные -
полуавтоматы -
автоматы -
станки с ЧПУ -
гибкие производственные системы
Классификация металлорежущих станков по степени специализации:
-универсальные-для изготовления широкой номенклатуры деталей малыми партиями.
Используются в единичном и серийном производстве. Также используют при ремонтных работах.
-специализированные-для изготовления больших партий деталей одного типа. Используются в среднем и крупносерийном производстве
-специальные-для изготовления одной детали или детали одного типоразмера.
Используются в крупносерийном и массовом производстве.
1.4 Формообразующие движения
Для осуществления процесса резания на металлорежущих станках необходимо обеспечить взаимосвязь формообразующих движений.
У металлорежущего станка имеется привод (механический, гидравлический, пневматический), с помощью которого обеспечивается передача движения рабочим органам: шпинделю, суппорту и т.п.
Комплекс этих движений называется формообразующими движениями.
Их классифицируют на два вида:
1) Основные движения (рабочие), которые предназначены непосредственно для осуществления процесса резания:
а) Главное движение Dг осуществляется с максимальной скоростью.
Может передаваться как заготовке (например, в токарных станках), так и инструменту (напр., в сверлильных, шлифовальных, фрезерных станках).
Характер движения: вращательный или поступательный.
Характеризуется скоростью — v (м/с).
б) Движение подачи Ds осуществляется с меньшей скоростью и так же может передаваться и заготовке и инструменту.
Характер движения: вращательный, круговой, поступательный, прерывистый.
Виды подач:
-подача на ход, на двойной ход Sx. (мм/ход), Sдв.х. (мм/дв.ход);
-подача на зуб Sz (мм/зуб);
-подача на оборот So (мм/оборот);
-минутная подача Sm (мм/мин).
2) Вспомогательные движения способствуют осуществлению процесса резания, но не участвуют в нём непосредственно.
Виды вспомогательных движений:
-наладка станка;
-задача режимов резания;
-установка ограничителей хода в соответствии с размерами и конфигурациями заготовок;
-управление станком в процессе работы;
-установка заготовки, снятие готовой детали;
-установка и смена инструмента и прочие.
1.5 Характерные особенности станка
Основные узлы станка: станина, передняя (шпиндельная) бабка с коробкой скоростей и шпинделем, суппорт, задняя бабка, коробка подач, фартук и шкаф с электрооборудованием.
Станина является основной несущей конструкцией станка.
По направляющим станины перемещается нижняя каретка суппорта, а также задняя бабка.
Шпиндель представляет собой полый вал, через который можно пропускать прутковый материал при обработке его на станке.
На шпиндель навертывается патрон либо планшайба для закрепления обрабатываемого изделия, а также может устанавливаться передний центр при обработке изделия в центрах.
Суппорт служит для закрепления режущего инструмента (резца) и сообщения ему движений подачи:
продольной и поперечной.
Фартук соединен с нижней кареткой суппорта й перемещается вместе с ней вдоль станины.
Движение суппорту передается через механизм фартука от ходового вала, либо от ходового винта, которые получают вращение от коробки подач.
Ходовой винт используется при нарезании резьб, ходовой вал - при всех других видах обработки.
Задняя бабка используется как вторая опора при обработке в центрах сравнительно длинных изделий.
Она имеет выдвижную пиноль, в которой закрепляется задний центр или режущий инструмент для обработки отверстий - сверла, метчики, развертки и др.
Технологические возможности станков могут быть расширены применением делительной головки, накладного круглого стола.
Основные узлы станка:
-станина;
-передняя бабка;
-коробка скоростей;
-шпиндель;
-суппорт;
-задняя бабка;
-коробка подач;
-фартук;
-шкаф с электрооборудованием.
Основные технические данные и характеристики
Наименование параметра | Единица измерения | Величина параметра | |
Главный привод | усилие резания | Н | 500 |
| скорость резания | м/мин | 18 |
Привод электронасоса подачи охлаждающей жидкости | напор | м | 1,2 |
| подача насоса | м 3/с | 0,15 |
Привод каретки | момент | Н м | 6,5 |
| частота вращ. | об/мин | 1500 |
1.6 Требования к электрооборудованию
Главный привод, а также привод каретки и привод насоса охлаждения осуществляются от асинхронного двигателя с короткозамкнутым ротором.
В механических цехах машиностроительных заводов токарно-винторезные станки используются в условиях индивидуального и мелкосерийного производства.
Питание силовой цепи будет осуществляться от сети 380 В.
В целях повышения надежности работы аппаратов, в схеме управления будем использовать напряжение 110 В, для местного освещения - 24 В и для цепей сигнализации - 36 В.
Для этого используем понижающий трансформатор ОСВМ - 1-380/110/36/24.
Электрические аппараты должны соответствовать следующим требованиям: изоляция электрических аппаратов должна быть рассчитана в зависимости от условий возможных перенапряжений, которые могут возникнуть в процессе работы.
Аппараты, предназначенные для частого включения и отключения, должны иметь высокую механическую и электрическую износоустойчивость, а температура токоведущих элементов не должна превышать допустимых значений.
При коротком замыкании токоведущая часть аппарата подвергается значительным термическим и динамическим нагрузкам, которые вызваны большим током.
Эти нагрузки не должны препятствовать дальнейшей работе аппарата.
Установка электродвигателей и аппаратов должна осуществляться таким образом, чтобы они были доступны для осмотра, замены и ремонта.
Электродвигатели должны быть заземлены или занулены в соответствии с требованиями ПУЭ.
На коммутационных аппаратах, пускорегулирующих устройствах, предохранителях и т. п. должны быть надписи, указывающие, к какому электродвигателю они относятся.
Перед началом работы необходимо убедиться; что все автоматические включатели включены.
Пуск электродвигателя главного привода М 1 осуществляется нажатием кнопки SB1 или SB2, которая замыкает цепь катушки контактора КМ 1, переводя его на самопитание.
Остановка электродвигателя главного приводе М 1осуществляется нажатием кнопки SB3 или SB4.
Управление вращением шпинделя осуществляется рукояткой включения фрикциона.
При отключенном фрикционе (шпиндель не вращается) замыкается размыкаемый контакт конечного выключателя QSи включаются реле временя КТ 1, тормознаямуфта YA5. При этом загорается сигнальная лампа HL2.
При работе двигателя главного привода на холостом ходу реле времени КТ, настроенное на выдержку времени 2,5…3 мин., отключает двигатель посредством контактов КТ.
Одновременно реле времени КТ 1 потеряет питание и с выдержкой времени 25 с отключает тормозную муфту YA5.
При включенном фрикционе контакт QS размыкается, отключает реле времена КТ и тормозную муфту YA5.
При отключении двигателя М 1 кнопкой SB3 или SB4 посредством размыкаемого контакта КМ 1 включается реле времени КТ и тормозная муфта YA5.
Контроль за нагрузкой электродвигателя главного привода осуществляется по амперметру.
Рабочие подача суппорта осуществляются от двигателя главного привода, быстрые перемещения - двигателя быстрого хода.
В фартуке станка имеются четыре электромагнитные муфты, две из которых используются для управления перемещением каретки в продольном направлении, две - для управления перемещением суппорта в поперечном направлении.
Управление муфтами производится рукояткой постового переключателя, имеющего пять положений: 1 - вертикальное нейтральное и четыре наклонных, соответствующих направлению перемещения каретки и суппорта.
Включение электродвигателя быстрого хода при любом положении рукоятки переключателя обеспечивается толчковой кнопкой, встроенной в головку крестового переключателя.
Во избежание одновременного включения меточной гайки и электромагнитных муфт предусмотрен конечный выключатель QS1, установленный внутри фартука, который обрывает цепь питания муфт при включении маточной гайки.
Для предотвращения пробоя катушек электромагнитных муфт при их отключении и уменьшении искрообразования на контактах крестового переключателя предусмотрены разрядные сопротивления.
На фартуке установлен переключатель SA2 на три положения, который включает электромагнитные муфты на требуемый режим работы.
2.1 Шлифовальный станоки
Шлифовальные станки применяются в основном для снижения шероховатости обрабатываемых деталей и получения точных размеров.
Основной инструмент при шлифовании – шлифовальный круг.
На шлифовальных станках можно обрабатывать наружные и внутренние цилиндрические, конические и фасонные поверхности и плоскости, разрезать заготовки, шлифовать резьбу и зубья зубчатых колёс, затачивать режущий инструмент и т.д.
Шлифовальные станки в зависимости от назначения подразделяются на кругло шлифовальные, внутришлифовальные, без центра шлифовальные, плоскошлифовальные и специальные.
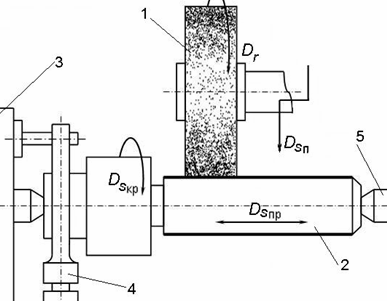
Шлифовочный станок
Круглое шлифование:
1 – шлифовальный круг;
2 – заготовка;
3 – поводковый патрон;
4 – хомутик;
5 – задний центр.
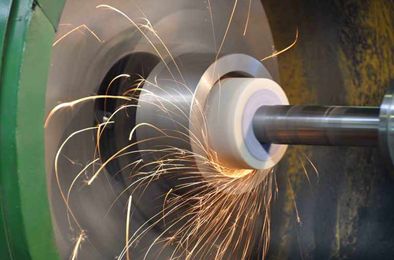
Внутреннее шлифование
Внутреннее шлифование применяют для окончательной обработки отверстий закаленных деталей или в тех случаях, когда невозможно применить другие, более производительные методы обработки.
Осуществляется на внутришлифовальных станках напроход или методом врезания (короткие отверстия)
Внутреннее