Файл: Введение. Цели переработки тги. Цели переработки тги.docx
ВУЗ: Не указан
Категория: Не указан
Дисциплина: Не указана
Добавлен: 07.11.2023
Просмотров: 33
Скачиваний: 1
ВНИМАНИЕ! Если данный файл нарушает Ваши авторские права, то обязательно сообщите нам.
Введение. Цели переработки ТГИ.
Цели переработки ТГИ:
-
Превращение ТГИ в облагороженное твёрдое топливо и углеродные восстановители; -
Получение из ТГИ высококалорийных горючих газов и смеси органических веществ; -
Получение из ТГИ твёрдых асфальтоподобных продуктов, используемых в качестве сырья в производстве строительных и углеграфитных материалов; -
Приготовление из ТГИ жидких и газообразных топлив близких по свойствам нефти и природному газу; -
Комплексное использование энергетического и химического потенциала ТГИ для решения экологических задач.
Данные цели достигаются при использовании определённых групп использовании определённых групп технологических процессов:
-
Термическая переработка без доступа воздуха при температурах 550-1100. При этом происходит расщепление органической массы ТГИ и рекомбинация продуктов расщепления с получением термодинамически стабильных веществ (твёрдый остаток, смола и газ). По конечной температуре нагрева различают:
-
Низкотемпературное коксование (полукоксование) при температурах 500-550;
-
Среднетемпературное коксование при температурах 650-750;
-
Высокотемпературное коксование при температурах 900-1100.
-
Газификация ТГИ – высокотемпературный процесс взаимодействия газифицирующих агентов (воздух, кислород, водяной пар) с органической массы ТГИ. При температурах 800-1200. Основная часть органической массы ТГИ превращается в газы (H2, CH4, CO).
-
Гидрогенизация – сочетания низкотемпературного термического расщепления ТГИ с каталитическим гидрированием продуктов термической деструкции ТГИ. -
Экстракция – термическое растворение ТГИ органическими растворителями с целью получения облагороженных беззольных органических веществ.
Все методы переработки ТГИ можно классифицировать по группам:
-
Механические (дробление, брикетирование, гранулирование, классификация с получением заданного состава, обогащение); -
Термохимические (сушка, бертенирование, все виды коксования); -
Химические и каталитические процессы (гидрогенизация, улавливание и переработка парогазовых продуктов, экстракция и термическое растворение ТГИ).
Технология переработки ТГИ имеет основные стадии (переделы):
-
Подготовка ТГИ к переработки (обогащение, дробление, классификация, сушка, брикетирование, омасливание ТГИ); -
Основной передел состоит из стадий и операций, характерных для конкретного технологического процесса; -
Улавливание примесей из образующегося газа; -
Переработка жидких продуктов – это очистка сточных вод, утилизация твёрдых отходов.
Подготовка ТГИ к переработке.
1.Приём и складирование ТГИ.
Углеподготовительный цех осуществляет приём, хранение, усреднение углей по маркам или технологическим группам, дробление, грохочение, дозирование угля для получения шихты – смесь угля разных марок, смешение готовой шихты.
Склад выполняет две функции:
-
Буферная ёмкость между поставщиком и потребителем; -
Усреднение показателей качества угля во времени.
К – коэффициент усреднения:
К > 1 – лучшее усреднение;
К = 1 – отсутствует усреднение;
К < 1 – ухудшение качества шихты.
Вместимость склада зависит:
-
От расстояния между поставщиком и потребителем; -
От суточной потребности в угле; -
От ритмичности поставок; -
От требуемой степени усреднения; -
От допустимого срока хранения.
Нормы запаса углей на складе:
Расстояние, км | <150 | 150-300 | 300-1000 | 1000-2000 | >2000 |
Запас, сутки | 4 | 6 | 10 | 15 | 20 |
Эксплуатируются 2 типа складов:
-
Открытые (напольные); -
Закрытые (бункерные).
Склад открытого типа сооружается на специально подготовленной открытой площадке разделённой на участки (поля) для складирования углей по отдельным группам поставщиков. Для каждой группы угля отводится два поля: 1 – для закладки штабеля угля; 2 – для забора и выдачи угля на производство.
Склад закрытого типа состоит из одного или более рядов железо-бетонных бункеров вместимостью 2500т каждый. Бункер цилиндрически-конической формы с диаметром 13м и высотой 35м.
Усреднение угля.
На открытом складе наиболее эффективное усреднение – укладка штабеля тонкими горизонтальными слоями, что достигается движением тележки вдоль штабеля с малым раскрытием грейфера, а при заборе угля на производство в вертикальном пересечении всех слоёв угля.
K =

На закрытом складе усреднение осуществляется за счёт одновременной выдачи угля каждой марки из нескольких бункеров. Уголь на конвейере укладывается слоями, чем больше работающих бункеров, тем лучше (больше) усреднение.
K =

Выгрузка угля на складах осуществляется в вагоноопрокидывателя (ВСР):




Недостатки и преимущества складов:
У открытого склада (недостатки):
-
Большие площади; -
Большая стоимость и громоздкость углеперегружателей; -
Воздействие атмосферных осадков; -
Пыль.
У закрытого склада (недостатки):
-
Ограниченная вместимость; -
Высокая стоимость; -
Трудная ликвидация очагов самовозгорания.
У закрытого склада (преимущества):
-
Компактность; -
Полная механизация; -
Использование склада как дозировочного отделения; -
Защищённость от осадков; -
Отсутствие потерь угля при перезагрузочных работах; -
Борьба со смерзаемостью углей.
В зимнее время при перевозке угля влажностью больше 8%, уголь смерзается (образуется корка 100-200мм, примерзает к дну и стенкам вагона). Для устранения принимают следующие мероприятия:
-
Подсушка и транспортирование угля с влажностью до 7%; -
Добавление органических веществ к углю в количестве 0,3-0,5% от массы угля (нефтяные масла); -
Использование гаражей размораживания.
2. Механическая переработка ТГИ.
-
Грохочение – разделение сыпучих материалов с помощью одного или нескольких сит. Материал не прошедший сито называют надрешёточный, а прошедший – подрешёточный. Шкала грохочения – последовательный ряд абсолютных значений величин смежных сит: 100,80,60,40,20 мм – стандартная шкала.
Эффективность грохочения (КПД):
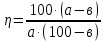
а и в – содержание подрешёточного продукта в исходном и надрешёточном продукте, %.
Производительность грохота зависит от влажности материала, от формы зёрен и отверстия сит, от угла наклона грохота, от скорости движения ТГИ по грохоту.






Распространены три типа поверхностей грохота:
-
Стальные перфорированные листы (решета); -
Проволочные сетки < 10мм; -
Колосниковые решетки (отверстия > 80мм).
Отверстия в просеявшейся поверхности могут иметь форму: квадратную, прямоугольную, овальную, круглую, щелевидную.
В зависимости от способов выделения материалов определённого класса по крупности различны.
Три схемы грохочения:
-
От крупного к мелкому; -
От мелкого к крупному; -
Комбинированная.
В
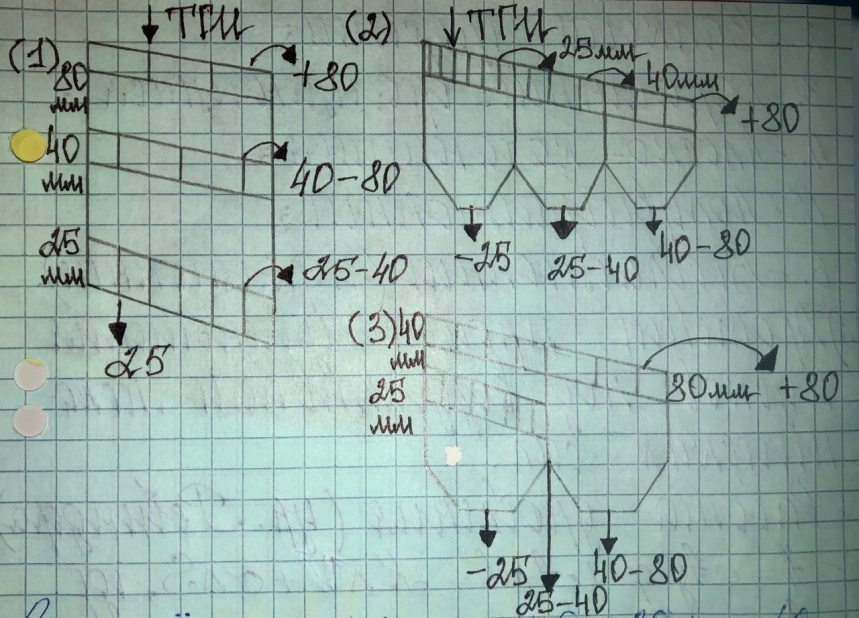
Грохоты по конструкции делят на 6 типов:
-
Неподвижные колосниковые решетки; -
Валковые грохоты; -
Барабанные вращающиеся; -
Плоско-качающиеся; -
Полувибрационные; -
Вибрационные (гирационные).
-
Дробление – процесс уменьшения кусков под воздействием механических сил.
Работа дробления (уравнение Ребиндера):






Схемы дробления делят на:
-
Открытые: однократное прохождение ТГИ через дробилку. -
Закрытые: параллельное или последовательное расположение агрегатов.

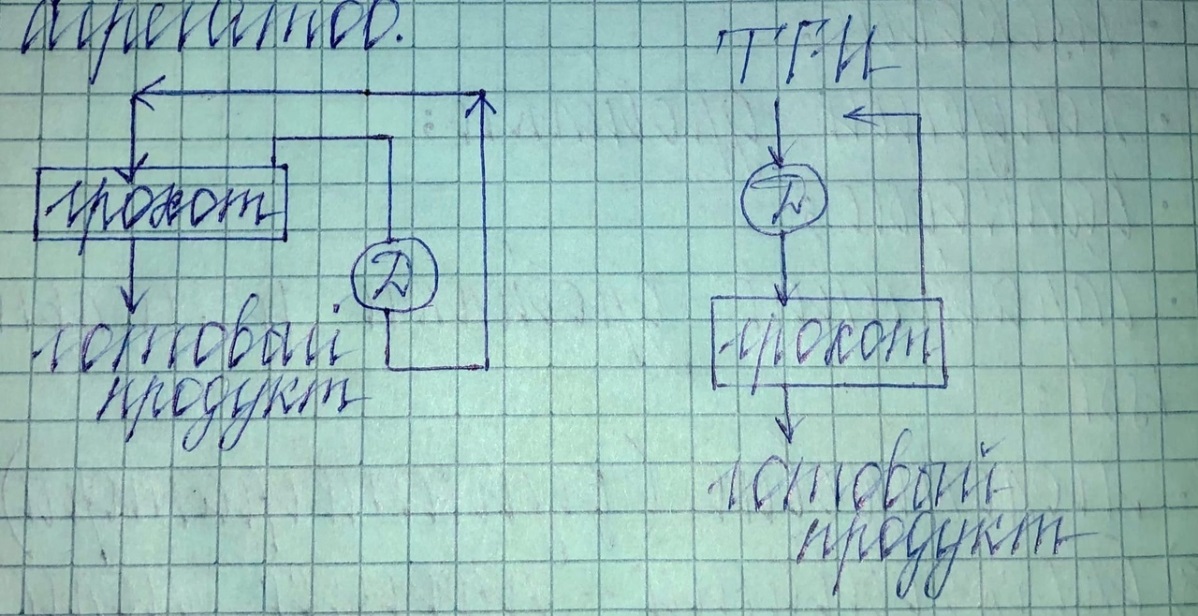
Процесс дробления в зависимости от крупности дробленого продукта делят на 3 вида:
-
Крупное от 1500-300 до 350-100 мм; -
Среднее от 350-100 до 100-40 мм; -
Мелкое от 100-40 до 30-5 мм; < 5 мм – измельчение.
Способы дробления: раздавливание, раскалывание, истирание, удар.
Дробильные аппараты делят на 5 основных типов: щековые, конусные дробилки, валковые, барабанные дробилки и мельницы, молотковые дробилки (дезинтеграторы).
-
Окусковывание – процесс получения брикетов или гранул нужной формы и крупности из ТГИ мелких классов.
Используют два способа брикетирования:
-
Со связующим. Брикетируют каменный уголь в качестве связующего используют нефтяные битумы, каменноугольные смолы и пеки. -
Без связующим. Брикетируются торф и бурый уголь.
Для брикетирования используют прессы: вальцовые, штемпельные, кольцевые.