Файл: 1. Назначение, устройство, принцип работы Назначение.docx
ВУЗ: Не указан
Категория: Не указан
Дисциплина: Не указана
Добавлен: 08.11.2023
Просмотров: 83
Скачиваний: 2
ВНИМАНИЕ! Если данный файл нарушает Ваши авторские права, то обязательно сообщите нам.
-
Ослабив затяжку хомута, снимаем шланг вентиляции картера с патрубка блока цилиндров.
2. Ключом на 10 мм отворачиваем два болта крепления подводящей трубы к блоку цилиндров и отсоединяем ее от блока.
Замечание.
Соединение уплотнено прокладкой
3. Снимаем датчик детонации
4. Снимаем датчик положения коленчатого вала
5. Снимаем насос охлаждающей жидкости
6. Снимаем стартер
7. Снимаем генератор
Снимаем зубчатый шкив привода распределительного вала
Замечание
На 16-клапанных двигателях отсоединяем нижнюю штангу крепления двигателя от поперечины передней подвески, торцовым ключом на 17 мм отворачиваем три болта крепления нижнего кронштейна генератора и снимаем кронштейн в сборе со штангой
8. Устанавливаем регулируемый упор под коробку передач и подвешиваем блок цилиндров к подъемному устройству или устанавливаем регулируемый упор под блок цилиндров. Слегка приподнимаем блок цилиндров, разгружая опоры силового агрегата.
9. Снимаем нижнюю крышку картера сцепления и отворачиваем болты крепления коробки передач к блоку цилиндров.
10. Отворачиваем верхнюю гайку болта подушки правой опоры .
11. Торцовым ключом на 13 мм отворачиваем три болта крепления кронштейна правой опоры двигателя к блоку цилиндров.
15. Снимаем кронштейн опоры двигателя в сборе с верхним кронштейном крепления генератора.
16. Торцовым ключом на 15 мм под правым передним крылом автомобиля отворачиваем три болта крепления кронштейна опоры к правому лонжерону.
17. Снимаем кронштейн вместе с правой опорой силового агрегата.
18. Слегка покачивая блок цилиндров, отсоединяем его от коробки передач и вынимаем из моторного отсека.
19. Снимаем маховик
20. Торцовым ключом на 10 мм отворачиваем шесть болтов крепления держателя заднего сальника коленчатого вала и снимаем его.
Замечание
Под держателем установлена прокладка, которую при сборке необходимо заменить.
21. Снимаем масляный насос
22. Торцовым ключом на 17 мм отворачиваем по два болта крепления пяти крышек коренных подшипников.
23. Снимаем крышки коренных подшипников.
24. Вынимаем из крышек нижние вкладыши коренных подшипников.
25. Вынимаем коленчатый вал из блока цилиндров.
26. Из проточек третьей опоры вынимаем два упорных полукольца.
27. Из опор блока цилиндров вынимаем верхние вкладыши коренных подшипников.
28. Отмываем блок цилиндров от грязи и отложений специальным моющим средством, дизельным топливом или керосином, продуваем масляные каналы.
29. Тонкой медной проволокой прочищаем выходные отверстия масляных форсунок на двигателях ваз 2112, 21124 и 21114.
30. Вытираем блок насухо и осматриваем его. Трещины и выкрашивание металла – недопустимы.
31. Микрометром измеряем коренные шейки коленчатого вала, а также шатунные шейки.
Ремонт
Трещины в любом месте коленчатого вала не допускаются
Процесс восстановления шатунных шеек
Таблица ремонтных размеров вкладышей и шеек КВ
Размеры | Коренные шейки | Шатунные шейки |
Номинальный размер | 50,799-50,819 | 47,83-47,85 |
1-ый ремонтный (- 0,25) | 50,549-50,569 | 47,58-47,60 |
2-ой ремонтный(- 0,50) | 50,299-50,319 | 47,33-47,35 |
3-ий ремонтный(- 0,75) | 50,049-50,069 | 47,08-47,10 |
4-ый ремонтный(- 1,00) | 49,799-49,819 | 46,83-46,85 |
Ремонт произвожу наплавкой в углеродной среде.
Диагностика
После ремонта вал должен проходить по следующим параметрам
1)Допустимые биения основных поверхностей коленчатого вала
Установите коленчатый вал крайними коренными шейками на две призмы и проверьте индикатором биение:
– коренных шеек и посадочной поверхности под ведущую шестерню масляного насоса (не более 0,03 мм);
– посадочной поверхности под маховик (не более 0,04 мм);
– посадочной поверхности под шкивы и поверхностей, сопрягающихся с сальниками (не более 0,05 мм).
– смещение осей шатунных шеек от плоскости, проходящей через оси шатунных и коренных шеек, после шлифования должно быть в пределах ±0,35 мм. Для проверки установите вал крайними коренными шейками на призмы и выставьте вал так, чтобы ось шатунной шейки первого цилиндра находилась в горизонтальной плоскости, проходящей через оси коренных шеек. Затем индикатором проверьте смещение в вертикальном направлении шатунных шеек 2, 3 и 4 цилиндров относительно шатунной шейки 1-го цилиндра.
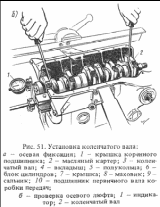
Полукольца заменяются также, если осевой зазор коленчатого вала превышает максимально допустимый – 0,35 мм. Новые полукольца подбирайте номинальной толщины или увеличенной на 0,127 мм, чтобы получить осевой зазор в пределах 0,06–0,26 мм.
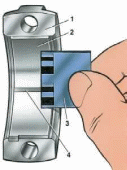
Измерение зазора в шатунном подшипнике: 1 – сплющенная калиброванная пластмассовая проволока; 2 – вкладыш; 3 – крышка шатуна; 4 – шкала для измерения зазора
– снимите крышку и по шкале, нанесенной на упаковке, по сплющиванию проволоки определите величину зазора.
Номинальный расчетный зазор составляет 0,02–0,07 мм для шатунных и 0,026–0,073 мм для коренных шеек. Если зазор меньше предельного (0,1 мм для шатунных и 0,15 мм для коренных шеек), то можно снова использовать эти вкладыши.
Сборка
Обработать гнезда фрезой А.94016/10.
Промыть КВ от остатков абразива и продуть сжатым воздухом.
Обезжирить посадочные места под заглушки (уайт-спирит ГОСТ 3134-78, ветошь ТУ 68-178-77-82).
Установить новые заглушки масляных каналов на герметик и зачеканить в 3 точках (оправка А.86010, зубило ГОСТ 7211-72, молоток ГОСТ 2310-77, герметизатор резьбовых соединений ТУ 6-10-1048-78).
32. Подбираем соответствующие кольца, вкладыши подшипников коленчатого вала
33. Обезжириваем гнезда вкладышей в опорах и крышках коренных подшипников.
34. Укладываем в гнезда опор вкладыши коренных шеек с канавками.
35. В крышки подшипников укладываем вкладыши без канавок.
36. В проточки третьей коренной опоры устанавливаем упорные полукольца. С передней стороны сталеалюминиевое (с внутренней стороны белое, а с наружной желтое), с задней – металлокерамическое (желтое с обеих сторон).
Замечание
Полукольца изготавливаются номинальной и увеличенной на 0,127 мм толщины. Осевое перемещение коленчатого вала должно быть в пределах 0,06–0,26 мм
37. Полукольца устанавливаем канавками наружу (к щекам коленчатого вала)
38. Смазываем шейки коленчатого вала и вкладыши чистым моторным маслом.
39. Укладываем вал в опоры блока цилиндров и устанавливаем крышки коренных подшипников.
На крышках рисками обозначены номера подшипников (с 1-го по 5-й). Крышка пятого коренного подшипника обозначена двумя рисками, разнесенными к краям крышки.
При установке в блок крышки должны быть рисками обращены к той стороне блока, на которой устанавливается направляющая указателя уровня масла.
40. Затягиваем болты крепления крышек динамометрическим ключом моментом 68,31–84,38 Н·м (6,97–8,61 кгс·м). Гайки шатунных болтов затягиваем моментом 51 Н·м (5,2 кгс·м)
41. Дальнейшую сборку выполняем в обратном порядке.
6. Способы восстановления КВ
Восстановление деталей имеет большое народнохозяйственное значение. Стоимость восстановления деталей в 2 - 3 раза ниже стоимости их изготовления. Это объясняется тем, что при восстановлении деталей значительно сокращаются расходы материалов, электроэнергии и трудовых ресурсов.
Эффективность и качество восстановления деталей зависят от принятого способа.
Наиболее широкое применение получили следующие восстановления деталей: механическая обработка; сварка и наплавка; напыление; гальваническая и химическая обработка; обработка давлением; применение синтетических материалов.
Механическую обработку применяют в качестве подготовительной или завершающей операции при нанесении покрытий на изношенные поверхности, а также при восстановлении деталей обработкой под ремонтный размер или постановкой дополнительных ремонтных деталей. Обработкой деталей под ремонтный размер восстанавливают геометрическую форму их рабочих поверхностей, а установкой дополнительной ремонтной детали обеспечивают соответствие размеров детали размерам новой детали.
Сварка и наплавка - самые распространенные способы восстановления деталей. Сварку применяют при устранении механических повреждений деталей (трещин, пробоин и т. п.), а наплавку - для нанесения покрытий с целью компенсации износа рабочих поверхностей. На ремонтных предприятиях применяют как ручные, так и механизированные способы сварки и наплавки. Среди механизированных способов наплавки наибольшее применение нашли автоматическая дуговая наплавка под флюсом и в среде защитных газов и вибродуговая наплавка. В настоящее время при восстановлении деталей применяют такие перспективные способы сварки, как лазерная и плазменная.
Напыление как способ восстановления деталей основан на нанесении распыленного металла на изношенные поверхности деталей. В зависимости от способа расплавления металла различают следующие виды напыления: дуговое, газопламенное, высокочастотное, детонационное и плазменное.
Гальваническая и химическая обработка основаны на осаждении металла на поверхности деталей из растворов солей гальваническим или химическим методом. Для компенсации износа деталей наиболее часто применяют хромирование, железнение и химическое никелирование. Нанесение на поверхности деталей защитных покрытий осуществляют с помощью гальванических процессов (хромирование, никелирование, цинкование, меднение), а также химических (оксидирование и фосфатирование).