Файл: 1. Устройство тормозной системы с гидравлическим приводом.docx
ВУЗ: Не указан
Категория: Не указан
Дисциплина: Не указана
Добавлен: 11.01.2024
Просмотров: 96
Скачиваний: 1
ВНИМАНИЕ! Если данный файл нарушает Ваши авторские права, то обязательно сообщите нам.
ТО-1 — дополнительно к объему работ по ЕО необходимо очистить от пыли и грязи все доступные элементы тормозной системы, у легковых автомобилей тщательно очистить скобы (суппорт) передних дисковых тормозов, проверить крепление основных узлов, штуцерных соединений и т.д. Следует соблюдать осторожность при подтягивании гайки штуцерных соединений (во избежание «подрезки» развальцованной головки трубопровода): подтягивание штуцерных гаек гаечным ключом лучше проводить левой рукой, а правой в это время прижимать трубопровод к гнезду сопрягаемого элемента системы гидропривода.
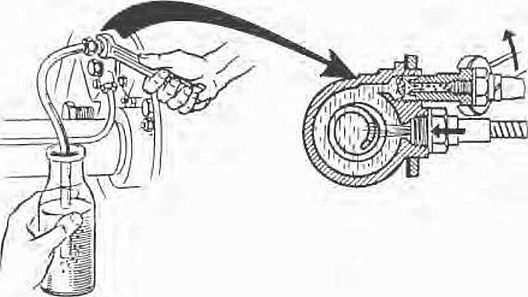
Рис. 3 Удаление воздуха из системы гидравлического привода тормозов автомобиля
Необходимо проверить уровень тормозной жидкости в бачке главного тормозного цилиндра, отвернув пробку заливной горловины, и тщательно прочистить воздушное отверстие в ней. При необходимости долить жидкость той же марки (БСК «Нева», «Томь», «Роса» и др.). Категорически запрещается смешивать тормозные жидкости, изготовленные на различной основе (во избежание их расслаивания). При работе автомобилей в особо пыльных дорожных условиях рекомендуется производить полную замену жидкости один раз в год (в противном случае возможно образование твердых грязевых комков в полости главного цилиндра, способных вывести тормозную систему из строя). При нормальных условиях эксплуатации жидкость следует менять раз в 2—4 года, в зависимости от степени загрязнения. При подозрении на попадание воздуха в систему гидропривода (по вышеуказанным признакам) необходимо произвести прокачку системы, начиная с самого дальнего колесного тормозного цилиндра от главного тормозного цилиндра и переходя затем к остальным, по мере их удаления. Прокачку производят отворачиванием гаечным ключом клапанов прокачки, располагаемых в верхней части колесного тормозного цилиндра (где обычно скапливается воздух), предварительно надев на головку клапана резиновый шланг, опущенный в прозрачный сосуд с тормозной жидкостью (рис. 7.18). При прокачке напарник по команде несколько раз нажимает резко на педаль тормоза (создавая тем самым давление в системе) и держит ее в нажатом состоянии, пока другой слесарь открывает клапан и выпускает жидкость. Если она выходит с пузырьками воздуха, то прокачку данного цилиндра следует повторить. В ходе прокачки следует следить за уровнем жидкости в бачке главного цилиндра, периодически доливая ее. После окончания прокачки довести уровень жидкости в бачке до нормы — 15—20 мм от края заливной горловины (или в соответствии с ТУ для данной модели).
В АТП рекомендуется использовать специальные баки для заправки и прокачки — мод.
При этом не требуется напарника, значительно облегчается сам процесс прокачки. Подсоединяют наконечник шланга к горловине заливного отверстия, предварительно подав с помощью шланга сжатый воздух в бак до рабочего давления 0,15—0,2 МПа, открывают кран на подводящем шланге для опрессовки гидравлической
системы тормозов. Удаление воздуха из колесных тормозных цилиндров производят, поочередно открывая гаечным ключом клапаны прокачки (с учетом вышеописанного правила очередности), до полного удаления воздуха, о чем свидетельствует прекращение выделения пузырьков воздуха из прокачиваемого цилиндра. В ходе проверки уже не надо постоянно следить за уровнем жидкости в бачке главного цилиндра и подливать ее. В крупных АТП для этой же цели используют передвижную установку С-90), которая снабжена дополнительным баком и системой шлангов для сбора «отработанной», вытекающей в ходе прокачки жидкости из гидросистемы тормозов. Следует помнить, что в двух контурных тормозных системах каждый контур надо прокачивать отдельно. У автомобилей с гидровакуумным усилителем прокачку рекомендуется начинать с дополнительного цилиндра усилителя, используя прокачные (перепускные) клапаны
Перед началом прокачки гидросистемы необходимо отрегулировать зазор между поршнем и штоком главного тормозного цилиндра (в тех моделях, где это предусмотрено). В одних моделях (например, у грузовых автомобилей ГАЗ) регулировка производится заворачиванием тяги в резьбовую часть штока 17, в некоторых моделях легковых автомобилей — вращением эксцентрика оси крепления педали, у автомобилей ВАЗ-2108 — перемещением корпуса выключателя стоп-сигнала вместе с буфером, упирающимся в выступ педали тормоза.
При ТО-1 в некоторых моделях предусмотрена частичная регулировка колесных тормозных механизмов задних колес. Эта регулировка предусматривает подвод колодок к тормозным барабанам, в основном в верхней части возле колесного тормозного цилиндра. Колеса перед регулировкой должны быть вывешены. Регулировку производят, медленно вращая регулировочный эксцентрик 5 за шестигранную головку болта, стопорящегося относительно опорного диска пружиной. Вначале регулируют переднюю колодку, вращая колесо вперед, — как только
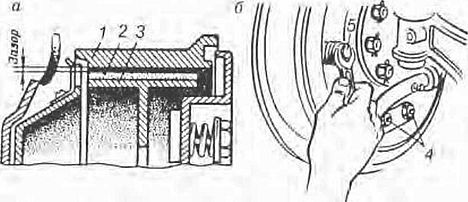
Рис. 4. Проверка и регулирование зазора между накладками тормозных колодок и тормозным барабаном:
а — проверка зазора; б — регулирование зазора;
1 — тормозной барабан; 2 — фрикционная накладка; 3 — тормозная колодка; 4 — опорные пальцы колодок; 5 — регулировочный эксцентрик колодки
оно затормозится, эксцентрик начинают вращать в обратном направлении до начала свободного вращения колеса (допускается легкое задевание накладок колодок за барабан). Таким же образом регулируют вторую колодку, но колесо при этом вращают уже в другую сторону, чтобы регулируемую колодку как бы отжимало от колесного тормозного цилиндра.
ТО-2 — дополнительно к объему ТО-1 проводят углубленную диагностику (поэлементную и полную) технического состояния тормозной системы. Для этого используются как небольшие переносные приборы, так и стационарные стенды (преимущественно с беговыми барабанами). Так, например, перед постановкой автомобиля на ТО-2, при наличии деселерометра, целесообразно провести ходовые испытания. Деселерометр (рис. 7.20) маятникового типа, состоящего из корпуса с маятником
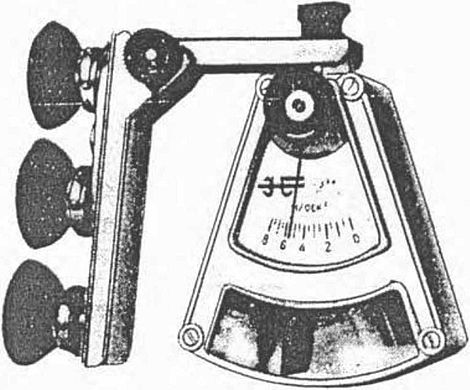
Рис. 5. Деселерометр для замера максимального замедления автомобиля при торможении, мод. 1155М
и кронштейна, с помощью резиновых присосов устанавливают на лобовом стекле или на стекле двери так, чтобы направление качания маятника совпадало с направлением движения автомобиля. Замер замедления производят при торможении со скорости 30 км/ч (КамАЗ и ЗИЛ-4331 — 40 км/ч) по отклонению маятника со стрелкой от нулевого положения и сравнивают показания с нормативным (для ГАЗ-3102 — 5,2 и 6,1 м/с2 для полностью заправленного автомобиля), оценивая тем самым общее состояние тормозов.
С помощью несложного по конструкции прибора (рис. 7.21) можно проверить техническое состояние гидровакуумного усилителя. Для этого тройник с вакуумметром устанавливают в систему трубопроводов, идущих от впускного коллектора двигателя к корпусу мембраны усилителя. Увеличивая постепенно частоту вращения КВ двигателя и тем самым разряжение во впускном коллекторе, по стрелке
Приложение 1
УСТРОЙСТВА ДЛЯ ПРОКАЧКИ ГИДРОСИСТЕМ ТОРМОЗОВ
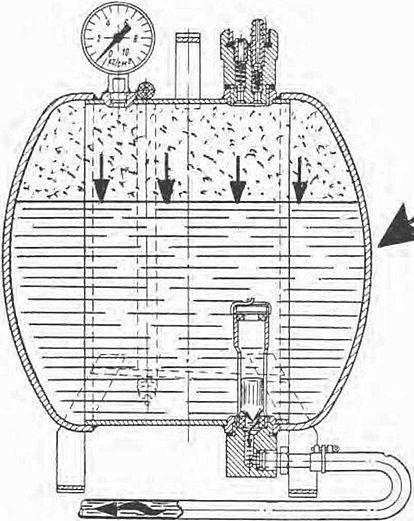
Рис. 1. Бак мод. 326 для заправки гидропривода тормозов
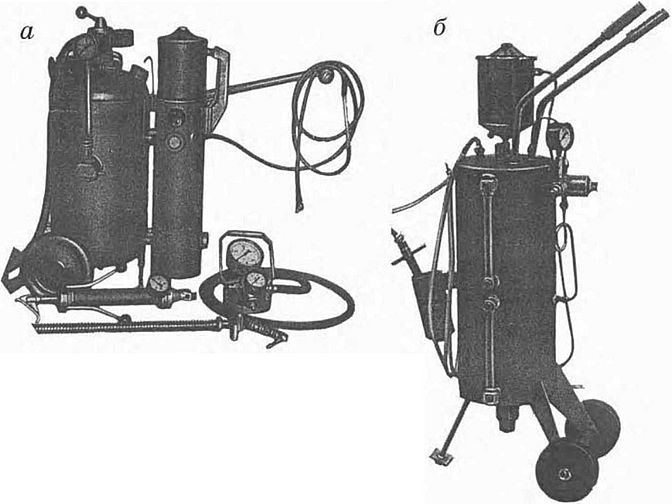
Рис. 2. Первые отечественные установки (а, б) для прокачки гидросистем тормозов
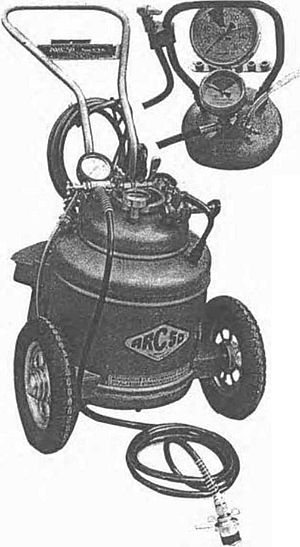
Рис. 4. Аппарат АРК-50 (Франция)
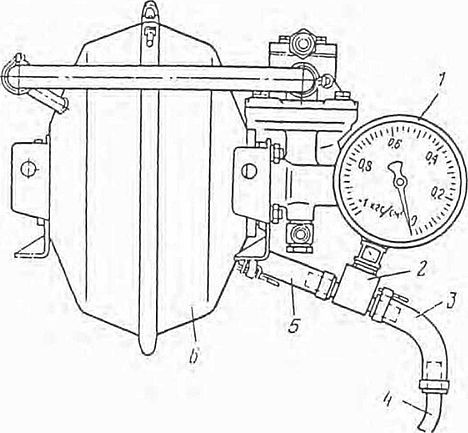
Рис. 5. Проверка работы гидровакуумного усилителя с помощью тройника с вакуумметром:
1 — вакуумметр; 2 — тройник; 3 — трубопровод от впускного коллектора двигателя; 6 — корпус диафрагмы усилителя
При ТО-2 в обязательном порядке снимаются все колеса и барабаны автомобиля в целях оценки состояния колесных тормозных механизмов и их обслуживания: отсоединяют стяжную пружину и проверяют легкость поворота на опорных эксцентричных пальцах колодок. В случае их заедания пальцы снимают, зачищают стеклянной шкуркой, смазывают тонким слоем тугоплавкой водостойкой смазки (1-13, Литол-24) и устанавливают на место так, чтобы контрольные метки на внешних торцах были обращены друг к другу.
При обнаружении течи из колесных тормозных цилиндров их следует заменять в сборе (производить ремонт на постах, в грязных условиях, путем замены поршеньков с манжетами не рекомендуется). При заедании поршеньков в цилиндрах, в т.ч. и в дисковых тормозах требуется замена колесных тормозных цилиндров. Ремонт их следует проводить в агрегатном цехе с соблюдением при сборке идеальной чистоты. Колодки с изношенными накладками или при наличии на них сколов и трещин заменяют. Менять рекомендуется сразу обе колодки. При незначительном замасливании накладок колодок их промывают ветошью, смоченной в чистом бензине. После высыхания бензина поверхность накладок, так же как и рабочую внутреннюю поверхность барабанов, следует зачистить шкуркой до полного удаления рисок и задиров. При большой овальности износа тормозных барабанов (разрешается биение рабочей поверхности у легковых автомобилей до 0,1—0,15 мм, у грузовых 0,2—0,25 мм) их следует сдать на расточку.
Перед сборкой тормозного механизма следует очистить от грязи опорный щит, продуть все детали сжатым воздухом. После установки на место тормозных барабанов следует провести полную регулировку тормозного механизма (в тех моделях автомобилей, где это предусмотрено по ТУ) — вначале колодки подводят поочередно к тормозным барабанам в нижней части, поворачивая эксцентриковые опорные пальцы метками наружу до затормаживания колеса, а затем отпуская до свободного вращения колеса.
При ТО-2, в порядке сопутствующего ремонта, можно заменять любые неисправные узлы и детали. Предварительно качество проведенных работ и регулировок можно оценить по ходу педали:
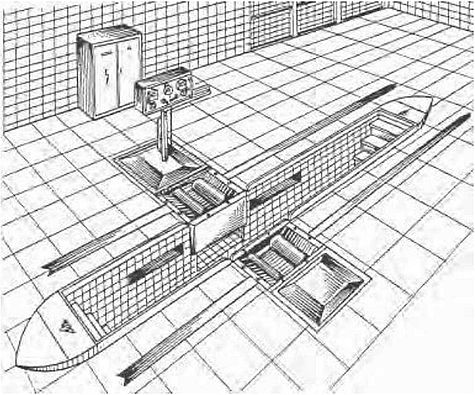
при нажатии на нее она не должна опускаться более чем на 1/2 хода, после чего сопротивление нажатию должно резко возрасти.
В крупных АТП и СТОА проверку тормозов производят на стационарных стендах отечественного (рис. 7.22, 7.23) или зарубежного (прилож. 47, рис. 1—6) производства.
Раньше для контроля тормозов легковых автомобилей выпускался стенд К-208, предусмотренный для установки на осмотровой канаве (для облегчения проведения регулировочных работ). В настоящее время выпускается модернизированный стенд модели К-208М, который в отличие от предыдущей модели имеет цельнометаллическую сварную раму с установленными в ней беговыми роликами и ряд других отличий. В его конструкцию входит пневмоподъемник, обеспечивающий въезд и съезд авто-Рис. 7.22. Стенд К-208 для проверки тормозов лег- мобилей со стенда; блок подготовки воздуха; возду-
ковых автомобилей хораспределитель для подачи воздуха в цилиндры
подъемника и пневмопривод нагрузочных устройств системы замеров; основной и выносной (в кабину автомобиля) пульты для управления электродвигателями беговых роликов, подъемником и для сброса показаний измерительных приборов; аппаратный шкаф и другие приспособления. Стенд может монтироваться на полу (в приямках), на полуэстакаде, а также на осмотровой канаве. На стенде проверяется тормозная сила на отдельных колесах и синхронность срабатывания тормозов отдельной оси автомобиля, время срабатывания тормозного привода и усилие, прикладываемое к педали тормоза. Оценка состояния тормозов производится по окружному тормозному усилию, измеряемому при прокручивании заторможенных колес автомобиля блоками беговых роликов стенда; при этом на корпусах их электродвигателей создается реактивный момент (пропорциональный тормозному моменту на колесах), регистрируемый датчиками давления гидроэлектрической системы замеров, ток с которых подается на измерительные приборы стенда. Блоки роликов имеют автономные приводы и системы замеров, что позволяет испытывать тормоз каждого колеса в отдельности или обоих колес одной оси сразу. Для фиксации тормозных сил на колесах на пульте управления расположены два прибора (со стабилизатором напряжения) оттарирован-ные в кН. Допустимая нагрузка на ось обслуживаемого автомобиля до 2 т, поэтому на стенде допускается также проверка малотоннажных грузовых автомобилей. Предел замера тормозной силы — 5 кН. Имитируемая скорость движения автомобиля — 5 км/ч. Погрешность замера тормозной силы — ±5%. Погрешность измерения во многом зависит от коэффициента сцепления колеса автомобиля с беговым роликом. Над этим вопросом уже много лет работают различные фирмы. Оригинальным конструкторским решением отличается отечественная разработка — на беговых роликах предусмотрено наличие большого количества сквозных (сверленых) отверстий, в углубления которых в ходе испытаний вдавливаются микроучастки резинового протектора шин колес автомобиля, благодаря чему