ВУЗ: Не указан
Категория: Не указан
Дисциплина: Не указана
Добавлен: 04.02.2024
Просмотров: 24
Скачиваний: 1
ВНИМАНИЕ! Если данный файл нарушает Ваши авторские права, то обязательно сообщите нам.
1. ВВЕДЕНИЕ
2.НАЗНАЧЕНИЕ мотор-вагонного депо
3.Система технического обслуживания и ремонта вагонов..
4. Периодичность проведения технического обслуживания.
5. ТЕХНОЛОГИЧЕСКИЙ ПРОЦЕСС РЕМОНТА вагона.
6.Охрана труда и техника безопасности.
7. ЗАКЛЮЧЕНИЕ
8. Список литературы
ВВЕДЕНИЕ
Железнодорожный транспорт был и остается важнейшей составной частью транспортной системы государства. На его долю приходится примерно 86% грузооборота и более 38% пассажирооборота. Железные дороги несут главную нагрузку по транспортировке таких массовых грузов, как уголь, руда, черные металлы, лесные грузы, удобрения, и перевозят треть производимых в стране нефтепродуктов. Железнодорожные перевозки в значительной мере влияют на состояние российской экономики, затраты на них напрямую связаны с эффективностью промышленного производства, его конкурентоспособностью на внутреннем и внешнем рынках. Этим же во многом определяется и финансово-экономическое положение самого железнодорожного транспорта. Вагонный парк является одним из важных технических средств. От технического уровня вагонного парка, его состояния, численности и состава, потребностях в перевозках, зависит качество перевозочного процесса, своевременность доставки пассажиров и грузов, производительность транспорта и его экономические показатели. Вагонное хозяйство обеспечивает работоспособность вагонного парка, поддерживая в исправном техническом и коммерческом состоянии вагоны, а так же безопасное и бесперебойное движение поездов, проводя планово-предупредительные ремонты и техническое обслуживание вагонов. Вагонное хозяйство, кроме того, обеспечивает пассажирам комфортабельные условия проезда. Для выполнения выше указанных задач вагонное хозяйство располагает необходимой производственной базой, включающей вагонные депо, мастерские, промывочно-пропарочные предприятия, конторы обслуживания пассажиров, прачечные, а также пункты технического обслуживания вагонов, пункты подготовки вагонов к перевозкам, ремонтно-экипировочные депо, контрольные пункты автотормозов и другие сооружения и устройства, входящие в состав вагонного депо или участка. Для обеспечения выполнения непрерывной и чёткой работы станции важен технологический процесс – это система работы станции, основанная на применении передовых методов и научной организации труда, предусматривающая наиболее целесообразный порядок и последовательность обработки поездов и вагонов, погрузки и выгрузки и нормы времени на выполнение этих операций, порядок планирования и оперативного руководства станцией. Технологический процесс обеспечивает наилучшее обслуживание производственных цехов, использование технических средств, параллельность выполнения операций, рациональную расстановку людей, слаженность действий работников разных специальностей при обработке поездов и вагонов, строгое соблюдение безопасности движения. Чёткая работа станции по технологическому процессу обеспечивает выполнение плана грузоперевозок, графика движения поездов и контактного графика обслуживания производственных цехов, а также обеспечивает непрерывность производства станционных операций и взаимодействие всех производственных звеньев станции.
2.В период с 27.03.2023г по 23.04.2023г, я проходил преддипломную практику в мотор-вагонном депо станции Алтайская по профессии: слесарь по ремонту подвижного состава.
Моторвагонное депо алтайская (тч-34) - структурное подразделение дирекции по обслуживанию пассажиров в пригородном сообщении - структурного подразделения западно-сибирской железной дороги - филиала открытого акционерного общества «российские железные дороги» - было открыто 23 сентября 2003г.
В депо производится обслуживание электропоездов алтайского отделения. здесь же изготавливают электромотрисы(например, мотриса начальника зсжд)
На сегодня моторвагонное депо алтайская - единственное на сети дорог, выполняющее самый сложный и трудоемкий ремонт электропоездов в объеме кр-2. после такого капитально-восстановительного ремонта они служат еще 15 лет. это экономически выгодно, так как ремонт вдвое дешевле приобретения нового поезда. сейчас на западно-сибирской железной дороге успешно эксплуатируется 75 обновленных в депо секций электропоездов.
3.плановая система то и ремонта электроподвижного состава (эпс), содержит комплекс правил, входящих в техническую и технологическую документацию, которые определяют организацию, порядок и сроки проведения работ для обеспечения надежности работы перевозочных средств, высокого качества обслуживания пассажиров, выполнения всех требований безопасности движения. она включает в себя три стадии технического обслуживания (то-1, то-2 и то-3, то-4) и три разновидности текущего ремонта (тр-1, тр-2 и тр-3). стадии то непосредственно увязаны и являются составной частью технологии обработки составов пригородных поездов.
4.периодичность проведения то определяется нормами:
— ТО-1 осуществляется локомотивной бригадой, закрепленной за электропоездом, в течение 20—60 мин в пунктах приписки и оборота до начала и после окончания смены, а также на стоянках поездов в отстое;
— ТО-2 проводится в пунктах технического обслуживания электропоездов (ПТОЭ) и на специализированных путях экипировки дизель-поездов и автомотрис в течение 1—2 ч локомотивной бригадой;
— ТО-3 выполняется на путях электродепо приписки в специализированных ремонтных стойлах через 5—6 суток в течение 2—4 ч в зависимости от технического состояния состава. Многие моторвагонные и локомотивные депо располагают цехом ТО-3 с одним или несколькими (двумя-тремя) ремонтными стойлами, в которых электропоезда и дизель-поезда устанавливаются без расцепки. Автомотрисы проходят ТО-3 в стойлах тепловозных депо или в цехах ТО-3, предназначенных для обслуживания дизель-поездов;
— ТО-4 (обточка колесных пар без выкатки из-под вагона) производится по необходимости.
Объем работ при ТР-1, ТР-2 и ТР-3 определяется Правилами текущего ремонта и технического обслуживания. Во время ТР-1 выполняют все работы, предусмотренные ТО-3, и дополнительно следующие работы: ремонт автотормозного оборудования, осмотр и проверку радиостанций, устройств автоматической локомотивной сигнализации и автостопов; осмотр и ремонт аккумуляторной батареи, силовых контроллеров и переключателей; ревизию междувагонных соединений, токоведущих устройств, осветительной аппаратуры, токоприемников, электропневматических клапанов токоприемников.
При текущем ремонте (ТР-2) выполняют все работы, предусмотренные ТР-1, и дополнительно производят следующие работы: обточку колесных пар, полный осмотр автосцепного устройства, ревизию тягового привода, опор кузова, тормозного оборудования, авторегулятора и пневматического регулятора тормозной рычажной передачи, электрокомпрессора, гидравлических гасителей колебаний, ручного насоса и вспомогательного компрессора, пневматических цилиндров электрических аппаратов, автоматических выключателей и автоматических дверей, аккумуляторной батареи с промывкой элементов, защитной аппаратуры с регулировкой тока уставки; ТР-2 производят после 175 тыс. км пробега.
При ТР-3 выполняют следующие работы:
по механическому оборудованию: выкатку тележек и проверку рам со снятием всего оборудования, ремонт деталей тележек и замену негодных, освидетельствование колесных пар, ревизию редукторов, ремонт упругих муфт и деталей подвески редуктора, ремонт тормозной рычажной передачи с заменой изношенных валиков и втулок, ремонт автосцепного устройства и рессорного подвешивания с переборкой листовых- рессор или заменой листовых рессор и цилиндрических пружин, дефектоскопию деталей и узлов, окраску ходовых частей, рам и тележек, ремонт и испытания гидравлических гасителей колебаний, смазку соединений и трущихся частей;
по электрическому оборудованию: ремонт, пропитку (покрытие) и испытание тяговых двигателей и вспомогательных машин, ремонт высоковольтных выключателей, дросселей, токоприемников, резисторов, ремонт и промывку аккумуляторной батареи, ревизию пневматических приводов электроаппаратов, электропневматических вентилей, клапанов токоприемников и цилиндров пневматических дверей, ревизию на месте не снимаемого электрического оборудования, проверку состояния изоляции и целостности проводов электрических цепей вагонов; "
по тормозному и пневматическому оборудованию: разборку, очистку, ремонт и испытание всего оборудования, ремонт и испытание компрессоров, техническое освидетельствование, ремонт и гидравлическое испытание воздушных резервуаров с промывкой и пропаркой главных резервуаров, осмотр и продувку воздухопроводов;
по кузовам вагонов: ремонт дверей, полов, стен, потолков, крыш, рам и деталей внутреннего оборудования, шпинтонов и упругих переходных площадок, осмотр рамы кузова, окраску кузовов вагонов внутри и снаружи (включая днище кузова и несъемное оборудование), зачистку и покрытие лаком деревянной арматуры пассажирских помещений без разборки и ремонт жестких и полумягких сидений с последующим покрытием лаком;
по оборудованию общего назначения: снятие, осмотр и ремонт устройств АЛСН,^ оборудования радиостанции, телефонной и громкоговорящей оповестительной установок, ремонт скоростемеров и их приводов.
Капитальный ремонт (КР-1) производят после пробега 700 тыс. км для восстановления эксплуатационных характеристик, исправности и ресурса (срока службы) изношенных и поврежденных агрегатов, узлов и деталей электропоездов путем их замены или ремонта, а также модернизации.
Капитальный ремонт (КР-2) выполняют после пробега 2100 тыс. км для восстановления эксплуатационных характеристик, исправности и полного ресурса всех агрегатов, узлов и деталей электропоездов, включая базовые, для полной замены проводов и кабелей, а также с целью проведения модернизации.
5.Технологический процесс ремонта вагонов
Общий технологический процесс ремонта вагонов в депо, как правило, включает в себя работы, представленные на рис. 1.1
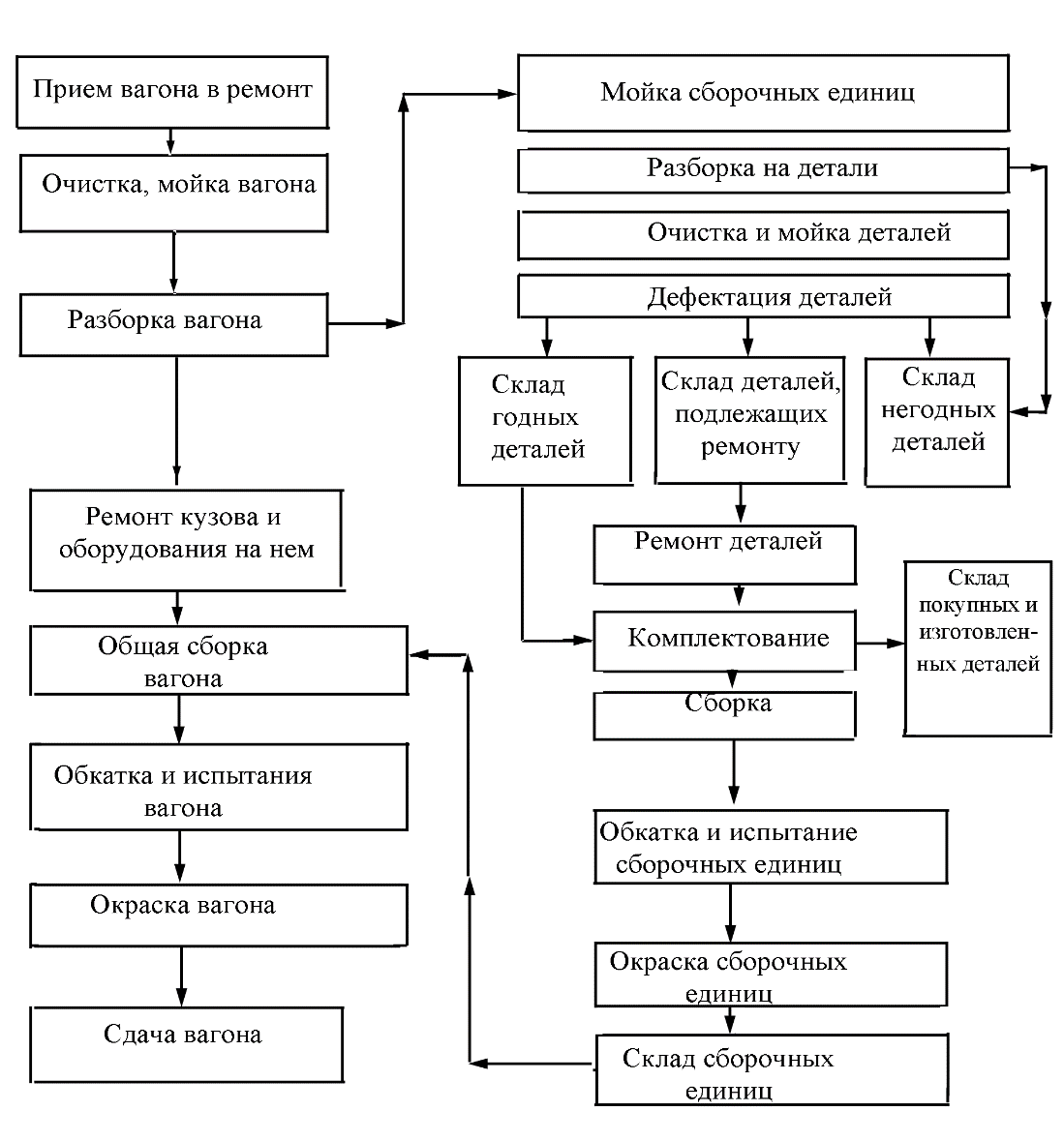
Рис.1.1.
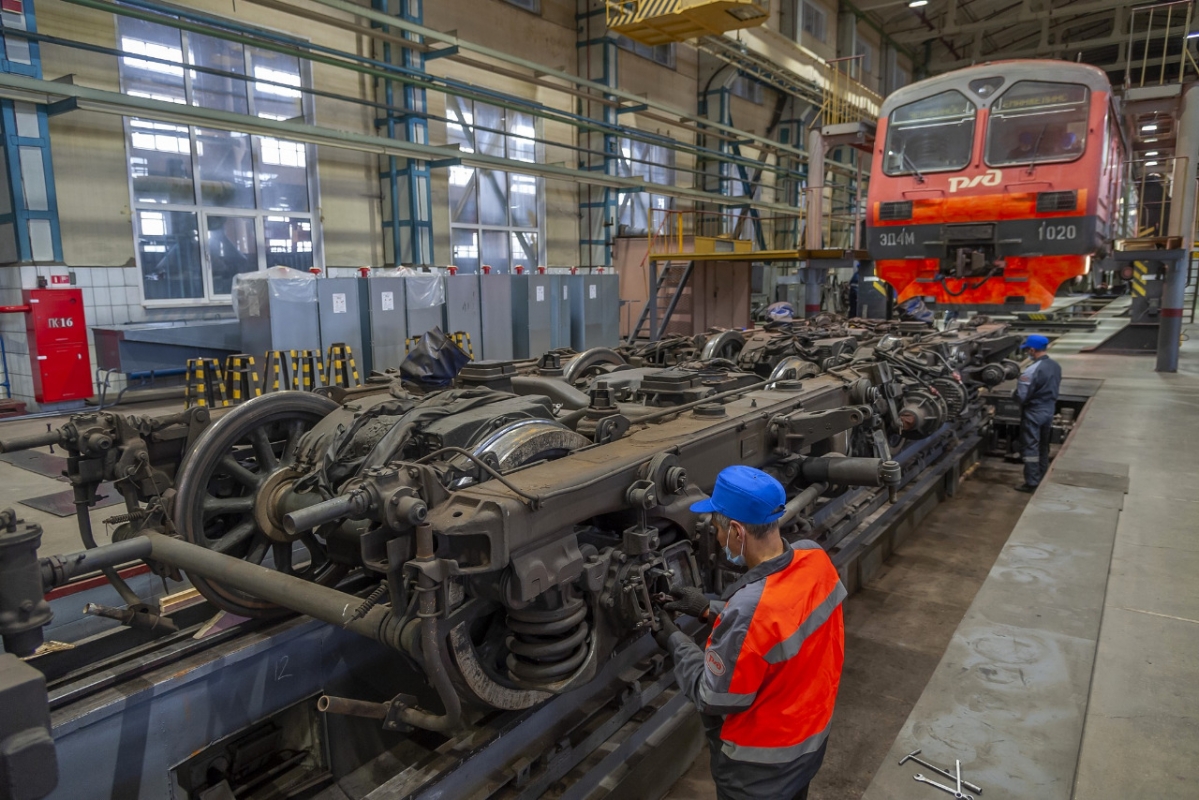
6. Охрана труда и техника безопасности Виды инструктажей: 1. Вводный – проводит инженер по охране труда со всеми вновь принятыми на предприятие. Инструктаж проводится по конспекту вводного инструктажа (оговариваются общие меры по безопасности на предприятии); 2. Первичный – проводится после вводного на рабочем месте руководителем подразделения (оговариваются меры безопасности данного рабочего места); 3. Повторный (повтор первичного инструктажа) – проводит руководитель подразделения с периодичностью один раз в шесть месяцев (или один раз в три месяца); 4. Целевой – проводится в случаях: при выполнении работ не связанных с прямыми обязанностями; при проведении экскурсии по предприятию; при выполнении работ на которые оформляется наряд допуска (опасные работы); при ликвидации последствий аварии. 5. Внеплановый – производится при происшествии несчастного случая, при поступлении телеграммы о несчастных случаях, по требованию гос. инспектора, при перерыве в работе, при любых нововведениях, при изменении погодных условий. Все виды инструктажей регистрируются в журнале установленной формы. За безопасное производство работ, соблюдение техники безопасности и производственной санитарии несут ответственность начальник вагонного депо, главный инженер, мастер ЦРТ и бригадир. Требования к оборудованию, инструменту, приспособлениям и рабочим местам. Оборудование, средства неразрушающего контроля должны быть исправны, своевременно проверены и безопасны в работе. Техническое освидетельствование и обслуживание кран-балки, а также выполнение работы на ней должны производиться в соответствии с действующими правилами устройства и безопасной эксплуатации грузоподъемных кранов. Стенды и приспособления должны надежно удерживать детали в процессе их разборки, сборки, ремонта и контроля. Шлифовальные круги не должны иметь биения по окружности. При работе со шлифовальными кругами необходимо следить, чтобы стружка летела от работающего. Дефектоскопы должны быть надежно заземлены. Запрещается пользоваться дефектоскопами при наличии повреждений изоляции катушек, соединительных проводов, сетевых выключателей, неисправности корпуса и т.п. в процессе работы дефектоскоп должен находиться под напряжением только в течение времени, необходимого для намагничивания или испытания детали. Переносные электролампы, применяемые для осмотра внутренних частей литых деталей тележки, должны быть напряжением не выше 36в и иметь защитные устройства. Все слесарные работы по ремонту тележек должны выполняться только исправным слесарным инструментом. Молотки должны иметь ровную, без заусенцев слегка выпуклую поверхность бойка, овальное отверстие для ручки с небольшим конусом наружу, ручку овального сечения, гладкую, без сучков и трещин. Гаечные ключи должны точно соответствовать указанным на них размерам и не иметь разошедшихся челюстей. Нельзя наращивать гаечные ключи другими ключами, а также применять прокладки между гайкой и ключом. Зубила должны иметь ровные, не сбитые, слегка выпуклые затылки без заусенцев. Длина зубила должна быть не менее 150мм, оттянутая часть зубила – 60-70мм. Электроинструмент и пневмоинструмент, имеющие неисправности, к эксплуатации не допускаются. Рабочие места и проходы к ним должны содержаться в чистоте, не допускается загромождение их запасными частями, снятыми с вагона деталями, посторонними предметами. Детали и инструмент необходимо размещать так, чтобы работа с ними не вызывала лишних движений. Детали и инструмент следует укладывать в местах. Исключающих их падение. Электросварочные работы должны выполняться в кабинах, защищенных от других участков перегородками из тонкой листовой стали. В цехе должна находиться медицинская аптечка для оказания доврачебной помощи. Работник должен знать: правило оказания первой (до врачебной) помощи пострадавшему при несчастном случае; действие на человека опасных и вредных производственных факторов, возникающих во время работы; требование техники безопасности, производственной санитарии и пожарной безопасности. Допустимая масса поднимаемого и перемещаемого груза вручную постоянно в течении рабочей смены не должна превышать для мужчин 15 кг, для женщин 7 кг. Масса поднимаемого и перемещаемого груза вручную при чередовании с другой работой не должна превышать для мужчин 30 кг, для женщин 10 кг. Допускается поднимать и перемещать вдвоем вручную грузы массой более 30 кг для мужчин и более 10 кг для женщин. Установку тяжелых деталей следует производить при помощи подъемно-транспортных механизмов. Работник должен: выполнять только порученную ему мастером (бригадиром) работу; владеть безопасными приемами труда; содержать в исправном состоянии и чистоте закрепленное за ним рабочее место, инструмент, приспособления, а также СИЗ; использовать в работе только исправный инструмент; носить инструмент и измерительные приборы в специальных футлярах или сумках; выполнять требования запрещающих, предупреждающих, указательных и предписывающих знаков и надписей, а также сигналов, подаваемых крановщиками, водителями транспортных средств и работниками, занятыми ремонтными работами на территории предприятия; проходить по территории предприятия по установленным маршрутам, пешеходным дорожкам, проходам и переходам; быть предельно внимательными в местах движения транспорта; соблюдать правила внутреннего трудового распорядка. Запрещается: оставлять без присмотра электрооборудование подключенным к сети; работать в болезненном состоянии, а также в состоянии алкогольного или наркотического опьянения; использовать переносные светильники без предохранительных сеток, с поврежденной вилкой и изоляцией проводов; находиться под поднятым и перемещаемым грузом; работать без СИЗ; переходить или перебегать перед движущимся составом, локомотивом, мотовозами, дрезинами и другими транспортными средствами; подлезать под подвижной состав и перелезать через автосцепку при переходе через путь; подниматься на подвижной состав, находящийся под контактным проводом; садиться на подножки вагонов или локомотивов и сходить с них во время движения; находиться на междупутье между поездами при безостановочном их следовании по смежным путям; переходить стрелки, оборудованные электрической централизацией, в местах расположения остряков и крестовин, ставить ноги между рамным рельсом и остряком или в желоба на стрелочном переводе, наступать и садиться на рельсы и концы железобетонных шпал; находиться на территории депо, железнодорожной станции в местах отмеченных знаком «Осторожно! Негабаритное место», а также около этих мест при прохождении подвижного состава; работать под подъемными механизмами и подвешенным грузом. Работник обязан соблюдать следующие требования пожарной безопасности: не курить и не пользоваться открытым огнем во время работы; не производить работы, связанные с применением открытого огня, факелов; обо всех неисправностях электрооборудования немедленно сообщать бригадиру (мастеру); курить только в отведенных и приспособленных для этого местах; знать и уметь пользоваться первичными средствами пожаротушения.
7. Заключение.
Прохождение практики считаю весьма полезным мероприятием для выработки профессиональных навыков и для моей будущей работы по специальности.
Я считаю, что производственная практика является важной частью подготовки высоко-квалифицированных специалистов, поскольку в процессе ее ставится задача закрепления и расширения знаний, полученных при обучении студентов в университете. Требуется изучение работы предприятия, учреждения, в которых будущие специалисты проходят практику. В течение же производственной практики работа студентов должна строиться таким образом, чтобы поставленная узкая задача завершалась конкретным результатом. Только в этом случае достигается основная цель практики, как формы приобщения студента к самостоятельной исследовательской работе.
В процессе практикума на производстве у меня возникла мысль о необходимости увеличения производительности труда за счет экстенсивного развития предприятия, то есть об автоматизации ремонта тележек.
Основной проблемой, стоящей перед железнодорожными компаниями, является сокращение эксплуатационных расходов. Одна из наиболее значимых статей этих расходов - затраты на техническое обслуживание и ремонт подвижного состава, которые включают много трудоемких операций, зачастую выполняемых в неблагоприятных условиях. Положение усу-губляется недостатком рабочей силы, так как ремонтно-эксплуатационный персонал постепенно "стареет" и выходит на пенсию, а для новых, более молодых рабочих такие работы не-привлекательны (судя по своему опыту). Поэтому в последнее время механизации и автоматизации технологического процесса обслуживания и ремонта нужно уделять особое внимание. К числу операций, входящих в процесс ремонта, относятся разборочные.
Эти операции имеют свою специфику и практически не встречаются в современном машиностроительном производстве. Кроме того, подлежащие разборке узлы и агрегаты после длительной эксплуатации загрязнены, изношены, крепежные соединения труднодоступны и разнохарактерны, после снятия креплений следует обеспечить целостность высвобождаемых деталей. Все это осложняет разборочные работы и ставит их на одно из последних мест по технико-социальному уровню. Для преодоления указанных затруднений необходимо создать и использовать при разборке подвижного состава устройства, требующие минимально возможных затрат ручного труда. Это в полной мере относится к разборке тележек, выполняемой в наиболее трудных условиях.