Файл: Содержание Введение 2 Дуговая сталеплавильная печь 4 Конструкция печи 5 Принцип работы 7 Заключение 10 Список литературы 11 Введение.docx
Добавлен: 30.11.2023
Просмотров: 82
Скачиваний: 5
ВНИМАНИЕ! Если данный файл нарушает Ваши авторские права, то обязательно сообщите нам.
Содержание
Введение 2
Дуговая сталеплавильная печь 4
Конструкция печи 5
Принцип работы 7
Заключение 10
Список литературы 11
Введение
Дуговая печь - электрическая плавильная печь, в которой используется тепловой эффект электрической дуги для плавки металлов и других материалов.
В конструкции Дуговых печей используется современные технические решения, позволяющие повысить скорость плавки за счет трансформаторов высокой мощности, сократить удельный расход электроэнергии, повысить безопасность, увеличить качество получаемой продукции.
Аналогичное конструктивное исполнение элементов печей переменного тока и печей постоянного тока – кожух, свод, механизм наклона печи и перемещения электрода, одинаковая схема загрузки шихты и разлива металла, использование одних и тех же огнеупорных материалов – позволяют хорошо вписать дуговые печи постоянного тока в существующие технологические линии литейных и металлургических цехов, почти полностью используя разработанные технологические процессы плавления и рафинирования металла.
Дуговые печи называются дуговыми или электродуговыми из-за принципа образования источника тепловой энергии, которая выделяется на электрической дуге. Температура на дуге составляет 6000К.
Подаваемый в плавильное пространство ток выпрямляется тиристорами и дает ряд эксплуатационных преимуществ, в сравнении с переменным током. Дуговые печи работают бесшумно, нет обратных токовых бросков в сеть, ниже угар и газообразование, есть возможность переработки мелкодисперсных материалов и стружки. Скорость плавки ДСП и ДППТ аналогичны, по расходу электроэнергии ДППТ экономичнее на 10-15%, по расходу графитированных электродов экономия составляет 30-50%, стойкость огнеупорных материалов выше. Все эти показатели справедливы при сравнении печей ДСП с 3 сводовыми электродами и ДППТ с 1 сводовым и 1 подовым.
Дуговая сталеплавильная печь
Сталеплавильные дуговые печи обычно являются печами прямого действия и их разделяют на печи переменного тока (ДСП) и печи постоянного тока (ДППТ). В печах переменного тока трехфазный ток проходит между электродами через посредник, которым является шихта (металл, углерод). В этих печах требуются дорогостоящие устройства для компенсации низкого cos ϕ и присутствуют большие индуктивные сопротивления токоподвода в короткой сети, что обусловливает самопроизвольный перенос мощности с одной фазы на другую. В результате возможно образование “мертвой” (отсутствие мощности) и “дикой” (избыточное выделение мощности) фазы.
В печах постоянного тока выделение мощности происходит равномерно и отсутствуют компенсирующие устройства, присущие печам переменного тока. В ДППТ вместо трех графитовых электродов находится только один (хотя он и может быть расщеплен на несколько), а вторым электродом (анодом) является подовый электрод. Преимущества печей постоянного тока по сравнению с печами на переменном токе в 1,5-2 раза меньшем расходе графитовых электродов, на 5-15 % меньшем расходе электроэнергии, на 10 % меньшем износе огнеупоров, в 8 раз меньшем выбросе пыли (0,9-1 кг/т вместо 7-8 кг/т в печи переменного тока) и в меньшем уровне шума (90 децибел взамен 120 децибел в печах переменного тока). Главный недостаток печей постоянного тока связан с получением постоянного тока из переменного тока и большие капитальные затраты на преобразователи тока. Для компенсации этого недостатка разработаны специальные полупроводниковые технологии. К недостаткам ДППТ также можно отнести необходимость использования более дорогостоящих электродов большего диаметра (700-750 мм) взамен электродов диаметром 350-610 мм в ДСП и недостаточную надежность подовых электродов.
Конструкция печи
Кожух печи должен выдерживать нагрузку от массы огнеупоров и металла. Его делают сварным из листового железа толщиной 40 мм в соответствии с размерами печи. Форма кожуха определяет профиль рабочего пространства дуговой электропечи. В данной печи используется кожух цилиндрической формы. Для сохранения правильной цилиндрической формы кожух усиливается ребрами и кольцами жесткости. Днище кожуха выполняется конусно-сферическим, что обеспечивает наибольшую прочность кожуха и минимальную массу кладки. Для размещения подовых электродов предусматривается два, диаметрально расположенных отверстия. Сверху печь закрыта сводом. Свод набирают из огнеупорного кирпича в металлическом водоохлаждаемом сводовом кольце, которое выдерживает распирающие усилия арочного сферического свода. В нижней части кольца имеется выступ - нож, который входит в песчаный затвор кожуха печи. В кирпичной кладке свода оставляют отверстие для электрода. Диаметр отверстия больше диаметра электрода, поэтому во время плавки в зазор устремляются горячие газы, которые разрушают электрод и выносят тепло из печи. Для предотвращения этого на своде устанавливают холодильники или экономайзеры, служащие для уплотнения электродного отверстия и для охлаждения кладки свода. Газодинамические экономайзеры обеспечивают уплотнение с помощью воздушной завесы вокруг электрода. В своде имеется также отверстие для отсоса запыленных газов и отверстие для кислородной фурмы. Для подгрузки легирующих и флюсов в печь, скачивания шлака, осмотра, заправки и ремонта печи имеется загрузочное окно, обрамленное литой рамой. К раме крепятся направляющие, по которым скользит заслонка. Заслонку футеруют огнеупорным кирпичом. Для подъема заслонки используют электромеханический привод. С противоположной стороны кожух имеет окно для выпуска стали из печи. К окну приварен сливной желоб. Отверстие для выпуска стали круглое диаметром 120 – 150 мм. Сливной желоб имеет корытообразное сечение и приварен к кожуху под углом 10 – 12° к горизонтали. Изнутри желоб футеруют шамотным кирпичом.
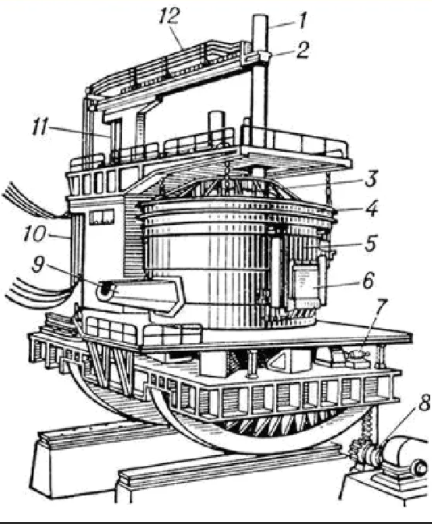
Рисунок 1 – Конструкция дуговая сталеплавильная печь: 1 – графитированный электрод; 2 – электродержатель; 3 – свод; 4 – водоохлаждаемое сводовое кольцо; 5 – цилиндрический кожух; 6 – водоохлаждаемая вспомогательная дверка; 7 – электромеханический механизм поворота печи вокруг вертикальной оси; 8 – электромеханический механизм наклона печи; 9 – сливной носок; 10 – подвижной токоподвод из водоохлаждаемых гибких кабелей; 11 – шток для вертикального перемещения системы стойка – рукав – электродержатель – электрод; 12 – токоподвод из охлаждаемых медных труб.
Принцип работы
Принцип работы ДСП следующий. Шихтовые материалы загружают на подину печи сверху в открываемое рабочее пространство с помощью бадьи (корзины) с открывающимся дном.
После этого свод печи надвигается на ванну, имеющую форму чаши. Электроды опускают через отверстия свода до возникновения короткого замыкания с шихтой и зажигают электрические дуги. Плавление и нагрев осуществляются за счёт теплоты электрических дуг, возникающих между электродами через жидкий металл или металлическую шихту. После расплавления шихты в печи образуется слой жидкого металла и шлака. Путем добавок в жидкую сталь раскислителей и легирующих добавок добиваются нужного состава стали. Готовую сталь и шлак выпускают через сливной желоб, наклоняя рабочее пространство. Рабочее окно, закрываемое заслонкой, предназначено для контроля за ходом плавки, ремонта пода, загрузки материалов и промежуточного выпуска шлака (в окислительный период). Температура жидкой стали при выпуске на 120-150 °С выше температуры ликвидус и составляет 1550-1650 °С.
По ходу плавки выделяют 4 периода:
1 – подготовка печи к плавке (20-40 минут). Исправление изношенных участков пода заправкой подины магнезитовым порошком, завалка шихты;
2 – период плавления (70-180 минут). Ввод максимальной электрической мощности. Нагрев и расплавление шихты; формирование шлака за счет окисления кремния, марганца, углерода и железа кислородом воздуха, окалины. Возможно использование газокислородных горелок, установленных в стенках или в своде, для ускорения расплавления твердой шихты. Возможна продувка жидкого металла кислородом для ускорения процесса плавления остатков нерасплавившейся шихты. Удаление основной массы фосфора из металла за счет наличия основного железистого шлака;
3 – окислительный период (30-90 минут). Слив основной массы шлака для удаления из печи фосфора; присадка шлакообразующих добавок (известь и др.); присадка руды для интенсивного окисления углерода, получения эффекта “кипения”, во время которого происходит дефосфорация металла и удаление с пузырьками СО водорода и азота; периодический слив вспененного шлака; нагрев металла до температуры выпуска; полный слив окислительного шлака для исключения перехода фосфора из шлака в металл в восстановительный период;
4 – восстановительный период (40-120 минут). Присадка ферромарганца и феррохрома для доведения содержания марганца и хрома до требуемого для выплавляемой марки стали, а также ферросилиция и алюминия для раскисления металла (раскисление – удаление из жидкого металла кислорода путем присадки раскислителей: углерода, кремния, марганца); наводка высокоосновного шлака путем добавки извести, плавикового шпата и шамотного боя для ускорения раскисления и удаления серы из металла; раскисление молотым коксом; раскисление молотым ферросилицием в смеси с известью, плавиковым шпатом и коксом; по необходимости добавка сильных раскислителей: силикокальция и алюминия; легирование стали ферровольфрамом, феррованадием, ферросилицием, ферротитаном, алюминием и др.; выпуск стали вместе с шлаком для дополнительного перехода в шлак серы и неметаллических включений.
Основные параметры, которые лимитируют процесс плавки, это температура футеровки и полная электрическая мощность. Если температура низкая, то мощность поддерживают максимальной без опасности перегрева футеровки. Нежелательным является для футеровки превышение температуры 1500-1800 °С. Подину обычно выполняют из магнезитового кирпича, а стены и свод ванны – из магнезитохромитового кирпича. Стойкость футеровки стен и свода колеблется в пределах 75-250 плавок. Стойкость подины составляет 1500-5000 плавок при условии ее обновления после каждой плавки путём заправки магнезитовым порошком. Общая толщина подины на печах, работающих с электромагнитным перемешиванием, не должна превышать 800-900 мм.
Заключение
Основные преимущества дуговой сталеплавильной печи:
-
возможность регулирования окислительно-
восстановительных свойств среды по ходу плавки, а также обеспечения в печи восстановительной атмосферы и безокислительных шлаков, что предопределяет малый угар легирующих элементов (для справки: угар – потери металла в результате окисления при плавке или при нагреве);
-
быстрый нагрев металла, связанный с вводом тепловой мощности в самом металле. Это позволяет вводить в печь большие количества легирующих элементов; -
плавная и точная регулировка температуры стали; -
более полное, чем в других печах, раскисление металла, получение его с низким содержанием неметаллических включений; -
получение стали с низким содержанием серы.
Одним из недостатков дуговой печи является необходимость обеспечения высокого качества шихтовых материалов, из которых 75-100 % составляет стальной лом. Лом должен иметь как можно меньше примесей цветных металлов, фосфора, ржавчины. Лом должен быть тяжеловесным для загрузки его в один приём, т.к. каждая загрузка лома значительно удлиняет плавку. Другой недостаток дуговой печи в непроизводительном использовании мощностей печи в периоды низкого потребления энергии (окислительный и восстановительный периоды).
Список литературы
1. Электрооборудование и автоматика электротермических установок. Справочник. Под.Ред. Альтгаузена А. П., – М.: Энергия, 1978. – 304с., ил.
2. Свенчанский А.Д., Смелянский М. Я. Ч. 2. Дуговые печи. Учебное пособие для вузов, – М.: Энергия, 1970, – 264 с.
3. Электротермические оборудование. Справочник. Изд .2-е перераб. и доп. /Под общей ред. А. П. Альтгаузена. – М.: Энергия, 1980. – 418 с., ил.
4. Электрические промышленные печи. Дуговые печи и установки специального нагрева. Учебник для вузов. Свенчанский А. Д., Жердов И. Т., Кручинин А. М. и др. Под ред. Свенчанского А. Д.. Изд. 2-е, перераб. и доп. – М.: Энергоиздат, 1981. – 296 с., ил.
5. Кацевич Л. С. Теория теплопередачи и тепловые расчеты электрических печей. Учебник для техникумов. М.: Энергия, 1977.
6. Крамаров А. Д. Производство стали в электропечах. Изд. 3-, испр. и дополн. – М.: Металлургия, 1969. – 348 с.
7. Макаров В. С., Цишевский В. П. Проектирование дуговых сталеплавильных печей. Методические указания к курсовому проекту. Под ред. Ткачева Л. Г. – Екатеринбург: МЭИ, 1988.
8. Трансформаторы для промышленных электропечей. В. Ш. Аншин, А. Г. Крайз, В. Г. Мейксон; Под ред. А. Г. Крайза – М.: Энергоиздат, 1982. – 296 с., ил. – (Трансформаторы; Вып. 39)