Файл: Лекция 1 Подготовка кромок. Сборка деталей, определение величины зазора. Инструмент для выполнения измерений ушс3.docx
ВУЗ: Не указан
Категория: Не указан
Дисциплина: Не указана
Добавлен: 06.12.2023
Просмотров: 236
Скачиваний: 1
ВНИМАНИЕ! Если данный файл нарушает Ваши авторские права, то обязательно сообщите нам.
СОДЕРЖАНИЕ
Устройство универсального шаблона сварщика УШС-3
Контроль квалификации сварщиков
5. Контроль подготовки изделий под сварку, сварочного оборудования и технологии сварки
Проверка сварных соединений на проницаемость
Преимущества полуавтоматической сварки трубы
Оборудование для полуавтоматической сварки трубы
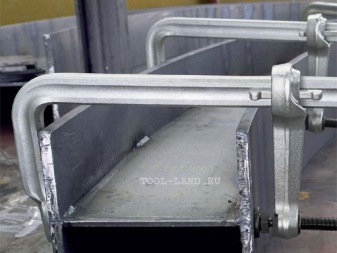
Призмы
Эта группа приспособлений используется для правильного позиционирования цилиндрических элементов. Если под рукой нет готовой конструкции, призму можно собрать из уголков, просто сварив их между собой.
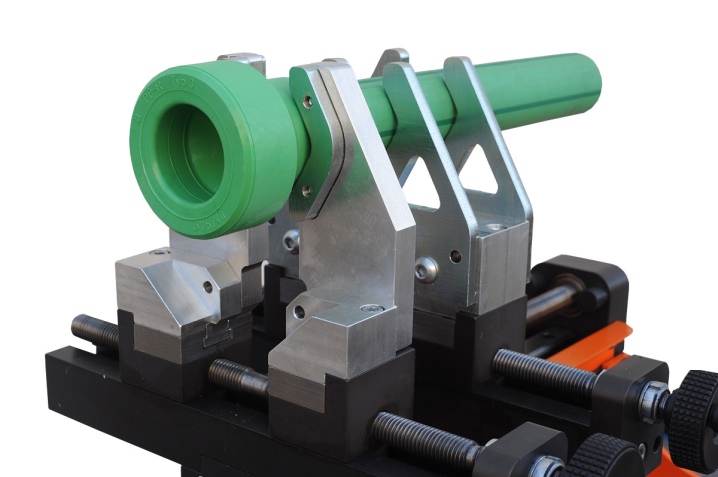
Шаблоны
Шаблоны нужны для того, чтобы обеспечить правильное расположение новых элементов конструкции относительно тех, что уже успешно закреплены.
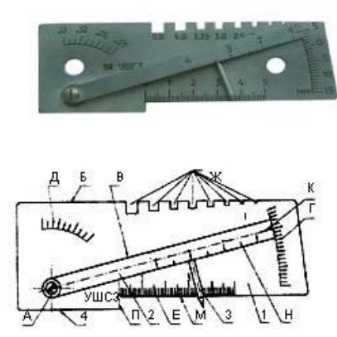
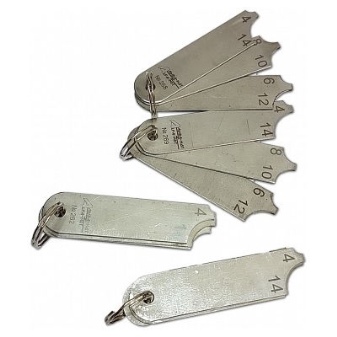
Крепежные приспособления
Оснастка нужна для того, чтобы обеспечить надежную фиксацию деталей в определенном положении после того, как установка уже будет произведена. При помощи таких приспособлений осуществляется финальная подготовка к сварке. С их помощью можно удержать на месте деталь под прямым углом или в другом заданном положении, предотвратить ее деформацию и смещение.
Иногда крепежные приспособления нужны при охлаждении деталей, чтобы они не меняли свои геометрические параметры.
Самыми популярными разновидностями сварочных принадлежностей в этой категории можно назвать несколько приспособлений.
-
Струбцины. Универсальное приспособление, позволяющее существенно облегчить и ускорить процессы при любом типе сварки. Струбцины бывают разными по размеру и форме, различаются по наличию регулируемого или стационарного зева. Самые простые и популярные из них — быстрозажимные, обеспечивающие сдавливание при помощи вращения кулачкового механизма вручную со сближением упорной площадки.
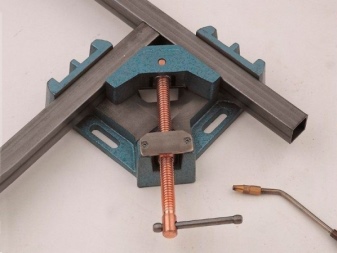
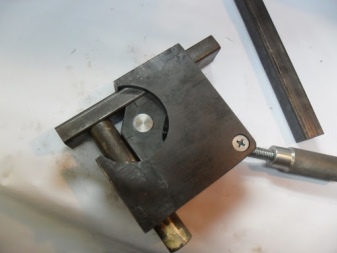
-
Зажимы. По принципу действия они похожи на струбцины, но более универсальны и удобны при сварочных работах. Деталь фиксируется путем сжатия их рукояток. Сила сжатия регулируется винтом, но также может применяться конструкция с переставляемым штифтом и несколькими отверстиями.
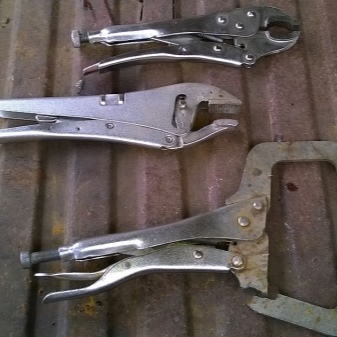
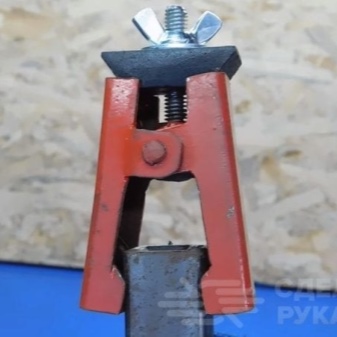
-
Прижимы. Эта разновидность крепежных приспособлений для сварки бывает нескольких типов: с пружинами и рычагами, эксцентриком, клиньями, вставляемыми в проушины. В зависимости от того, какой именно тип конструкции используется, нужное давление оказывается на определенный участок поверхности. Простейшие прижимы выглядят, как стальные пластины с винтами, продетыми в их отверстия — между плоскостями вставляется деталь, затем регулируется степень фиксации.
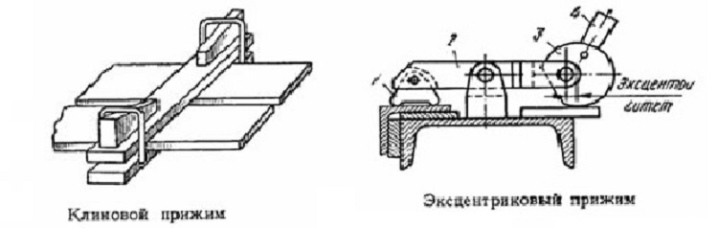
-
Распорки. Нужны для предотвращения деформационного расширения деталей. Их также используют при коррекции локальных дефектов, при придании нужной формы свариваемому изделию.
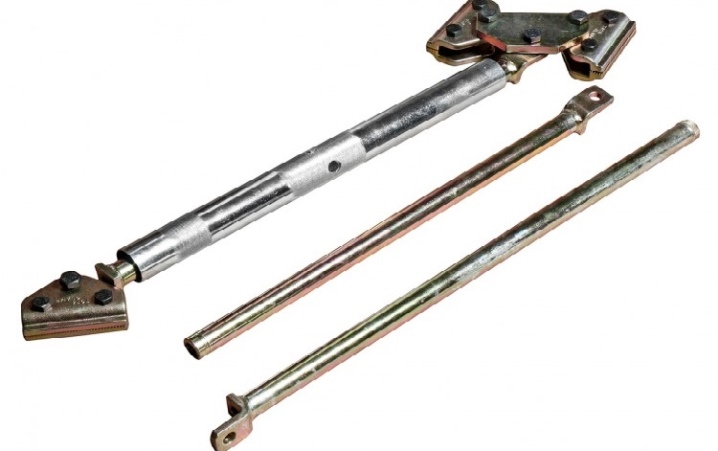
-
Стяжки. Этот элемент необходим для сведения кромок крупногабаритных свариваемых деталей. При помощи стяжек можно установить нужное расстояние, на котором будут удерживаться плоскости относительно друг друга. Длина и способ закрепления на поверхности конструкции варьируется, подбирается исходя из параметров детали.
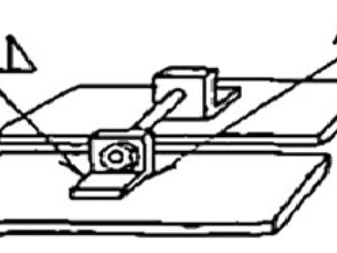
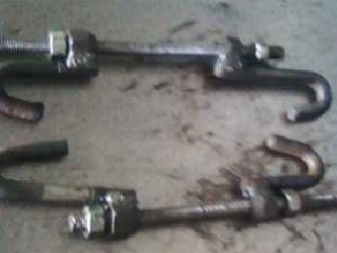
Крепежные приспособления, используемые при сварке, довольно просты в изготовлении. Часто мастера сами создают их из подручных материалов, особенно если работы ведутся не в оборудованном цехе, а в «полевых» условиях.
Универсальные варианты
Для того чтобы упростить и облегчить сварочный процесс, были созданы комплексы приспособлений, объединяющие в себе функции установочных и крепежных элементов. Такие универсальные решения удобны тем, что не требуют долгих и сложных расчетов, подгонки. Детали просто вставляются внутрь приспособления, затем их фиксируют эксцентриковым или винтовым креплением. Наиболее часто в готовом виде встречаются комплексы для сварки под прямым углом. Чтобы облегчить выемку детали по завершении сварочных работ, используется поворотно-зажимной элемент.
Универсальные приспособления часто называют комплексами для объемной сварки. Объединив установочные и закрепляющие функции, можно облегчить монтаж угловых соединений.
Трубные центраторы
К универсальным относятся и приспособления, используемые при сварке торцевой части труб. Они называются центраторы, при монтаже придают отрезкам правильное положение, помогают обеспечить их совпадение по оси, фиксируют детали в нужном положении, исключая их смещение. Выделяют наружные и внутренние разновидности таких конструкций. Чаще всего используется первый тип, не создающий сложностей при удалении по завершении сварки.
Для соединения кромок больших по диаметру труб используются звеньевые центраторы с шарнирно соединенными элементами, собранными в кольцо. Имеющиеся внутри упоры позволяют избежать смещения элементов в процессе работы. В домашних условиях более удобным решением становятся струбцинные центраторы, позволяющие обеспечить надежное скрепление труб малого диаметра.
Для каждого из популярных типоразмеров используется своя модель сварочного приспособления.
Приспособления на магнитах
К универсальным сборочно-сварочным изделиям можно отнести и магнитные приспособления. Они играют роль распорки, а также удерживают изделия из ферромагнитных сплавов в заданном положении. Наиболее часто встречаются угольники — разных форм, размеров, толщины. Некоторые имеют возможность изменения остроты угла. Такие приспособления довольно популярны при скреплении:
-
листовых деталей;
-
стоек;
-
рам.
Для соединения деталей разной конфигурации используются универсальные приспособления-магниты. Они гораздо более функциональные, имеют 2 плоскости-опоры, которые прикладываются к поверхности соединяемых деталей. Угол между ними легко меняется. Такие магнитные приспособления подходят для работы с цилиндрическими и плоскими элементами конструкций, а при помощи боковых площадок соединение легко можно дополнить вспомогательными сварными деталями.
Магниты в таком установочном крепежном блоке довольно мощные, чтобы обеспечить неподвижность конструкции при сварке. При этом их легко демонтировать по завершении работ. Сборочно-сварочные магнитные элементы существенно сокращают время, затрачиваемое на монтаж деталей между собой на подготовительном этапе. Они максимально просты в эксплуатации, долговечны, наравне с классическими зажимами и струбцинами, могут с уверенностью занять центральное место на домашнем верстаке.
Единственный их недостаток — возможность размагничивания под влиянием высоких температур.
Видеоролик:лик: https://yandex.ru/video/preview/?filmId=16715001731247291496&from=tabbar&text
Лекция № 3: Выбор режима сварки
Первый этап работы – это настроить режимы для сварки полуавтоматом в среде защитных газов. Для этого разберемся в основных составляющих полуавтомата.
Пройдемся по основным режимам, изучив которые вы без труда правильно настроите полуавтоматическую сварку, и не допустите досадных ошибок.
Начинаем с диаметра проволоки. Его размер может колебаться в промежутках от 0.5 до 3 миллиметров. Чаще всего размер проволоки выбирают в зависимости от размера материала, с которым вы будете работать.
Но, независимо от этого, у каждой толщины есть присущие ей особенности. К примеру, если вы хотите достичь более стойкое горение дуги и меньшее разбрызгивание металла, профессионалы рекомендуют работать с более тонкой проволокой.
Немаловажно учесть при процессе с толстым материалом – напряжение потребуется гораздо сильнее.
Обратите внимание – чтобы работать с низколегированной сталью обязательно использовать проволоку, в которой содержится марганец и кремний. Проволока должна быть с раскислителями. Тоже относится и к низкоуглеродистой стали.
К сожалению, частой ошибкой начинающих является как раз недостаточное внимание к фирме, которая изготавливает данный материал, а также металлам, которые входят в ее состав.
Все же стоит отметить, что сталь в среде защитного газа чаще всего легированная, или же высоколегированная. Выход в такой ситуации простой – нужно взять проволоку, которая сделана из того же материала, с которым вы работаете.
Это очень важно, ведь в случае ошибки шов будет непрочным, и это безусловно повлияет на весь результат работы.
Сила, полярность и род сварочного тока
После правильно подобранных материалов, следующим шагом будет настройка режима полуавтомата для работы в среде защитных газов. Эти три параметра – сила, род и полярность сварочного тока являются основными, и непременно присутствуют даже в дешевых образцах.
Давайте рассмотрим подробнее каждый из них. Силу напряжения настраивают, исходя их особенностей материала, с которым вы будете работать, и, конечно, диаметр электрода. В зависимости от силы тока меняется, например, глубина провара.
Поговорим про остальные два параметра. Самый распространенный среди мастеров высокого класса метод сваривания в среде защитного газа – задать такие параметры: постоянный ток и обратная полярность.
Сделайте вы наоборот – и получите весьма нежелательный результат в виде неустойчивого горения дуги и, как следствие, значительно ухудшите результат своей работы.
Следуя правилам, не забывайте и про исключения: если работаете с алюминием, ток необходим именно переменный.
Чтобы не попасться на удочку, как и все новички, обязательно обратите внимание на напряжение сварочной дуги. А ведь именно этот важный параметр обеспечивает нужную глубину провара металла и само сварочное соединение.
Для настройки ориентируйтесь на силу сварочного тока. Если металл разбрызгивается, а в материале появляются нежелательный поры, значит напряжение слишком большое, и защитный газ не сможет проникнуть в нужную зону.
Скорость подачи проволоки
На качество вышей работы влияет механизм. Который обеспечивает подачу проволоки. При полуавтоматический сварке это залог точной и слаженной работы.
Как только вы приступаете к свариванию, сразу же настройте этот параметр сварки полуавтоматом в среде защитных газов – не слишком быстро и не слишком медленно. Только это может гарантировать вам ровный и прочный шов.
Опять же, следует руководствоваться силой тока при настройке данного параметра. Нужно стремиться к тому, чтобы скорость подачи обеспечивала стойкость дуги и равномерное формирование тока.
Скорость сварки
Следующее – это скорость сварки. Она влияет в основном на физические характеристики вашего шва. Для этого существуют стандарты расчета режима сварки полуавтоматом в среде защитных газов, однако с опытом вы сможете регулировать ее самостоятельно, в зависимости от специфики металла и его размеры.
Так, чем толще ваш материал, тем выше должна быть скорость и уже шов. Но и чрезмерная спешка недопустима, и приведет только к тому, что электрод перестанет находиться в зоне защитного газа и просто окислится под влиянием кислорода.
Ну а медлительность – залог рыхлого и пористого шва.
Наклон электрода
Наконец, угол преткновения всех начинающих мастеров во время сварки – это угол наклона электрода. В основном все стараются держать электрод наиболее удобным методом, но это значительный промах, который непременно даст о себе знать.
Ведь это главным образом влияет на итоговый результат.
Какие есть варианты сваривания? В основном их два, рассмотрим каждый из них. Сварка углом вперед – так вы лучше видите края, но при этом хуже область свари. При этом глубина получается меньше.
Сварка углом назад же все наоборот – здесь необходимо руководствоваться спецификой процесса. Первый тип отлично подойдет для тонкого материала, а вот второй можно применять с материалом любой другой толщины.
Лекция № 4: Наплавка отдельных валиков в нижнем положении
Видео: https://www.youtube.com/watch?v=RXq6IqbZxMo
Лекция № 5: Техника сварки в вертикальном положениях шва
https://www.youtube.com/watch?v=VhWK7KU2Sg0 – сварка вертикальных швов.
https://yandex.ru/video/preview/?filmId=10245767367574129749&text- сварка горизонтальных швов
Лекция № 6: Техника сварки стыковых швов листовых конструкций.
https://yandex.ru/video/preview/?filmId=5333390472273081148&reqid=1595984710502032-376962305038492945400124-man2-5857&text – сварка стыков в нижнем положении
Лекций № 7: Наплавка дефектов под механическую обработку
Наплавка — это процесс нанесения при помощи сварки слоя металла на поверхность изделия. Путем наплавки получают изделия с износостойкими, кислотоупорными, жаростойкими, антифрикционными и тому подобными свойствами. Наплавку применяют при изготовлении новых и восстановлении изношенных деталей.
В настоящее время в промышленности используется большое количество различных видов наплавки.
Ручная дуговая наплавка. Наплавка выполняется металлическими плавящимися одиночными электродами, пучком электродов, лежачими пластинчатыми электродами, трубчатыми электродами, дугой прямого и косвенного действия и трехфазной дугой.
Наплавку электродами можно выполнять во всех пространственных положениях. Она выполняется путем последовательного наложения валиков, наплавляемых при расплавлении электрода, на поверхность изделия. Наплавляемая поверхность при этом должна быть чистой (зачищена до металлического блеска). Поверхность каждого наложенного валика и место для наложения следующего валика также тщательно зачищают от шлака, окалины и брызг.
Для получения сплошного монолитного слоя наплавленного металла каждый последующий валик должен перекрывать предыдущий на 1/3—1/2 своей ширины.
Толщина однослойной наплавки составляет 3 — 6 мм. Если необходимо наплавить слой толщиной более 6 мм, перпендикулярно первому наплавляют второй слой валиков. При этом первый слой валиков должен быть тщательно очищен от брызг, окалины, шлаковых включений и других загрязнений.
Дуговая наплавка под флюсом. По способу выполнения может быть автоматической или полуавтоматической, а по количеству применяемых проволок — одноэлектродной и многоэлектродной. Применяемые для наплавки под флюсом наплавочные проволоки по конструкции разделяют на сплошные XI порошковые, а по форме — на круглые и ленточные.
Дуговая наплавка в защитных газах вольфрамовым (неплавящимся) и проволочным металлическим (плавящимся) электродом. Для защиты дуги используют аргон, азот, водород и углекислый газ.
Производительность труда при наплавке оценивают массой или площадью (размерами) наплавленного металла.
Вибродуговая наплавка. Эта наплавка является разновидностью электрической дуговой наплавки металлическим электродом и выполняется путем вибрации электрода. Амплитуда вибрации находится в пределах от 0,75 до 1,0 диаметра электродной проволоки.
Электрошлаковая наплавка. Отличительной особенностью этого способа наплавки является высокая производительность, при которой могут быть достигнуты не только десятки, но и сотни килограммов наплавленного металла в час. Наплавка производится с принудительным формированием металла за один проход. Электроды применяются практически любого сечения: прутки, пластины и т. п. Глубину проплавления основного металла можно регулировать в широких пределах.
Наплавка открытой дугой. Для этой цели применяют порошковую проволоку с внутренней защитой, которая позволяет расширить область применения механизированной износостойкой наплавки. При наплавке этой проволокой применение флюса или защитного газа не требуется, поэтому способ отличается простотой и маневренностью и создается возможность восстановления деталей сложной формы, глубоких внутренних поверхностей, деталей малых диаметров и пр. В настоящее время имеются различные конструкции аппаратуры, а также разработана технология упрочения деталей широкой номенклатуры. Расход проволоки составляет 1,15—1,35 кг на 1 кг наплавленного металла. Производительность при полуавтоматической наплавке повышается в 2 — 3 раза по сравнению с наплавкой штучными электродами.
Плазменная наплавка. При плазменной наплавке источником тепла является высокотемпературная сжатая дуга, получаемая в специальных горелках. Большое применение получили плазменные горелки с дугой прямого действия, горящей между неплавящимся вольфрамовым электродом и наплавляемым изделием. Иногда применяют горелки комбинированного типа, в которых от одного Электрода одновременно горят две дуги — прямого и косвенного действия.
Присадочным материалом при этом способе наплавки служит проволока, лента, порошок и пр. Практический интерес представляет прежде всего наплавка с присадкой мелкозернистого порошка. В этом случае применяется плазменная горелка комбинированного типа. Порошок при помощи транспортирующего газа подается из питателя в горелку и там вдувается в дугу. За время пребывания в дуге большая часть порошка успевает расплавиться, так что на наплавляемую поверхность попадают уже капельки жидкого присадочного материала.
Область применения наплавки: различные прокатные валки сталепрокатных станов, перед запуском в эксплуатацию наплаваются новым слоем (проволокой ЗХ2В8); уплотнительные поверхности задвижек пара и воды наплавляются новыми хромоникелевым сплавом; поршни и штоки гидравлики горных машин наплавляются в процессе изготовления бронзовой (антифрикционной) проволокой Бр. КМЦ-3-1; крестовины железнодорожный путей; опорные ролики рольгангов, тележек, тракторов и экскаваторов (гусеничных); колеса мостовых кранов, штампы вырубные; выхлопные клапаны автомобильных двигателей (слоем Х20Н80Т - нихром); ножи плужных лемехов; детали экскаваторов и землесосов; засыпные аппараты доменных печей; режущий инструмент и т. д.
Наплавка износостойкими сплавами повышает твердость и износоустойчивость деталей. Применение наплавки снижает расход дорогих и дефицитных легированных сталей. Лучше всего наплавке поддаются углеродистые, содержащие не более 0,6% углерода, хромоникелевые и ванадиевые стали.
Марганцовистые, хромомолибденовые, кремнистые и другие стали, склонные к закалке и трещинам при нагреве, а также чугун труднее поддаются наплавке и требуют предварительного подогрева.
Для получения ровной хорошей наплавки, без трещин, отслоений и пор необходимо, чтобы наплавляемый сплав имел более низкую температуру плавления, чем основной металл, а коэффициент его линейного расширения был близок к таковому для основного металла. Имеет значение также и способ наплавки.
Для наплавки применяют зернистые и порошковые наплавочные смеси, литые сплавы в виде прутков, металлические электроды с легирующим покрытием, порошковую проволоку, керамические легирующие флюсы, трубчатые наплавочные электроды, стальную наплавочную проволоку.
Из износостойких сплавов нашли широкое применение следующие:
Сталинит М (ГОСТ 11546—65) порошкообразный применяют для наплавки электродуговым способом быстроизнашивающихся стальных и чугунных деталей. Химический состав сталинита М следующий (%): хрома 24—26, марганца 6—8,5, углерода 7—10, кремния до 3, ceры до 0,5, фосфора до 0,5, железа — остальное. Сталинит изготовляют из феррохрома марки ХР-6, ферромарганца марки МН-6, нефтяного кокса и чугунной стружки, смешивая их в пропорциях, обеспечивающих указанный выше химический состав порошка сталинита. Твердость наплавки сталинитом составляет не менее 75 HRA или 52 HRC. Насыпной вес сталинита должен быть в пределах 2,70—2,75 Г/см3.
Вокар — зернистая смесь измельченного вольфрама и углерода (из сахара). В структуре наплавки дает раствор высокотвердых карбидов вольфрама в железе. Это дорогой сплав, применяемый в основном для наплавки бурового инструмента. Твердость 1-го слоя 56—58, 2-го слоя — 61—63 HRC.
Для наплавки бурового инструмента применяют релиты — трубчато-зерновые сплавы ТЗ на основе вольфрама. Зерна релита содержат около 3% углерода, который с основной массой вольфрама (97%) образует карбиды WC и W2C. Наплавленный слой состоит из частиц карбидов вольфрама и связующего сплава углерод-железо-вольфрам. Твердость наплавленного слоя составляет 70—90 HRA в зависимости от способа наплавки.
В и с х о м — дешевый зернистый сплав, не содержащий вольфрама. Содержит 6% углерода, 15% марганца, 5% хрома, остальное— железо (чугунная стружка). Широко используется в сельхозмашиностроении для наплавки лемехов, плугов, дисков и зубьев борон и пр. Твердость наплавки 250—320 НВ.
Боридная порошковая смесь содержит 50% боридов хрома и 50% железного порошка. Дает хрупкий наплавленный слой. Применяется для наплавки деталей, работающих в условиях абразивного износа. Твердость наплавки 82—84 HRA.
Литые износостойкие сплавы имеют температуру плавления 1260—1300° С и представляют собой твердый раствор карбидов хрома в кобальте (стеллиты) или в никеле и железе (сормайты). Сплавы на железной основе более хрупки, но дешевле, чем сплавы на никелевой и кобальтовой основе. Стеллиты имеют большую вязкость, коррозионную стойкость и лучшие наплавочные свойства, чем сормайты. Литые сплавы применяют для наплавки инструмента, ножей для резки металла, штампов, конусов, загрузочных устройств доменных печей и других подобных деталей.
Сормайт № 1 не требует термообработки после наплавки и может обрабатываться резцом. Сормайт № 2 менее хрупок, чем сормайт № 1 и после отжига может обрабатываться резцом; после закалки приобретает высокую твердость.
При наплавке дают твердость (HRC): стеллит В2К—46-48; стеллит ВЗК—42-43; сормайт № 1-49-54; сормайт № 2-40-45. Литые сплавы применяются в прутках диаметром 5—6 мм, длиной 250 мм. Содержание серы и фосфора не должно превышать в сумме 0,08%.
деталей. Для наплавки прутковым сормайтом рекомендуется применять газовую или электродуговую наплавку, для порошкового — нагрев токами высокой частоты. Химический состав сормайта следующий (%): хрома 25—31, никеля 3— 5, углерода 2,5—3, кремния 2,8—3,5, марганца до 1,5, серы до 0,07, фосфора до 0,08, железа — остальное. Твердость поверхностного слоя наплавки сормайтом равна 73—74 HRA или 48—50 HRC.
ГОСТ 10051—62 предусматривает 25 типов наплавочных электродов, обеспечивающих твердость наплавленного слоя от 25 до 65 HRC. Этот ГОСТ устанавливает также химический состав наплавленного металла и соответствующее обозначение для электрода каждого типа, например, ЦН-5-ЭН-20Х12-40-5.0 расшифровывается так: ЦН-5 — марка электрода; буквы ЭН — электрод наплавочный; 20X12-40-5,0 обозначает содержание в наплавке в среднем 0,20% углерода, 12%) хрома, 40 HRC — твердость; 5 —диаметр проволоки в мм. Если в обозначении электрода стоит буква У, то цифра после нее обозначает содержание углерода в наплавке з десятых долях процента. Например, ЭН-У30Х23Р2С2ТГ-55 означает, что наплавка содержит: 0,3% углерода, 23% хрома, 2% бора, 2% кремния, 1% титана и марганца, твердость 55 HRC.
Широкое распространение получили наплавочные электроды Московского опытно-сварочного завода. Характеристика и области применения их указаны в табл. 31.
Для наплавки резцов, фрез и других инструментов применяют также электроды марок ЦИ-1М, ЦИ-1У, ЦИ-1Л, РК-2, дающие в наплавке металл типа быстрорежущей стали и допускающие термообработку для получения твердости до 62—65 HRC.
Электроды ЦИ-1М имеют стержень из проволоки Св-08А и покрытие следующего состава: 23% мела, 16% плавикового шпата, 1,5% графита, 1,5% ферромарганца, 1,5% ферросилиция, 10% феррохрома, 5,2% феррованадия, 40,3% ферровольфрама, 1% алюминия, 30—35% жидкого стекла к весу сухой смеси.
НАПЛАВКА ЗЕРНИСТЫХ И ПОРОШКОВЫХ СПЛАВОВ (дуговая) — ручная наплавка угольным электродом, состоящая в том, что зернистые и порошковые твердые сплавы (сталинит, вокар и т.п.) насыпают на наплавляемую поверхность слоем в несколько миллиметров, а затем расплавляют сварочной дугой, горящей между неплавящимся угольным или графитовым электродом и слоем сплава на детали. Этот способ рекомендуется для наплавки небольших поверхностей с высокой твердостью. Например, сплавом вокар наплавляют буровой инструмент для глубокого бурения нефтяных скважин. На рисунке показана схема наплавки режущей кромки ножа зернистым сплавом угольным электродом: 1 — графитовая или медная подкладка; 2 — слой зернистого сплава; 3 — угольный электрод; 4 — наплавляемая деталь.
Технологический процесс наплавки начинается с подготовки детали, для этого ее тщательно очищают от грязи, масла, краски. Рекомендуется поверхности, подлежащие наплавке, обжигать газовыми горелками. Применяют также промывку горячим раствором щелочи с последующей промывкой горячей водой, очистку стальной щеткой. Для предупреждения больших внутренних напряжений и образования трещин часто наплавляемые детали подогревают до температуры, зависящей от основного и наплавляемого металла. Технологические приемы и режимы наплавки зависят от формы и размеров деталей, также от толщины и требуемых свойств наплавляемого слоя.
Большое значение для качества наплавляемого слоя имеют доли участия основного и присадочного металлов в формировании слоя. Доля участия основного металла зависит от способа наплавки и особенно от режима. Например, при наплавке под флюсом влияние режима на качество наплавляемого слоя больше, чем при ручной наплавке покрытыми электродами, что объясняется большим проплавлением основного металла. Преимуществом наплавки порошковой проволокой (или лентой) является меньшая плотность тока, что обеспечивает меньшую глубину проплавления основного металла и, как следствие, меньшее перемешивание его с наплавляемым металлом.
При нанесении слоя в виде отдельных валиков должно быть обеспечено оптимальное перекрытие валиков: при ручной наплавке на 0,30…0,35ширины, а при автоматической и полуавтоматической на0,4… 0,5ширимы валика.
Ручную дуговую наплавку производят электродами диаметром стержня4…5 мм. Сварочный ток составляет160…250 А. Напряжение дуги —22…26 В. Наплавку производят короткой дугой постоянным током обратной полярности. При наплавке (особенно электродами ОЗН) перегрев наплавленного слоя не допускается. Для этого слой наплавляют отдельными валиками с полным последовательным охлаждением каждого валика.
Зернистые порошковые смеси наплавляют с помощью угольного электрода. На подготовленную поверхность насыпают тонкий слой флюса (прокаленной буры)толщиной0,2…0,3 мми слой порошковой смеси толщиной3…7 мм, шириной не более 50 мм. При большей ширине наплавляют несколько полос. Слой разравнивают и слегка уплотняют. Наплавку производят плавными поперечными движениями угольного электрода вдоль наплавляемой поверхности. Скорость перемещения должна обеспечивать сплавление наплавляемого сплава с основным металлом. Ток постоянный, прямой полярности. При диаметре электрода10… 16 мм сварочный ток составляет200…250 А при напряжении дуги24…28 В. Длину дуги поддерживают в пределах 4…8 мм.
Размеры электродов для наплавки
Эскиз электрода:
1 - стержень; 2 - участок перехода; 3 - покрытие; 4 - контактный торец без покрытия
Классификация электродов для наплавки (по ГОСТ 9466-95)
Условное обозначение электродов для наплавки поверхностных слоев с особыми свойствами -Н (индекс в условном обозначении)
По толщине покрытия электроды для наплавки подразделяются:
с тонким покрытием - М (D/d ≤ 1,20)
со средним покрытием - С (1,20 < D/d ≤ 1,45)
с толстым покрытием - Д (1,45 < D/d ≤ 1,80)
с особо толстым покрытием - Г ( D/d > 1,80),
где: D - диаметр покрытия, d - диаметр электрода, определяемый диаметром стержня.
По виду электродного покрытия наплавочные электроды подразделяются:
с кислым покрытием - А;
с основным покрытием - Б;
с целлюлозным покрытием - Ц;
с рутиловым покрытием - Р;
с покрытием смешанного вида - соответствующее двойное условное обозначение;
с прочими видами покрытий - П.
При наличии в составе покрытия железного порошка в количестве более 20 % к обозначению вида покрытия электродов добавляется буква Ж.
По допустимым пространственным положениям наплавки электроды подразделяются:
для всех положений - 1;
для всех положений, кроме вертикального сверху вниз - 2;
для нижнего, горизонтального на вертикальной плоскости и вертикального снизу вверх - 3;
для нижнего и нижнего в лодочку - 4
По роду и полярности применяемого при наплавке тока, по номинальному напряжению холостого хода используемого источника питания сварочной дуги переменного тока частотой 50 Гц электроды для наплавки подразделяются:
Цифрой 0 - электроды для наплавки только на постоянном токе обратной полярности.
Пример условного обозначения электродов для наплавки (на этикетках, в маркировке коробок, пачек и ящиков):
Электроды типа Э-11Г3 по ГОСТ 10051-75, марки ОЗН-300У, диаметром 4,0 мм, для наплавки поверхностных слоев с особыми свойствами Н, с толстым покрытием Д, обеспечивающие среднюю твердость 300HB (HRCэ 33;
300HV) - 300/33, без термической обработки после наплавки - 1, с основным покрытием Б, для наплавки в нижнем положении 4на постоянном токе обратной полярности (0):
листовых деталей;
стоек;
рам.
| Э-11Г3-ОЗН-300У-4,0-НД | | ГОСТ 9466-75, ГОСТ 10051-75 |
| Е-300/33-1-Б40 | |
В документации: Электроды ОЗН-300У-4,0 ГОСТ 9466-75.
Наплавочная проволока - это горячекатаная и холоднотянутая проволока из углеродистой, легированной и высоколегированной стали, предназначенная для механизированной электродуговой наплавки. Она служит для наплавки на поверхность металлических изделий с целью их укрепления, особенно при действии неравномерных нагрузок. Применение наплавочной проволоки позволяет сэкономить, поскольку приобретать в таком случае дорогое изделие из высокопрочного металла не придется, нужно лишь периодически менять наплавку, когда поверхность будет изнашиваться. Проволока используется для укрепления строительных элементов, различных машин, детали которых подвергаются абразивному износу.
Производится данная проволока методом холодной прокатки либо горячей деформации. Первым способом изготавливаются более тонкие изделия диаметром до 7 мм, горячим — 7-8 мм. Производство проволоки данного типа регулируется ГОСТ 10543-98.
Различные виды проволоки наплавляемой могут выдерживать эксплуатацию в агрессивной среде, в том числе при высокой температуре, устойчивы к механическому воздействию. Технологические характеристики наплавляемой проволоки (НП) отражены в ее маркировке.
Условное обозначение марки проволоки состоит из индекса Нп (наплавочная); следующие за индексом Нп цифры указывают среднюю массовую долю углерода в сотых долях процента. Цифры, следующие за буквенными обозначениями химических элементов, указывают среднюю массовую долю элемента в процентах. Отсутствие цифр за буквенными обозначениями указывает, что их содержание не превышает 0,5 %. Химические элементы, содержащиеся в металле проволоки, обозначены: В - вольфрам, Г - марганец, М - молибден, Н - никель, С - кремний, Т - титан, Ф - ванадий, X - хром, Б - ниобий. Буква А указывает на повышенную чистоту металла проволоки по содержанию серы и фосфора.
Видео: https://www.youtube.com/watch?v=_xllqLfy3Ts – электроды для наплавки
https://www.youtube.com/watch?v=_n6ryscIKoY – наплавка валиков
Лекция № 8: