Файл: 1. Сущность токарной обработки. Основные виды токарных работ.docx
Добавлен: 25.10.2023
Просмотров: 106
Скачиваний: 7
ВНИМАНИЕ! Если данный файл нарушает Ваши авторские права, то обязательно сообщите нам.
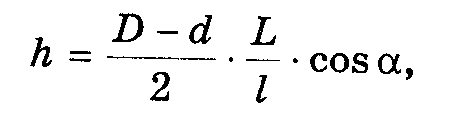
где L — общая длина обрабатываемой заготовки, мм.
Способ обработки конических поверхностей с помощью конусной линейки (рис.11, г), прикрепляемой к станине станка, позволяет получать коническую поверхность с углом при вершине до 40°. Обработка ведется с включением механической подачи.
В зависимости от формы и размеров заготовок применяют различные способы их закрепления. При отношении длины заготовки к диаметру L/D < 4 заготовку закрепляют в патроне. При 4
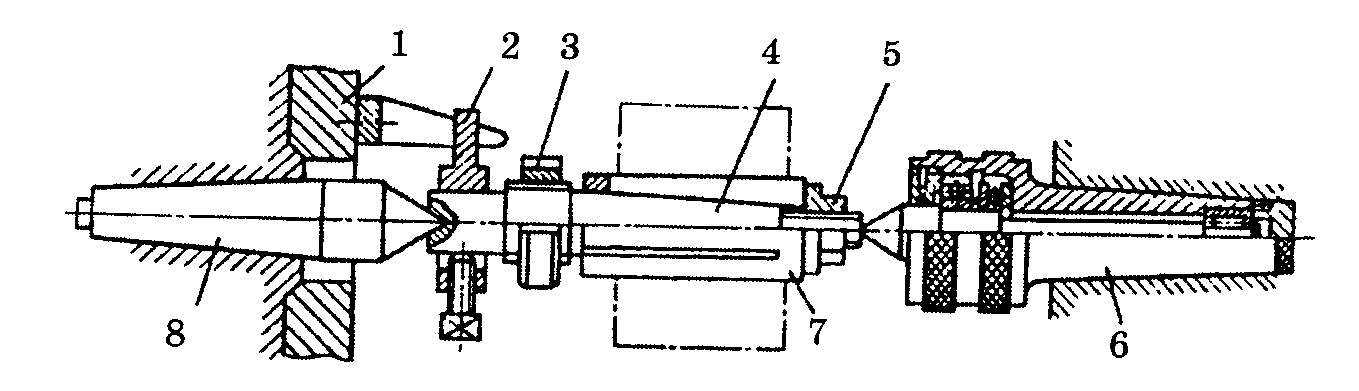
Рис.12. Обработка в центрах: 1 -поводковый патрон, 2 — хомутик, 3 - гайка, 4 -стержень, 5 -гайка, 6 - вращающийся центр, 7 - втулка, 8 - передний центр
Распространенным способом является обработка в центрах (рис. 12), так как она позволяет переставлять деталь со станка на станок без последующей выверки. При этом в торцах обрабатываемой детали предварительно засверливают центровые отверстия. Форма и размеры центровых отверстий (рис.12) стандартизованы. При установке на станке в эти отверстия входят острия центров передней и задней бабок станка. Для передачи вращения от шпинделя передней бабки к обрабатываемой детали применяют поводковый патрон 1 (рис.12), устанавливаемый на шпинделе, и хомутик 2, закрепленный на заготовке.
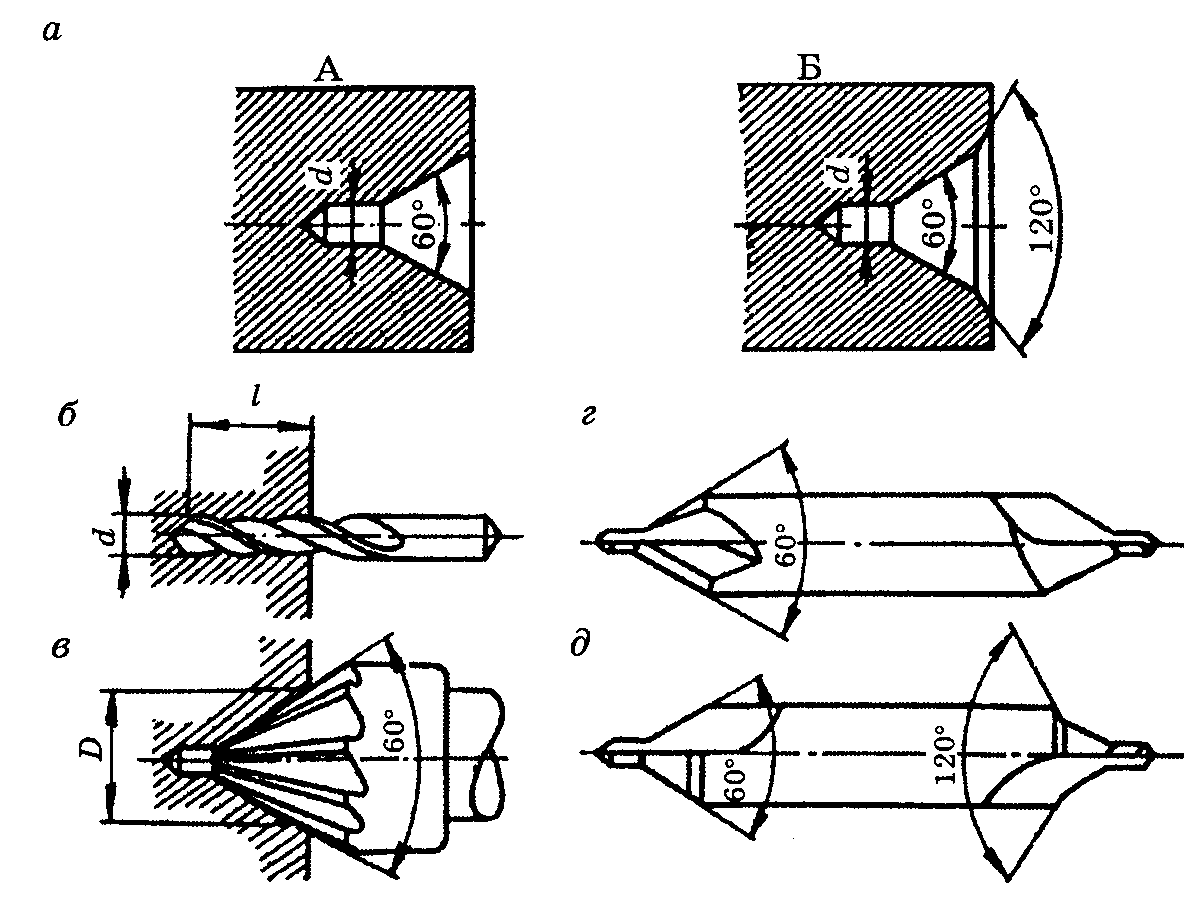
Рис.13. Центровые отверстия (а) и инструмент (б) — цилиндрическое сверло, (в) — зенковка, (г,д) — комбинированые сверла
Центры устанавливаются в шпинделе станка и пиноли задней бабки. Центр, установленный в шпинделе, вращается вместе с заготовкой. Простой центр (рис.13, а), установленный в пиноли задней бабки, не вращается, поэтому изнашивается сам и изнашивает центровое отверстие заготовки. Для предотвращения износа применяют вращающийся центр Иногда используют: срезанный центр при подрезке торца; обратный центр (рис13, б) при обтачивании заготовок небольшого диаметра (до 5 мм).
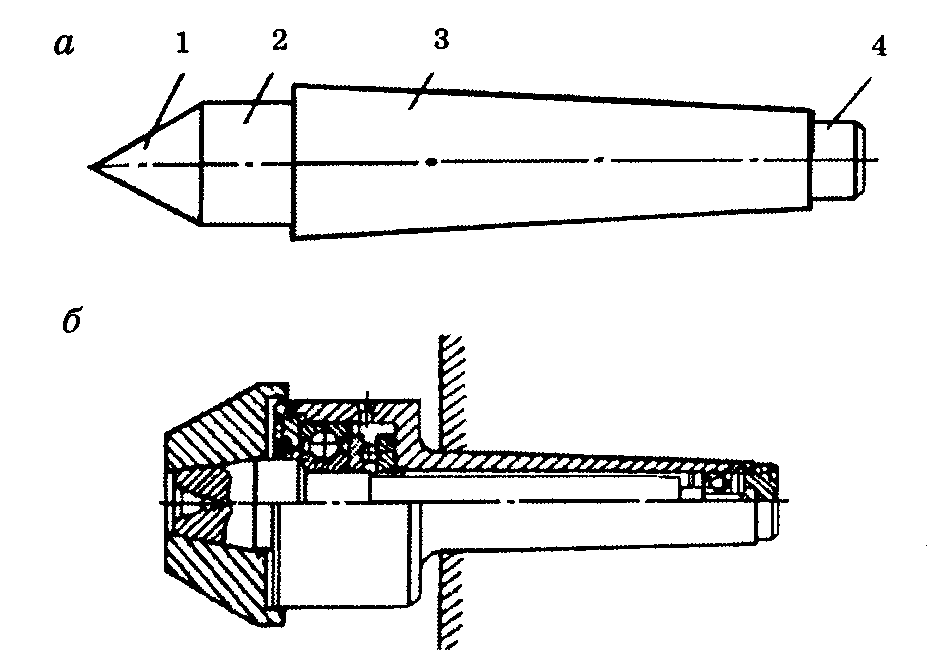
Рис.14. Токарные центры: а — простой центр (1 — конус, 2 — шейка, 3 — конус, 4 — хвостовик); б — обратный центр
2. Обработка конструкционных материалов на малогабаритном широкоуниверсальном станке
Назначение и область применения станка
Малогабаритный широкоуниверсальный станок мод.ЕРТ03 (ЕРТ03-1) предназначен для различных видов механической обработки деталей из металлов, пластмасс и древесины. Отличительной особенностью станка модели ЕРТ03 (ЕРТ03-1) является возможность переналадки базового токарного варианта в различные горизонтально-вертикально-фрезерные сверлильные и деревообрабатывающие наладки. На станке можно выполнять токарные, резьбонарезные, сверлильно-расточные и фрезерные операции. Дополнительные приспособления и оснастка дают возможность проводить на станке и такие операции как отрезка, распиловка, прорезка пазов, строгально-фуговальные операции при обработке древесины, а также зачистка, шлифование и полирование поверхностей деталей, заточка инструмента.
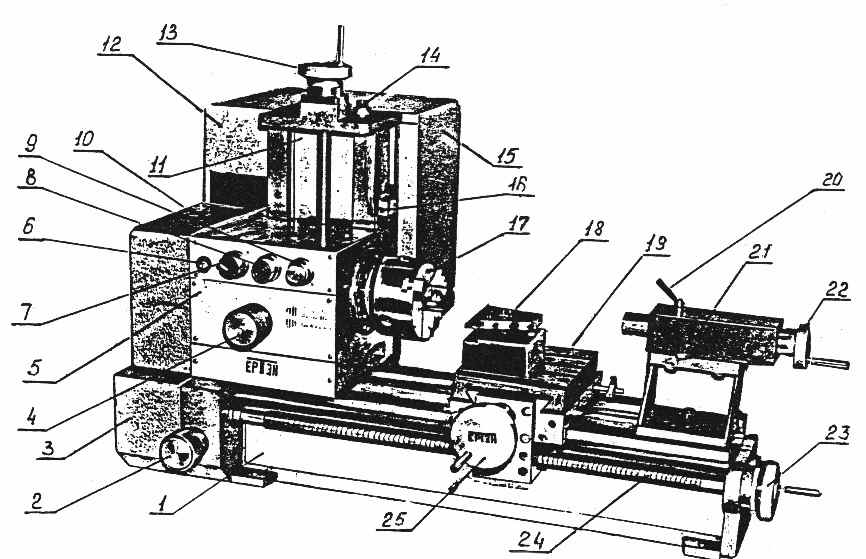
Рис.15. Малогабаритный широкоуниверсальный станок мод.ЕРТ03 (ЕРТ03-1)
Основные узлы и органы управления станком (рис. 2.1.):
1 - основание (станина) станка;
2 - рукоятка включения механической продольной подачи;
3 - крышка гитары сменных зубчатых колес продольной подачи (коробка подач);
4 - рукоятка переключения диапазонов (А и Б) частот вращения шпинделя ;
5 - шпиндельная коробка;
6 - индикатор включения электрооборудования;
7 - рукоятка включения прямого или обратного вращения шпинделя;
8 - кнопка «пуск» включения блока электрооборудования станка;
9 - кнопка «стоп» для выключения блока электрооборудования станка)
10 - крышка шпиндельной коробки;
11 - стойка вертикального перемещения шпиндельной коробки с подвижной кареткой;
12 - крышка блока электрооборудования станка;
13 - маховик вертикального перемещения шпиндельной коробки;
14 - винт вертикального перемещения стойки;
15 - кожух ограждения электродвигателя и блока электрооборудования станка;
16 - болт крепления каретки на стойке вертикального перемещения шпиндельной коробки;
17 - трех кулачковый патрон;
18 - резцедержка;
19 - суппорт;
20 - рукоятка зажима пиноли задней бабки;
21 - задняя бабка;
22 - маховик перемещения пиноли задней бабки;
23 - маховик ручного продольного перемещения суппорта;
24 - ходовой винт продольного перемещения суппорта;
25 - маховик поперечного перемещения стола суппорта.
Основные технические характеристики станка
Наибольшие размеры обрабатываемого изделия, мм: | |
- в центpax (диаметр х длина) | 105 х 440 (105х220) |
- в патроне (диаметр над суппортом) | 230 |
- на столе (длина х ширина х высота) | 140 х 160 х 180 |
Наибольший диаметр устанавливаемого изделия | |
на планшайбе или в патроне, мм | 600 |
Наибольший диаметр сверления, мм | 10 |
Диаметр отверстия в шпинделе, пинали задней | Конус Морзе 2 АТ6 |
бабки и вертикально-фрезерной головки | (ГОСТ 2848-75) |
Наибольшие перемещения рабочих органов, мм: | |
- продольное суппорта при точении | 440 (220) |
- продольное суппорта при фрезеровании | 600 (480) |
- поперечное суппорта | 100 |
- вертикальное шпиндельной коробки | 180 |
- пиноли задней бабки | 50 |
Наибольшие наладочные перемещения стойки, мм: | |
- вертикальное | 80 |
- горизонтальное | 420 |
Наибольший ход зажимных губок тисок, мм | 100 |
Поворот резцедержки, град. | 90 х 4 |
Наибольшие размеры деревообработки, mmi | |
- толщина распиловки (дисковой пилой) | 35 |
- ширина фугования | 100 |
Наибольший ход вертикального стола, мм | 100 |
Наибольший ход подвижной резцедержки, мм | 70 |
Угол поворота подвижной резцедержки, град | 45 |
Наибольший угол поворота вертикально-фрезерной головки, град | 45 |
Количество ступеней частот вращения шпинделя | 6 |
Диапазон частот вращения шпинделя, 1/мин. | 160...2500 |
Продольная механическая подача, мм/об. | 0,1… 0,16 |
Шаг нарезаемых резьб: | |
- метрических, мм | 0,5...2,5 |
- дюймовых, п/1» (ниток на дюйм) | 10...20 |
Цена деления лимба маховика, мм | |
- суппорта, шпиндельной коробки и продольной подачи | 0,02 |
- пиноли задней бабки | 0,04 |
Мощность электродвигателя, квт | 0,37 |
Питание электрооборудования | Однофазное, 220B; 50 Гц |
Габарит станка (длина х ширина х высота), мм | 1120х680х640 |
Масса (без оснастки и инструмента), кг | 160 |
3. Правила эксплуатации токарных станков.
Типовые отказы и методы их устранения. Основными факторами, определяющими эксплуатацию токарных станков являются: вращающиеся станочные приспособления (патроны) и заготовки, а также образующаяся в процессе резания стружка. При работе с высокими скоростями резания особое внимание должно быть уделено правильному и надежному закреплению заготовок. Отказы при точении и способы их устранения. Точность при чистовых видах точения может достигать 7-8-го квалитета, а шероховатость обработанной поверхности — 1,6-3,2 мкм. Разрезание заготовок на токарных станках выполняют отрезными резцами, которые по конструктивному исполнению могут быть прямыми и обратными. Прямые отрезные резцы имеют длинную и узкую головку для прорезания заготовки до центра с наименьшим расходом материала в стружку. Однако, они обладают недостаточной прочностью и жесткостью, что следует учитывать при их исполнении. Поэтому место реза должно быть как можно ближе к кулачкам патрона, на расстоянии не более одного диаметра заготовки. Отрезной резец устанавливают строго на уровне линии центров станка и перпендикулярно к оси заготовки.
При разрезании заготовок больших диаметров возможна поломка резца в конце прохода в результате того, что тонкая перемычка под действием сил тяжести и резания прогибается и отрезной резец защемляется в прорези. В этом случае необходимо, не доходя до центра примерно 1,5-2,0 мм, вывести резец из прорези, выключить вращение шпинделя и отпилить отрезаемую часть вручную. Запрещается поддерживать руками в процессе резания отрезаемую часть заготовки. Выход стружки из узкой и глубокой прорези сильно затруднен. В этом случае разрезание следует выполнять поочередным расширением прорези.
Перед сверлением, зенкерованием или развертываньем токарный станок следует тщательно выверить на соосность центров.
Важными условиями операции сверления являются; прочное закрепление заготовки, перпендикулярность ее торца оси вращения, отсутствие на торце выпуклостей, задание первоначального направления сверлу. Для этого заготовку в станочном приспособлении устанавливают с возможно наименьшим вылетом, а торец перед сверлением гладко подрезают. Для задания первоначального направления сверлу в центре торца делают углубление центровочным сверлом или коротким жестким сверлом; глубина сверления приблизительно должна быть равной диаметру получаемого отверстия.
Сверление отверстий большого диаметра с ручной подачей затруднено из-за необходимости приложения со стороны токаря больших усилий. Поэтому отверстия диаметром свыше 20 мм следует обрабатывать последовательно двумя сверлами. Диаметр первого сверла выбирают примерно равным половине диаметра получаемого отверстия. Благодаря этому перемычка второго сверла не участвует в резании и, соответственно, усилие подачи значительно снижается.
Опиливание применяют для зачистки поверхностей, удаления заусенцев, снятия небольших фасок и т.п. Его выполняют напильниками разнообразной формы и с различной насечкой. Применять можно только напильники с целой и плотно насаженной ручкой. Так как опиливание производят вручную, то для предотвращения травмирования, токарь должен стоять примерно под углом 45° к оси центров станка с разворотом вправо. Ручку напильника следует зажимать в левой руке, а противоположный его конец удерживать пальцами правой.
Полирование применяют для снижения шероховатости обработанных поверхностей. Его осуществляют шлифовальными шкурками различной зернистости. Во время полирования шкурку удерживают пальцами либо правой руки, либо обеих рук. В последнем случае токарь должен располагаться у станка так же, как и при опиливании, то есть передний конец шкурки удерживать левой рукой, а противоположный — правой.
Удерживать шкурку на детали путем охвата ее рукой нельзя, так как она может намотаться на деталь и защемить пальцы руки.
Обычно в суппорте токарного станка закрепляют одновременно несколько резцов, поэтому при опиливании и полировании следует остерегаться порезов рук острыми кромками резцов, а также при повороте резцовой головки, осуществлении измерений.
Заключение
По итогам проведённого исследования необходимо отметить, что цели и задачи, поставленные нами в начале исследования, выполнены.
Обработка на металлорежущих станках является наиболее распространенным методом формообразования поверхности твердых тел с высокой точностью размеров и низкой шероховатостью. Например, в общей трудоемкости радиотехнических изделий бортового оборудования 20 - 35 % составляет трудоемкость механической обработки. В настоящее время проводится политика замены предварительных операций обработки резанием на более высокопроизводительные методы (обработка давлением, точное литье и др.), чтобы на металлорежущих станках проводить только заключительные операции по изготовлению деталей РЭС с целью дальнейшего снижения затрат труда и материалов на производство РЭС.
На токарных станках производится обработка наружных и внутренних цилиндрических, конических, фасонных поверхностей, торцевых плоскостей; нарезка резьбы внутренней и наружной резцами, метчиками и плашками; обрабатываются отверстия сверлами, зенкерами, развертками; накатывается рельеф и мелкомодульные зубчатые колеса и другое.
Таким образом, токарная обработка является одним из самых универсальных видов обработки. Этим методом можно получать детали любой формы при любых требованиях к чистоте и точности обрабатываемых поверхностей. Однако универсальность токарной обработки (универсальные методы, универсальное оборудование) способствует увеличению стоимости изготовления, т.к. многие операции требуют ручного труда высокой квалификации.
Список использованной литературы
1. Бергер И.И. Токарное дело. – М.: Высш. шк.., 1990. – 314 с.
2. Брунштейн Б.Е.; Дементьев В.И. Токарное дело, М.: Высшая школа, 1987.
3. Зайцев Б.Г., Завгороднев П.И., Справочник молодого токаря, М.: Высшая школа, 1976.
4. Захаров В.А., Чистоклетов А.С., Токарь, М.: Машиностроение, 1999.
5. Оглобин А.Н. Основы токарного дела, М.: Машиностроение, 1997.
6. Лакирев С.Г. Обработка отверстий: Справочник.- М.: Машиностроение., 2004. - 208 с.
7. Тишенина Т.И.; Фёдоров Б.В. Токарные станки и работы на них. - М.: Машиностроение, 2002.10>