Файл: Визуальный и измерительный контроль сварных соединений.docx
ВУЗ: Не указан
Категория: Не указан
Дисциплина: Не указана
Добавлен: 06.11.2023
Просмотров: 39
Скачиваний: 1
ВНИМАНИЕ! Если данный файл нарушает Ваши авторские права, то обязательно сообщите нам.
Практическое занятие № 1
Тема: Визуальный и измерительный контроль сварных соединений
Цель работы: Ознакомление с неразрушающими методами контроля качества сварных соединений, применяемыми приборами и инструментами.
Этапы занятия:
-
Ознакомиться с теоретическим материалом. -
Заполнить таблицу 1.
Теоретическая часть
Сварные соединения подвергают проверке для определения возможных отклонений от технических условий, предъявляемых данному виду изделий. Изделие считается качественным, если отклонения не превышают допустимые нормы. В зависимости от вида сварных соединений и условий дальнейшей эксплуатации, изделия после сварки подвергают соответствующему контролю.
Контроль сварных соединений может быть предварительным, когда проверяют качество исходных материалов, подготовку свариваемых поверхностей, состояние оснастки и оборудования. К предварительному контролю относят также сварку опытных образцов, которые подвергают соответствующим испытаниям. При этом в зависимости от условий эксплуатации опытные образы подвергают металлографическим исследованиям и неразрушающим или разрушающим методам контроля.
Под текущим контролем понимают проверку соблюдения технологических режимов, стабильность режимов сварки. При текущем контроле проверяют качество наложения послойных швов и их зачистку. Окончательный контроль осуществляют в соответствии с техническими условиями. Дефекты, обнаруженные в результате контроля, подлежат исправлению.
НЕРАЗРУШАЮЩИЕ МЕТОДЫ КОНТРОЛЯ СВАРНЫХ СОЕДИНЕНИЙ
Существует десять неразрушающих методов контроля сварных соединений, которые применяют в соответствии с техническими условиями. Вид и количество методов зависят от технической оснащенности сварочного производства и ответственности сварного соединения.
Внешний осмотр — наиболее распространенный и доступный вид контроля, не требующий материальных затрат. Данному контролю подвергают все виды сварных соединений, несмотря на использование дальнейших методов. При внешнем осмотре выявляют практически все виды наружных дефектов. При этом виде контроля определяют непровары, наплывы, подрезы и другие дефекты, доступные обозрению. Внешний осмотр выполняют невооруженным глазом или используют лупу с 10-ти кратным увеличением. Внешний осмотр предусматривает не только визуальное наблюдение, но и обмер сварных соединений и швов, а также замер подготовленных кромок. В условиях массового производства существуют специальные шаблоны, позволяющие с достаточной степенью точности измерить параметры сварных швов.
В условиях единичного производства сварные соединения обмеряют универсальными мерительными инструментами или стандартными шаблонами, пример которых приведен на рис.1.
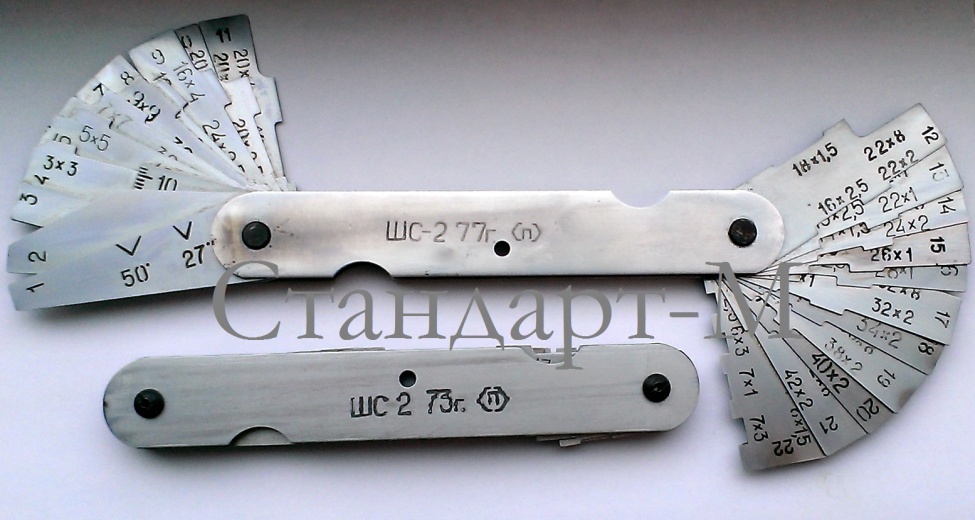
Рис.1 Набор шаблонов ШС-2
Набор шаблонов ШС-2 представляет собой комплект стальных пластинок одинаковой толщины, расположенных на осях между двумя щеками. На каждой из осей закреплено по 11 пластин, которые с двух сторон поджимаются плоскими пружинами. Две пластины предназначены для проверки узлов разделки кромок, остальные — для проверки ширины и высоты шва. С помощью этого универсального шаблона можно проверять углы разделки кромок, зазоры и размеры швов стыковых, тавровых и угловых соединений.
Непроницаемость емкостей и сосудов, работающих под давлением, проверяют гидравлическими и пневматическими испытаниями. Гидравлические испытания бывают с давлением, наливом или поливом водой. Для испытания наливом сварные швы сушат или протирают насухо, а емкость заполняют водой так, чтобы влага не попала на швы. После наполнения емкости водой все швы осматривают, отсутствие влажных швов будет свидетельствовать об их герметичности.
Испытаниям поливом подвергают громоздкие изделия, у которых есть доступ к швам с двух сторон. Одну сторону изделия поливают водой из шланга под давлением и проверяют герметичность швов с другой стороны.
При гидравлическом испытании с давлением сосуд наполняют водой и создают избыточное давление, превышающее в 1,2 —2 раза рабочее давление. В таком состоянии изделие выдерживают в течение 5 — 10 минут. Герметичность проверяют по наличию влаги наливах и величине снижения давления. Все виды гидравлических испытаний проводят при положительных температурах.
Пневматические испытания в случаях, когда невозможно выполнить гидравлические испытания. Пневматические испытания предусматривают заполнение сосуда сжатым воздухом под давлением, превышающим на 10-20 кПа атмосферное или 10 - 20% выше рабочего. Швы смачивают мыльным раствором или погружают изделие в воду. Отсутствие пузырей свидетельствует о герметичности. Существует вариант пневматических испытаний с гелиевым течеискателем. Для этого внутри сосуда создают вакуум, а снаружи его обдувают смесью воздуха с гелием, который обладает исключительной проницаемостью. Попавший внутрь гелий отсасывается и попадает на специальный прибор — течеискатель, фиксирующий гелий. По количеству уловленного гелия судят о герметичности сосуда. Вакуумный контроль проводят тогда, когда невозможно выполнить другие виды испытаний.
Герметичность швов можно проверить керосином. Для этого одну сторону шва при помощи пульверизатора окрашивают мелом, а другую смачивают керосином. Керосин имеет высокую проникающую способность, поэтому при неплотных швах обратная сторона окрашивается в темный тон или появляются пятна.
Химический метод испытания основан на использовании взаимодействия аммиака с контрольным веществом. Для этого в сосуд закачивают смесь аммиака (1%) с воздухом, а швы проклеивают лентой, пропитанной 5%-ным раствором азотнокислой ртути или раствором фенилфталеина. При утечках цвет ленты меняется в местах проникновения аммиака.
Магнитный контроль. При этом методе контроля дефекты швов обнаруживают рассеиванием магнитного поля. Для этого к изделию подключают сердечник электромагнита или помещают его внутрь соленоида. На поверхность намагниченного соединения наносят железные опилки, окалину и т.д., реагирующие на магнитное поле. В местах дефектов на поверхности изделия образуются скопления порошка, в виде направленного магнитного спектра. Чтобы порошок легко перемещался под воздействием магнитного поля, изделие слегка постукивают, придавая мельчайшим крупинкам подвижность. Поле магнитного рассеивания можно фиксировать специальным прибором, называемым магнитографическим дефектоскопом. Качество соединения определяют методом сравнивания с эталонным образцом. Простота, надежность и дешевизна метода, а главное его высокая производительность и чувствительность позволяют использовать его в условиях строительных площадок, в частности при монтаже ответственных трубопроводов.
Радиационный контроль позволяет обнаружить в полости шва дефекты, невидимые при наружном осмотре. Сварной шов просвечивают рентгеновским или гамма-излучением, проникающим через металл (рис.2), для этого излучатель (рентгеновскую трубку или гамма-установку) размещают напротив контролируемого шва, а с противоположной стороны - рентгеновскую пленку, установленную в светонепроницаемой кассете.
![]() | ![]() |
Рис. 1. Измерение разделки кромок, зазоров и размеров швов шаблоном ШС-2 | Рис. 2. Радиационный контроль: А — рентгеновское излучение; Б — гамма-излучение: 1 — экраны усиливающие; 2 — рентгеновская пленка; 3 — кассета; 4 — рентгеновское излучение; 5 — рентгеновская трубка; 6 — гамма-излучение; 7 — свинцовый кожух; 8 — ампула радиоактивного вещества. |
Лучи, проходя через металл, облучают пленку, оставляя в местах дефектов более темные пятна, так как дефектные места обладают меньшим поглощением. Рентгеновский метод более безопасен для работающих, однако его установка слишком громоздка, поэтому он используется только в стационарных условиях. Гамма-излучатели обладают значительной интенсивностью и позволяют контролировать металл большей толщины. Благодаря портативности аппаратуры и дешевизне метода этот тип контроля широко распространен в монтажных организациях. Но гамма-излучение представляет большую опасность при неосторожном обращении, поэтому пользоваться этим методом можно только после соответствующего обучения. К недостаткам радиографического контроля относят тот факт, что просвечивание не позволяет выявить трещины, расположенные не по направлению основного луча.
Наряду с радиационными методами контроля применяют рентгеноскопию, то есть получение сигнала о дефектах на экране прибора. Этот метод отличается большей производительностью, а его точность практически не уступает радиационным методам.
Ультразвуковой метод (рис.3) относится к акустическим методам контроля, обнаруживающим дефекты с малым раскрытием: трещины, газовые поры и шлаковые включения, в том числе и те, которые невозможно определить радиационной дефектоскопией. Принцип его действия основан на способности ультразвуковых волн отражаться от границы раздела двух сред. Наибольшее распространение получил пьезоэлектрический способ получения звуковых волн. Этот метод основан на возбуждении механических колебаний при наложениях переменного электрического поля в пьезоэлектрических материалах, в качестве которых используют кварц, сульфат лития, титанат бария и др.
Для этого с помощью пьезометрического щупа ультразвукового дефектоскопа, помещаемого на поверхность сварного соединения, в металл посылают направленные звуковые колебания. Ультразвук с частотой колебаний более 20 000 Гц вводят в изделие отдельными импульсами под углом к поверхности металла. При встрече с границей раздела двух сред ультразвуковые колебания отражаются и улавливаются другим щупом. При однощуповой системе это может быть тот же щуп, который подавал сигналы. С приемного щупа колебания подаются на усилитель, а затем усиленный сигнал отражается на экране осциллографа. Для контроля качества сварных швов в труднодоступных местах в условиях строительных площадок используют малогабаритные дефектоскопы облегченной конструкции.
К преимуществам ультразвукового контроля сварных соединений относят: большую проникающую способность, позволяющую контролировать материалы большой толщины; высокую производительность прибора него чувствительность, определяющую местонахождение дефекта площадью 1 — 2 мм2. К недостаткам системы можно отнести сложность определения вида дефекта. Поэтому ультразвуковой метод контроля иногда применяют в комплексе с радиационным.
| ![]() | |
Рис. 3. Схема ультразвукового контроля: 1 — генератор ультразвуковых колебаний; 2 —пьезоэлектрический щуп; 3 — усилитель; 4 — экран дефектоскопа. |
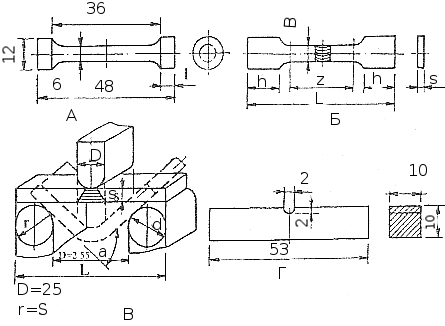
Рис. 4. Варианты образцов для определения механических свойств (размеры в мм):
А —Б — на растяжение наплавленного металла (А) и сварного соединения (Б);
В — на изгиб; Г — на ударную вязкость.
Устранение дефектов сварки
Выявленные в процессе контроля дефекты сварки, которые не соответствуют техническим условиям, должны быть устранены, а если это невозможно, изделие бракуют. В стальных конструкциях снятие бракованных сварных швов осуществляют плазменно-дуговой резкой или строжкой с последующей обработкой абразивными кругами.
Дефекты в швах, подлежащих термической обработке, исправляют после отпуска сварного соединения. При устранении дефектов следует соблюдать определенные правила:
-
длина удаляемого участка должна быть с каждой стороны длиннее дефектного участка; -
ширина разделки выборки должна быть такой, чтобы ширина шва после заварки не превышала его двойную ширину до заварки. -
профиль выборки должен обеспечивать надежность провара в любом месте шва; -
поверхность каждой выборки должна иметь плавные очертания без резких выступов, острых углублений и заусенцев; -
при заварке дефектного участка должно быть обеспечено перекрытие прилегающих участков основного металла.
После заварки участок зачищают до полного удаления раковин и рыхлости в кратере, выполняют плавные переходы к основному металлу. Удаление заглубленных наружных и внутренних дефектных участков в соединениях из алюминия, титана и их сплавов следует выполнять только механическим способом — шлифовкой абразивными инструментами или резанием. Допускается вырубка с последующей шлифовкой.