Добавлен: 07.11.2023
Просмотров: 583
Скачиваний: 28
ВНИМАНИЕ! Если данный файл нарушает Ваши авторские права, то обязательно сообщите нам.
В состав Октябрьской ЛПУМГ входят: газокомпрессорная служба, линейно-эксплуатационная служба, служба по ремонту и надзору за строительством, диспетчерская служба, служба защиты коррозии, служба автоматизации и метрологии, группа по охране природы и лабораторному контролю, служба связи, служба энерговодоснабжения, группа материально – технического обеспечения и складского хозяйства, подразделение культурно-бытового назначения (спортивный комплекс, санаторий и прочее).
-
Обзор, характеристика и технология проведения обследований ЛЧМГ, методы проведения контроля.
На текущий момент общая протяженность газопроводов ООО «Газпром тансгаз Югорск» составляет более 27,7 тыс. км.
Гидравлическое состояние газопроводов удовлетворительное. Коэффициент гидравлической эффективности участков газопроводов, оборудованных КП и КЗ очистных устройств, не ниже 0,95.
Отказы, аварии и инциденты в 2021г. на газопроводах Октябрьского ЛПУМГ отказов, аварий и инцидентов не зафиксировано. Поданным отчетности Октябрьского ЛПУМГ за 2020г. капитального ремонт магистральных газопроводов выполнен в объеме 13,36 километра (99% от плана), в т.ч. переизоляция (13,36 км.), замена труб (1,1 км.), устранено 756 дефектов выявленных по результатам внутри трубной диагностики.
На рисунке 2.1. представлен фрагмент капитального ремонта – полная замена части трубы с целью устранения выявленных дефектов ВТД.
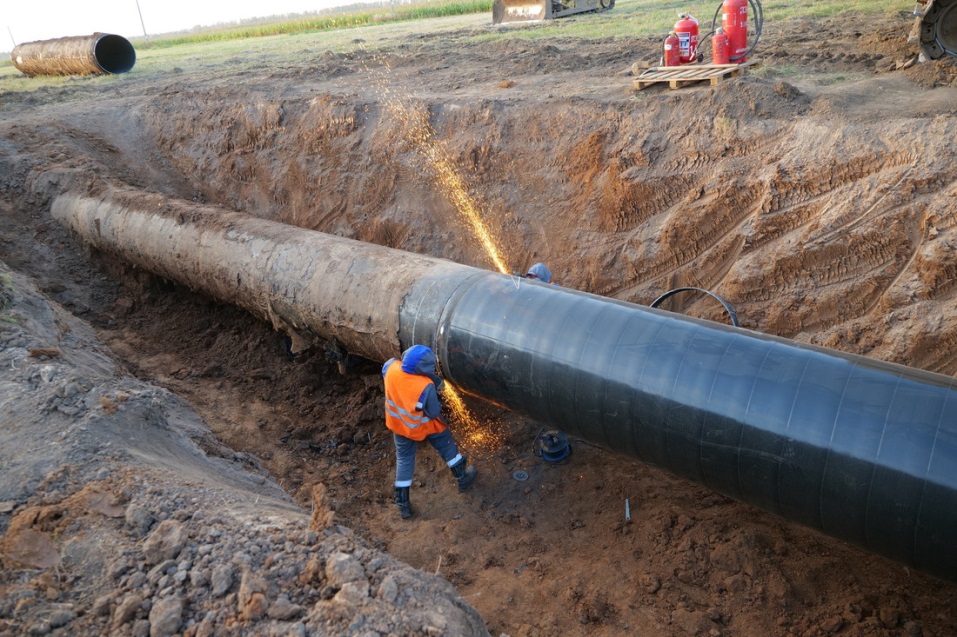
Рис. 2.1. Полная замена трубы для устранения дефектов, обнаруженных в результате ВТД.
В процессе проведения диагностических работ, на долю опасных дефектов, требующих остановки и вывода в ремонт участков газопроводов, приходиться больший объем.
По характеру выполняемых работ капитальный ремонт ЛЧМГ подразделяется на следующие виды:
- замена старой и дефектной изоляции;
- замена изоляции и восстановление стенки трубы или частичная замена труб;
- полная замена труб.
-
Технология проведения обследования линейной части магистрального газопровода.
Комплексные обследования ЛЧ МГ производятся организациями, имеющими лицензии на проведение работ, текущие обследования (осмотры) - бригадами линейно-эксплуатационных служб (ЛЭС), лабораториями ЭХЗ, линейными обходчиками.
Программы, методики и сроки проведения обследований, их периодичность и объемы должны разрабатываться газотранспортными предприятиями с привлечением проектных организаций.
Обследование ЛЧМГ состоит из осмотра и обследования с применением технических средств и оборудования.
Осмотры, как правило, выполняются ЛЭС с использованием транспортных средств: вертолетов, самолетов, автотранспорта или пешим обходом. Способ осмотров и их периодичность устанавливаются газотранспортным предприятием.
Целью осмотра является выявление:
-
вскрытий, оголений, нарушений балластировки, потери устойчивости газопроводов; -
утечек; -
предаварийных состояний и аварий; -
состояния запорной арматуры; -
состояния средств ЭХЗ; -
других неполадок и повреждений; -
аварий на близлежащих сооружениях и объектах, реально угрожающих целостности газопровода.
Обнаруженные при осмотрах нарушения, повреждения и отказы должны регистрироваться в журнале осмотра ЛЧМГ.
При обнаружении повреждений, характер и размеры которых, по оценке лица, выполняющего осмотр, могут привести к аварии, осмотр прекращается и немедленно извещается руководство газотранспортного предприятия о характере обнаруженных повреждений.
Обследование газопроводов, проложенных в горных местностях, должно включать осмотр оползневых мест вблизи газопроводов.
Для качественного проведения работ по обследованию с применением технических средств, важно правильно организовать материально – техническое обеспечение выполняемых работ.
Материально – техническое обеспечение работ
Цель - обеспечение объектов ремонта необходимыми материально-техническими ресурсами в соответствии с технологической последовательностью производства работ и в сроки, установленные графиками производства ремонта и графиками поступления материалов, машин и механизмов на трассу.
Доставку на трассу необходимых машин и механизмов, материалов осуществляют железнодорожным, водным и автомобильным транспортом, а в некоторых случаях и воздушным.
Все материалы хранят непосредственно у места базирования ремонтно-строительного потока на временно сооруженных складах и на трассу доставляют согласно графику.
Организация транспортирования, складирования и хранения материалов, деталей, конструкций и оборудования должна соответствовать требованиям стандартов и технических условий и исключать возможность их повреждения, порчи и потерь.
Проводится проверка фактически выполненных работ, с работами указанными в счете, соответствие условиям договора цен на материалы, запчасти, расценок на выполненную работу.
Составляется ведомость дефектов, устанавливается трудоемкость ремонта в единицах ремонтной сложности, составляется смета затрат на капитальный ремонт.
-
Современные методы проведения контроля (диагностики) для необходимости проведения ремонтно-восстановительных работ.
Контроль дефектов линейной части трубопроводов – это сопоставление показателей структурных элементов трубопровода с установленными нормативно-техническими требованиями.
Главные критерии оценки – геометрические, физические и функциональные показатели. Также важны технологические признаки качества, к примеру, отсутствие недопустимых дефектов, нарушений сплошности материала, соответствие требованиям технической документации геометрических размеров, структуры материала и чистоты состояния внутренней поверхности.
Различают следующие виды контроля: разрушающие и неразрушающие.
-
Разрушающие методы контроля.
Это совокупность методов измерения и контроля показателей качества изделия, по завершении которого нарушается пригодность объекта контроля к использованию по назначению. В транспортировке газа проводятся механические испытания образцов для оценки прочности материалов; гидроиспытания участков трубопровода или целых труб, оценка герметичности трубопровода и его прочностных свойств.
Данный метод позволяет непосредственно определить контролируемые параметры или характеристики (например, предел прочности или толщину покрытия), но не дает полной уверенности в удовлетворительном качестве всей партии. Принципиальный недостаток его заключается в выборочности, так как разрушаются одни изделия, а эксплуатируются другие. Достоверность разрушающих методов контроля зависит от однородности свойств в образцах, взятых для испытаний, и в реальных объектах, а также от сходства условий испытаний и эксплуатации.
К методам разрушающего контроля обычно относят предпусковые или периодические гидравлические испытания аппаратов, а также механические испытания образцов металла, вырезанных из их элементов.
Разрушающие методы контроля применяются при расследовании аварий и проведении приемосдаточных операций.
На рисунке 2.2. представлен результат разрушающего контроля.
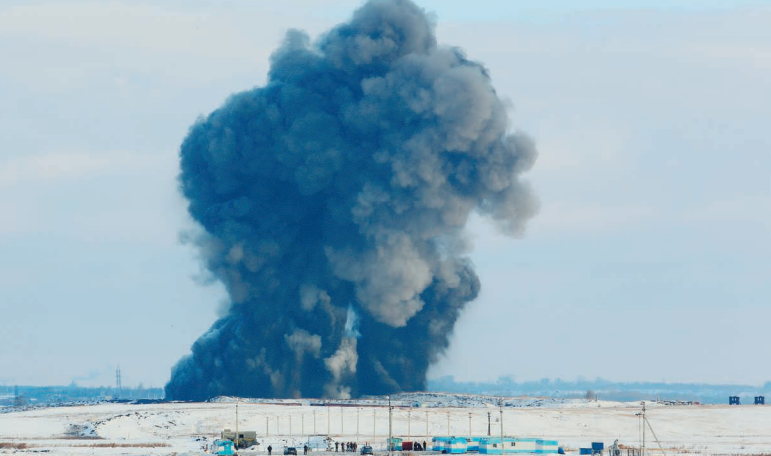
Рис. 2.2. Разрушающий контроль: испытание газопровода под давлением 305 атмосфер.
Разрушающий контроль прямо противоположен неразрушающему методу, суть которого состоит в контроле надежности и основных рабочих свойств и параметров объекта или отдельных его элементов/узлов, не требующем выведения объекта из работы либо его демонтажа.
При оценке технического состояния длительно проработавших аппаратов неразрушающие методы контроля обеспечивают получение наиболее существенной информации для прогнозирования ресурса их безопасной эксплуатации. Они предполагают применение физических методов контроля качества, не влияющих на работоспособность конструкции аппарата.
-
Неразрушающие методы контроля.
С помощью методов неразрушающего контроля проверяется качество труб без нарушения их пригодности к использованию, применяется для выявления таких дефектов, как нарушение сплошности материала изделий, потеря геометрических параметров, нарушение физико-химических свойств, качество сварки швов при всех видах капитального ремонта.
Неразрушающий контроль – это получение информации в виде световых, электрических, звуковых и аналогичных сигналов о состоянии проверяемых объектов при их взаимодействии с веществами и такими электрическим, акустическим, магнитным и другими физическими полями.
В зависимости от принципа работы контролируемого средства методы неразрушающего контроля можно разделить на: акустические, магнитные, ультразвуковые, электрические, радиационные, вихретоковые и др.
Для проведения неразрушающего контроля используется более больше 30 разных типов внутритрубных инспекционных снарядов (ВИС) или диагностических снарядов.
Современные диагностические устройства, используемые для внутреннего контроля за техническим состоянием трубопроводов, делятся на средства, которые приводит в движение транспортируемый газ или собственные источники энергии.
Диагностические снаряды делятся на профилемеры (определение отклонений геометрической формы от той, что была спроектирована) и
дефектоскопы (определение дефектов стенок трубопровода).
По принципу действия дефектоскопы делятся на ультразвуковые и магнитные. Принцип действия магнитных дефектоскопов – искажение магнитных линий в тех местах, где есть дефект, ультразвуковые дефектоскопы рассеивают ультразвуковых волны на дефектах.
Внутритрубная диагностика
Цель проведения такой диагностики – выявление дефектов потери металла, трещин, аномалий кольцевых швов, оценка состояния наружной изоляции.
Для обследования трубопроводов применяются магнитная диагностика, на основе принципов многоракурсного обследования.
Магнитный метод внутритрубной диагностики основан на регистрации магнитных полей рассеяния, образующихся при намагничивании стенки трубы. Суть метода: если в стенке трубы имеется дефект, часть магнитного потока рассеивается на дефекте, что может быть зафиксировано датчиком, расположенным вблизи поверхности трубы.
Намагничивание стенки трубопровода снарядами-дефектоскопами обеспечивается при помощи постоянных магнитов, размещённых на цилиндрическом ярме, и гибких металлических щёток, передающих магнитный поток от магнитов в стенку трубы.
Магнитная диагностика обладает следующими преимуществами:
-
высокая чувствительность к дефектам потери металла, разрешающая способность, высокая стабильность результатов контроля; -
наглядность результатов контроля; -
минимальное количество ложных срабатываний; -
высокая надежность и технологичность конструкции внутритрубных дефектоскопов.
Магнитная дефектоскопия осуществляется комплексом внутритрубных приборов дефектоскопов диаметром от 219мм (8") до 1420мм (56"), включающих:
- дефектоскоп продольного намагничивания ДМТ (MFL)
- дефектоскоп поперечного намагничивания ДМТП (TFI)
- интроскоп (MFL+).
Разновидностью магнитной диагностики является магнитоакустическая диагностика. Магнитоакустическая внутритрубная диагностика основана на электромагнитоакустическом (ЭМА) способе возбуждения и приема ультразвуковых сдвиговых колебаний в металле контролируемого трубопровода, позволяющем проводить диагностику без применения контактной жидкости.
На рисунке 2.3 представлен дефектоскоп продольного намагничивания ДМТ
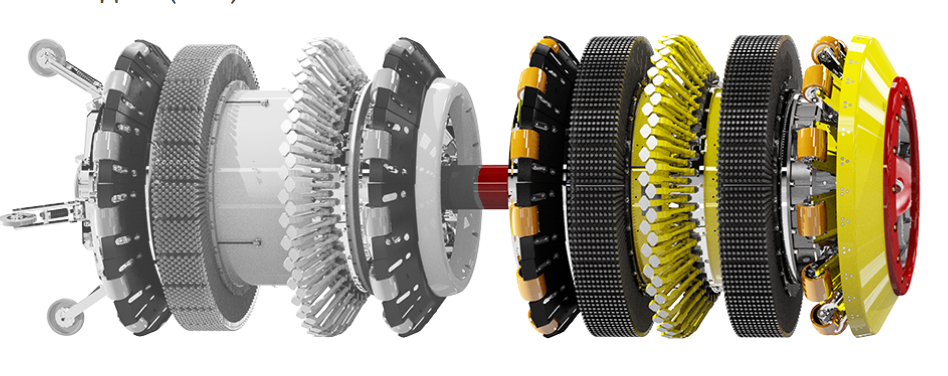
Рис. 2.3. Дефектоскоп продольного намагничивания ДМТ