Добавлен: 07.11.2023
Просмотров: 91
Скачиваний: 1
ВНИМАНИЕ! Если данный файл нарушает Ваши авторские права, то обязательно сообщите нам.
Ультразвуковой контроль сварных швов – это неразрушающий целостности сварочных соединений метод контроля и поиска скрытых и внутренних механических дефектов не допустимой величины и химических отклонений от заданной нормы
Радиографический контроль- неразрушающий контроль для проверки материалов на наличие скрытых дефектов. Радиографический контроль использует способность рентгеновских волн глубоко проникать в различные материалы.
Визуальный и измерительный контроль сварных соединений- это метод контроля качества, выполняемый с помощью визуального осмотра либо с применением простейших измерительных инструментов. С помощью визуального осмотра выявляются крупные дефекты, а с помощью инструментов выявляются мелкие дефекты, сразу незаметные глазу.
Капиллярный контроль сварных соединений применяется для выявления наружных (поверхностных и сквозных) дефектов в сварных швах и прилегающих зонах термического влияния. Такой способ проверки позволяет выявлять такие дефекты, как горячие и холодные трещины в сварных швах, непровары, поры, раковины и некоторые другие.
При помощи капиллярной дефектоскопии можно определить расположение и величину дефекта, а также его ориентацию по поверхности металла.
Магнитопорошковая дефектоскопия сварных соединений (она же магнитно-порошковая дефектоскопия) — метод контроля качества, суть которого заключается в обнаружении магнитных полей вокруг дефекта с применением ферримагнитных веществ.
Я произвёл визуальный контроль швов. Я измерил катит сварного шва, проверил диметры сварочной конструкции, произвел осмотр сварных соединений, проверил их на наличие дефектов.
1.5. Основные дефекты сварки, их характеристика, причины возникновения и способы исправления
Непровар — местное отсутствие сплавления между свариваемыми элементами, между основным и наплавленным металлом или отдельными слоями шва при многослойной сварке. Причинами непровара являются некачественная подготовка свариваемых кромок (окалина, ржавчина, малый зазор, излишнее притупление и т.д.), большая скорость сварки, смещение электрода с оси стыка, недостаточная сила тока.
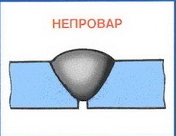
Подрез — дефект, наиболее часто встречающийся при сварке. Он выражен в виде углубления по линии сплавления сварного шва с основным металлом. В результате подреза происходит местное уменьшение толщины основного металла, что приводит к снижению прочности. Особенно опасен подрез в случаях, когда он расположен перпендикулярно действующим рабочим напряжениям. Подрез возникает обычно при повышенном напряжении дуги с завышенной скоростью сварки, когда одна из кромок проплавляется глубже, жидкий металл стекает на горизонтальную плоскость и его не хватает для заполнения канавки.
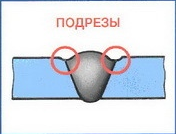
Наплыв — проявляется в виде натекания металла шва на поверхность основного металла без сплавления с ним. Наплывы резко изменяют очертания швов и тем самым снижают выносливость конструкции. Причиной этого дефекта может стать пониженное напряжение дуги, наличие окалины на свариваемых кромках, медленная сварка, когда появляются излишки расплавленного присадочного металла.
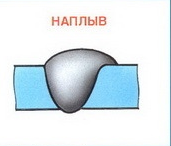
Прожог— сквозное проплавление обычно возникает из-за большого тока при малой скорости сварки. Проявляется он в виде сквозного отверстия в сварочном шве, которое возникает в результате утечки сварочной ванны. При многослойной сварке прожог возникает в процессе выполнения первого прохода шва. Причинами прожога могут стать - завышенный зазор между свариваемыми кромками, недостаточная толщина подкладки или неплотное ее прилегание к основному металлу, что создает предпосылку для утечки сварочной ванны.
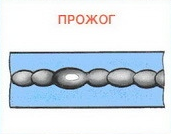
Свищ — воронкообразное углубление в сварочном шве, развивающееся из раковины или большой поры. Причиной развития свища чаще всего является некачественная подготовка поверхности и присадочной проволоки под сварку. Дефект обнаруживается визуально и подлежит переварке.
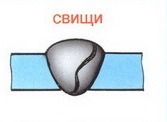
Трещины- Это наиболее опасные дефекты сварки, способные привести к практически мгновенному разрушению сваренных конструкций с самыми трагическими последствиям. Трещины различаются по размерам (микро- и макротрещины) и времени возникновения (в процессе сварки или после нее).
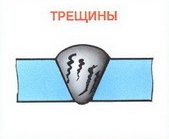
Кратеры- Это дефекты в виде углубления, возникающего в результате обрыва сварочной дуги. Кратеры снижают прочность шва из-за уменьшения его сечения. В них могут находиться усадочные рыхлости, способствующие образованию трещин. Кратеры надлежит вырезать до основного металла и заварить.
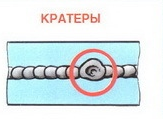
Пористость - это полости, заполненные газами. Они возникают из-за интенсивного газообразования внутри металла, при котором газовые пузырьки остаются в металле после его затвердевания. Размеры пор могут быть микроскопическими или достигать нескольких миллиметров. Нередко возникает целое скопление пор в сочетании со свищами и раковинами.
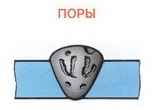
Перегрев и пережог металла. Пережог и перегрев возникают из-за чрезмерно большого сварочного тока или малой скорости сварки. При перегреве размеры зерен металла в шве и около шовной зоне увеличиваются, в результате чего снижаются прочностные характеристики сварного соединения, главным образом - ударная вязкость. Перегрев устраняется термической обработкой изделия.
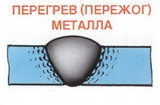
2.ОБОРУДОВАНИЕ, ИНСТРУМЕНТЫ, ПРИСПОСОБЛЕНИЯ И МАТЕРИАЛЫ ПРИМЕНЯЕМЫЕ ДЛЯ ВЫПОЛНЕНИЯ РАБОТЫ
2.1. Перечень оборудования, инструментов и материалов, применяемых для выполнения работы.
Оборудование и инструменты, используемые при сварке:
Для разметки заготовок применяем: металлическую линейку, угольник, чертилку.
Для резки трубы – Ленточнопильный станок W1318SSA
Для контроля при сборке конструкции: слесарный угольник, щупы.
Для выполнения сварочных работ:
сварочный аппарат для сварки не плавящимся электродом в защитном газе KEMPPI Kempact 181A.;
горелка;
Для зачистки сварных швов:
молоток для отбивки шлака;
металлическую щетку;
углошлифовальную машинку.
Для проверки размеров сварного шва: универсальный шаблон сварщика
УШС-3.
Используемый материал Ст3 сп.
Данный вид металла является углеродистой конструкционной сталью обыкновенного качества. Соответствует ГОСТу 380-2005.
Расшифровывается подобная маркировка следующим образом:
«Ст» – собственно название металла.
«3» – номер марки, определяемый химсоставом материла.
«сп» – спокойная. Эти буквы являются обозначением степени раскисления стали, и «говорят» о том, что при затвердевании вещества почти не выделяется газ.
Состав
Одной из отличительных особенностей стали СТ3 сп является ее химический состав, в котором:
углерод занимает 0,14 – 0,22%;
доля содержания марганца – 0,40 – 0,65%;
доля кремния – 0,15 – 0,30%;
никелевой, хромовой и медной составляющей – до 0,3%
содержание серы – не более 0,005%;
доля фосфор – 0,04%;
азота – менее 0,1%.
Все остальное составляет железо.
Преимущества стали Ст3сп
Благодаря своим техническим характеристикам, данная разновидность металла имеет ряд преимуществ по сравнению с другими марками стали. Основными плюсами материала являются:
повышенная коррозийная стойкость;
оптимальное сочетание упругости и твердости;
при отливке не возникает дефектов;
отсутствие отпускной хрупкости.
3. ОРГАНИЗАЦИЯ РАБОЧЕГО МЕСТА, ОХРАНА ТРУДА,
ТЕХНИКА БЕЗОПАСНОСТИ ВО ВРЕМЯ ВЫПОЛНЕНИЯ СВАРОЧНЫХ РАБОТ
3.1. Организация рабочего места сварщика
Организация рабочего места электросварщика, который трудится на постоянном месте в цеху, начинается с обустройства кабины. Это помогает спокойно выполнять сварочные работы, и ограждает других от искр и световых вспышек. Кабина должна иметь размеры, позволяющие заносить в нее изделия, предназначенные для сварки. Если производимые конструкции небольшие, то минимальная площадь кабины должна составлять 2 х 2 метра. Это даст расположить все необходимое и свободно перемещаться вокруг изделия. Чтобы излучение от сварки не мешало окружающим, высота стенок кабины устанавливается до 1,8 м. Поскольку большинство сварочных манипуляций производится на уровне стола, этой высоты будет достаточно. Каркас кабины выполняется из профильной трубы или уголков. Стойки крепятся к полу анкерами. Можно предусмотреть дверь, которая будет полностью изолировать рабочее пространство сварщика по периметру. Для улучшения естественной вентиляции, между полом и началом стенки кабинки выставляется зазор в 150 мм. Это содействует притоку воздуха и поднятию вредных газов от сварки вверх. Стороны кабины можно изготовить из листового шифера или тонкого железа. Допускаются варианты из брезента и даже фанеры, но эти материалы необходимо пропитать огнестойкими составами. Окрашивать стенки желательно в цинковые или титановые белила. Подойдет желтый крон. Эти вещества на поверхности кабины будут хорошо поглощать ультрафиолетовое излучение. Если покрасить подобную конструкцию в черный или темно-синий цвет, то ухудшится общая освещенность, т. к. будет поглощение света, исходящего от лампы над рабочим местом.
В организации сварочных работ важное значение имеет правильное размещение оборудования. Многопостовые агрегаты и установки, состоящие из нескольких сварочных агрегатов, располагают в отдельном помещении или на площади общего производственного помещения, огражденной постоянными перегородками высотой не менее 1,7 м.
3.2. Спецодежда и средства защиты сварщика
Костюм сварщика — предназначенная для защиты работающих от искр, брызг расплавленного металла, окалины, излучений сварочной дуги. В него входит: куртка, брюки, маска, краги, специальная обувь. Сварочный костюм должен быть прочным. Наличие механических повреждений, сквозных протертостей, отверстий категорически не допускается, так как в прорехи могут попасть искры и брызги расплавленного металла. Костюм сварщика — спецодежда, предназначенная для защиты работающих от искр, брызг расплавленного металла, окалины, излучений сварочной дуги. Сварочная маска- неотъемлемый атрибут любой сварочной экипировки. Она призвана защищать сварщика от ожогов и ультрафиолета.
3.3. Техника безопасности
1. Требование охраны труда перед началом работ
1.1. Надеть спецодежду, спец обувь и другие средства индивидуальной защиты. Застегнуть спецодежду на все пуговицы, не допуская свисающих концов одежды, убрать волосы под головной убор. Проверить отсутствие в одежде острых, колющих и режущих предметов.
1.2. После получения задания у руководителя работ электросварщик обязан:
проверить наличие и исправность газосварочной аппаратуры, вентиляции, инструмента, приспособлений;
подготовить холодную воду для охлаждения горелки (резака), огнетушители, ящик с песком и другие первичные средства пожаротушения;
убедиться, что вблизи места сварочных работ нет легковоспламеняющихся и горючих материалов, ЛВЖ. Если они имеются, поставить в известность непосредственного руководителя и потребовать, чтобы их убрали не менее чем на 5 м от места проведения огневых работ;
обеспечить транспортировку баллонов с газом к рабочему месту, при этом транспортировку производить только на специальных тележках. Не бросать баллоны, не ударять друг о друга, не браться при подъеме баллона за его вентиль. Следить, чтобы на штуцере вентиля была заглушка, а на баллоне защитный колпак;