Файл: Причины образования отложений солей при эксплуатации сборных трубопроводов. Методы предупреждения и борьбы.doc
ВУЗ: Не указан
Категория: Не указан
Дисциплина: Не указана
Добавлен: 07.11.2023
Просмотров: 20
Скачиваний: 1
ВНИМАНИЕ! Если данный файл нарушает Ваши авторские права, то обязательно сообщите нам.
-
Причины образования отложений солей при эксплуатации сборных трубопроводов. Методы предупреждения и борьбы.
Существует 3 основных типа отложения солей:
1



2)слоистые отложения
3)бугристые
Отложение солей наблюдается при обводненной продукции скважин:
1)водо-растворимые (NaCl, CaCl2)
2)водо-нерастворимые (CaCO3, MgCO3, CaSO4*2H2O,гипс и др.)
Причины отложения:
1)нарушение карбон-го равновесия, обуслов-го сниж.t и P.При его наруш-ии из водного р-ра выдел-ся СО2, при этом р-р становится перенасыщ-ым и происх-т в начале образование зародышей кристаллов, затем рост кристаллов и отложение кристаллов на внутр. пов-ти.
Основные р-ии:выдел-ся CO2 и образ-ся осадок солей.
C


M


Падение Р в НГВ-ом потоке интенсиф-ет образ-ие осадков солей, а сниж-ие t притормаж-ет.Падение Р сдвигает равновесие реакции вправо более интенс-но, чем сниж-ие t,сдвиг-ей эти реакции влево.
2)нарушение равновесия происх. и при смешении вод различных по составу.
Методы удаления отложений солей
Методы удаления солеотложений | | ||||||||||
| | | |||||||||
Химические | | Механические | | ||||||||
| | | | | | ||||||
Термохимическая обработка соляной кислотой | | Преобразование осадка с последующей обработкой соляной кислотой | | Растворение кислотами или комплексообразующими реагентами | | Очистка скважин специальными устройствами | | |
-использование пресной воды.
Методы предотвращения солеобразований.
Основным направлением борьбы с отложением неорганических солей является применение методов предотвращения их отложения в скважинах и на глубиннонасосном оборудовании. Существующие методы предотвращения отложения солей можно разделить на две группы:
-
безреагентные методы:
- воздействие на перенасыщенные солями растворы магнитными силовыми и акустическими полями;
- использование защитных покрытий труб и рабочих органов насосов;
- проведение специальных изоляционных работ в связи с негерметичностью цементного кольца или неисправности обсадной колонны и попадания верхних сульфатных вод в продукцию скважины происходит интенсивное выпадение солей, также селективная изоляция обводнившихся пропластков продуктивного пласта, поскольку при сокращении притока воды, перенасыщенной солями, уменьшается и интенсивность отложения солей;
- поддержание повышенных забойных давлений;
- использование хвостовиков, диспергаторов и других конструктивных изменений в глубиннонасосных установках.
2) Химические методы включают подготовку и использование для закачки в пласт высокоминерализованных вод, совместимых с пластовыми, что исключает или в значительной мере снижает интенсивность образования отложений неорганических солей. Поэтому одним из радикальных методов предотвращения выпадения гипса на ряде зарубежных месторождений является применение для заводнения залежей естественных или искусственно приготовленных вод высокой солености.
Из известных способов предотвращения отложения неорганических солей наиболее эффективным и технологичным в настоящее время является применение химических реагентов - ингибиторов отложения солей.
-
Резервуары и резервуарные парки.
Нефтепромысловые резервуары предназначены для хранения, приема и отпуска нефти.
Необходимы для бесперебойной работы скважин, для наполнения, кратковременного хранения и учета сырой товарной нефти.
Для обеспечения бесперебойной работы магистрального трубопровода.
Группу резервуаров, сосредоточенных в одном месте, называют резервуарным парком.
Общий объем товарного резервуарного парка должен быть равен двухсуточной плановой производительности всех эксплуатационных скважин месторождения.
В резервуар входит:
-
насосная станция -
котельная -
вспомогательные устройства -
средства пожаротушения -
КИП и автоматика -
Небольшие мастерские.
Классификация резервуаров следующая:
-
По назначению:
1)сырьевые
2)товарные
3)технологические
4)для хранения воды
-
По материалу изготовления:
1)металлические (10-15 лет)
2)железобетонные
3)каменные
4)земляные
-
По отношению к уровню земли
1)наземные
2)подземные (максимальный уровень жидкости на 20 см ниже отметки площадки)
3)полузаглубленные
-
По величине избыточного давления
1)низкого давления (Ризб. – 200 мм водного столба)
2)высокого давления (Ризб. - 2000 мм)
-
По конструкции
1)вертикальные, цилиндрические
-
с плоской крышей -
с конической крышей -
с сферической крышей
2)горизонтально цилиндрические
-
с плоскими боковинами -
пространственные боковины
3)вертикально прямоугольные
4)горизонтальные круглые
5)сфероидальные
-
сферические -
каплевидной формы -
многокупольные
-
По технологическим операциям
Обозначения РВС от 100 до 10000м3
Основные элементы резервуаров.
-
Корпус, материал изготовления листовая сталь, толщина стенки от 4 до 10 мм. -
Днище, толщина стенки 5 мм. -
Крыша, толщина стенки 2,5 мм.
Резервуары средней и большой емкости изготавливают с переменной толщиной стенки в нижней части резервуара.
При сооружении резервуара корпуса, стальные пояса могут располагаться тремя способами:
1)ступенчатым
2)телескопическим
3)встык
Перед сооружением резервуара подготавливается фундамент резервуара. Он состоит:
-
верхний слой – гидрозащита -
низкозернистый песок -
крупнозернистый песок -
гравий – нижний слой.
1 – световой люк
2 – вентиляционный патрубок
3 – огневой предохранитель
4 – дыхательный клапан
5 – замерный люк
6 – указатель уровня
7 – люк лаз
8 - сифонный клапан
9 – подъемная труба
10 – хлопушка
11 – шарнир подъемной трубы
12 – приемно-раздаточный патрубок
13 – перепускное устройство
14 – лебедка
15 – управление хлопушкой
16 – роликовый блок.
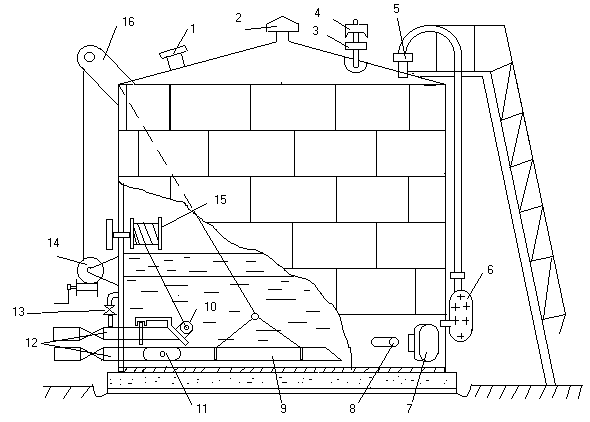
204. Условия образования и физические свойства водонефтяных эмульсий.
При разработке месторождений наступает момент, когда с продукции скважин начинает поступать вода, вначале содержание воды низкое, потом количество воды начинает расти.
При подъеме нефти с водой начинает образовываться эмульсия.
Эмульсия – это механическая смесь двух взаимно нерастворимых жидкостей нефть и вода, одна из которых распределяется в объеме другой в виде капелек различных размеров.
Образование эмульсий обусловлено процессом адсорбции на поверхности раздела фаз естественных ПАВ, к ним относятся смолистые вещества, асфальтены, продукты взаимодействия нафтеновых кислот и солей, которые находятся в пластовой воде.
О
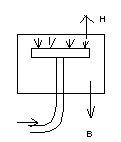
Оба эти явления связаны с кипением в системе третьего компонента эмульгатора.
Эмульгаторы бывают гидрофильные, гидрофобные. Образованные эмульсии можно классифицировать на три основных типа:
1. Обратные эмульсии – вода в пласте, т.е. капельки воды находятся в нефти. Дисперсная среда – нефть.
-
Нефть в воде или масло в воде – прямой тип, когда капельки нефти находятся в воде. -
Смешанный тип – вода находится в нефти, которая в капельках воды.
Обратный тип образуется при обводненности 75-80%. При увеличении содержания воды обратный тип переходит в прямой тип. Выше прямой и смешанный.
Свойства водонефтяных эмульсий.
-
Плотность
ρэ= ρн(1-β)+ ρв β
-
вязкость; нефтяные эмульсии, являясь дисперсными системами, т.е. имея определенную структуру, обладают аномальной вязкостью, т.е. их движение не подчиняется закону вязкого течения, т.е. зависимость напряжения σ от градиента скорости не является линейной.
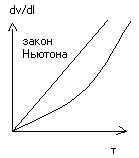
Для систем с аномальной вязкостью коэффициент вязкости не является постоянной величиной, а зависит от условий движения и градиента скорости, в этом случае вязкость называется кажущейся или эффективной, причем она будет зависеть от содержания водной фазы и температуры.
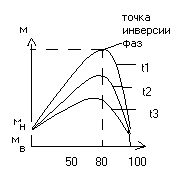
При увеличении температуры вязкость эмульсии будет снижаться
t1
Формулы для определения вязкости не существует, для различных условий она определяется экспериментально, и формулы разные.
Дисперсность эмульсии – раздробленность капель воды или нефти и их размеров, она определяется тремя параметрами:
-
Диаметр капелек. -
Обратная величина диаметра капельки. D=1/d -
Удельная межфазная поверхность – это отношение суммарной поверхности капелек к общему их объему Sуд=S/V
Для частицы шарообразной формы Sуд=S/r
Удельная поверхность обратно пропорциональна размерам частицы. Чем меньше размеры частицы, тем больше удельная поверхность.
По дисперсии эмульсии различают мелкодисперсные с размером капелек воды от 0,2 до 20 мк, среднедисперсные от 20 до 50 мк, грубодисперсные от 50 до 100 мк.
Наименьшие размеры частиц, если рассматривать по участкам, наблюдаются после сепаратора и после насоса.
-
Методы разрушения водонефтяных эмульсий.
Разделение водонефтяных эмульсий методом отстаивания.
Основными показателями, характеризующими процесс отстоя, являются:
-
Время отстоя эмульсии. -
Температура эмульсии. -
Количество деэмульгатора. -
Остаточное содержание воды и солей в нефти после отстоя.
В настоящее время на промыслах применяют напорные отстойники в виде горизонтальных цилиндрических емкостей .
Существуют в зависимости от направления ввода эмульсии 2 класса отстойников с вертикальным движением потоков и горизонтальным.
При вертикальном движении нефти эмульсию вводят через трубчатые перфорированные наконечники, которые могут располагаться в нижней части аппарата в слое дренажной воды.
Расчитывают несколько этапов процесса отстоя:
1.Каплеобразование (распыление водонефтяной эмульсии в водной фазе). Ввод эмульсии осуществляется в слой воды.
2.Всплывание крупных капель эмульсии в водной фазе.
3.Переход нефтяных капель через границу раздела нефть – вода.
4.Прохождение струек сырья через промежуточный слой эмульсии, т.е. над границей нефть – вода имеется промежуточный слой.
5.Протекание через кипящий слой, состоящий из взвешенных глобул воды, выше промежуточного слоя.
П
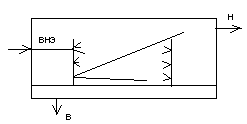
Термическое разделение водонефтяных эмульсий.
При нагревании водонефтяной эмульсии происходит:
1.обратная диффузия эмульгатора с блокирующих оболочек нефти
2.снижение прочности блокирующих оболочек
3.снижение межфазного натяжения на границе нефть – вода
4.увеличение объема капель дисперсной фазы и увеличение вероятности их столкновения
5.увеличение разности плотностей
6.уменьшение вязкости нефти
Разделение водонефтяных эмульсий путем ее фильтрации.
Нестойкие эмульсии успешно расслаиваются при пропускании их через фильтрующий слой, который может быть из гравия, битого стекла, древесины и металлических стружек, стекловаты и др. материалов.
В данном случае деэмульсация нефтей основана на явлении селективного смачивания.
Неполярные жидкости (нефть) с малым поверхностным натяжением (20 - 30 эрг/см2) обычно хорошо смачивает твердую поверхность. Вода с поверхностным натяжением 72.5 эрг/см2 смачивает лишь некоторые тела (стекло, кварц).
Фильтрующее твердое вещество должно удовлетворять основным требованиям:
-
иметь хорошую смачиваемость водой, чтобы произошло сцепление глобул воды с фильтрующим веществом, разрыв межфазных пленок, и произошла коалесценция (слияние) капель воды; -
быть достаточно прочным, чтобы обеспечить длительную эксплуатацию.
Показания:
-
большая обводненность нефти; -
малая обводненность, но эмульсия нестойкая. -
незначительная разность плотностей воды и нефти.
Данный метод самостоятельного применения не находит из-за громоздкого оборудования, малой производительности, необходимости часто менять фильтры, но встречается в сочетании с термохимическими методами разрушения эмульсий.
Применение химических реагентов для разделения водонефтяных эмульсий.
Деэмульгаторы – это вещества, понижающие поверхностное натяжение, делятся на 2 основные группы:
-
ионогенные (образуют ионы водных растворов) -
неионогенные (не образуют ионы водных растворов)
Принцип действия:
Деэмульгаторы, адсорбируясь на поверхности раздела фаз нефть – вода, вытесняют и замещают поверхностно активные природные эмульгаторы.
Пленка, образованная деэмульгатором, менее прочная, по мере накопления деэмульгатором на поверхности капелек воды, между каплями возникают силы взаимного притяжения.
Процесс слияния капелек воды называется коалисценцией, а слипание глобул при столкновении называется флокуляцией (хлопьеобразование).
Разделение эмульсий вода в масле можно разделить на несколько стадий:
1. Распределение деэмульгатора по всему объему нефтяной фазы.
2. Проникновение реагента в защитные слои и их разрушение.
3.Сближение и коалисценция капель воды и их осаждение за счет гравитационных сил.
4.Интенсификация процессов слияния.
Каплеобразователи.
Для доведения ПАВ до капелек пластовой воды и разрушения бронирующих оболочек применяют каплеобразователи. Они бывают двух типов: трубчатые и обычные.
Линейный каплеобразователь изготавливают из обрезков труб разного диаметра и располагают на опорах горизонтальной плоскости.
Разделение водонефтяных эмульсий в электрическом поле.
О
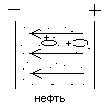
Под действием основного и дополнительного электрических полей сначала происходит упорядочение движения, а затем столкновение капель воды, это обусловлено силами притяжения
206. Комплексные установки для обезвоживания и обессоливания нефтей.
Технологические схемы обезвоживания нефти.
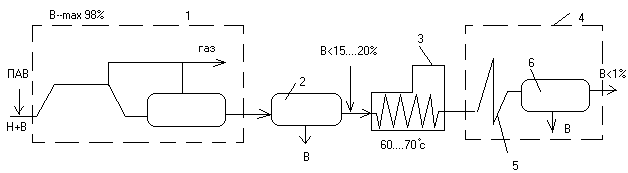
-
Газосепарационный узел. Вторая ступень сепарации. -
отстойник предварительного сбора воды. -
печь подогрева. -
узел обезвоживания нефти. -
каплеобразователь. -
гравитационный отстойник эмульсии
Обессоливание нефти.
После ступени обезвоживания нефть удовлетворяет норму по содержанию воды, однако минерализация и состав воды, по содержанию хлористых солей и минерализации превышает допустимую норму, поэтому нефть промывают пресной водой.
П
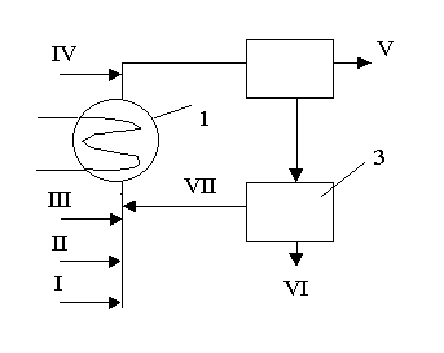
1 – теплообменник
2 – электродегидратор
3 – нефтеотделитель
-
нефть после первой ступени обезвоживается -
деэтиригатор -
Щелочь или сода (если в пластовой воде содержатся органические кислоты) -
Пресная вода -
Обессоливание нефти -
Дренажная вода системы ППД -
Нефть возвращается на прием электродегидратора
Объем пресной воды составляет 5-10%, объем обрабатываемой нефти в электродегидраторах под действием электрического поля происходит слияние капелек пресной и соленой воды. В результате укрупнения капли быстро оседают и переходят в водную фазу, которая направляется в нефтеотделитель для дополнительного отстоя, уловленная в нефтеотделителе нефть снова направляется в электродегидратор.
207. Обессоливание нефти при ее подготовке.
После ступени обезвоживания нефть удовлетворяет норму по содержанию воды, однако минерализация и состав воды, по содержанию хлористых солей и минерализации превышает допустимую норму, поэтому нефть промывают пресной водой.
П
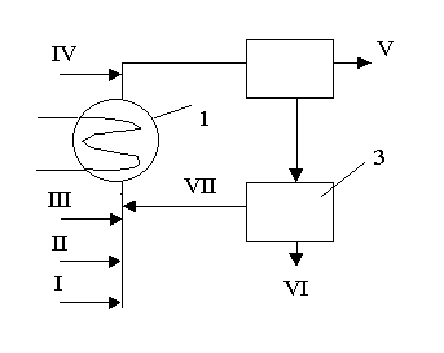
1 – теплообменник
2 – электродегидратор
3 – нефтеотделитель
-
нефть после первой ступени обезвоживается -
деэтиригатор -
Щелочь или сода (если в пластовой воде содержатся органические кислоты) -
Пресная вода -
Обессоливание нефти -
Дренажная вода системы ППД -
Нефть возвращается на прием электродегидратора
Объем пресной воды составляет 5-10%, объем обрабатываемой нефти в электродегидраторах под действием электрического поля происходит слияние капелек пресной и соленой воды. В результате укрупнения капли быстро оседают и переходят в водную фазу, которая направляется в нефтеотделитель для дополнительного отстоя, уловленная в нефтеотделителе нефть снова направляется в электродегидратор.
208. Стабилизация нефти. Оборудование, применяемое для стабилизации нефти.
Процесс извлечения легких углеводородов из нефти на прочные называют стабилизацией нефти.
Процесс стабилизации нефти – это завершающая стадия сепарации газа, его применяют для уменьшения потерь легких углеводородов в товарных резервуарах и за пределами прочности. Его осуществляют двумя путями.
-
сепарация углеводородов под вакуум (вакуумная сепарация) -
сепарация углеводородов при повышении давления и температуры.
Сущность стабилизации нефти заключается в отделении от нее летучих углеводородов (пропан-бутановой фракции), а также растворимых в нефти сопутствующих газов, таких как сероводород, углекислый газ и азот, что сокращает потери нефти от испарения, снижает интенсивность процесса коррозии аппаратуры, оборудования и трубопроводов по пути движения нефти от месторождения до нефтеперерабагывающего завода, а также позволяет получать ценное сырье для нефтехимии.
Применяют следующие способы стабилизации нефти: горячую, или вакуумную, сепарацию и ректификацию.
При горячей, или вакуумной, сепарации от нефти отделяется широкая газовая фракция, в которой наряду с пропан-бутановой фракцией содержится большое количество более высокомолекулярных углеводородов, извлечение которых из нефти ухудшает ее качество. Для извлечения высокомолекулярных углеводородов из широкой газовой фракции и последующего возвращения их в стабильную нефть, используют следующие процессы:
1) однократную конденсацию с последующей компрессией, масляной абсорбцией или низкотемпературной конденсацией остаточных газов. Принципиальная технологическая схема установки включает: насосы; теплообменники; подогреватели; трапы–сепараторы; конденсаторы-холодильники; бензосепараторы; емкости бензина; компрессор; маслоотделители; блок обезвоживания и обессоливания; товарные емкости.
Для определения соотношений, регулирующих процесс однократного испарения, достаточно исходить из следующей схемы.
2) фракционированную конденсацию с последующей компрессией газового остатка. Основной аппаратурой узла стабилизации являются теплообменники, подогреватели, трап-стабилизатор, газосепараторы, бензосепараторы, конденсаторы-холодильники и др. Из перечисленной аппаратуры особо следует остановиться на трап-стабилизаторе. Он представляет собой сочетание трапа-сепаратора и фракционирующего конденсатора.
На практике процесс фракционированной конденсации осуществляется в виде прямоточной или противоточной конденсации.
Прямоточная конденсация. Во всех сечениях аппарата газ находится в состоянии равновесия с жидкостью и в конце конденсации остаточный газ и полученная жидкость находятся в состоянии фазового равновесия, имея одинаковую температуру.
Противоточная конденсация. В отличие от прямоточной при противоточной фракционированной конденсации в любом сечении нет равновесия фаз, что и обусловливает процесс фазового массообмена, заключающегося в переходе высококипящих компонентов из газовой фазы в жидкую, таким образом, последняя обогащается высококипящими компонентами. В результате образуется газовый остаток не сконденсировавшихся углеводородов с предельным максимальным содержанием низкокипящих компонентов.
3) абсорбцию или ректификацию.
При стабилизации нефти ректификацией всю нефть подвергают процессу ректификации, при этом обеспечивается четкое разделение углеводородов и достигается заданная глубина стабилизации нефти.
Принципиальная технологическая схема установки включает: насосы; теплообменники; ректификационная колонна; подогреватели; конденсаторы-холодильники; сепараторы бензина; сборник нестабильного бензина; блок обезвоживания и обессоливания. Колонна, в которой осуществляется процесс ректификации, состоит из двух основных частей: концентрационной, расположенной выше ввода сырья, и отгонной (или как ее еще иногда называют нижней, отпарной и лютерной). Но иногда колонны конструктивно расчленяются на две самостоятельные, выполняющие функции указанных частей, т. е. концентрационной и отгонной.
В концентрационной части осуществляется ректификация паровой фазы, в отгонной – ректификация жидкости, отделившейся в эвапорационном пространстве колонны.
209. Борьба с коррозией при эксплуатации трубопроводов и нефтепромыслового оборудования.
Коррозия – это разрушение металлов в результате химического или электрохимического воздействия окружающей среды, это окислительно-восстановительный гетерогенный процесс, происходящий на поверхности раздела фаз.
Различают:
1)атмосферная
2)почвенная
3)внутренняя
Атмосферную устраняют путем нанесения краски.
Интенсивность почвенной коррозии зависит от состояния почвы, от влажности и неоднородности металла.
При изготовлении ТП невозможно достичь того, чтобы металл на всем протяжении имел одинаковый сплав, с другой стороны ТП нах-ся в земле, как в эл. химич. ванне. Неоднородные участки ТП образуют гальванопары, по кот. протекает эл.ток, т.е. образуется анод и катод, при этом анод разрушается. Кроме того на участках ТП возник. напряж. участки.
Кардинальным средством борьбы с коррозионным повреждением стальных труб является замена их на пластмассовые.
Задача надежности защиты от внутренней коррозии решается с помощью технологии футерования трубных плетей полиэтиленом и специальной конструкцией стыка.
Эффективным методом защиты является ингибирование, так как ингибиторы тормозят процесс коррозионного зарождения трещин на поверхности металла. Кроме того, многие ингибиторы способны проникать в вершину зародившейся трещины и сдерживать ее развитие.
Из других методов защиты реально осуществимым является термообработка труб. Однако режимы термообработки для конкретных видов труб должны выбираться с учетом особенностей коррозионной среды и механизма коррозии, характерных для конкретного месторождения.
Пассивные способы защиты предусматривают изоляцию наружной поверхности трубы от контакта с грунтовыми водами и от блуждающих электрических токов, которая осуществляется с помощью противокоррозионных диэлектрических покрытий, обладающих водонепроницаемостью, прочным сцеплением с металлом, механической прочностью. Для изоляции промысловых трубопроводов применяют покрытие на битумной основе и на основе полимеров.
Активные способы защиты: катодная и протекторная.
Катодной защитой называется способ предупреждения коррозии металла, при котором защищаемый объект делают катодом, а разрушению подвергается специально установленный анод.
При катодной защите наложением внешнего тока источник постоянного тока через плюсовую клемму соединен с помещенным в землю анодом. Минусовая клемма источника тока соединена дренажем с трубопроводом. Электрический ток проходит через анод в почву, затем через поврежденную изоляцию натекает на трубопровод и возвращается по дренажу к минусовой клемме источника тока. Поступая в трубу через поврежденную изоляцию, электрический ток превращает эти места в катоды, вследствие чего поверхности самого трубопровода не подвергается коррозии, а разрушается анод, который для этого и предназначен.
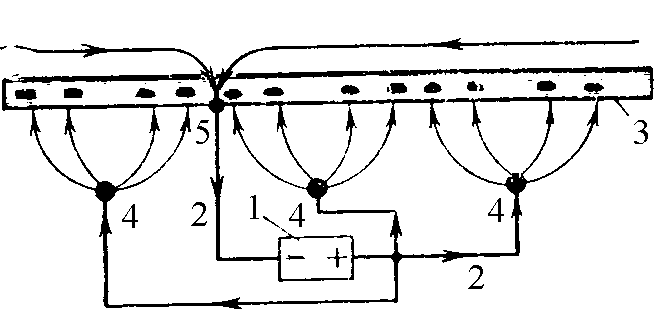
Схема катодной защиты трубопровода внешним током: 1 – источник постоянного тока; 2 – изолированный электропровод; 3 – трубопровод с поврежденной изоляцией; 4 – анод; 5 –дренаж
Одна катодная станция в зависимости от сопротивления защитного покрытия может защищать участок трубопровода длиной от 5 до 25 км. Катодной защитой можно предотвращать коррозию днищ нефтяных резервуаров и различных подземных металлических емкостей.
Защита трубопроводов от электрохимической коррозии протекторами осуществляется без подведения внешней электроэнергии и сводится к работе гальванического элемента. Принцип работы протекторной защиты трубопроводов следующий. Параллельно защищаемому трубопроводу в землю зарывают протекторы, электрический потенциал которых ниже потенциала материала трубопровода (магний, рафинированный цинк, алюминий и т. д.). Протекторы соединяют с трубопроводом изолированным проводником. При возникновении разности потенциалов между трубой и почвой протекторы превращаются в разрушаемые аноды, в результате чего трубопровод предохраняется от коррозии.
Преимущества протекторной защиты:
-
отпадает необходимость в сооружении катодных станций и источников тока; -
простота схемы; -
отсутствие эксплуатационных затрат.
К недостаткам протекторной защиты следует отнести, прежде всего, необходимость расходования цветных металлов и поэтому, сравнительно большие капитальные затраты.
-
Системы сбора и подготовки промысловых сточных вод.
Для подготовки сточных вод на нефтяных месторождениях обычно применяются установки трех типов: открытые, полузакрытые и закрытые. В открытых установках сточные воды движутся самотеком, и они контактируют с кислородом воздуха. Это один из их основных недостатков, часто приводящих к изменению свойств воды: происходит окисление железа, содержащегося в воде, изменяется водородный показатель рН, повышается коррозионная активность и т. д. Однако открытые системы позволяют на одних и тех же сооружениях очищать воды разного состава и изменять в нужном направлении их качество при помощи различных реагентов (коагулянтов).
Кроме того, открытые системы позволяют очищать пластовые и промливневые сточные воды в одном потоке независимо от состава, давления и газонасыщенности воды и совместно закачивать их в нагнетательные скважины. Открытые системы чаще всего рекомендуются для сточных вод с большим содержанием сероводорода (Н2S) и углекислого газа (CO2) и для более глубокой очистки воды от капелек нефти и механических примесей.
На рисунке 1 показана открытая схема установки очистки сточных вод, которая пока еще широко применяется на месторождениях. Работает она следующим образом. Отделившаяся от нефти вода в отстойниках и в сепараторах-деэмульсаторах автоматически сбрасывается в песколовку, ловушку нефти 1, а затем перетекает в пруды-отстойники 3. Из прудов-отстойников вода забирается насосами 4 и подается через песчаные фильтры 5 в емкости очищенной воды 6. Из этих емкостей сточная вода поступает на прием насосов 7 и подается на кустовые насосные станции (КНС), где создается высокое давление (14,7 – 19,62 МПа), для закачки ее через нагнетательные скважины в пласт. В песколовках за счет разности в плотностях из сточной воды выпадают механические примеси.
В ловушках нефти из воды "улавливаются" (всплывают на поверхность) капельки нефти диаметром свыше 80 мкм; затем скопившаяся на поверхности воды нефть забирается насосом 2 и подается вновь в отстойники или сепараторы-демульсаторы (подогреватели). В прудах-отстойниках 3 в результате резкого снижения скорости воды (v>0,008 см/с) улавливаются капельки нефти размером до 30 – 40 мкм и оседают механические примеси. Окончательной, "тонкой" очистке сточные воды подвергаются в попеременно работающих песчаных фильтрах 5. Песчаные фильтры через определенное время

Рисунок 1. Открытая схема установки очистки сточных вод: 1 – ловушка нефти; 2 – насос для откачки ловушечной нефти; 3 – пруды-отстойники; 4 – насос для подачи воды на фильтры; 5 – песчаные фильтры; 6 – емкости для чистой воды; 7 – насос для подачи чистой сточной воды на КНС; 8 – насос для подачи чистой воды при промывке фильтров; 9 – пруд (амбар) для загрязненной воды необходимо промывать от осевших микрочастиц. Для промывки используется очищенная вода из емкости 6, подаваемая насосом 8. Грязная вода после очистки фильтров сбрасывается в амбар 9.
Недостатки описанной установки очистки сточных вод следующие: 1) ловушки нефти и пруды-отстойники сооружаются из железобетона, а это обходится очень дорого; 2) для строительства такой установки нужна большая площадь; 3) в процессе разработки нефтяного месторождения производительность этой установки должна постоянно увеличиваться в связи со все большим обводнением добываемой нефти; 4) сточная вода в данной установке контактирует с кислородом воздуха, который, растворяясь в ней, способствует коррозии водопроводов и насосов, перекачивающих эту воду.
Закрытые системы очистки сточных вод могут быть как напорными, так и безнапорными.
Закрытая напорная система очистки позволяет интенсифицировать процесс подготовки воды с применением отстоя и фильтрования под давлением, существенно снизить агрессивность сточной воды путем исключения контакта ее с кислородом воздуха, уменьшить количество загрязнений в воде, использовать остаточное давление газа после аппаратов УПН для очистки сточной воды и для транспорта уловленной нефти и осадка, сохранить свойства пластовых вод, наиболее полно и рационально использовать оборудование заводского изготовления. Из-за отсутствия контакта сточной воды с кислородом воздуха коррозионная активность ее не повышается и не происходит окисления гидрата закиси железа Fе(ОН)2 в гидрат окиси Fе(ОН)3, а это значит, что не происходит и выпадения последнего в осадок, снижающий приемистость нагнетательных скважин.
К недостаткам закрытых систем следует отнести необходимость строительства параллельного блока очистки для поверхностных промливневых стоков, расход которых обычно колеблется в пределах 7 – 10% от расхода вод, сбрасываемых из аппаратов УПН.
Рассмотрим установки очистки сточных вод закрытого типа, в которых не происходит контакта воды с воздухом.
УПВ работает следующим образом. Из сепаратора-деэмульсатора сточная вода с ПАВ сбрасывается в линии la и 1, из которых она поступает на смешение с нефтяной эмульсией и в герметизированные емкости 2 и 7 УПВ. В емкостях 2, показанных на рисунке в поперечном разрезе, имеются гофрированные гидрофобные пластины 3, к которым могут прилипать капельки нефти, скапливаться на них и в виде тонкой пленки двигаться по гофрам этих пластин к верхней образующей емкостей 2.
Скопившуюся в верхней части емкостей 2 нефть отбирают насосом 4 и по нефтепроводу 5 подают на вход теплообменников для доведения ее до кондиции в сепараторах-деэмульсаторах. Отстоявшаяся в емкостях 2 вода самотеком по водоводу 6 поступает в емкости для хранения чистой воды 7. Из емкостей 7 вода забирается насосом 8 и подается на КНС для закачки ее в нагнетательные скважины. Так осуществляется система использования сточной воды по замкнутому циклу без контакта с кислородом воздуха.
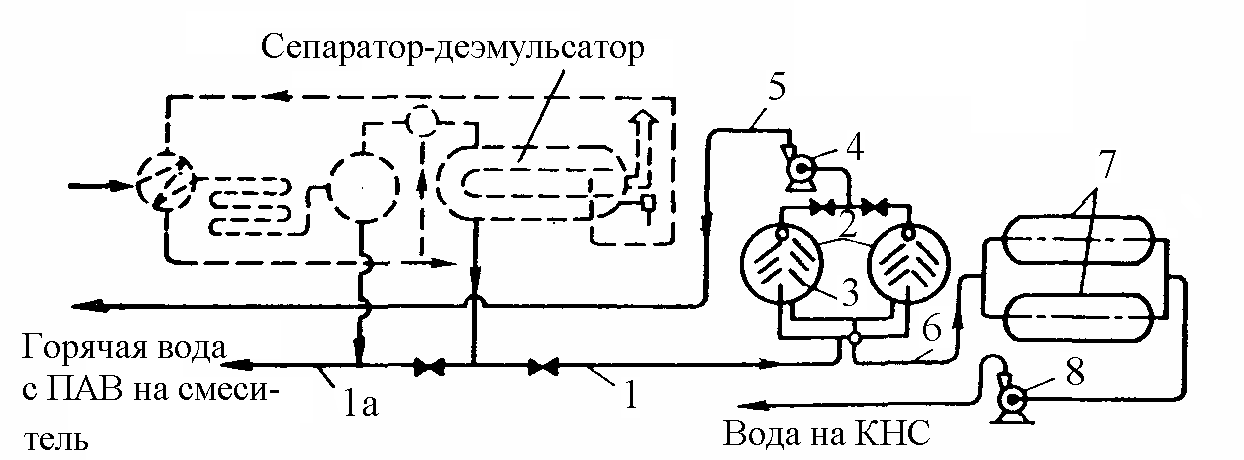
Рисунок 2. Установка очистки сточных вод закрытого типа: la, 1 – линии для транспорта сточной воды; 2, 7 – герметизированные емкости; 3 – гофрированные гидрофобные пластины; 4 – насос для откачки нефти; 5 – нефтепровод; 6 – водовод; 8 – насос для подачи води на КНС