Файл: Реферат учебной дисциплины Техническая документация по специальности среднего профессионального образования.docx
Добавлен: 07.11.2023
Просмотров: 45
Скачиваний: 2
ВНИМАНИЕ! Если данный файл нарушает Ваши авторские права, то обязательно сообщите нам.
Министерство образования и науки Российской Федерации
Федеральное государственное бюджетное образовательное учреждение
высшего образования
Воронежский государственный лесотехнический
университет имени Г.Ф. Морозова
Кафедра: «Производства, ремонта и эксплуатации машин»
РЕФЕРАТ
Учебной дисциплины
Техническая документация
по специальности
среднего профессионального образования
23.02.07 «Техническое обслуживание и ремонт двигателей,
систем и агрегатов автомобилей»
ТЕМА: «Порядок разработки технологических процессов на ремонтные работы »
Студент ТО1-192-ОТ (номер группы) Руководитель к.т.н., доцент (ученая степень, ученое звание) | _________ (подпись) _________ (подпись) | Лебедев П.С. (Фамилия И. О.) Жайворонок Д.А. (Фамилия И. О.) |
-
г.
Содержание
Содержание 2
1.ПОРЯДОК РАЗРАБОТКИ ТЕХНОЛОГИЧЕСКИХ ПРОЦЕССОВ НА РЕМОНТНЫЕ РАБОТЫ. 3
2.Ремонт и ТО двигателя 10
Заключение 19
Список использованной литературы 20
Порядок разработки технологического процесса существует на каждом предприятии. При таком положении завод-изготовитель не может обеспечить всей потребности в снабжении парка автомобилей запасными частями. Эта задача решается путем организации специализированных заводов по производству запасных частей и восстановлению сложных и металлоемких деталей на авторемонтных предприятиях или на специализированных заводах по восстановлению деталей.
Качество деталей задается техническими требованиями, которые определены рабочим чертежом детали. Рабочий чертеж детали является основным исходным документом при разработке технологического процесса изготовления детали. Он должен содержать все данные, необходимые для изготовления детали.
|
-
ПОРЯДОК РАЗРАБОТКИ ТЕХНОЛОГИЧЕСКИХ ПРОЦЕССОВ НА РЕМОНТНЫЕ РАБОТЫ.
Технологический процесс ремонта — часть производственного процесса, связанная с выполнением основных работ по ремонту автомобиля: разборка его на агрегаты, узлы, детали; ремонт деталей; сборка, испытание и окраска; сдача автомобиля заказчику. Эти работы выполняются в определенной последовательности в соответствии с технологическим процессом.
Элементами технологического процесса являются следующие его части.
Операция — часть технологического процесса ремонта, выполняемая непрерывно на одном рабочем месте, определенным видом оборудования, рабочими одной профессии. Операция обычно носит название оборудования, с помощью которого производится операция. Например, сборочная операция выполняется в сборочном цехе с использованием сборочного оборудования слесарем-сборщиком и т. д.
Установка — часть операции, выполняемая на изделии при изменении его положения относительно оборудования, инструмента. Например, сборочная операция автомобиля состоит из установки двигателя, коробки перемены передач и т. д.
Переход — часть операции, установки, выполняемая над одним участком изделия, одним инструментом, работающим в одном и том же режиме. Например, установка двигателя состоит из нескольких переходов: строповка двигателя; поднять, перенести, поставить двигатель на раму; закрепить двигатель на раме.
Проходом называется один из нескольких переходов, следующих друг за другим. Например, переход — строповка двигателя состоит из двух проходов — увязка одного стропа на двигателе с одной стороны и закрепление другого конца на крюке крана; то же самое, но со вторым стропом и с другой стороны двигателя.
Рабочий прием — часть перехода или прохода, представляющая собой законченный цикл рабочих движений. Например, закрепление одного конца стропа на двигателе с одной стороны — один прием, закрепление другого конца стропа за крюк крана — другой рабочий прием.
Рабочее движение — наименьший момент операции. Например, взять деталь есть рабочее движение.
Разработка технологического процесса состоит в том, что для каждого его элемента устанавливаются описание содержания работ, необходимое оборудование, приспособления и инструмент, сложность работ и нормы трудозатрат. Все эти данные заносятся в технологические карты. В зависимости от объема выполняемых работ устанавливается различная глубина разработки техпроцесса. Для небольших предприятий с малым объемом работ техпроцесс разрабатывается на уровне операций и установок с использованием универсального оборудования и инструмента. В технологической карте указывается только порядок выполнения операций (маршрутная технологическая карта). Работы производятся рабочими высокой квалификации.
Для СТОА с достаточно большим объемом работ разработка технологического процесса ведется на уровне переходов и проходов с указанием содержания работ по каждой операции. Работы выполняются на специальном оборудовании (стендах) с использованием специальных приспособлений и инструмента по операционным технологическим картам.
Разработка техпроцесса ведется отдельно для технического обслуживания ТО-1, ТО-2 и для ремонтных работ по текущему и капитальному ремонтам.
Наибольший объем выполняемых работ имеет место при капитальном ремонте автомобилей, который производится на специализированных авторемонтных заводах.
Принятые на ремонт автомобили проходят наружную мойку и поступают на операцию разборки. С рамы автомобиля, базовой детали снимают все агрегаты, очищают их от грязи, масла, разбирают на узлы и детали. Снятые детали сортируют на годные, негодные и требующие ремонта. Годные детали идут повторно на сборку, негодные детали отправляют на металлолом, детали, требующие ремонта, восстанавливают и направляют на сборку узлов. Узлы собирают в агрегаты, агрегаты снова устанавливают на раму автомобиля. Собранный автомобиль испытывают и сдают заказчику.
Важно отметить, что по такой же схеме производится разработка технологического процесса проведения текущего ремонта с той особенностью, что в этом случае меньше количество и выполняются они в меньшем объеме.
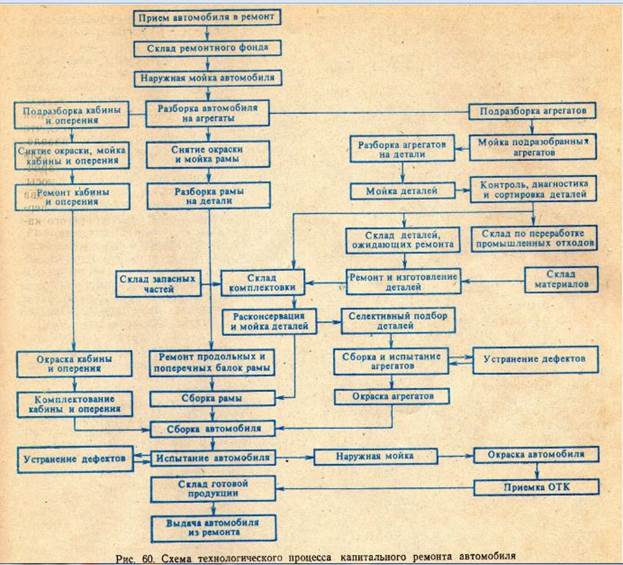
Рис.1.1 - Схема технологического процесса ремонта
Технологический процесс ремонта электрооборудования состоит ИЗ следующих этапов работ.
1. Наружная очистка. Обычно осуществляется сухим или слегка смоченным в керосине обтирочным материалом. Аккумуляторные батареи хорошо очищаются теплым или горячим раствором кальцинированной соды или горячей водой.
2. Внешний осмотр. На этом этапе дается предварительная оценка состояния агрегатов электрооборудования. Осмотр генератора, стартера проводится при снятой защитной ленте, что позволяет оценить состояние коллектора и щеток.
Реле-регуляторы,реле сигналов и другие реле осматривают при снятой крышке.
3. Предварительная проверка проводится с применением контрольного оборудования и стендов для выяснения электрических дефектов. Генераторы проверяют на частоту вращения при номинальном напряжении без нагрузки и с полной нагрузкой, а также в режиме электродвигателей. Стартеры и электродвигатели проверяют в режиме холостого хода, фиксируя потребляемую силу тока и частоту вращения вала якоря, распределители и катушки зажигания на бесперебойность искрообразования и т. д. С учетом выявленных дефектов приступают к ремонту, который может быть произведен о частичной или полной разборкой.
4. Разборка на узлы и детали. Для предупреждения повреждения деталей и сокращения времени на разборку необходимо применять специально предназначенные для выполнения этих работ инструменты и приспособления (съемники, торцовые ключи, прессовые отвертки и т. п.), а в условиях специализированного производства механический разборочный инструмент (гайковерты, специализированные разборочные стенды и т. д.). Детали укладывают на стеллаж или в специальную тару.
Следует иметь в виду, что в условиях специализированного производства (мастерские, авторемонтные предприятия), где ремонт производится обезличенным методом, работы, перечисленные в пунктах 1, 2, 3, не производят, а сразу же приступают к разборке поступивших в ремонт агрегатов электрооборудования.
5. Очистка и сушка деталей. Промывку производят волосяными кистями в бензине или керосине в моечных ваннах, размещенных подвытяжными колпаками с отсосом паров топлива. В условиях специализированного производства целесообразно применять машинную мойку с применением моечных растворов. Сушку деталей желательно проводить в потоке горячего воздуха при температуре до 110° С.
Войлочные и фетровые защитные уплотнители подшипников и смазочные фитили промывают в чистом бензине с последующим отжатием.
Детали с обмотками протирают обтирочным материалом, смоченным в бензине с последующим обдувом сжатым воздухом.
6. Контроль состояния узлов и деталей производится внешним
осмотром или специальной аппаратурой и инструментами. Электриче
скую прочность изоляции обмоток проверяют под напряжением 220—
550 В.
В результате проверок в соответствии с техническими условиями детали и узлы сортируют на годные к дальнейшему использованию без ремонта, требующие ремонта и негодные.
7. Ремонт узлов и деталей, включая перемотку обмоток и замену изоляции.
8. Сборка агрегатов и приборов производится в соответствии с техническими условиями с последующей приработкой подшипников, щеток и других сопряжений.
9. Контрольные испытания позволяют определить качество ремонта и сборки, а также получить данные, характеризующие надежную работу в дальнейшем агрегата или прибора электрооборудования.
10. Регулировка производится в соответствии с техническими условиями на определенную модель агрегата или прибора.
11. Окраска наружной поверхности электрических агрегатов и приборов необходима для обновления вида выпускаемой из ремонта продукции.
-
Ремонт и ТО двигателя
Проверка технического состояния двигателя на автомобиле
Проверка технического состояния двигателя включает проверку его мощности, экономичности, расхода (угара) масла, компрессии в цилиндрах двигателя, шумности его работы и токсичности отработавших газов.
Проверка мощности двигателя производится по изменению динамических качеств автомобиля — по уменьшению максимальной скорости, а также динамики разгона. Максимальная скорость и динамика разгона определяются в результате дорожных испытаний при полностью исправной ходовой части. Исправность ходовой части автомобиля определяется по выбегу автомобиля, т. е. по расстоянию, которое проходит автомобиль на нейтральной передаче со скорости 50 км/ч до полной остановки. Максимальная скорость и время разгона определяются на контрольном участке дороги длиной 1 км.
Все дорожные испытания проводятся с полностью прогретым двигателем на горизонтальном прямолинейном участке дороги с ровным асфальтовым или бетонным покрытием при наличии в автомобиле двух человек, включая водителя, в сухую погоду и при отсутствии сильного ветра.
Выбег автомобиля определяется по двум заездам во взаимно-противоположных направлениях как среднее из двух значений с соблюдением вышеперечисленных условий. Выбег легкового автомобиля обычно составляет не менее 400 м.
Максимальная скорость автомобиля определяется с предварительным разгоном его до максимальной скорости на высшей передаче к началу мерного участка (1 км) по результатам прохождения мерного участка на максимальной скорости в двух взаимнопротивоположных направлениях. При этом измеряется время t прохождения участка 1 км в секундах, по которому определяют максимальную скорость v по формуле v =3600/t. За действительное значение максимальной скорости принимается среднее арифметическое скоростей, полученных по результатам двух заездов во взаимно-противоположных направлениях.
Динамика разгона автомобиля определяется по времени разгона до 100 км/ч либо по времени прохождения 1 км с места при интенсивном разгоне автомобиля с последовательным и быстрым переключением передач также по двум заездам во взаимно-противоположных направлениях.
Полученные в результате дорожных испытаний значения сравнивают с паспортными данными автомобиля. Снижение максимальной скорости на 10...15%, а также увеличение времени разгона на 20...25% указывают на недостаточную мощность двигателя и необходимость более детальной проверки его состояния в целях определения причин, вызвавших снижение мощности и их устранения.