Файл: Электрические и магнитные методы неразрушающего контроля.rtf
Добавлен: 07.11.2023
Просмотров: 99
Скачиваний: 3
ВНИМАНИЕ! Если данный файл нарушает Ваши авторские права, то обязательно сообщите нам.
Министерство Образования и Науки Кыргызской Республики
Министерство Образования и Науки Российской Федерации
Кыргызско-Российский Славянский Университет
Естественно-Технический Факультет
Кафедра Приборостроение
Курсовая работа
по дисциплине: Основы автоматического управления
на тему: Электрические и магнитные методы неразрушающего контроля
Выполнил: Коноплев Т.Д.
Проверил: Муслимов А.П.
Бишкек 2021
Содержание
Введение
Электрические МНК
Электроемкостной метод контроля
Электропотенциальные методы
Термоэлектрическиеметоды
Магнитные методы МНК
Магнитопорошковый МНК
Магнитографический метод
Феррозондовый метод
Индукционный метод
Сравнение разрушающих и неразрушающих методов контроля
Список источников и литературы
Введение
Улучшение качества промышленной продукции, повышение надежности и долговечности оборудования и изделий возможно при условии совершенствования производства и внедрения системы управления качеством.
Система контроля качества продукции является одной из существеннейших частей системы управления качеством. На каждом этапе развития общественного производства существовали специфические требования к качеству продукции. На ранних стадиях становления промышленности основными требованиями к качеству являлись точность и прочность. Масштабы производства позволяли проводить проверку каждого и отбраковку дефектных изделий.
По мере развития промышленного производства продукция становилась все более сложной, число ее характеристик постоянно росло. Встал вопрос проверки не отдельных свойств изделий, а его функциональной способности в целом. Начала складываться система контроля качества продукции, суть которой заключалась в обнаружении дефектной продукции и изъятии ее из производственного процесса. Контроль качества продукции состоит в проверке соответствия показателей её качества установленным требованиям.
До недавнего времени на металлургических предприятиях, выпускающих трубы, на контроле было занято до 18-20% рабочих, при этом разрушению подвергались до 10-12% труб от партии. На машиностроительных заводах количество разрушенных деталей порой достигает 15-20% от партии, поскольку после каждой основной технологической операции из деталей выполняются образцы для механических и металлографических испытаний.
Важными критериями высокого качества деталей машин, механизмов, приборов являются физические, геометрические и функциональные показатели, а также технологические признаки качества, например, отсутствие недопустимых дефектов; соответствие физико-механических свойств и структуры основного материала и покрытия; соответствие геометрических размеров и чистоты обработки поверхности требуемым нормативам и т.п.
Широкое применение неразрушающих методов контроля, не требующих вырезки образцов или разрушения готовых изделий, позволяет избежать больших потерь времени и материальных затрат, обеспечить частичную или полную автоматизацию операций контроля при одновременном значительном повышении качества и надежности изделий. В настоящее время ни один технологический процесс получения ответственной продукции не внедряется в промышленность без соответствующей системы неразрушающего контроля.
Электрические методы
Электрические методы неразрушающего контроля (ЭМНК) основаны на создании в контролируемом объекте электрического поля либо непосредственным воздействием на него электрическим возмущением (например, электростатическим полем, полем постоянного или переменного тока), либо косвенно с помощью воздействия возмущениями неэлектрической природы (например, тепловым, механическим и др.). В качестве информативного параметра используются электрические параметры объекта контроля (емкость, тангенс угла потерь, проводимость).
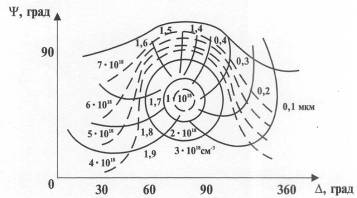
Рисунок 1 – Номограмма


- линии равной концентрации
- линии равной толщины
По назначению ЭМНК делятся по определению исследуемых характеристик состава и структуры материала на электроемкостные, электропотенциальные и термоэлектрические.
1. Электроемкостной метод контроля (ЭМК) предусматривает введение объекта контроля или его исследуемого участка в электростатическое поле определение искомых характеристик материала по вызванной им обратной реакции на источник этого поля.
Информативность ЭМК определяется зависимостью первичных параметров емкости, тангенса угла потерь от характеристик объекта контроля, (диэлектрической проницаемости и коэффициента диэлектрических потерь (см. рис. 2). Косвенным путем с помощью ЭМК можно определить и другие физические и структурные характеристики материала: плотность, содержание компонентов, механические параметры, радиопрозрачность, толщину, проводящие и диэлектрические включения и т.п.
Примеры значений диэлектрической проницаемости и тангенса угла диэлектрических потерь электроизоляционных материалов на высоких частотах 105-108 Гц приведены в приложении.
2. Электропотенциальные методы.
Работа электропотенциальных приборов основана на прямом пропускании тока через контролируемый участок и измерении разности потенциалов на определенном участке.
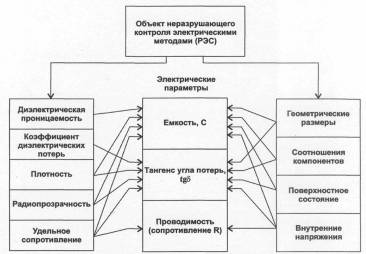
Рисунок 2 – Схема воздействия характеристик объекта
контроля на электрические параметры
При пропускании через электропроводящий объект электрического тока в объекте создается электрическое поле. Геометрическое место точек с одинаковым потенциалом составляет эквипотенциальные линии (рис. 3). На рисунке показано распределение эквипотенциальных линий при отсутствии (рис. 3,а) и наличии дефекта (рис. 3,6). Разность потенциалов зависит от трех факторов: удельной электрической проводимости а, геометрических размеров (например, толщины) и наличия поверхностных трещин. При пропускании переменного тока разность потенциалов будет зависеть и от магнитной проницаемости м.
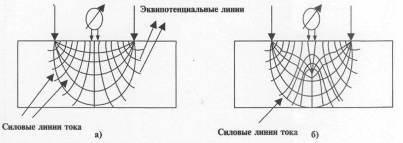
Рисунок 3 – Распределение эквипотенциальных линий
В приборах имеется четыре электрода. С помощью двух из них (токопрово-дящих) к контролируемому участку подводится ток, а два других измерительные измеряют разность потенциалов на определенном расстоянии (обычно не более 2 мм), по которой судят о глубине обнаруженной трещины.
Электропотенциальные приборы применяют для измерения толщины стенок деталей, для изучения анизотропии электрических и магнитных свойств, обусловленной приложенными к объекту контроля механическими напряжениями, но основное назначение этих приборов – измерение глубины трещин, обнаруженных другими методами неразрушающего контроля. Электропотенциальный метод с использованием четырех электродов, является единственным методом, который позволяет осуществить простое измерение глубины (до 100 - 120 мм ) поверхностных трещин.
В этом смысле характерным представителем таких приборов является прибор – измеритель глубины трещин типа ИГТ – 10НК позволяющий контролировать глубины трещин от 0,5 до 20 мм в ферромагнитных, аустенитных сталях с 10% относительной погрешностью.
Применение измерителей глубины трещин совместно с другими методами, например, магнитопорошковым или капиллярным, позволяет повысить эффективность обнаружения трещин.
Помимо контроля трещин электропотенциальные методы используются при контроле удельного сопротивления полупроводниковых структур.
3. Термоэлектрические методы.
Приборы неразрушающего контроля, основанные на термоэлектрическом методе, находят применение при контроле деталей по маркам сталей, при контроле полупроводниковых пластин по типам проводимостей и т.д.
а) Контроль деталей по маркам сталей.
Источником информации о физическом состоянии материала при термоэлектрическом методе неразрушающего контроля является термо-ЭДС, возникающая в цепи, состоящей из пары электродов (горячего и холодного) и наличие контролируемого металла или полупроводника.
Обработка информации может проводиться или путем прямого преобразования или дифференцированным методом (рис. 4,а и рис. 4,б).
Сущность работы приборов по схеме прямого преобразования заключается в следующем. Контролируемый образец 1 помещают на площадку холодного электрода 3. К контролируемой поверхности прикасаются горячим электродом 2, нагреваемым элементом 4. В месте контакта горячего электрода возникает термо-ЭДС, и ток начинает протекать в цепи, в которую включен индикаторный прибор V.
При работе прибора по дифференцированной схеме к холодным электродам, на которых размещены: образец 5 из известной марки стали и контролируемая деталь 1, подключен индикаторный прибор V. К этим деталям одновременно прикасаются горячим электродом - щупом 2 и, наблюдая за показаниями индикаторного прибора V, судят о принадлежности контролируемой детали к марке стали образца.
Регистрация результатов контроля возможна тремя способами: по углу отклонения стрелки индикаторного прибора, по измерению знака термо-ЭДС и по индикации нулевого показания.
В таблице 1. приведены значения термо-ЭДС для некоторых сталей.
Контроль типа проводимости монокристаллических слитков и пластин
Для (кремния или арсенида галлия)
n – типа горячий токоподвод имеет положительную полярность, а холодный – отрицательную. При нагреве токоподвода скорость электронов в нем становится больше, чем в холодном, поэтому они диффундируют от горячего токоподвода к холодному до тех пор, пока горячий токоподвод, отдавший электроны, не окажется заряженным положительно а холодный токоподвод получивший избыток, зарядится отрицательно (рис.5,а) (в кремнии или арсениде галлия), дырки диффундируют от горячего токоподвода к холодному и горячий токоподвод заряжается отрицательно (рис.5,б).
Таблица 1
Значения термо-ЭДС для марок сталей.
Марка стали | Значение термо-ЭДС, мВ |
40Х14Н14В2М | 0,30 – 0,38 |
10Х18Н10Т | 0,27 – 0,36 |
ЗОХГСНА | 0,16 – 0,28 |
18ХНВА | 0,15 – 0,27 |
ЗОХГСА | 0,12 – 0,18 |
ЭИ868 | 0,13 – 0,19 |
12ХНЗА | 0,02 – 0,06 |
10 | -0,07 – +0,09 |
20 | -0,09 – +0,11 |
25 | -0,09 – +0,11 |
45 | -0,11 – +0,11 |
15ХА | -0,17 – +0,11 |
ЭИ617 | -0,21 – +0,14 |
16ХГТА | -0,27 – +0,20 |
ЭИ617 | -0,28 – +0,23 |
16ХГТА | -0,27 – +0,30 |
ЭИ347 | -0,28 – +0,23 |
10X18 | -0,27 – +0,30 |
Р18 | -0,30 – +0,32 |
20X23 | -0,31 – +0,33 |
10Х12М | -0,37 – +0,41 |
10X12Ф1 | -0,40 – +0,46 |
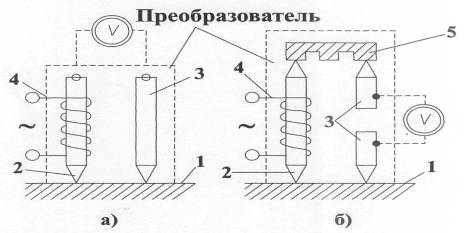
Рисунок 4 – Схемы контроля путем прямого преобразования (а) и диф-ференцированным методом(б)
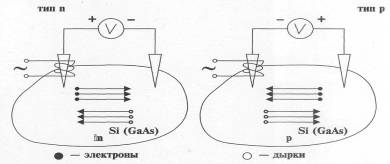