Файл: Отходы, выбросы и сбросы на производстве изопрен одностадийным способом.docx
ВУЗ: Не указан
Категория: Не указан
Дисциплина: Не указана
Добавлен: 09.11.2023
Просмотров: 35
Скачиваний: 1
ВНИМАНИЕ! Если данный файл нарушает Ваши авторские права, то обязательно сообщите нам.
ОТХОДЫ, ВЫБРОСЫ И СБРОСЫ НА ПРОИЗВОДСТВЕ «ИЗОПРЕН ОДНОСТАДИЙНЫМ СПОСОБОМ»
Синтез ДМД проводят путем конденсации изобутилена и формальдегида в реакторах синтеза ДМД в присутствии ортофосфорной, щавелевой и оксиэтилидендифосфоновой (ОЭДФ) кислот в качестве катализатора процесса.
Сырьем для синтеза диметилдиоксана являются изобутан-изобутиленовая фракция и безметанольный формалин.
Перед подачей в реактор БМФ и ИИФ смешивают с раствором катализатора (ОФК) и подогревают. Реакционную массу после реакторов синтеза ДМД подают на охлаждение и сепарацию на масляный и водный слои. Водный слой выводят на дегазацию и упарку, после чего концентрированный водный раствор ОФК возвращают в реакторы синтеза ДМД. Масляный слой направляют на узел перегонки, где происходит выделение ДМД. Синтез ТМК из изобутилена и воды проводят в реакторах синтеза ТМК. Перед подачей в реактор исходные компоненты подогревают. После реактора синтеза ТМК реакционную массу охлаждают и перегоняют в колонне для отгонки изобутановой фракции от фракции ТМК.
Синтез изопрена проводят в реакторах кожухотрубчатого типа. В реакторе протекают гидролиз и конденсация углеводородов с получением изопрена, изобутилена, пирановых спиртов, тяжелых побочных продуктов. В реактор синтеза изопрена в качестве питания подают кислый водный слой и углеводороды (содержащие ДМД, ТМК).
Поскольку в технологии отсутствует стадия каталитического расщепления ДМД на изопрен, формальдегид и воду, процесс условно назван «одностадийным». После реакторов синтеза изопрена углеводороды конденсируют, охлаждают и подают на выделение непрореагировавшего изобутилена в ректификационную колонну.
Изобутилен с верха колонны подают на узел синтеза ТМК, а изопренсодержащую фракцию с куба подают в отделение выделения и очистки изопрена. Изопренсодержащую фракцию подвергают последовательной перегонке в ректификационных колоннах с выделением тяжелых углеводородов, изобутилена, далее изопрен подвергают отмывке от карбонильных соединений в экстракционных колоннах и химической очистке. Очищенный изопрен откачивают на склад.
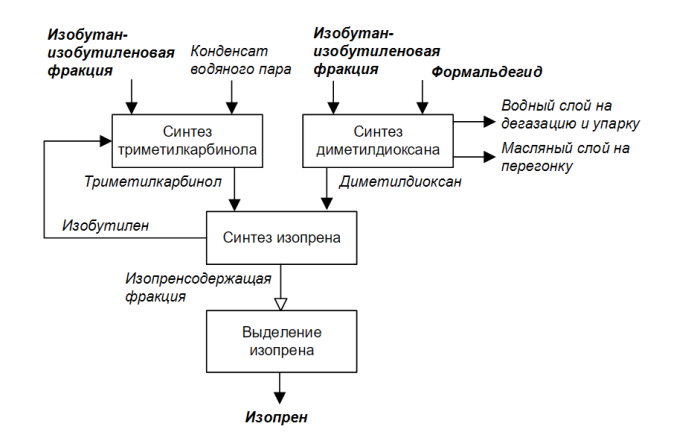
https://docs.cntd.ru/document/564068892
Сточные воды при производстве изопрена.
№ | Наименование сбрасываемых сточных вод | Место сбрасывания | Периодичность | Количество | Требования к качеству стоков | Куда направляется сток |
1 | Химзагрязненные Сточные воды | Общий сток завода ИМ, колодец ХЗК №775 | Постоянно | 121 м3/час | Метанол не более 100 мг/дм3 ХПК не более 2500 мгО2/дм3 Температура не более 40°С Формальдегид не более 150 мг/дм3 Аммоний-ион факультативно мг/дм3 рН 2.5-9.0 ед. рН | БОС |
| | | | | | |
Твердые отходы при производстве изопрена.
№ | Наименование | Состав в % | Периодичность | Количество | Место накопления | Операция по обращению с отходами. |
1 | Кокс | Углерод-100% | После чистки оборудования | 50-150 тонн | Собирается на бетонной площадке после чистке аппаратов. | Размещение (захоронение) на полигоне промышленных отходов ПАО НКНХ. |
2 | Катализатор-сульфокатионит | Полистирол-97.5% Вода-2.5% | После перегрузки реакторов | 505 тонн | Собирается на бетонной площадке после чистке аппаратов | Используется на производстве МТБЭ или продается на регенерацию. |
Выбросы в атмосферу при производстве изопрена.
№ | Место сбрасывания на факел | Позиция прибора | Периодичность | Количество | Позиция факела | Состав |
1 | Наружная установка №2 | 6593 | Постоянно | 1-100 м3/час | Р-16/4, Р-16/4а | Азот, изобутан, изобутилен, изопрен. |
2 | Наружная установка №3 | 6591 | Постоянно | 1-100 м3/час | Р-16/4а | . Азот, изобутан, изобутилен, изопрен |
Технологический регламент производство изопрена.
Основные отходы производство изопрена «Одностадийным способ»:
-
Кокс -
Большое количество стоков в ХЗК -
Сбросы на факел
На первом этапе получают деметилдиоксан (ДМД) синтез ДМД путем жидкофазной конденсации изобутилена и формальдегида в присутствии кислоты ОФК. На этой стадии проводится отмывкакатализаторах при давлении 17-22 кг/см2 и температуре 90-100 масляного слоя реакционной смеси ДМД от формальдегида и кислот паровым конденсатом в отмывной колонне со сбросом фузельной воды в цех водоочистки и водоотведения. Масляный слой направляется на ректификацию в специальные колонны, где происходит отгонка изобутана, изобутилена и других лёгких углеводородов, отдувки в линию контактного газа на компремирование.
Выделение фракции ДМД-ректификата осуществляется методом ректификации в колонне, работающей под вакуумом, остаточное давление в которой должно соответствовать параметрам 70-30 мм.рт.ст. Отогнанная фракция ДМД направляется на разложение, а кубовый продукт колонны, представляющий собой высококипящие побочные продукты (ВПП), направляется на фракционирование, в ходе которой получают такие продукты как оксаль и оксанол, в которые складируются для отгрузки потребителю. В ином случае ВПП направляются в реакторы разложения. Для этого фракцию ВПП подогревают в теплообменнике до температуры не более 250°С и подают в реактор. Здесь в присутствии катализатора и перегретого пара происходит термокаталитическое разложение ВПП. ( Технологический регламент)
На первом же этапе получение изопрена мы видим образования большего количества отходов в виде высококипящих побочных продуктов. Легкие ВПП утилизируются на том же производстве до формальдегида и изобутилена. Но недостатком данного метода является образование большого количества кокса на узле конденсации. В период капитального ремонта вывозится до 100 тонн кокса. На данный момент нет квалифицированного применения данного кокса из-за чего, ведутся его захоронения на полигоне для отходов.
Частично решить эту проблему возможно с помощью патента №2461538 общество с ограниченной ответственностью «Научно-производственное объединение ЕВРОХИМ». В своем патенте предлагают уменьшить образование кокса и органических соединений в водном слое на узле конденсации. Путем подачи в линию контактного газа изопреновую фракцию. Реакция разложения ВПП проходит в реакторах на твердом катализаторе при температуре не более 450°С
На выходе из реактора контактный газ охлаждается в первом теплообменнике охлаждается паровым конденсатом до температуры 250°С и выработкой вторичного пара далее контактный газ охлаждается горячей до температуры 90°С и поступает в холодильник для захолаживания до 25-30°С Главным условием патента является подачи изопреновой фракции в контактный газ является температура контактного газа 90-45°С и соотношение контактный газ: изопреновая фракция 1:0.2-5.
https://new.fips.ru/registers-doc-view/fips_servlet?DB=RUPAT&DocNumber=2461538&TypeFile=html
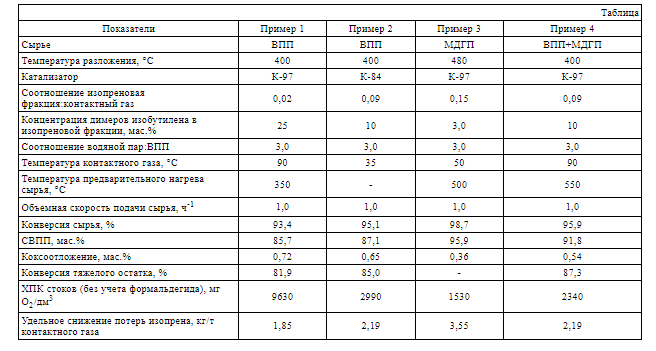
На разложение высококипящих побочных продуктов затрачивается большое количество водяного пара вследствие чего происходит образование огромного количество сточных вод в которых содержится не только органические вещества, влияющие на ХПК, но и формальдегид из-за последнего погибают бактерии на очистных сооружениях. Водный слой содержащий в себе формальдегид поступает в ректификационную колонну, где извлекается формальдегид. Но недостатком данного метода является проскок формальдегида.
Из патента № 2432349 патентообладателем является Открытое акционерное общество Научно-исследовательский институт "Ярсинтез" (ОАО НИИ "Ярсинтез"). В патенте прописан метод получения метилаля с помощью реакции формальдегида с метанолом. Реакция проходит в комфортных условиях то есть при атмосферном давлении и температуре 80-90°С Конверсия формальдегида и метанола достигает 99.9%. Этот метод возможно внедрить и использовать воду после ректификационной колонны в которой так же содержится формальдегид. Этим методом можно будет полностью очистить воду сбрасываемую в ХЗК от формальдегида и получить готовый продукт метилаль. https://fips.ru/iiss/document.xhtml?faces-redirect=true&id=f6c06badeae2ea20b8a2e3e3cd7f248f
Улучшение качество сточных вод можно добиться за счет фильтрования. В период остановочного капитального ремонта или выводе на чистку какого либо оборудования образуется большое количество полимера мелкие частички кокса. Которые в свою очередь попадают в ХЗК. Из справочника НТД предлагается метод предварительной очистки сточных вод применяемых на разных предприятиях, но на производстве изопрена его нет. Сущность метода: Для глубокой очистки воды от загрязнений большинство предприятий используют фильтрование, представляющее собой процесс улавливания загрязнений в пористой среде, которая может быть образована зернистыми минеральными, искусственными полимерными и волокнистыми материалами. Процесс очистки происходит за счёт адгезии загрязнений к поверхности загрузки, а также вследствие их механического улавливания в её порах. В качестве зернистых загрузок несколько предприятий используют песок, керамзит, цеолит, гравий, горелые породы, антрацит и проч.; многие предприятия используют искусственные загрузки (полистирол, пенополиуретан, волокнистые отходы синтетических волокон). На ряде предприятий, очистные сооружения которых оборудованы в последнее десятилетие, предусмотрена регенерация искусственных материалов, использованных в качестве загрузок. От эффективной регенерации фильтровальных загрузок зависит эффективность и продолжительность использования загрузки. На нескольких предприятиях зернистые фильтры дооснащали узлом интенсивной регенерации. На рассмотренных предприятиях фильтры работают при подаче на них сточных вод как под давлением, так и без него. В первом случае они имеют герметичный корпус. Особую роль в
конструкции фильтра играет дренажная система, через которую отводится очищенная в фильтре вода.
№ | Название |
8 | «Очистка сточных вод при производстве продукции (товаров), выполнении работ и оказании услуг на крупных предприятиях» |
На стадии разложение деметилдиоксана ДМД ряд побочных продуктов которые не находит квалифицированное применение и продаются в качестве печного топлива при не соответствии требованиям так же уходит на полигон захоронения. Процесс проводится в трубчатых реакторах при температуре 150-170°С и давление 0.9 Мпа. В присутствии ортофосфорной кислоты. Подвод тепла осуществляется с помощью подачи пара давления 1,4Мпа. В реакторах проходит реакция разложение ДМД до изопрена. Питанием в реактора служат смесь ТМК и ДМД соотношение которых должно быть 3:1. Так же в реактора подается изобутилен по отдельному вводу. Ортофосфорная кислота предварительно смешивается с паровым конденсатом и дозировано подается в реактора в зависимости от уменьшение кислотности в системе которое контролируется аналитическим контролем. Основными недостатками данной схемы является образования большого количества побочных продуктов которые прямо пропорционально влияют на количество сточных вод и сдувок на факел. Так же недостатком является коррозия металла из-за присутствии кислоты в процессе.
Данную проблему может частично решить техническое решение по патенту № 2554354.
1.Способ получения изопрена жидкофазным взаимодействием формальдегида и изобутилена и/или веществ, являющихся их источниками, например 4,4-диметилдиоксана-1,3 и триметилкарбинола, при повышенной температуре и давлении в присутствии в качестве катализатора водного раствора неорганической кислоты и катионов металлов, с отгонкой продуктов реакции и воды из реакционной зоны и последующим выделением изопрена, где синтез изопрена ведут в присутствии катализатора, включающего смесь либо орто- и пирофосфорных кислот, либо орто- и полифосфорных кислот, либо орто- и мета-фосфорных кислот и катионы металлов.
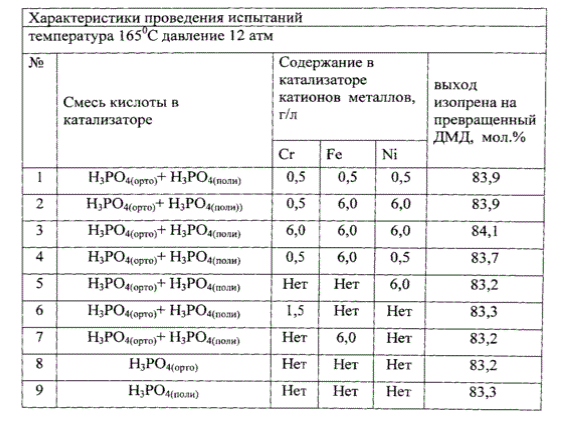