Файл: Реферат дисциплина Газовые турбины Задание выдано 2023 г.docx
Добавлен: 22.11.2023
Просмотров: 484
Скачиваний: 4
ВНИМАНИЕ! Если данный файл нарушает Ваши авторские права, то обязательно сообщите нам.
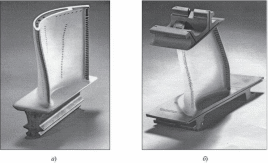
Рис.9. Рабочая и сопловая лопатки ГТУ типа SGT5-4000F (фирмы Siemens):
а)-рабочая лопатка; б)-сопловая лопатка;
Технология прецизионного вакуумного литья обеспечивает изготовление полых лопаток со сложной системой охлаждающих каналов. Для уменьшения и предотвращения дефектов материала на границах зерна применяются лопатки с направленной кристаллизацией и монокристаллические лопатки. Получаемые при этом преимущества по прочности обеспечивают возможность повышения допустимой температуры поверхности лопаток на 25 °С при направленной кристаллизации и на 50 °С при монокристаллах (в итоге эта температура достигает 950 °С).В перспективе намечается применение керамических материалов, что позволит увеличить температуру поверхности лопаток, КПД и мощность установки. Ведётся работа по повышению надёжности их изготовления, а также по улучшению таких параметров, как вязкость и коррозионная стойкость материалов. В Японии в рамках нового проекта «Солнечное сияние» (концерн Kawasaki) разрабатывается ГТУ мощностью 300 кВг с керамическими деталями на основе нитрида и карбида кремния. В США этим занимается компания Solar. Они планируют повысить Тнт до 1120 °С.
Итак, наиболее острым является вопрос долговечности турбинных лопаток. Их работоспособность определяет срок службы и экономичность ГТУ. По мнению специалистов, создание рабочей лопатки высокотемпературной ГТ — это сложная комплексная проблема. К такой лопатке предъявляется ряд требований:
1) Минимальные аэродинамические потери;
2) Высокие требования по сопротивлению ползучести, малоцикловому (термоциклическому) и многоцикловому (вибрационному) разрушениям;
3) Стойкости к коррозии и эрозии в окисляющей среде высокотемпературного газа;
4) Оптимизированная развитая система внутреннего охлаждения;
5) Защитные покрытия.
Для обеспечения высокой надёжности при эксплуатации лопаток, особенно первой турбинной ступени, применяются теплозащитные (термобарьерные слои) и антикоррозионные покрытия (обычно двухслойные: керамика + металл). Эти покрытия позволяют удлинить срок службы лопаток до 15 тыс. ч при температуре газов свыше 1200 °С. Существуют три основных типа покрытий:
а) термобарьерные с толщиной слоя 100—300 мкм. Они создаются на основе соединений ZrO
? и У703 и снижают температуру металла на 50— 150 °С;
б) диффузионные с толщиной слоя 25—75 мкм, увеличивающие стойкость лопаток к окислению и коррозии;
в) плазменные, позволяющие защищать лопатки как от коррозии и окисления, так и от воздействия высоких температур.
Конструкция проточной части позволяет заменить любую лопатку без извлечения ротора и дополнительной его балансировки. Все лопатки проточных частей ГТ и компрессора проходят индивидуальную стендовую проверку. Каждая лопатка взвешивается, и ее параметры вводятся в компьютер. Во избежание проблем с резонансными колебаниями количество сопловых лопаток ГТ выбирают равным или кратным простым числам. Масса отдельной лопатки может составить от К) до 30 кг. В табл. 1 в качестве примера приведены конструктивные параметры проточной части ГТУ типа ГТЭ-115-1170 (ОАО «Турбоатом», г. Харьков). Диаметр дисков рабочих лопаток обычно не превышает 2 м, а их толщина доходит до 600 мм. Ротор газотурбинного агрегата (компрессора и ГТ) вращается в опорных подшипниках, рабочие поверхности которых изготовлены из баббита.
Таблица 1. Конструктивные параметры проточной части ГТУ типа ГТЭ-115-1170
Параметр | Ступень газовой Турбины | |||
Первая | Вторая | Третья | Четвёртая | |
Высота сопловой лопатки, мм | 144 | 207 | 336 | 510 |
Высота рабочей лопатки, мм | 155 | 256 | 398 | 600 |
Число сопловых лопаток в ступени | 84 | 73 | 66 | 72 |
Число рабочих лопаток в ступени | 107 | 86 | 89 | 97 |
Реактивность ступени | 0,36 | 0,38 | 0,42 | 0,45 |
Распределение мощности по ступеням, % | 31 | 24 | 24 | 21 |
Упорный подшипник и один из опорных подшипников расположены в зоне входного патрубка компрессора. Второй опорный подшипник обычно находится в отдельном корпусе в зоне выходного патрубка ГТ. Подшипники смазываются и охлаждаются маслом, поступающим из масляной системы. Корпуса подшипников имеют горизонтальный разъем. Благодаря этому ревизия, ремонт и замена подшипников могут быть выполнены без вскрытия газотурбинного блока. При прохождении горячих газов по ступеням ГТ часть их попадает в зазор между обоймой сопловой решётки и ротором, а часть уходит через зазор между вершинами рабочих лопаток и корпусом турбины. Эти утечки рабочего тела не совершают полезную работу. Для уменьшения утечек газов между ступенями в турбине устанавливаются внутренние уплотнения разной конструкции (рис. 10). Герметизация вращающегося ротора со стороны компрессора и выходной части ГТ осуществляется концевыми уплотнениями различной конфигурации и соответствующей эффективности (рис. 11).
Статор газотурбинного агрегата состоит из отдельных секций: кожухов компрессора, КС и ГТ вместе с диффузором воздушного кожуха, кожухов компрессорного выхлопа, оболочки КС, кожухов турбины и выхлопа. Эти элементы корпуса, разделённые горизонтальным разъёмом на верхнюю и нижнюю половины, соединены болтами и образуют жёсткую конструкцию. Корпусной блок с помощью стульев со спаренными «мёртвыми» точками опирается на основную фундаментную раму.
Расположение некоторых ГТУ на раме типа салазок с максимально возможным размещением вспомогательных агрегатов, трубопроводов, электропроводки характерно для установок небольшой мощности. Такое конструктивное решение позволяет сократить сроки и затраты на монтаж, повысить его качество, упрощает устройство фундамента и облегчает доступ для осмотра и ремонта.
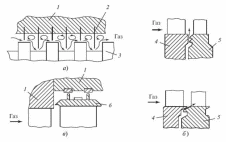
Рис.10. Уплотнения в проточной части турбины:
а — концевое; б — корневое; в — бандажное; 1,3 — корпус и ротор
турбины; 2 — гребень уплотнения; 4 — диафрагма; 5 — диск; 6 — бандаж
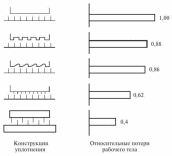
Рис.11.
Концевые уплотнения вала ГТ
Выходные газы ГТУ либо отводятся непосредственно в дымовую трубу, либо направляются для использования большей части их теплоты в теплообменниках, котле-утилизаторе и т. п. Во всех случаях в конце тракта устанавливается перекрывающая заслонка против ускоренного расхолаживания турбины тягой дымовой трубы в периоды простоя. На выходе из проточной части ГТ газы имеют высокую температуру (500—600 °С) и значительную осевую скорость, достигающую 200 м/с и более. Сопротивление газового тракта за ГТ преодолевается за счёт избыточного давления ее газов, и с его увеличением снижаются использованный теплоперепад и электрическая нагрузка ГТУ. При выборе конструктивной схемы выходного патрубка ГТ в виде диффузора учитываются требования эффективности и надёжности. Диффузор в современных ГТУ часто выполняется с осевым или диагональным выходом (рис. 12). Он обеспечивает снижение скорости газов и восстановление их давления, некоторое его увеличение по сравнению с давлением газов за последней турбинной ступенью, т. е. преобразование кинетической энергии в потенциальную.
Коэффициент полезного действия диффузора г|д равен отношению действительного прироста потенциальной энергии к максимально возможному при изоэнтропном сжатии (рис. 13):

Возрастание конечного давления газов за ГТ /;кт и его влияние на характеристики цикла Брайтона энергетической ГТУ приведены на рис. 4.26. Рост рк т на 1 % приводит к увеличению удельного расхода теплоты на 0,25—0,75 % и температуры Ткг на 1—2 %. Мощность ГТУ при этом уменьшается на 0,25—0,75 % так же, как и КПД установки рД. При этом неизменными остаются расход газов Сг и начальная температура Тнт.
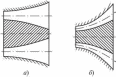
Рис.12. Схемы диффузора с осевым (а) и диагональным (6) выходами.
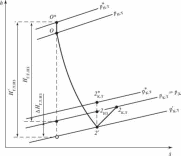
Рис.13. Рабочий процесс многоступенчатой ГТ с выходным диффузором в H-S диаграмме:
ДЯГТИЗ — увеличение располагаемого изоэнтропного теплоперепада в ГТ Ягтиз в результате установки выходного диффузора;
Ярт1П — полный располагаемый изоэнтропный теплопере- пад в ГТ с учетом установки диффузора
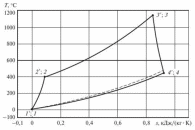
Влияние возрастания конечного давления газов за ГТ на
характеристики цикла Брайтона ГТУ.
4. Охлаждение газовых турбин.
С ростом начальной температуры газов растёт тепловая экономичность цикла ГТУ и уменьшается расход воздуха. Вместе с тем рост начальной температуры ограничен допускаемыми напряжениями в рабочих лопатках. В результате в ГТУ начальные температуры газа значительно ниже теоретически возможных, т.е. температур сжигания топлива с минимальным избытком воздуха, необходимым только для его окисления.
Охлаждение наиболее горячих элементов газовых турбин позволяет снизить их температуру при достаточно высокой температуре газа. Однако применение охлаждения уменьшает полезную работу ГТУ, так как часть теплоты, отбираемая охлаждающей средой от газа, не может быть преобразована в механическую работу, В некоторых случаях, если используется теплота охлаждающей среды, возможно частичное уменьшение этих потерь.
Снижение температуры элементов газовой турбины в результате охлаждения позволяет поднять термодинамический потенциал цикла ГТУ за счёт увеличения начальной температуры рабочего газа. Охлаждение целесообразно применять в том случае, когда выигрыш в кпд от возможного повышения начальных параметров рабочего газа больше потерь, вызываемых охлаждением.
Система охлаждения ГТУ должна удовлетворять следующим требованиям:
-
температура металла охлаждаемых деталей должна быть такой, чтобы его прочностные свойства обеспечивали заданный ресурс работы; -
градиенты температур охлаждаемых деталей не должны превышать значений, при которых температурные напряжения достигают опасных значений или возникает возможность недопустимого коробления деталей; -
затраты энергии на охлаждение должны быть значительно ниже дополнительной полезной энергии, вырабатываемой ГТУ за счет увеличения начальной температуры рабочего тела.