ВУЗ: Не указан
Категория: Не указан
Дисциплина: Не указана
Добавлен: 22.11.2023
Просмотров: 76
Скачиваний: 2
ВНИМАНИЕ! Если данный файл нарушает Ваши авторские права, то обязательно сообщите нам.
Маркировку выполняют теми же методами, что и рисунок печатных элементов (сеткографическим; фотохимическим и др.) на самоклеящихся-этикетках из полимерных пленок: полиимида, полиэстера, полиэфирамида с линейчатым (1D) штрих-кодом или двумерным (2D) матричным кодом. Высокая плотность размещения информации в матрице в виде темных и светлых прямоугольников позволяет закодировать большой объем информации вплоть до основных технических характеристик на этикетке шириной от 3 мм.
Информация на этикетку заносится на матричном, лазерном или термо-
трансферном принтерах. Наиболее перспективным является последний из-за высокого качества печати и производительности (до 14 000 долл.). Одной из фирм, занимающейся производством этикеток является фирма Brady Corp. (США).
Этикетки из полиимида можно размещать как на верхней, так и на нижней стороне ПП при пайке волной припоя или оплавлением припой-ной пасты; из полиэфирамида - на верхней при пайке волной припоя и на обеих сторонах при пайке оплавлением; из полиэстера - только на верхней при пайке волной припоя.
Фирмы Brady Corp. (США), Lackwcrke Peters GmbH (Германия), компания Beicrsdorf AG (Германия) выпускают, кроме этикеток, стрип-резисты (липкие аппликации из полиимида) для временной локальной защиты ПП при обработке в электролитах золочения, при облуживании, при левеллировании горячим воздухом, при пайке волной припоя и пр.
Лазерная маркировка ПП осуществляется одним из методов:
-
проекционным методом, при котором форма сечения лазерного луча задается с помощью маски и проецируется на ПП в нужном масштабе для получения любых сложных знаков идентификации; -
сканированием сфокусированного лазерного пучка на поверхность ПП, модуляцией его интенсивности для испарения части материала в заранее намеченных местах и получения требуемой маркировки.
2.11 Испытания ПП
Испытания - экспериментальное определение количественных и качественных показателей качества ПП как результат воздействия на них внешних дестабилизирующих факторов, включая технологические. ПП должны обеспечивать работоспособность при воздействии на них внешних факторов (режим работы, климатические и механические воздействия) (рис. 6). Предельные значения внешних воздействующих факторов определяют группу жесткости работы ПП. Группу жесткости, определяющую перечень воздействующих факторов и соответствующих им видов испытаний, устанавливает конструктор, в зависимости от группы ЭА, для которой разрабатывают ПП (стационарная, возимая, носимая, самолетная, бытовая и др.), объекта установки, условий эксплуатации и в соответствии с предельными значениями внешних воздействующих факторов; ее указывают в ТЗ.
Целью проведения испытаний является:
-
проверка качества материалов, покрытий, свойств, размеров и эксплуатационных характеристик ПП; -
контроль точности, устойчивости и надежности ТП изготовления; -
проверка работоспособности ПП с учетом влияния воздействующих факторов; -
проверка соответствия ПП стандартам, техническим условиям (ТУ) или частным ТУ (ЧТУ); -
гарантирование качества ПП при международном товарообмене; -
доводка ПП до необходимого уровня качества;
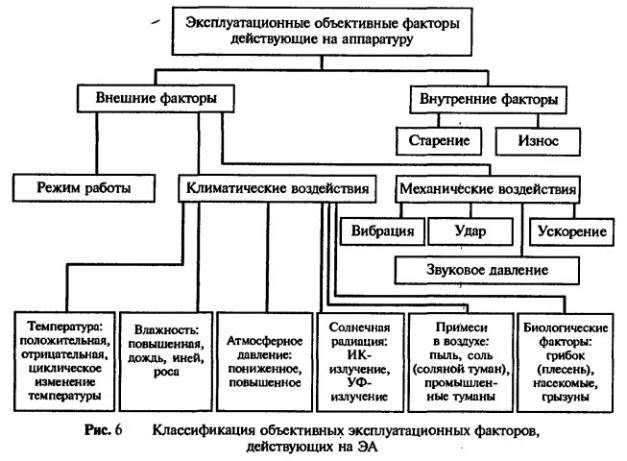
Качество ПП - совокупность свойств, которые определяют способность ПП удовлетворять заданным требованиям. Качество ПП определяют конструктивные, технологические, экономические и другие параметры. Качество ПП как свойство закладывается на этапе разработки конструкции и ТП изготовления, а оценивается в процессе эксплуатации, когда на изготовление ПП затрачены значительные средства.
Наиболее целесообразно оценивать качество ПП путем контроля и проведения испытаний на каждом этапе жизненного цикла ПП: при проектировании, постановке на производство, изготовлении, эксплуатации (при анализе рекламаций) и др. Поэтому испытания проводятся на различных этапах жизненного цикла ПП: при проектировании; при изготовлении; при выпуске ПП;
Цели и задачи проведения испытаний на этих стадиях различны: при проектировании целью испытаний является повышение качества ПП, а на этапах изготовления и выпуска - оценка их качества, поэтому проводятся различные виды испытаний при проектировании, при изготовлении опытного образца или опытной партии, а также в серийном и массовом производстве ПП.
Испытания готовых ПП (при выпуске) бывают различные:
-
квалификационные - проводятся на установочной серии ПП на стадии освоения производства с целью оценки готовности предприятия к выпуску ПП данного типа в заданном объеме; -
предъявительские - осуществляет служба технического контроля предприятия перед предъявлением ПП для приемки представителям заказчика; -
приемо-сдаточные - проводятся в освоенном производстве. Это контрольные испытания готовых ПП при приемке изготовителем или представителем заказчика вместе с изготовителем; -
периодические - осуществляются один раз в месяц или квартал с целью контроля качества ПП и возможности продолжения их выпуска. Это длительные дорогостоящие испытания с термоциклами, продолжительными вибрациями и пр. Поэтому они всегда бывают выборочными; -
инспекционные - выполняются специально уполномоченными организациями выборочно для оценки стабильности качества ПП; -
типовые - испытания выпускаемых ПП, которые проводятся с целью оценки эффективности внесения изменений в конструкцию, ТП изготовления ПП и др.; -
аттестационные - для оценки качества ПП при их аттестации по категориям качества; -
сертификационные - для установления соответствия показателей качеств ПП требованиям национальных и международных стандартов.
Испытания проводят в определенной последовательности:
-
облуживают контактную площадку в течение (4±1) с паяльником; -
впаивают облуженную проволоку в отверстие, перпендикулярно ПП в течение (4±1) с; -
охлаждают контактную площадку; -
отпаивают проволоку вторым касанием паяльника в течение (4±1) с и извлекают из отверстия; -
после охлаждения проволоку повторно впаивают в отверстие в течение (4±1) с; -
количество циклов испытаний указывается в ЧТУ; -
после последнего цикла пайки образец остывает в течение 30 мин в нормальных атмосферных условиях; -
помещают на разрывную машину, на которой прикладывается постепенно увеличивающееся усилие перпендикулярно ПП со скоростью не более 50 Н/с до полного отделения контактной площадки от основания ПП.
2.12 Контроль
В производстве ПП применяют следующие основные методы контроля:
-
электрический; -
оптический; -
рентгеновский; -
рефлектометрический.
Контроль ПП производится по целой совокупности параметров: механических, электрических и пр.
При электрическом контроле ПП проверяется:
-
на целостность проводников; -
на наличие КЗ между проводниками; -
на качество изоляции.
Для электрического тестирования применяют различные анализаторы производственных дефектов, в которых контактирование осуществляется следующими способами:
-
через односторонний или двусторонний тестовый адаптер «поле подпружиненных контактов» (рис. 7); -
при помощи гибкой пробниковой системы с подвижными пробниками (метод «летающий пробник»); -
с использованием вакуумных, кассетных, пневматических адаптеров; -
большим количеством разъемов. -
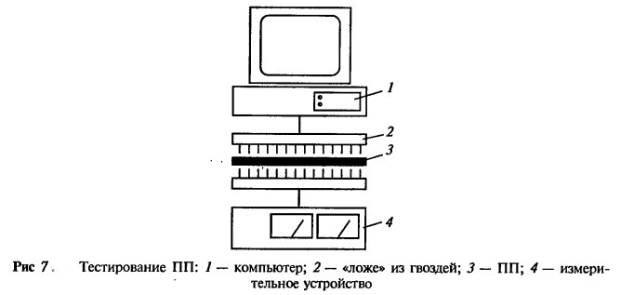
При оптическом контроле системы оптического контроля ПП работают под управлением компьютера и снабжены:
-
рабочей платформой с перемещением по X/Y; -
вращающейся на 360° смотровой призмой; -
35-миллиметровое фото- или видеооборудованием; -
цветным монитором с высоким разрешением; -
сменными объективами для изменения масштаба изображения (кратного 4, 8, 12); -
принтером; -
волоконно-оптической подсветкой контролируемой области ПП; -
специализированным ПО для оптического контроля.
Системы оптического контроля применяются для обнаружения следующих дефектов:
-
проколы, выступы, царапины, вырывы на проводниках; -
неточность размещения контактных площадок и проводников; -
изменения ширины проводников; -
неточность размеров контактных площадок; -
непараллельность и неровность краев проводников; -
подтравливание и нависание проводников; -
дефекты металлизации переходных отверстий и др.
Система оптического контроля может работать как в ручном (без компьютера), так и в автоматическом режиме путем сопряжения с совместимыми или управляющими компьютерами.
При рентгеновском контроле используют системы инспекции МПП с открытыми рентгеновскими трубками (Япония) и с закрытыми (Германия). Закрытые трубки более надежны, но существуют проблемы с разрешающей способностью и временем работы. Открытые трубки имеют лучшее разрешение, неограниченное время жизни, но требуют специальных условий для работы.
Рентгеновские системы применяют:
-
для поиска свищей слоев; -
при базировании слоев при составлении пакета МПП для определения места сверления базового отверстия следующего (расположенного ниже) слоя; -
для контроля качества просверленных отверстий; -
для контроля качества металлизации в слоях.
Большинство тестовых систем предназначено как для контроля всех основных неисправностей ПП, так и электронных модулей.
3. Заключение
В данной курсовой работе были рассмотрены материалы для печатных плат, приведены основные этапы изготовления печатных плат.
4. Список литературы
1. Галецкий Ф. Особенности производства печатных плат в России // Электронные компоненты. 2001. № 5. С. 18-26.
2. Котов Е., Махмудов М„ Жак Л. Автоматизация процессов прессования многослойных печатных плат. М.: Радио и связь, 1982. (Б-ка технолога радиоэлектронной аппаратуры).
3. Елшин Ю. М. Система проектирования печатных плат ГРИФ //