Файл: Подготовка заготовок к разметке начинается с её очистки щеткой от.docx
ВУЗ: Не указан
Категория: Не указан
Дисциплина: Не указана
Добавлен: 23.11.2023
Просмотров: 41
Скачиваний: 1
ВНИМАНИЕ! Если данный файл нарушает Ваши авторские права, то обязательно сообщите нам.
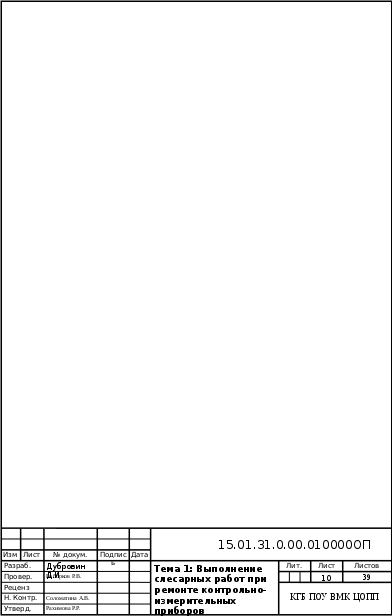
При разметке на заготовку наносят контурные линии (риски) по заданным размерам или шаблонам. Пространственная разметка более распространена в машиностроение и существенно отличается от плоскостной. Трудность пространственной разметки в том что приходится размечать не только поверхности детали расположенные в различных плоскостях и под различными углами друг к другу но и увязывать эту разметку поверхностей между собой.
Разметка – операция нанесения на обрабатываемую заготовку разметочных линий (рисок), которые определяют контуры будущей детали или места, подлежащие обработке.
Точность разметки может достигать 0,05мм. Перед разметкой необходимо изучить чертеж размечаемой детали, выяснить особенности и размеры детали, её назначения.
Разметка должна отвечать следующим основным требованиям: точно соответствовать размерам, указанным на чертеже; разметочные линии (риски) должны быть хорошо видны и не стираться в процессе обработки. Для установки подлежащей разметки деталей используют разметочные плиты, подкладки, домкраты и поворотные приспособления. Для разметки используют чертилки, кернеры, разметочные штангенциркули, и рейсмасы. В зависимости от формы размечаемых заготовок и деталей применяют плоскостную или пространственную (объемную) разметку.
База – базирующая поверхность или базовая линия, от которой ведут отсчет всех размеров при разметке. Её выбирают по следующим правилам: при наличии у заготовки хотя бы одной обработанной поверхности её выбирают в качестве базовой; при отсутствии обработанной поверхности у заготовки в качестве базовой принимают наружную поверхность.
Подготовка заготовок к разметке начинается с её очистки щеткой от
загрязнений, окалипы, следов коррозии. Затем заготовку зачищают шлифовальной бумагой и обезжиривают уайт-спиритом. Перед окрашиванием
поверхности, подлежащей разметки, необходимо убедится в отсутствии на детали раковин, трещин, заусенцев и других дефектов. Для окраски поверхности перед разметкой используют следующие составы: мел, разведенный в воде; обыкновенный сухой мел. Сухим мелом натирают размечаемые сухие необработанные поверхности мелких неответственных заготовок, так как эта окраска не прочная; раствор медного купороса, спиртовой лак применяют только при прочной разметке поверхностей небольших изделий. Выбор окрашивающего состава для нанесения на базовую поверхность зависит от вида материала заготовки и способа её получения: необработанные поверхности заготовок из черных и цветных металлов, полученных ковкой, штамповкой или прокаткой, окрашивают водным раствором мела; обработанные поверхности заготовок из черных металлов окрашивают раствором медного купороса который при взаимодействии с материалом заготовки образует на её поверхности тонкую пленку чистой меди и обеспечивает четкое выделение разметочных рисок; обработанные поверхности заготовок из цветных металлов окрашивают быстросохнущими лаками.
Разметку по шаблону применяют при изготовлении больших партий одинаковых по форме и размерам деталей, иногда для разметки малых партий сложной заготовки.
Разметку по образцу используют при ремонтных работах, когда размеры снимают непосредственно с вышедшей из строя деталей и переносят на размечаемую деталь, при этом учитывается износ детали. Образец отличается от шаблона тем, что имеет разовое применение. Разметку по месту производят, когда детали являются сопрягаемые и одна из них соединяется с другой в определенном положении. В этом случае одна их деталей выполняет роль шаблона. Разметку карандашом производят по линейке на заготовке из алюминия или дюралюминия. При разметке заготовок из этих материалов чертилки не используют, так как при нанесении рисок разрушается защитный слой и создаются условия для появлении коррозии. Брак при разметке т.е. не соответствие размеров размеченной заготовки данным чертежа, возникает из-за невнимательности разметчика или неточности разметочного инструмента, грязной поверхности плиты или заготовки.
Рубка металла. Рубка металла-это операция, при которой с поверхности заготовки удалят лишнее слои металла или заготовку разрубают на части. Рубка осуществляется с помощью режущего и ударного инструмента.
Режущим инструментом при рубке служат зубило, крейцмейсель и канавочник. Ударный инструмент- слесарный молоток. Назначение рубки: -удаление с заготовки больших неровностей, снятие твердой корки, окалины; -вырубание шпоночных пазов и смазочных канавок; - разделка кромок трещин в деталях под сварку; -срубание головок заклепок при их удалении; - вырубание отверстий в листовом материале; - рубка пруткового, полосового или листового материала. Рубка может быть чистой и черновой. В первом случае зубилом за один проход снимают слой металла толщиной 0,5 мм, а во втором случае снимают слой металла толщиной до 0,2 мм. Точность обработки, достигаемая при рубке составляет 0,4 мм.
Резка – слесарная работа, выполняемая при надрезании, или вырезании, или разрезании на части металла и различных твердых материалов. В ремонтной практике операции резки выполняются двумя способами:
-
Вручную – с помощью ножниц по металлу или ножовки. -
Машинным способом – гильотинными ножницами и на металлорежущих станках.
Преимущественным способом резки металла и других твердых режущих материалов является ручная резка ножовкой при которой необходимо соблюдать технику безопасности и обратить внимание на правильное
закрепление ножовочного полотна в станке, положение рук на рукоятке и станке ножовки, положение ножовки по отношению к разрезаемому материалу. Полотно не должно быть натянуто слишком сильно, и не должно быть натянуто слишком слабо, зубья ножовочного полотна должны быть направленны «от себя» то есть в сторону движения ножовки вперед. Правильное положение рук электрослесаря на рукоятке и станке ножовки при резке показаны на рисунке а, б. Приемы работы с ножовкой при резке металла:
-
Положение правой руки на рукоятке. -
Положение левой руки на станке.
Во время резки ножовку следует держать в горизонтальном положении; нормальная длина хода ножовки должна быть такой, чтобы в работе участвовало не менее 2/3 длины полотна.
Опиливание – наиболее распространенный вид слесарной работы, которая заключается в последовательном снятии (срезании) необходимого слоя металла с поверхности обрабатываемой заготовки или детали. Делается это для того что бы предать придать ей форму или нужный нам размер; деталь опиливают для достижения заданной шероховатости её поверхности. Опиливание заготовок и деталей производят вручную или на станках. При ремонте электрооборудования применяется преимущественно ручное опиливание плоскими, трехгранными, круглыми и полукруглыми напильниками. Плоскими напильника опиливают легко доступные плоские и выпуклые поверхности, а также широкие шпоночные канавки на концах валов электрических машин, трехгранными – внутренние углы, а также плоскости, недоступные для опиливание круглыми напильниками. Круглыми напильниками распиливают круглые и овальные отверстия, а также опиливают вогнуты поверхности заготовок и деталей.
Напильниками двойного применения являются полукруглые, плоской стороной которых можно опиливать прямолинейные поверхности, а полукруглой (выпуклой) – криволинейные (вогнутые) поверхности с различными радиусами кривизны. Ручное опиливание заготовок и деталей – самая массовая и трудоемкая слесарная работа, требующая больших затрат физических сил рабочего-электрослесаря. Основными условиями обеспечения производительного труда электрослесаря и сохранения его сил при выполнение работы ручного опиливания является правильное распределения силы нажима на напильник и обрабатываемую поверхность на начальном, рабочем и конечным путем нажатия на напильник, а также умением выбрать оптимальную для себя частоту движения напильника по обрабатываемой поверхности. При обработке заготовки или детали напильником, надо учитывать, что при нажиме на него с постоянным усилием он в начале хода (движением от себя) будет отклонятся рукояткой вниз, а в конце хода – носком вниз, в результате это приведет к бесполезной трате сил и «заваливанию» краев опиливаемой поверхности.
Правильное держание напильника и распределение усилий нажима при обработке поверхности детали опиливанием:
-
Начало конец движения рук. -
Постепенно увеличиваемое усилие, создаваемое правой рук. -
Постепенно уменьшаем усилие создаваемое левой рукой. -
Правильное распределение усилий нажима создаваемое правой рукой -
Постепенно уменьшаем усилие, создаваемое левой рукой правильное распределение усилий нажима на напильник при опиливании схематично (удлиняющимися и укорачивающимися стрелками) показано на рисунке. Оптимальной частотой движения напильника при обливании считается 40-60 двойных движений в минуту.
Правка и рихтовка имеют одно и то же назначение, но отличается приемами выполнения и применяемыми инструментами и приспособлениями. Правка – это выправление металла действием давления на ту или иную его часть независимо от того, производится ли это давление прессом или ударным молотком.
Правка и рихтовка представляют собой операции по выправке металла, заготовок и деталей. Листовой материал и заготовки из него могут быть покороблены по краям и в середине, иметь изгибы и местные неровности в виде вмятин и выпуклости различной формы. При рассмотрении деформированных заготовок можно заметить, что вогнутая сторона их короче выпуклой. Волокна на выпуклой стороне растянуты, а на вогнутой наоборот сжаты.
Под рихтовкой следует понимать выправление металла растяжением т.е удлинением той или иной его части. Рихтовка обычно выполняется ударами носком молотка или специальным рихтовальным инструментом с острыми бойками. После рихтовки на заготовке или детали остаются ясно видимые следы молотка: при правке этого не бывает. Правка представляет собой как правило, подготовительную операцию, предшествующую основным операциям обработки металлов. Правке подвергаются стальные листы и листы из цветных металлов и их сплавов, полосы прутковый материал, трубы, проволока, а также металлические сварные конструкции. Заготовки и детали из хрупких материалов (чугун, бронза и т.п) править нельзя. Различают два метода правки металлов: ручная правка выполняемая с помощью молотка на стальных или чугунных правильных плитах, наковальнях и др., и правка машинная, производимая на правильных машинах. При ручной правке слесарь отыскивает на поверхности заготовки или детали такие места, при ударе по котором заготовка выправлялась бы т.е лежала бы на плите без выпуклостей, изгибов или волнистых линий.
Металл подвергается правке как в холодном так и в нагретом состоянии. В последнем случае нужно иметь в виду, что правку стальных заготовок и деталей можно производить в интервале температур 1100-850о, а дюралюминия 470-350о. нагрев выше указанной температуры приводит к перегреву а затем к пережогу т.е к неисправному браку. Выбор способа зависит от величины прогиба, размеров и материала изделий. Гибка металла применяется для придания заготовке изогнутой форме согласно чертежу. Сущность её заключается в том, что одна часть заготовки перегибается по отношению к другой на какой-либо заданный угол.
Напряжения изгиба должны превышать предел упругости, а деформация заготовки должна быть пластической. Только в этом случае заготовка сохранит приданную ей форму после снятия нагрузки. Ручную гибку производят в тисках с помощью слесарного молотка и различных приспособлений. Последовательность выполнения гибки зависит от размеров контура и материала заготовки. Плоскогубцы и круглогубцы применяют при гибке профильного проката толщиной менее 0,5 мм и проволоки. Плоскогубцы предназначены для захвата и удержания заготовок в процессе гибки. Они имеют прорезь около шарнира. Наличие прорези позволяет производить откусывание проволоки. Круглогубцы также обеспечивают захват и удержание заготовки в процессе гибки и, кроме того, позволяют производить гибку проволоки. Гибку тонкого листового металла производят киянкой. При использовании для гибки металлов различных оправок их форма должна соответствовать форме профиля детали с учетом деформации металла. В тех случаях, когда требуется изогнуть стальную полосу на ребро, используется роликовое приспособление. Выполняя гибку заготовки, важно правильно определить ее размеры. Расчет длины заготовки выполняют по чертежу с учетом радиусов всех изгибов. Для деталей, изгибаемых под прямым углом без закруглений с внутренней стороны, припуск заготовки на изгиб должен составлять от 0,6 до 0,8 толщины металла. При изготовлении изделий иногда возникает необходимость в получении криволинейных участков труб, изогнутых под различными углами. Гибке могут подвергаться цельнотянутые и сварные трубы, а также трубы из цветных металлов и сплавов. Гибку труб производят с наполнителем (обычно сухой речной песок) или без него. Это зависит от материала трубы, ее диаметра и радиуса изгиба. Наполнитель предохраняет стенки трубы от образования в местах изгиба складок и морщин (гофров). Техника безопасности при гибке металла: Изм. Лист № докум. Подпись Дата Лист 17 15.01.31.0.00.010000ОП - молотки и кувалды должны иметь надежно заклиненные, крепкие, без сучков и трещин рукоятки; - рабочие части молотков, бородков, подкладок, оправок не должны иметь расклепа; - обрезки металла необходимо собирать и складывать в отведенный для них ящик во избежание порезов ног и рук; - листы очищать только металлической щеткой, а затем ветошью или концами; - правку металла проводить только на надежных подкладках, исключающих возможность соскальзывания металла при ударе; - подсобный рабочий должен держать металл при правке только кузнечными клещами; - при засыпке трубы песком перед гнутьем в торце одной из пробок необходимо сделать отверстие для выхода газов, иначе может произойти разрыв трубы: - при гнутье труб в горячем состоянии поддерживать их только в рукавицах во избежание ожогов рук. В производственных условиях гибка металла выполняется на гибочных и растяжных машинах различных конструкций. При пластической деформации металла в процессе гибки нужно учитывать упругость материала: после снятия нагрузки угол загиба несколько увеличивается. Изготовление деталей с очень малыми радиусами изгиба связано с опасностью разрыва наружного слоя заготовки в месте изгиба. Размер минимально допустимого радиуса изгиба зависит от механических свойств материала заготовки, от технологии гибки и качества поверхности заготовки. Детали с малыми радиусами закруглений необходимо изготовлять из пластичных материалов или предварительно подвергать отжигу. Резка - слесарная операция, выполняемая при надрезании, вырезании и разрезании на части металла и различных твердых материалов (текстолита, гетинакса и др.). В ремонтной практике операции резки выполняют: вручную - с помощью ножниц по металлу и. ножовок; машинным способом т- гильотинными ножницами и на металлорежущих станках. Преимущественным способом резки металла и других твердых материалов является ручная резка ножовкой, при которой необходимо обратить особое внимание на правильное закрепление ножовочного полотна в станке, положение рук на рукоятке и станке ножовки, положение ножовки по отношению к разрезаемому материалу. Ножовочное полотно должно быть закреплено в станке так, чтобы оно не было натянуто слишком туго или слабо, зубья ножовочного полотна должны быть направлены «от себя», т. е. в сторону движения ножовки вперед. Опиливание - наиболее распространенная слесарная операция, заключающаяся в последовательном снятии (срезании) необходимого слоя металла с поверхности обрабатываемой заготовки или детали. Цель опиливания заготовки - придать ей форму и размеры детали; деталь опиливают для достижения заданной шероховатости ее поверхности. Опиливание заготовок и деталей производят вручную или на станках. При ремонте электрооборудования применяется преимущественно ручное опиливание плоскими, трехгранными, круглыми и полукруглыми напильниками. Плоскими напильниками опиливают легко доступные плоские и выпуклые поверхности, а также широкие шпоночные канавки на концах валов электрических машин, трехгранными - внутренние углы, а также плоскости, недоступные для опиливания плоскими напильниками. Круглыми напильниками распиливают круглые и овальные отверстия, а также опиливают вогнутые поверхности заготовок и деталей. Напильниками двойного применения являются полукруглые, плоской стороной которых можно опиливать прямолинейные поверхности, а полукруглой (выпуклой) - криволинейные (вогнутые) поверхности с различными радиусами кривизны. Ручное опиливание заготовок и деталей - самая массовая и трудоемкая слесарная операция, требующая больших затрат физических сил рабочего-электрослесаря. Основными условиями обеспечения производительного труда электрослесаря и сохранения его сил при выполнении операций ручного опиливания являются правильное распределение усилий нажима напильника на обрабатываемую поверхность на начальном, рабочем и конечном пути движения напильника, а также умение выбрать оптимальную для себя частоту движения напильника по обрабатываемой поверхности. При обработке заготовки или детали напильником надо учитывать, что при нажиме на него с постоянным усилием он в начале хода (движение от себя) будет отклоняться рукояткой вниз, а в конце хода - носком вниз, в результате это приведет к бесполезной трате сил и «заваливанию» краев опиливаемой поверхности. Правильное распределение усилий нажима на. напильник при опиливании схематично (удлиняющимися и укорачивающимися стрелками) показано на. Оптимальной частотой движения напильника при обливании считается 40 -60 двойных движений в минуту. Сверление — это один из видов получения и обработки отверстий резанием с помощью специального инструмента — сверла. Как и любой другой режущий инструмент, сверло работает по принципу клина. По конструкции и назначению сверла делятся на перовые, спиральные, центровочные и др. В современном производстве применяются преимущественно спиральные сверла и реже специальные виды сверл. Режущую часть сверла (рис. 1) образуют 2 кромки, расположенные под определенным углом друг к другу (угол при вершине). Величина угла зависит от свойств обрабатываемого материала. Для стали и чугуна средней твердости он составляет 116–118°.