Файл: Подготовка заготовок к разметке начинается с её очистки щеткой от.docx
ВУЗ: Не указан
Категория: Не указан
Дисциплина: Не указана
Добавлен: 23.11.2023
Просмотров: 42
Скачиваний: 1
ВНИМАНИЕ! Если данный файл нарушает Ваши авторские права, то обязательно сообщите нам.
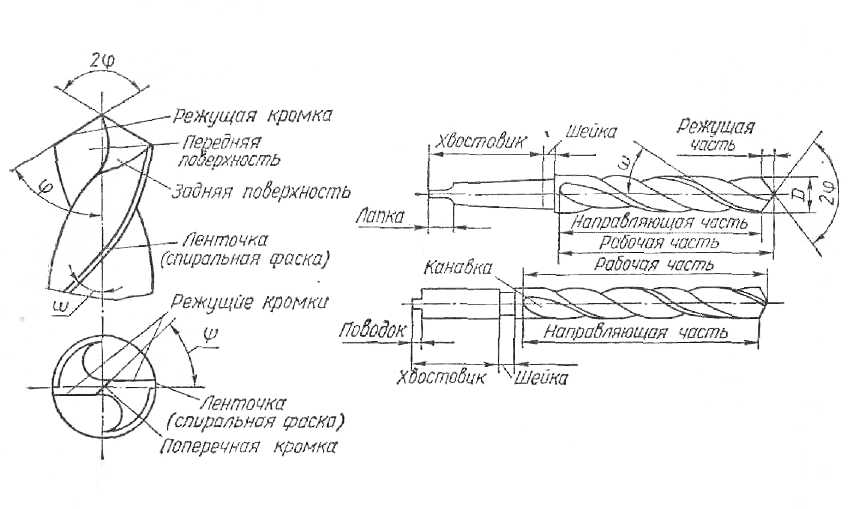
Рисунок 1 - Сверло Хвостовик служит для закрепления сверла в шпинделе станка или сверлильном патроне и может быть конической или цилиндрической формы. Конический хвостовик имеет на конце лапку, которая служит упором при выталкивании сверла из гнезда. Шейка сверла соединяет рабочую часть и хвостовик и служит для выхода абразивного круга в процессе шлифования сверла при его изготовлении. На шейке обычно проставляется марка сверла. Изготавливаются сверла преимущественно из быстрорежущей стали или твердых спеченных сплавов марок ВК6, ВК8 и Т15К6. Из таких сплавов делается только рабочая (режущая) часть инструмента. В процессе работы режущая кромка сверла притупляется, поэтому сверла периодически затачивают. Сверлами производят не только сверление глухих (засверливание) и сквозных отверстий, т.е. получение этих отверстий в сплошном материале, но и рассверливание — увеличение размера (диаметра) уже полученных отверстий. Перовые сверла являются наиболее простыми по конструкции. Они применяются при обработке твердых поковок, а также ступенчатых и фасонных отверстий. Особую группу сверл составляют центровочные сверла, предназначенные для обработки центровых отверстий. Они бывают простые, комбинированные, комбинированные с предохранительным конусом. Простые спиральные сверла отличаются от обычных спиральных сверл только меньшей длиной их рабочей части, так как ими производится сверление отверстий небольшой длины. Они применяются при обработке высокопрочных материалов, в то время как комбинированные сверла часто ломаются. Зенкованием называется обработка верхней части отверстий в целях получения фасок и цилиндрических углублений, например, под потайную головку винта или заклепки. Выполняется зенкование с помощью зенковок или сверлом большего диаметра; Зенкерование — это обработка отверстий, полученных; литьем, штамповкой или сверлением, для придания им цилиндрической формы, повышения точности и качества поверхности. Зенкерование выполняется специальными инструментами— зенкерами. Зенкеры могут быть с режущими кромками на цилиндрической или конической поверхности (цилиндрические и конические зенкеры), а также с режущими кромками, расположенными на торце (торцовые зенкеры). Для обеспечения целостности обрабатываемого отверстия и зенкера на торце зенкера иногда делают гладкую цилиндрическую направляющую часть. Зенкерование может быть процессом окончательной обработки или подготовительным к развертыванию. В последнем случае при зенкеровании оставляют припуск на дальнейшую обработку. Нарезание наружной резьбы вручную осуществляется с помощью плашек - круглых (цельных или разрезных) либо призматических. Круглые плашки при нарезании резьбы закрепляют в специальном приспособлении - плашкодержателе, призматические - в клуппе. При нарезании наружной резьбы, как и внутренней, важно определить диаметр стержня под резьбу, так как в этом случае происходит некоторое выдавливание металла и увеличение наружного диаметра образовавшейся резьбы по сравнению с диаметром стержня. Последовательность операций при нарезании наружной резьбы плашкой: вертикально закрепляют стержень в тисках, напильником снимают на его конце фаску; устанавливают на конец стержня плашку с плашкодержателем таким образом, чтобы маркировка на плашке была внизу, а плоскость плашки была перпендикулярна оси стержня; правой рукой слегка нажимают на плашкодержатель, а левой поворачивают его до надёжного врезания плашки в металл; смазав стержень и плашку соответствующей смазочно-охлаждающей жидкостью, медленным попеременным вращением (как и при нарезании внутренней резьбы) продолжают нарезание резьбы до тех пор, пока не «прогонят»
плашку по требуемой длине стержня; плашку свёртывают со стержня; очищают плашку и стержень от смазочно-охлаждающей жидкости и стружки; нарезанную резьбу проверяют эталонной гайкой. Внутреннюю резьбу в отверстиях нарезают специальным режущим инструментом – метчиком (рис. 1). Для нарезания резьбы вручную применяют комплекты ручных метчиков, состоящие обычно из трёх или двух метчиков. В комплект из трёх метчиков входят черновой, получистовой (средний) и чистовой метчики. Первым и вторым метчиками нарезают резьбу предварительно, а третьим придают ей окончательный размер и форму. При нарезании внутренней и наружной резьбы важно правильно выбрать диаметр сверла для получения отверстия под внутреннюю резьбу и диаметр стержня под наружную. Диаметр сверла (или стержня) должен быть несколько меньше наружного диаметра резьбы, так как материал при нарезании резьбы будет частично выдавливаться по направлению к оси отверстия (от оси стержня). Диаметр отверстия (сверла) под внутреннюю резьбу можно определить и без таблицы: приближённо он равен диаметру резьбы за вычетом её шага. Чтобы узнать шаг резьбы, с помощью штангенциркуля или измерительной линейки определяют высоту 10 ниток метчика и полученный результат делят на 10. Нарезание внутренней резьбы выполняют в следующей последовательности. Деталь с предварительно просверленным в ней отверстием закрепляют в тисках таким образом, чтобы ось отверстия была строго вертикальна. В резьбовое отверстие вставляют заборную часть чернового метчика. Проверяют установку метчика по угольнику. Чтобы резьба получилась чистой (а не рваной, грязной), режущую часть метчика и поверхность отверстия смазывают смазочно-охлаждающей жидкостью (например, для стали обычно используют машинное масло, для твёрдого чугуна - керосин). На хвостовую часть метчика надевают подходящий вороток. Прижимая левой рукой вороток к метчику, правой проворачивают его до врезания на несколько витков в металл. Взяв вороток двумя руками, начинают медленно и попеременно его вращать (1...1,5 оборота по часовой стрелке, 0,5 оборота - против).
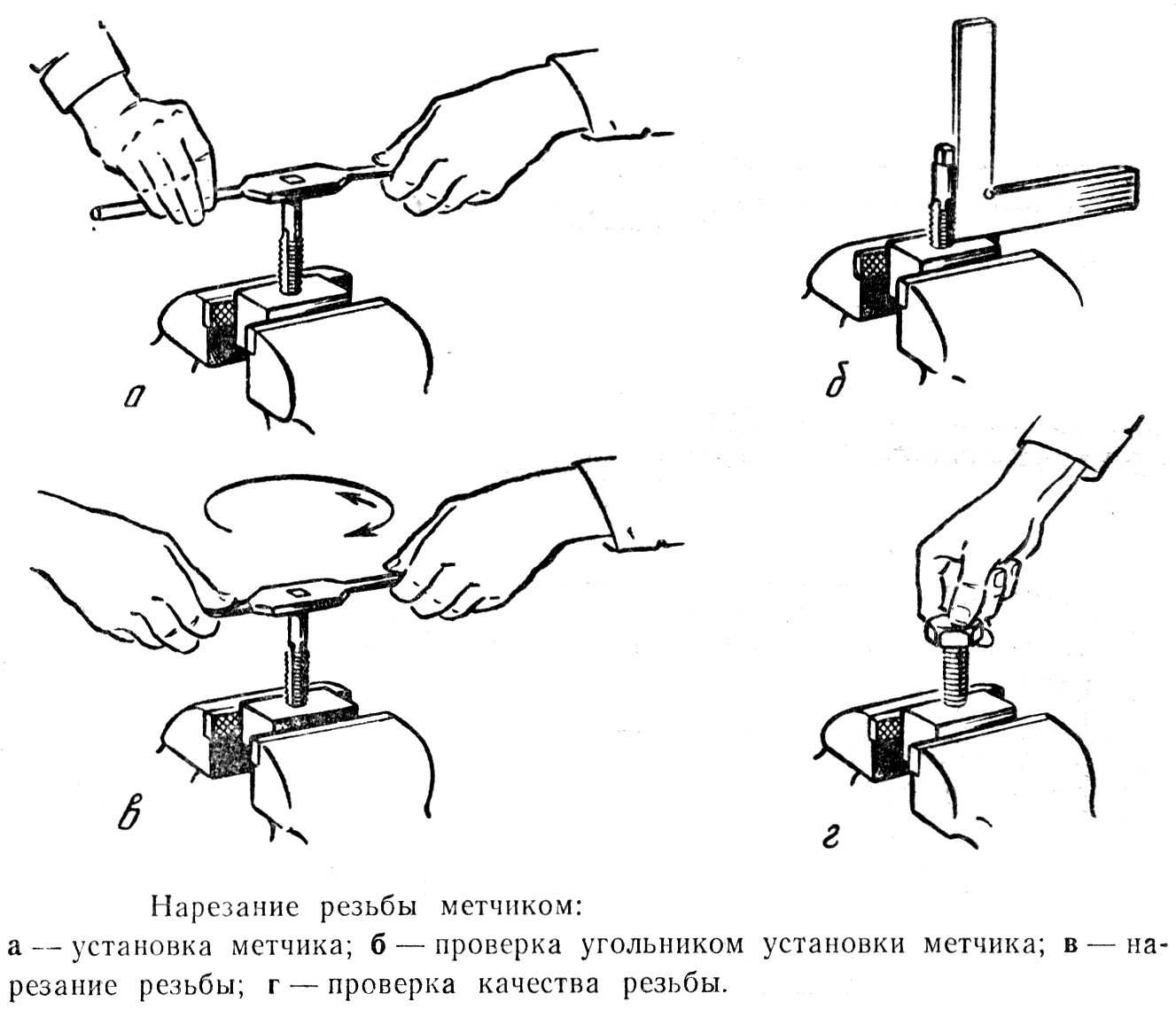
Рисунок 2 – Нарезание резьбы метчиком Закончив нарезание черновым метчиком, его вывёртывают из отверстия, на его место ставят средний, а затем чистовой метчик и повторяют те же операции до полного нарезания резьбы. В процессе резания, как и при установке метчика, угольником регулярно контролируют положение оси метчика по отношению к поверхности детали. Деталь с нарезанной резьбой освобождают от смазочно-охлаждающей жидкости и стружки, тщательно протирают и затем проверяют резьбу на качество; для этого в отверстие ввёртывают эталонный винт или резьбовой калибр - пробку. Шабрение — это снятие очень тонкой поверхности слоя металла для обеспечения гладкости сопрягаемых поверхностей режущим инструментом — шабером. С помощью шабрения устраняют неточности обработанных ранее поверхностей, а также незначительные повреждения (царапины и пр.). Шабрение осуществляют в несколько проходов. При черновом проходе (ширина прохода 20-30 мм и длина 10-15 мм) от-шаброванная поверхность при нанесении на нее краски должна покрыться до четырех пятен на площади 25x25 мм. Шаберы затачивают на образцовых дисковых станках, а затем заправляют и доводят на образцовых брусках или оселках вручную. Шаберы обычно заправляют в течение смены несколько раз. В процессе заправки брусок смазывают тонким слоем машинного масла. Шабрение — трудоемкая операция. Для повышения производительности труда применяются различные механизированные шаберы. При шабрении особое внимание следует уделять остроте заточки шаберов и умеренному нажиму на шабер во время работы, а также внимательной проверке качества шабрения «на краску». Притиркой называется окончательная обработка поверхностей при помощи абразивных паст и порошков с целью плотного соединения сопрягаемых деталей. Перед притиркой поверхности должны быть тщательно обработаны с припуском не более 0,01-0,02 мм, иначе притирка затягивается надолго. Притирку производят, сжимая притираемые поверхности специальными притирами из чугуна, меди, текстолита, а также дерева твердых пород. В качестве притирочных вспомогательных материалов применяют абразивные пасты, состоящие из абразивного порошка и смазывающей жидкости (масла). Для притирки стальных поверхностей используют кордун, карбид бора, а для чугунных и бронзовых — мелко-тертое стекло. Широкое применение получили пасты ГОИ, которые имеют три класса крупности наполнителей. Для грубой притирки используют пасту ГОИ темно-зеленого (почти черного) цвета, для средней притирки —
пасту темно-зеленого цвета, а для тонкой — светло-зеленого цвета. Для механизации притирки поверхностей деталей используют различные устройства и приспособления. Для ускорения и облегчения операции шабрения применяют станки для шабрения и механизированные шаберы, приводимые в движение от электродвигателя посредством гибкого вала. Притиркой называется операция тонкой (точной) обработки поверхностей твердыми шлифующими порошками. В результате притирки достигают герметичности соединения или увеличения поверхности контакта деталей. Материалами для изготовления порошков служат алмаз, корунд, стекло, наждак и др. Притирка производится с помощью притиров или без них. Притиры изготовляют из мягкой стали, серого чугуна, меди, латуни, свинца и твердых пород дерева, причем материал притира должен быть мягче обрабатываемого материала. Форма притиров зависит от величины и формы обрабатываемой заготовки; притиры могут иметь вид плиты, диска, стержня, кольца и др. При работе с помощью притира последний посыпают тонким слоем порошка, и этот порошок вдавливают в поверхность притира закаленным роликом; в цилиндрические притиры порошок вдавливают, катая их по закаленной плите. Притирка может производиться при неподвижном притире (заготовка перемещается) и при подвижном притире (заготовка неподвижна). Поверхность притира и обрабатываемую поверхность вводят в контакт (накладывают одну на другую), и при относительном их перемещении шлифующий порошок, вдавленный в поверхность притира, снимает с поверхности заготовки весьма тонкий (0,001—0,002 мм) слой. Для улучшения качества и увеличения производительности притирки применяют различные смазки: машинное масло, керосин, бензин и др. Притирка без применения притиров используется для точной припасовки двух трущиеся поверхностей: например, пробки крана и гнезда, подшипника и вала и др. Притирка ведется так: пробку (вал) смазывают маслом, посыпают порошком, вставляют в гнездо и вращают то в одну, то в другую сторону с легким нажимом. В результате снимаются неровности с поверхностей, и пробка притирается к гнезду. Для механизации используют дрели и притирочные станки.