Файл: Предоставить краткую геологичесую характеристику Мамонтовского месторождения.docx
ВУЗ: Не указан
Категория: Не указан
Дисциплина: Не указана
Добавлен: 30.11.2023
Просмотров: 172
Скачиваний: 5
ВНИМАНИЕ! Если данный файл нарушает Ваши авторские права, то обязательно сообщите нам.
Именно анодные добавки, если с ними переборщить, могут не уменьшить, а ускорить коррозионное разрушение материала. Популярны карбонаты, силикаты, фосфаты, нитрит натрия, как ингибиторы анодной коррозии.
-
Смешанные – добавки, которые замедляют реакции и катодные, а анодные. Смешанные добавки – это хроматы. Хроматы значительно тормозят анодную и катодную реакцию вместе, поэтому они являются наиболее эффективными. Процесс такой реакции протекает по окислительному типу.
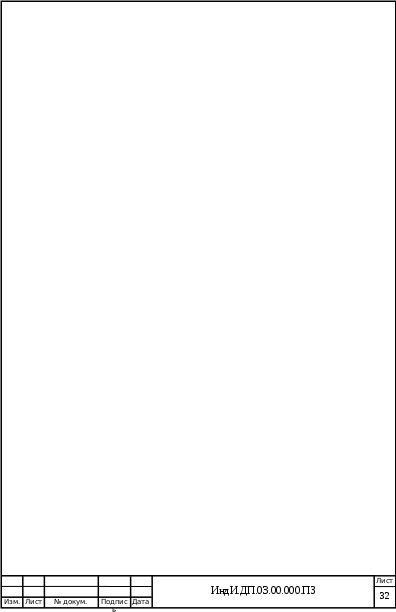
-
Органические – это органические вещества, которые являются более универсальными, так как уменьшают скорость катодных и анодных реакций. К ним можно отнести азот, серу, кислород, ароматические соединения. Главным преимуществом и отличием от неорганических ингибиторов выступает тот факт, что органические вещества адсорбируются только на поверхности материала, не вступая в реакцию с ржавчиной. -
Неорганические ингибиторы коррозии, что это такое? Они содержат неорганические вещества в составе ингибитора. Особенность работы с неорганическими частицами в ингибиторе заключается в том, что при неверно подобранной концентрации, они могут не защитить металл, образовав на нем тончайшую пленку, а наоборот вступить в реакцию с продуктами коррозии и ускорить процесс разрушения. Относятся хроматы, бихроматы натрия и калия, бикарбонат кальция и т.д.
Классификация ингибиторов по механизму действия:
-
Работающие в кислотной среде — амины, ацетиленовые спирты, серосодержащие соединения, альдегиды. Данный тип веществ применяется в газо- и нефтедобывающей промышленности, ими покрываются трубопроводы, по которым идет газ или нефтепродукты, а также изделия, участвующие в этих процессах. Ингибитор коррозии кислотной среды активно борется с катодным и смешанным разрушением. -
Ингибиторы для нейтральных сред – фосфаты, нитриты, аминокислоты, хроматы, алкилфосфаты, сульфонаты. Наибольшее применение нашли в сфере водоснабжения, охлаждения, применяются на морских судах. Здесь также как везде, раствор ингибитора используется в качестве защитного покрытия любых изделий перечисленных отраслей, емкости, несущие конструкции, отдельные элементы. -
Протекающие в щелочной среде. Вещества участвуют в составах специальных моющих средств. Действие их основано на том, что они уменьшают силу тока в его химических источниках. Ингибиторы для таких целей чаще всего используют совместно с катионами.
Свойства ингибиторов коррозии:
Все свойства ингибиторов сводятся к антикоррозийной защите металлических изделий. Механизм работы прост: ингибитор в составе раствора наносится на поверхность элемента и защищает его от внешнего
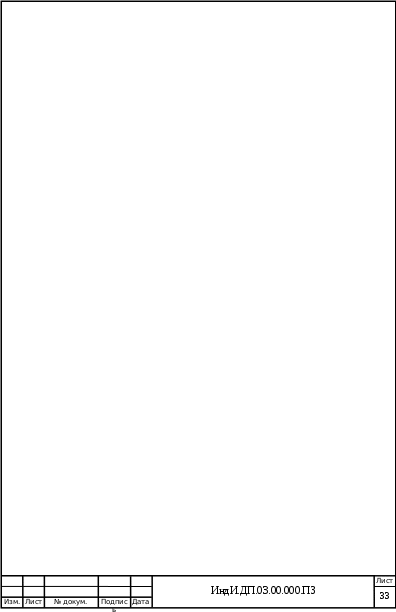
2.4 СОВРЕМЕННЫЕ МЕТОДЫ БОРЬБЫ С КОРРОЗИЕЙ НАЗЕМНОГО И ПОДЗЕМНОГО ОБОРУДОВАНИЯ
Антикоррозионная защита требуется любым инструментальным и конструкционным изделиям, изготовленным из металла, так как в той или иной мере все они испытывают на себе негативное коррозионное влияние среды, окружающей нас.
Подземная коррозия может вызываться жизнедеятельностью микроорганизмов. В настоящее время биокоррозии уделяют большое внимание. Некоторые зарубежные авторы считают, что на долю биокоррозии приходится значительное число всех коррозионных разрушений. Эти данные недостаточно обоснованы, однако активное участие микроорганизмов в подземной коррозии не вызывает сомнений.
Наряду с дальнейшим усиленным развитием практических мероприятий по борьбе с подземной коррозией необходимо более детальное изучение механизма подземной коррозии и построение общей теории подземной коррозии металлов. Такая теория, помимо объяснения и предвидения практических случаев коррозии, позволила бы также повысить эффективность известных методов борьбы с коррозией металлов для почвенных условий и указать новые более совершенные пути борьбы с подземной коррозией
конструкций.
Все современные методы борьбы с коррозией можно разделить на несколько групп:
-
применение электрохимических способов защиты изделий; -
использование защитных покрытий; -
проектирование и выпуск инновационных, высокоустойчивых к процессам ржавления конструкционных материалов; -
введение в коррозионную среду соединений, способных уменьшить
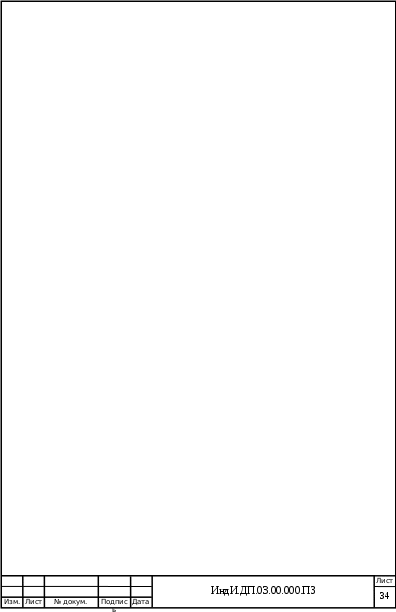
-
рациональное строительство и эксплуатация деталей и сооружений из металлов.
Защита от коррозии посредством специальных покрытий.
Чтобы защитное покрытие справлялось с задачами, которые возлагаются на него, оно должно обладать целым рядом особых качеств:
-
быть износостойким и максимально твердым; -
характеризоваться высоким показателем прочности сцепления с поверхностью обрабатываемого изделия (то есть обладать повышенной адгезией); -
иметь такую величину теплового расширения, которая бы незначительно отличалась от расширения защищаемой конструкции; -
быть максимально недоступным для вредных факторов окружающей среды.
Также покрытие должно наноситься на всю конструкцию как можно более равномерно и сплошным слоем.
Все используемые в наши дни защитные покрытия делят на:
-
металлические и неметаллические; -
органические и неорганические.
Такие покрытия, которые мы опишем далее, применяются (и весьма активно) по всему миру. Поэтому о них будет рассказано достаточно подробно.
Борьба с коррозией при помощи органических неметаллических покрытий
Самым распространенным и сравнительно несложным вариантом защиты металлов от ржавления, известным уже очень давно, признается использование лакокрасочных составов. Антикоррозионная обработка материалов такими соединениями характеризуется не только простотой и дешевизной, но еще и следующими положительными свойствами:
-
возможностью нанесения покрытий разных цветовых оттенков - что и элегантный облик конструкциям придает, и надежно защищает их от ржавчины; -
элементарностью восстановления защитного слоя в случае его повреждения.
К сожалению, лакокрасочные составы имеют совсем небольшой
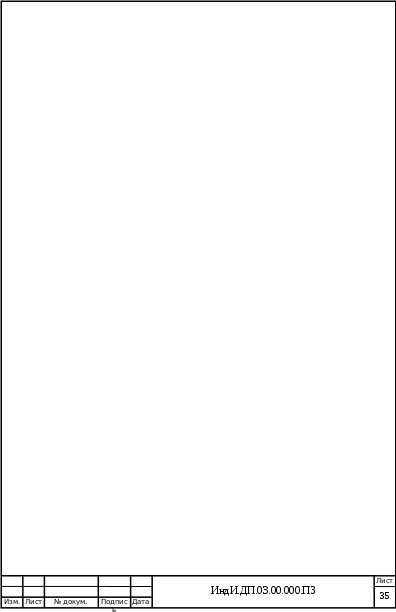
К составляющим современных лакокрасочных составов относят такие элементы:
-
краски: суспензии пигментов с минеральной структурой; -
лаки: растворы (коллоидные) смол и масел в растворителях органического происхождения (защита от коррозии при их применении достигается после полимеризации смолы либо масла или их испарения под влиянием дополнительного катализатора, а также при нагреве); -
искусственные и природные соединения, называемые пленкообразователями (например, олифа – самый, пожалуй, популярный неметаллический "защитник" чугуна и стали); -
эмали: лаковые растворы с комплексом подобранных пигментов в измельченном виде; -
смягчители и разнообразные пластификаторы: адипиновая кислота в виде эфиров, дибутилфтолат, касторовое масло, трикрезилфосфат, каучук, другие элементы, которые увеличивают эластичность защитного слоя; -
этилацетат, толуол, бензин, спирт, ксилол, ацетон и другие (данные компоненты нужны для того, чтобы лакокрасочные составы без проблем наносились на обрабатываемую поверхность); -
инертные наполнители: мельчайшие частицы асбеста, тальк, мел, каолин (они делают антикоррозионные возможности пленок более высокими, а также уменьшают траты других составляющих лакокрасочных покрытий); -
пигменты и краски; -
катализаторы (на языке профессионалов – сиккативы): необходимые для быстрого высыхания защитных составов кобальтовые и магниевые соли жирных органических кислот.
Лакокрасочные соединения выбирают с учетом того, в каких условиях эксплуатируется обрабатываемое изделие. Составы на базе эпоксидных элементов рекомендованы для использования в атмосферах, где постоянно присутствуют испарения хлороформа, двухвалентного хлора, а также для
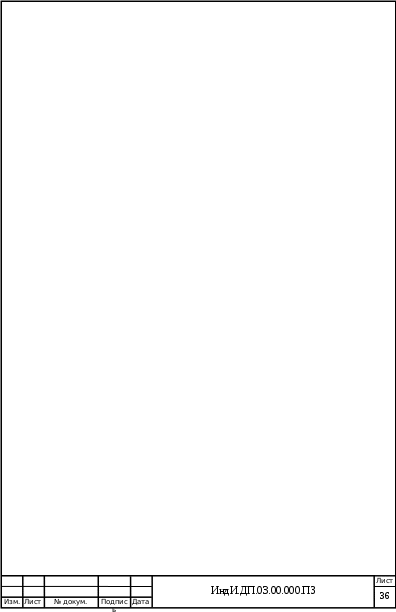
К кислотам также устойчивы и лакокрасочные составы с полихровинилом. Они, кроме того, применяются для предохранения металла от воздействия масел и щелочей. А вот для защиты конструкций от газов чаще применяются составы на базе полимеров (эпоксидных, фторорганических и иных).
2.5 МЕРОПРИЯТИЯ ПО БОРЬБЕ С КОРРОЗИЕЙ НЕФТЕПРОМЫСЛОВОГО ОБОРУДОВАНИЯ
Основные методы борьбы с коррозией нефтепромыслового оборудования, которые сегодня применяют отечественные и зарубежные компании, можно разделить на три группы: химические, физические и технологические.
-
Химические методы основаны на использовании химреагентов, в основном ингибиторов коррозии. Физические методы подразумевают применение коррозионностойких материалов, защитных покрытий и протекторной защиты.
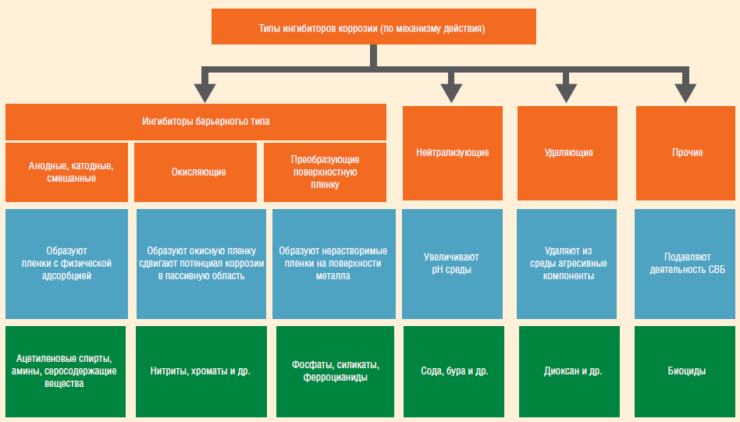
Рисунок 2 – Типы ингибиторов коррозии.
Действие ингибиторов барьерного типа основано на образовании пленок. Анодные, катодные и смешанные ингибиторы барьерного типа
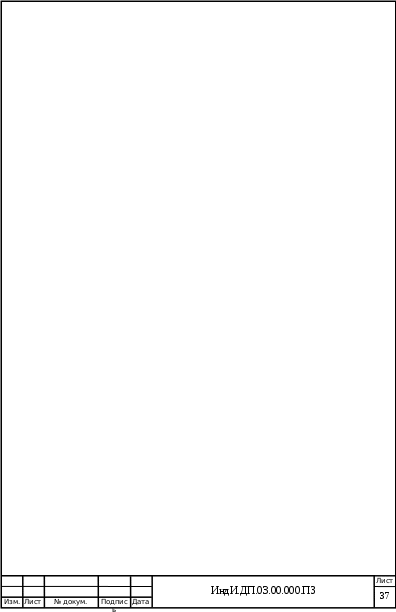
Выделяют два объекта подачи ингибитора — скважина и пласт. Подача ингибитора в скважину возможна несколькими способами: дозирование с помощью устьевых дозаторов в затрубное пространство, дозирование с помощью устьевых дозаторов в заданную точку по капиллярной трубке, периодическая закачка в заданное пространство с помощью агрегатов и др. (см. «Объекты и способы подачи ингибиторов коррозии»).