Файл: Конспект лекций по учебной дисциплине Материаловедение.doc
ВУЗ: Не указан
Категория: Не указан
Дисциплина: Не указана
Добавлен: 01.12.2023
Просмотров: 745
Скачиваний: 3
ВНИМАНИЕ! Если данный файл нарушает Ваши авторские права, то обязательно сообщите нам.
.
Диффузионную металлизацию можно проводить в твердых, жидких и газообразных средах.
При твердой диффузионной метализации металлизатором является ферросплав с добавлением хлористого аммония (NH4Cl). В результате реакции металлизатора с HCl или CL2 образуется соединение хлора с металлом (AlCl3, CrCl2, SiCl4), которые при контакте с поверхностью диссоциируют с образованием свободных атомов.
Жидкая диффузионная металлизация проводится погружением детали в расплавленный металл (например, алюминий).
Газовая диффузионная металлизация проводится в газовых средах, являющихся хлоридами различных металлов.
Диффузия металлов протекает очень медленно, так как образуются растворы замещения, поэтому при одинаковых температурах диффузионные слои в десятки и сотни раз тоньше, чем при цементации.
Диффузионная металлизация – процесс дорогостоящий, осуществляется при высоких температурах (1000…1200oС) в течение длительного времени.
Одним из основных свойств металлизированных поверхностей является жаростойкость, поэтому жаростойкие детали для рабочих температур 1000…1200oС изготавливают из простых углеродистых сталей с последующим алитированием, хромированием или силицированием.
Исключительно высокой твердостью (2000 HV) и высоким сопротивлением износу из-за образования боридов железа (FeB, FeB2) характеризуются борированные слои, но эти слои очень хрупкие.
Контрольные вопросы.
1.Почему при высокотемпературном цианировании сталь в большей степени насыщается углеродом, а при низкотемпературном - азотом?
2.Преимущества цианирования по сравнению с цементацией и азотированием.
3. Какие стали можно цементировать?
4. Почему при азотировании поверхность стали получает очень высокую твёрдость и износоустойчивость?
5.Преимущества азотирования по сравнению с цементацией. Недостатки его.
6.Что произойдёт, если при цементации детали будут касаться друг друга?
7.Выше какой критической точки ведётся нагрев стали при цементации?
8. Чем объясняется высокая твёрдость цементированного слоя?
9. В результате каких способов диффузной металлизации снижается трение?
10. В результате какой обработки можно повысить долговечность измерительных инструментов?
Методы повышения конструктивной прочности металла.
Термомеханическая обработка стали
Одним из технологических процессов упрочняющей обработки является термомеханическая обработка (ТМО).
Термомеханическая обработка относится к комбинированным способам изменения строения и свойств материалов.
При термомеханической обработке совмещаются пластическая деформация и термическая обработка (закалка предварительно деформированной стали в аустенитном состоянии).
Преимуществом термомеханической обработки является то, что при существенном увеличении прочности характеристики пластичности снижаются незначительно, а ударная вязкость выше в 1,5…2 раза по сравнению с ударной вязкостью для той же стали после закалки с низким отпуском.
В зависимости от температуры, при которой проводят деформацию, различают высокотемпературную термомеханическую обработку (ВТМО) и низкотемпературную термомеханическую обработку (НТМО).
Сущность высокотемпературной термомеханической обработки заключается в нагреве стали до температуры аустенитного состояния (выше А3). При этой температуре осуществляют деформацию стали, что ведет к наклепу аустенита. Сталь с таким состоянием аустенита подвергают закалке (рис. 16.1 а).
Высокотемпературная термомеханическая обработка практически устраняет развитие отпускной хрупкости в опасном интервале температур, ослабляет необратимую отпускную хрупкость и резко повышает ударную вязкость при комнатной температуре. Понижается температурный порог хладоломкости. Высокотемпературная термомеханическая обработка повышает сопротивление хрупкому разрушению, уменьшает чувствительность к трещинообразованию при термической обработке.
Рис. 16.1. Схема режимов термомеханической обработки стали: а – высокотемпературная термомеханическая обработка (ВТМО); б – низкотемпературная термомеханическая обработка (НТМО).
Высокотемпературную термомеханическую обработку эффективно использовать для углеродистых, легированных, конструкционных, пружинных и инструментальных сталей.
Последующий отпуск при температуре 100…200oС проводится для сохранения высоких значений прочности.
Низкотемпературная термомеханическая обработка (аусформинг).
Сталь нагревают до аустенитного состояния. Затем выдерживают при высокой температуре, производят охлаждение до температуры, выше температуры начала мартенситного превращения (400…600oС), но ниже температуры рекристаллизации, и при этой температуре осуществляют обработку давлением и закалку (рис. 16.1 б).
Низкотемпературная термомеханическая обработка, хотя и дает более высокое упрочнение, но не снижает склонности стали к отпускной хрупкости. Кроме того, она требует высоких степеней деформации (75…95 %), поэтому требуется мощное оборудование.
Низкотемпературную термомеханическую обработку применяют к среднеуглеродистым легированным сталям, закаливаемым на мартенсит, которые имеют вторичную стабильность аустенита.
Повышение прочности при термомеханической обработке объясняют тем, что в результате деформации аустенита происходит дробление его зерен (блоков). Размеры блоков уменьшаются в два – четыре раза по сравнению с обычной закалкой. Также увеличивается плотность дислокаций. При последующей закалке такого аустенита образуются более мелкие пластинки мартенсита, снижаются напряжения.
Механические свойства после разных видов ТМО для машиностроительных сталей в среднем имеют следующие характеристики (см. табл. 16.1):
Таблица 16.1. Механические свойства сталей после ТМО
Термомеханическую обработку применяют и для других сплавов.
Поверхностное упрочнение стальных деталей
Конструкционная прочность часто зависит от состояния материала в поверхностных слоях детали. Одним из способов поверхностного упрочнения стальных деталей является поверхностная закалка.
В результате поверхностной закалки увеличивается твердость поверхностных слоев изделия с одновременным повышением сопротивления истиранию и предела выносливости.
Общим для всех видов поверхностной закалки является нагрев поверхностного слоя детали до температуры закалки с последующим быстрым охлаждением. Эти способы различаются методами нагрева деталей. Толщина закаленного слоя при поверхностной закалке определяется глубиной нагрева.
Наибольшее распространение имеют электротермическая закалка с нагревом изделий токами высокой частоты (ТВЧ) и газопламенная закалка с нагревом газово-кислородным или кислородно-керосиновым пламенем.
Закалка токами высокой частоты.
Метод разработан советским ученым Вологдиным В.П.
Основан на том, что если в переменное магнитное поле, создаваемое проводником-индуктором, поместить металлическую деталь, то в ней будут индуцироваться вихревые токи, вызывающие нагрев металла. Чем больше частота тока, тем тоньше получается закаленный слой.
Обычно используются машинные генераторы с частотой 50…15000 Гц и ламповые генераторы с частотой больше 106 Гц. Глубина закаленного слоя – до 2 мм.
Индукторы изготавливаются из медных трубок, внутри которых циркулирует вода, благодаря чему они не нагреваются. Форма индуктора соответствует внешней форме изделия, при этом необходимо постоянство зазора между индуктором и поверхностью изделия.
Схема технологического процесса закалки ТВЧ представлена на рис. 16.2.
Рис. 16.2. Схема технологического процесса закалки ТВЧ
После нагрева в течение 3…5 с индуктора 2 деталь 1 быстро перемещается в специальное охлаждающее устройство – спрейер 3, через отверстия которого на нагретую поверхность разбрызгивается закалочная жидкость.
Высокая скорость нагрева смещает фазовые превращения в область более высоких температур. Температура закалки при нагреве токами высокой частоты должна быть выше, чем при обычном нагреве.
При правильных режимах нагрева после охлаждения получается структура мелкоигольчатого мартенсита. Твердость повышается на 2…4 HRC по сравнению с обычной закалкой, возрастает износостойкость и предел выносливости.
Перед закалкой ТВЧ изделие подвергают нормализации, а после закалки низкому отпуску при температуре 150…200oС (самоотпуск).
Наиболее целесообразно использовать этот метод для изделий из сталей с содержанием углерода более 0,4 %.
Преимущества метода:
Диффузионную металлизацию можно проводить в твердых, жидких и газообразных средах.
При твердой диффузионной метализации металлизатором является ферросплав с добавлением хлористого аммония (NH4Cl). В результате реакции металлизатора с HCl или CL2 образуется соединение хлора с металлом (AlCl3, CrCl2, SiCl4), которые при контакте с поверхностью диссоциируют с образованием свободных атомов.
Жидкая диффузионная металлизация проводится погружением детали в расплавленный металл (например, алюминий).
Газовая диффузионная металлизация проводится в газовых средах, являющихся хлоридами различных металлов.
Диффузия металлов протекает очень медленно, так как образуются растворы замещения, поэтому при одинаковых температурах диффузионные слои в десятки и сотни раз тоньше, чем при цементации.
Диффузионная металлизация – процесс дорогостоящий, осуществляется при высоких температурах (1000…1200oС) в течение длительного времени.
Одним из основных свойств металлизированных поверхностей является жаростойкость, поэтому жаростойкие детали для рабочих температур 1000…1200oС изготавливают из простых углеродистых сталей с последующим алитированием, хромированием или силицированием.
Исключительно высокой твердостью (2000 HV) и высоким сопротивлением износу из-за образования боридов железа (FeB, FeB2) характеризуются борированные слои, но эти слои очень хрупкие.
-
- 1 ... 8 9 10 11 12 13 14 15 ... 29
Контрольные вопросы.
1.Почему при высокотемпературном цианировании сталь в большей степени насыщается углеродом, а при низкотемпературном - азотом?
2.Преимущества цианирования по сравнению с цементацией и азотированием.
3. Какие стали можно цементировать?
4. Почему при азотировании поверхность стали получает очень высокую твёрдость и износоустойчивость?
5.Преимущества азотирования по сравнению с цементацией. Недостатки его.
6.Что произойдёт, если при цементации детали будут касаться друг друга?
7.Выше какой критической точки ведётся нагрев стали при цементации?
8. Чем объясняется высокая твёрдость цементированного слоя?
9. В результате каких способов диффузной металлизации снижается трение?
10. В результате какой обработки можно повысить долговечность измерительных инструментов?
-
1.Используя диаграмму Fe-Fe3C и зная, что цементация проводилась при температуре 930 0С, нарисуйте схему изменения структуры от поверхности к середине после охлаждения детали, если исходное содержание углерода в стали было 0,2 %, содержание углерода в поверхностном слое 1,0 %. -
2. Ответственное изделие было изготовлено из крупнозернистой углеродистой стали с 0,15 % С. Подумайте, какой режим термообработки обеспечит оптимальные свойства изделия, если цементация проводилась при 950 0С и содержание углерода в поверхностном слое 0,9 %. -
-
-
-
Лекция 11 -
Методы повышения конструктивной прочности металла.
-
Термомеханическая обработка стали -
Поверхностное упрочнение стальных деталей -
Закалка токами высокой частоты. -
Газопламенная закалка. -
Старение -
Обработка стали холодом -
Упрочнение методом пластической деформации
Термомеханическая обработка стали
Одним из технологических процессов упрочняющей обработки является термомеханическая обработка (ТМО).
Термомеханическая обработка относится к комбинированным способам изменения строения и свойств материалов.
При термомеханической обработке совмещаются пластическая деформация и термическая обработка (закалка предварительно деформированной стали в аустенитном состоянии).
Преимуществом термомеханической обработки является то, что при существенном увеличении прочности характеристики пластичности снижаются незначительно, а ударная вязкость выше в 1,5…2 раза по сравнению с ударной вязкостью для той же стали после закалки с низким отпуском.
В зависимости от температуры, при которой проводят деформацию, различают высокотемпературную термомеханическую обработку (ВТМО) и низкотемпературную термомеханическую обработку (НТМО).
Сущность высокотемпературной термомеханической обработки заключается в нагреве стали до температуры аустенитного состояния (выше А3). При этой температуре осуществляют деформацию стали, что ведет к наклепу аустенита. Сталь с таким состоянием аустенита подвергают закалке (рис. 16.1 а).
Высокотемпературная термомеханическая обработка практически устраняет развитие отпускной хрупкости в опасном интервале температур, ослабляет необратимую отпускную хрупкость и резко повышает ударную вязкость при комнатной температуре. Понижается температурный порог хладоломкости. Высокотемпературная термомеханическая обработка повышает сопротивление хрупкому разрушению, уменьшает чувствительность к трещинообразованию при термической обработке.
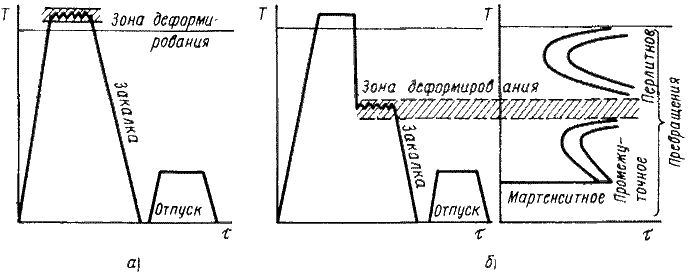
Рис. 16.1. Схема режимов термомеханической обработки стали: а – высокотемпературная термомеханическая обработка (ВТМО); б – низкотемпературная термомеханическая обработка (НТМО).
Высокотемпературную термомеханическую обработку эффективно использовать для углеродистых, легированных, конструкционных, пружинных и инструментальных сталей.
Последующий отпуск при температуре 100…200oС проводится для сохранения высоких значений прочности.
Низкотемпературная термомеханическая обработка (аусформинг).
Сталь нагревают до аустенитного состояния. Затем выдерживают при высокой температуре, производят охлаждение до температуры, выше температуры начала мартенситного превращения (400…600oС), но ниже температуры рекристаллизации, и при этой температуре осуществляют обработку давлением и закалку (рис. 16.1 б).
Низкотемпературная термомеханическая обработка, хотя и дает более высокое упрочнение, но не снижает склонности стали к отпускной хрупкости. Кроме того, она требует высоких степеней деформации (75…95 %), поэтому требуется мощное оборудование.
Низкотемпературную термомеханическую обработку применяют к среднеуглеродистым легированным сталям, закаливаемым на мартенсит, которые имеют вторичную стабильность аустенита.
Повышение прочности при термомеханической обработке объясняют тем, что в результате деформации аустенита происходит дробление его зерен (блоков). Размеры блоков уменьшаются в два – четыре раза по сравнению с обычной закалкой. Также увеличивается плотность дислокаций. При последующей закалке такого аустенита образуются более мелкие пластинки мартенсита, снижаются напряжения.
Механические свойства после разных видов ТМО для машиностроительных сталей в среднем имеют следующие характеристики (см. табл. 16.1):
Таблица 16.1. Механические свойства сталей после ТМО
| , МПа | , МПа | , % | , % |
НТМО | 2400…2900 | 2000…2400 | 5…8 | 15…30 |
ВТМО | 2100…2700 | 1900…2200 | 7…9 | 25… 40 |
ТО | 1400 | 1100 | 2 | 3 |
| | | | (сталь 40 после обычной закалки) |
Термомеханическую обработку применяют и для других сплавов.
Поверхностное упрочнение стальных деталей
Конструкционная прочность часто зависит от состояния материала в поверхностных слоях детали. Одним из способов поверхностного упрочнения стальных деталей является поверхностная закалка.
В результате поверхностной закалки увеличивается твердость поверхностных слоев изделия с одновременным повышением сопротивления истиранию и предела выносливости.
Общим для всех видов поверхностной закалки является нагрев поверхностного слоя детали до температуры закалки с последующим быстрым охлаждением. Эти способы различаются методами нагрева деталей. Толщина закаленного слоя при поверхностной закалке определяется глубиной нагрева.
Наибольшее распространение имеют электротермическая закалка с нагревом изделий токами высокой частоты (ТВЧ) и газопламенная закалка с нагревом газово-кислородным или кислородно-керосиновым пламенем.
Закалка токами высокой частоты.
Метод разработан советским ученым Вологдиным В.П.
Основан на том, что если в переменное магнитное поле, создаваемое проводником-индуктором, поместить металлическую деталь, то в ней будут индуцироваться вихревые токи, вызывающие нагрев металла. Чем больше частота тока, тем тоньше получается закаленный слой.
Обычно используются машинные генераторы с частотой 50…15000 Гц и ламповые генераторы с частотой больше 106 Гц. Глубина закаленного слоя – до 2 мм.
Индукторы изготавливаются из медных трубок, внутри которых циркулирует вода, благодаря чему они не нагреваются. Форма индуктора соответствует внешней форме изделия, при этом необходимо постоянство зазора между индуктором и поверхностью изделия.
Схема технологического процесса закалки ТВЧ представлена на рис. 16.2.
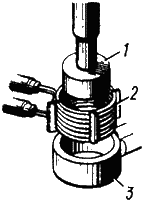
Рис. 16.2. Схема технологического процесса закалки ТВЧ
После нагрева в течение 3…5 с индуктора 2 деталь 1 быстро перемещается в специальное охлаждающее устройство – спрейер 3, через отверстия которого на нагретую поверхность разбрызгивается закалочная жидкость.
Высокая скорость нагрева смещает фазовые превращения в область более высоких температур. Температура закалки при нагреве токами высокой частоты должна быть выше, чем при обычном нагреве.
При правильных режимах нагрева после охлаждения получается структура мелкоигольчатого мартенсита. Твердость повышается на 2…4 HRC по сравнению с обычной закалкой, возрастает износостойкость и предел выносливости.
Перед закалкой ТВЧ изделие подвергают нормализации, а после закалки низкому отпуску при температуре 150…200oС (самоотпуск).
Наиболее целесообразно использовать этот метод для изделий из сталей с содержанием углерода более 0,4 %.
Преимущества метода:
-
большая экономичность, нет необходимости нагревать все изделие; -
более высокие механические свойства; -
отсутствие обезуглероживания и окисления поверхности детали; -
снижение брака по короблению и образованию закалочных трещин; -
возможность автоматизации процесса; -
использование закалки ТВЧ позволяет заменить легированные стали на более дешевые углеродистые; -
позволяет проводить закалку отдельных участков детали.