Файл: Конспект лекций по учебной дисциплине Материаловедение.doc
ВУЗ: Не указан
Категория: Не указан
Дисциплина: Не указана
Добавлен: 01.12.2023
Просмотров: 722
Скачиваний: 3
ВНИМАНИЕ! Если данный файл нарушает Ваши авторские права, то обязательно сообщите нам.
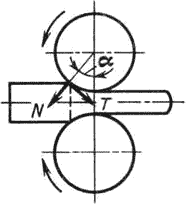
Рис. 10.1. Схема сил, действующих при прокатке
Угол – угол захвата, дуга, по которой валок соприкасается с прокатываемым металлом – дуга захвата, а объ¨м металла между дугами захвата – очаг деформации.
Возможность осуществления прокатки определяется условием захвата металла валками или соотношением ,
где: – втягивающая сила - проекция силы трения на горизонтальную ось; – выталкивающая сила – проекция нормальной реакции валков на горизонтальную ось.
При этом условии результирующая сила будет направлена в сторону движения металла.
Условие захвата металла можно выразить:
Выразив силу трения через нормальную силу и коэффициент трения : , и, подставив это выражение в условие захвата, получим:
или .
Таким образом, для захвата металла валками необходимо, чтобы коэффициент трения между валками и заготовкой был больше тангенса угла захвата.
Коэффициент трения можно увеличить применением насечки на валках.
При прокатке стали = 20…25 0, при горячей прокатке листов и полос из цветных металлов – = 12…15 0, при холодной прокатке листов – = 2…10 0.
Степень деформации характеризуется показателями:
– абсолютное обжатие: ( – начальная и конечная высоты заготовки);
относительное обжатие:
Площадь поперечного сечения заготовки всегда уменьшается. Поэтому для определения деформации (особенно когда обжатие по сечению различно) используют показатель, называемый вытяжкой (коэффициентом вытяжки).
где: – первоначальные длина и площадь поперечного сечения, – те же величины после прокатки.
Вытяжка обычно составляет 1,1…1,6 за проход, но может быть и больше.
Способы прокатки
Когда требуется высокая прочность и пластичность, применяют заготовки из сортового или специального проката. В процессе прокатки литые заготовки подвергают многократному обжатию в валках прокатных станов, в результате чего повышается плотность материала за сч¨т залечивания литейных дефектов, пористости, микротрещин. Это прида¨т заготовкам из проката высокую прочность и герметичность при небольшой их толщине.
Существуют три основных способа прокатки, имеющих определенное отличие по характеру выполнения деформации: продольная, поперечная, поперечно – винтовая (рис.10.2).
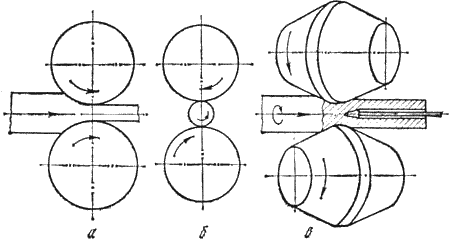
Рис. 10.2. Схемы основных видов прокатки:
а – продольная; б – поперечная; в – поперечно – винтовая
При продольной прокатке деформация осуществляется между вращающимися в разные стороны валками (рис.10.2 а). Заготовка втягивается в зазор между валками за сч¨т сил трения. Этим способом изготавливается около 90 % проката: весь листовой и профильный прокат.
Поперечная прокатка (рис. 10.2.б). Оси прокатных валков и обрабатываемого тела параллельны или пересекаются под небольшим углом. Оба валка вращаются в одном направлении, а заготовка круглого сечения – в противоположном.
В процессе поперечной прокатки обрабатываемое тело удерживается в валках с помощью специального приспособления. Обжатие заготовки по диаметру и придание ей требуемой формы сечения обеспечивается профилировкой валков и изменением расстояния между ними. Данным способом производят специальные периодические профили, изделия представляющие тела вращения – шары, оси, шестерни.
Поперечно – винтовая прокатка (рис. 10.2.в). Валки, вращающиеся в одну сторону, установлены под углом друг другу. Прокатываемый металл получает ещ¨ и поступательное движение. В результате сложения этих движений каждая точка заготовки движется по винтовой линии. Применяется для получения пустотелых трубных заготовок.
В качестве инструмента для прокатки применяют валки прокатные, конструкция которых представлена на рис. 10.3. В зависимости от прокатываемого профиля валки могут быть гладкими (рис.10.3.а), применяемыми для прокатки листов, лент и т.п. и калиброванными (ручьевыми) (рис. 10.3.б) для получения сортового проката.
Ручей – профиль на боковой поверхности валка. Промежутки между ручьями называются буртами. Совокупность двух ручь¨в образует полость, называемую калибром, каждая пара валков образует несколько калибров. Система последовательно расположенных калибров, обеспечивающая получение требуемого профиля заданных размеров называется калибровкой.
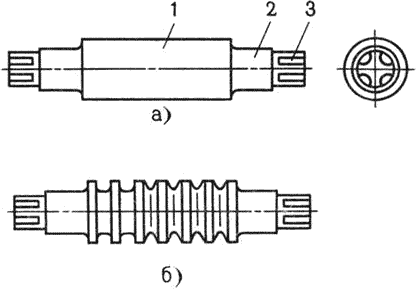
Рис. 10.3. Прокатные валки: а – гладкий ; б – калиброванный
Валки состоят из рабочей части – бочки 1, шеек 2 и трефы 3.
Шейки валков вращаются в подшипниках, которые, у одного из валков, могут перемещаться специальным нажимным механизмом для изменения расстояния между валками и регулирования взаимного расположения осей.
Трефа предназначена для соединения валка с муфтой или шпинделем.
Используются роликовые подшипники с низким коэффициентом трения, = 0,003…0,005, что обеспечивает большой срок службы.
Технологический процесс прокатки
Исходным продуктом для прокатки могут служить квадратные, прямоугольные или многогранные слитки, прессованные плиты или кованые заготовки.
Процесс прокатки осуществляется как в холодном, так и горячем состоянии. Начинается в горячем состоянии и проводится до определ¨нной толщины заготовки. Тонкостенные изделия в окончательной форме получают, как правило, в холодном виде (с уменьшением сечения увеличивается теплоотдача, поэтому горячая обработка затруднена).
Основными технологическими операциями прокатного производства являются подготовка исходного металла, нагрев, прокатка и отделка проката.
Подготовка исходных металлов включает удаление различных поверхностных дефектов (трещин, царапин, закатов), что увеличивает выход готового проката.
Нагрев слитков и заготовок обеспечивает высокую пластичность, высокое качество готового проката и получение требуемой структуры. Необходимо строгое соблюдение режимов нагрева.
Основное требование при нагреве: равномерный прогрев слитка или заготовки по сечению и длине до соответствующей температуры за минимальное время с наименьшей потерей металла в окалину и экономным расходом топлива.
Температуры начала и конца горячей деформации определяются в зависимости от температур плавления и рекристаллизации. Прокатка большинства марок углеродистой стали начинается при температуре 1200…1150 0С, а заканчивается при температуре 950…9000С.
Существенное значение имеет режим охлаждения. Быстрое и неравномерное охлаждение приводит к образованию трещин и короблению.
При прокатке контролируется температура начала и конца процесса, режим обжатия, настройка валков в результате наблюдения за размерами и формой проката. Для контроля состояния поверхности проката регулярно отбирают пробы.
Отделка проката включает резку на мерные длины, правку, удаление поверхностных дефектов и т.п. Готовый прокат подвергают конечному контролю.
Процесс прокатки осуществляют на специальных прокатных станах.
Прокатный стан – комплекс машин для деформирования металла во вращающихся валках и выполнения вспомогательных операций (транспортирование, нагрев, термическая обработка, контроль и т.д.).
Оборудование для деформирования металла называется основным и располагается на главной линии прокатного стана (линии рабочих клетей).
Главная линия прокатного стана состоит из рабочей клети и линии привода, включающей двигатель, редуктор, шестеренную клеть, муфты, шпиндели. Схема главной линии прокатного стана представлена на рис. 10.4.
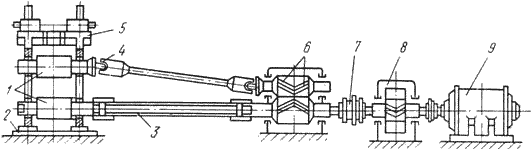
Рис.10.4. Схема главной линии прокатного стана
1 – прокатные валки; 2 – плита; 3 – трефовый шпиндель; 4 – универсальный шпиндель;
5 – рабочая клеть; 6 – шестеренная клеть; 7 – муфта; 8 – редуктор; 9 – двигатель
Прокатные валки 1 установлены в рабочей клети 5, которая воспринимает давление прокатки. Определяющей характеристикой рабочей клети являются размеры прокатных валков: диаметр (для сортового проката) или длина (для листового проката) бочки. В зависимости от числа и расположения валков в рабочей клети различают прокатные станы: двухвалковые (дуо-стан), трехвалковые (трио-стан), четырехвалковые (кварто-стан) и универсальные (рис.10.5).
В двухвалковых клетях (рис.10.5.а) осуществляется только по одному пропуску металла в одном направлении. Металл в трехвалковых клетях (рис. 10.5.б) движется в одну сторону между нижним и верхним, а в обратную – между средним и верхним валками.
В четырехвалковых клетях (рис. 10.5.в) устанавливаются опорные валки, которые позволяют применять рабочие валки малого диаметра, благодаря чему увеличивается вытяжка и снижаются деформирующие усилия.
Универсальные клети (рис.10.5.г) имеют неприводные вертикальные валки, которые находятся между опорами подшипников горизонтальных валков и в одной плоскости с ними.
Шестеренная клеть 6 предназначена для распределения крутящего момента двигателя между валками. Это одноступенчатый редуктор, передаточное отношение которого равно единице, а роль шестерен выполняют шестеренные валки.
Шпиндели предназначены для передачи крутящего момента от шестеренной клети прокатным валкам при отклонении от соосности до 10…12 0. При незначительном перемещении в вертикальной плоскости применяют шпиндели трефового типа 3 в комплекте с трефовой муфтой. Внутренние очертания трефовых муфт отвечают форме сечения хвостовика валка или шпинделя. Муфтой предусмотрен зазор 5…8 мм, что допускает возможность работы с перекосом 1…2 0
. При значительных перемещениях валков в вертикальной плоскости ось шпинделя может составлять значительный угол с горизонтальной плоскостью, в этом случае применяют шарнирные или универсальные шпиндели 4, которые могут передавать крутящий момент прокатным валкам при перекосе шпинделя до 10…12 0.
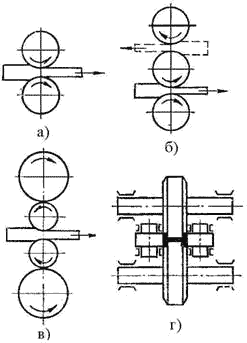
Рис. 10.5. Рабочие клети прокатных станов
В качестве двигателя прокатного стана 9 применяют двигатели постоянного и переменного тока, тип и мощность зависят от производительности стана.
Редуктор 8 используется для изменения чисел оборотов при передаче движения от двигателя к валкам. Зубчатые колеса – обычно шевронные с наклоном спирали 30 0.
По назначению прокатные станы подразделяют на станы для производства полупродукта и станы для выпуска готового проката.
Нагрев металла осуществляют в пламенных и электрических печах. По распределению температуры печи могут быть камерные и методические. В камерных печах периодического нагрева температура одинакова по всему рабочему пространству. В методических печах температура рабочего пространства постоянно повышается от места загрузки заготовок до места их выгрузки. Металл нагревается постепенно, методически. Печи характеризуются высокой производительностью. Применяются в прокатных и кузнечно-штамповочных цехах для нагрева слитков из цветных металлов. Крупные слитки перед прокаткой нагревают в нагревательных колодцах – разновидности камерных, пламенных печей.
В качестве транспортных устройств в прокатном производстве используют:
-
слитковозы и различного вида тележки для подачи слитков и заготовок от нагревательных устройств к стану; -
рольганги – основное транспортное средство прокатных цехов (транспортеры с последовательно установленными вращающимися роликами обеспечивают продольное перемещение металла; при косом расположении роликов возникает возможность поперечного движения полосы); -
манипуляторы, предназначенные для правильной задачи полосы в калибр; -
кантователи, предназначенные для поворота заготовки вокруг горизонтальной оси.
Правка проката
Изделия, полученные прокаткой, часто требуют правки. Иногда правку выполняют в горячем состоянии, например, при производстве толстых листов. Но обычно в холодном состоянии, так как последующее охлаждение после горячей правки может вызвать дополнительное изменение формы.