Добавлен: 02.12.2023
Просмотров: 40
Скачиваний: 2
ВНИМАНИЕ! Если данный файл нарушает Ваши авторские права, то обязательно сообщите нам.
Для регулировании подачи газа на баллоны устанавливаются редукторы. Редукторы окрашиваются в цвет баллона. На рисунке 8 показан внешний вид кислородного редуктора.
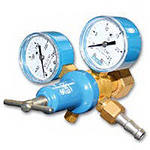
Рис.8. Внешний вид одноступенчатого редуктора:
1.4. ВЫБОР РЕЖИМА СВАРКИ.
Для электросварки. Под режимом сварки понимают совокупность контролируемых параметров, обеспечивающих устойчивое горение дуги и получение швов заданных размеров, формы и свойств.
По степени влияния на процессе сварки параметры режима подразделяют на основные и дополнительные. К основным параметрам относят диаметр стержня покрытого электрода, силу сварочного тока, его род и полярность, а также напряжение дуги.
Диаметр электродов выбирают в зависимости от толщины металла, катета шва и положения в пространстве. Примерное соотношение между толщиной S металла и диаметром d электрода при сварке шва в нижнем положении таково:
S, mm 1 - 2 3 - 5 4 - 10 12 - 24 30 - 60
d, mm 2 - 3 3 - 4 4 - 5 5 - 6 6 и более
Для сварки труб диаметром от 50мм до 100мм применяется электрод диаметром 4 мм.
Cилу сварочного тока обычно устанавливают в зависимости от выбранного диаметра электрода. При сварке швов в нижнем положении её значение, А, рассчитывают, пользуясь электрическими формулами:
Icв = Kd (1.1.)
I cв = (20 + 6d) d (1.2.)
где K – коэффициент, принимающий в зависимости от диаметра электрода d следующие значения:
d, mm 2 3 4 5 6
K 25……30 30……45 35……50 40……45 45……60
I cв = (20 + 6 4) 4=176 А
Род и полярность тока устанавливают в зависимости от вида свариваемого металла и его толщины.
Напряжение дуги при ручной дуговой сварке изменяется в пределах 20….. 36 В и регламентируется производителем электродов. В процессе сварки постоянное значение напряжения поддерживают за счет низменной длины дуги, которая зависит от марки и диаметра электрода. Ориентировочно нормальная длина дуги, мм:
Lд = (0,5……1,1) d (1.3.)
Длина дуги существенно влияет на качество сварного шва и его форму.
Для газовой сварки: 1. Мощность пламени зависит от толщины металла (5 мм) и химического состава металла (низколегированная сталь 10ХСНД), определяется по формуле:
M = cS (1.4.)
где с- удельный коэффициент мощности пламени;
S- толщина металла мм;
М = 80 5 = 400 л/ч.
2. Состав пламени – нормальное;
3. Скорость сварки:
Vсв = А/S (1.5.)
где А – коэффициент, зависящий от свойств металла (12-15) ммм/ч;
S – толщина металла (5) мм;
Vсв = 125=60 м/ч.
4. Диаметр присадочного прутка: 3 мм.
5. Угол наклона мундштука: 30 - 400 9
1.5. КОНТРОЛЬ КАЧЕСТВА СВАРОЧНЫХ РАБОТ.
Контроль сварных соединений производится в три этапа:
Предварительный контроль - проверка основного металла, электродов, качества сборки, подготовки под сварку, состоянию сварочной аппаратуры, квалификации сварщика.
Контроль в процессе сварки - проверка правильности выбранного режима, соблюдения технологии
Окончательный контроль качества сварных соединений.
При окончательном контроле качества сварных соединений производят следующие работы:
- Внешний осмотр, которым определяют видимые дефекты;
- Гидравлическое испытание проводят при давлении, на 25-50% превышающем рабочее;
- Радиоактивный метод.
При пневматическом испытании:
Установка регистра на решетки ванны
Установка заглушек с подсоединением шланга.
Погружение регистра в воду и испытание давлением 0,1 МПа (1 кгс/см2) в течение 0,5 мин.
Осмотр регистра с отметкой дефектных мест.
Отсоединение шланга и снятие заглушки.
Относка регистра с укладкой в контейнер.
Контроль качества шва.
Качество сварки и сварных соединений – это основной показатель, которому должно соответствовать изделие для удовлетворения запросов заказчика.
Стоит отметить, что в общем качество сварки и сварных соединений зависит от различных факторов, в том числе и от, собственно, технологического процесса. Общее качество сварки определяется по уровням дефектов при сваривании металлоизделий.
Основные показатели, влияющие на общее качество сварки, представлены на рисунке 9.
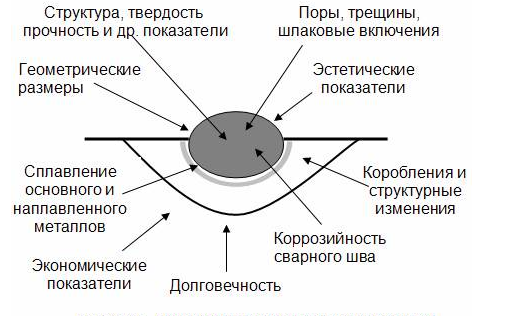
Рисунок 9. Показатели качества сварки деталей
Подробнее остановимся на основных технологических факторах, влияющих на качество сваривания:
-
режим сварочного процесса – это и сила тока, и напряжение; -
материалы необходимые для сваривания: электроды, флюсы, защитные газы; -
материал свариваемого изделия; -
профессионализм сварщика – это и разряд, и опыт работы; -
условия, в которых производится сваривание.
Способы контроля качества сварки и сварочных соединений.
Контроль качества сварки и сварных соединений состоит из нескольких обязательных этапов, которые позволяют определить дефекты. В ходе контроля осуществляется проверка таких показателей:
-
приемлемого внешнего вида (при внешнем осмотре); -
плотности сварного шва; -
физико-химических свойств сварного шва.
Кроме того, контроль качества сварных соединений может быть:
-
предварительным – это первичный контроль сварного соединения для определения качества сварки. Такой контроль предупреждает образование дефектов, он заключается в контроле электродов, флюсов, соблюдения режимов работы и т.д.; -
окончательный – это контроль, который оценивает результаты технологического процесса, его суть заключается в определении качества швов и выявлении дефектов.
Остановимся на каждом методе контроля детальнее.
Предварительный контроль качества сварки и сварных соединений включает в себя следующие этапы:
-
Контроль подготовки к сварочным работам. На этом этапе проверяется качество используемых в процессе работ сварочных материалов, кромок деталей металлоизделия, подготовленных под сварку, оборудования и оснастки, кроме того контрольную проверку проходит сам свариваемый материал и, конечно, необходимо удостовериться в готовности сварщиков к работе. -
Контроль непосредственно над самими сварочными работами. Этот этап заключается в контроле режимов сваривания, проверке соблюдения технологического процесса сваривания, проверке порядка наложения кромок деталей, зачистки кратеров, швов.
Окончательный контроль качества сварки, сварных соединений направлен на определение образовавшихся дефектов и состоит из множества видов проверки:
-
Визуальный осмотр сварного шва. При внешнем осмотре определяется наружный брак: наличие незаваренных мест, наплывов, подрезов, трещин, а также наличие смещения сваренных деталей, которое могло произойти в процессе сваривания. Обычно, после сварки деталь зачищают от окалин, брызг и шлака. Осмотр сварного соединения производится представителем отдела технического контроля с применением лупы с пяти и даже десятикратным увеличением. -
Испытание сварных соединений на проницаемость – это проверка, которой подвергают емкости, которые работают под давлением газовой или жидкой среды. Такая проверка проводится испытанием, но только после визуального осмотра и устранения выявленных дефектов.
Испытания сварочных швов в аппаратах, которые предназначены для работы под давлением:
-
Давление жидкостей (гидравлическое).
1 способ. Емкость полностью или частично заполняется водой на 2-24 часа. Сварной шов считается качественным, если в течение вышеуказанного времени не дал течи и остался с внешней стороны в сухом виде.
2 способ. Емкость, трубопровод или другого вида конструкция наполняется водой и на пять минут создается внутри сосуда избыточное давление – в два раза выше рабочего. После истечения вышеуказанного времени давление снижается до рабочего, а околошовную зону снаружи обстукивают молотком. Влажные и запотевшие участки – дефекты, отмечаются мелом. Затем вода сливается из сосуда, а некачественные швы завариваются! После устранения дефектов швы опять подвергаются испытаниям.
-
Давление газа.
В емкость или трубопровод подается газ, воздух или азот под давлением, указанным в технических условиях. Затем сосуд герметизируется, а все сварочные швы промазываются мыльным раствором, состоящим из 100 г мыла и одного литра воды. Если сварной шов с дефектом, то на нем будут появляться мыльные пузыри.
-
Испытание аммиаком.
Перед началом этого испытания предварительно необходимо очистить сварные швы от окалин, масла и ржавчины. Затем на шов накладывают тканевый кусочек или бумажную ленту, которые перед этим пропитывают специальным индикатором. Далее в проверяемую емкость нагнетают воздух с одним процентом аммиака. Если сварное соединение с дефектом – имеются микроскопические трещины или не проваренные места, то бумага или ткань с индикатором окрашиваются в серебристо-черный цвет в течение пяти минут под воздействием аммиака.
Контроль качества сварки и сварных соединений с помощью рентгеновского просвечивания представлен на рисунке 10.
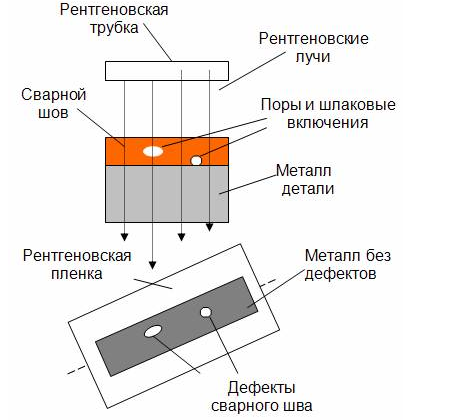
Рисунок 10. Рентгеновское просвечивание
Такой вид контроля позволяет выявлять трещины и непровары в изделиях из стали с глубиной залегания до 100 миллиметров, в медных деталях – до 25 мм и в алюминиевых – до 300 мм.
Преимущества рентгеновского метода.
-
высокая чувствительность; -
позволяет точно определить размер дефекта; -
точное нахождение места расположения дефекта.
Недостатки рентгеновского метода:
-
рентгеновское излучение вредно для человека; -
довольно большие габариты аппарата; -
трудоемкость работ; -
сложность управления аппаратурой.
Рассмотрим, также значение магнитного поля в контроле качества сварки и сварных соединений.
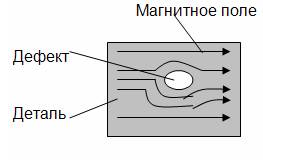
Рисунок 11. Магнитное поле
Магнитный порошок – это порошок, получаемый путем шлифовки металла. Порошок наносят в сухом или масляном виде на сварочное соединение, после чего изделие намагничивается. В местах дефекта магнитный порошок скапливается за счет искажения магнитного поля (рис.11).
Все виды вышеперечисленных методов контроля высокоэффективны и позволяют выявить даже микроскопические дефекты сварных соединений.
2. ОРГАНИЗАЦИОННАЯ ЧАСТЬ.
2.1. ОХРАНА ТРУДА.
Каждый сварщик обязан перед началом работы проверить исправность аппаратуры и готовность места сварки в противопожарном отношении (наличие средств пожаротушения — ящиков с песком, лопат, ведер с водой, огнетушителей).
Во время работы нельзя допускать попадания искр, расплавленного металла, пламени горелки, электродных огарков на сгораемые Конструкции и материалы.
После выполнения сварочных работ необходимо тщательно осмотреть рабочее место, нижележащие площадки и этажи и в случае обнаружения воспламенения полить их водой.
К проведению сварочных работ допускаются сварщики, прошедшие противопожарный минимум и получившие специальные квалификационные удостоверения и специальный талон на право допуска их к проведению огневых работ. Разрешение на право проведения огневых работ выдается начальником или главным инженером строительства.
При проведении сварочных работ запрещается:
а) приступать к работе при неисправной аппаратуре;
б) производить сварку или резку свежеокрашенных конструкций до полного высыхания краски;
в) пользоваться при сварке одеждой и рукавицами со следами масел и жиров, бензина и других горючих жидкостей;
г) хранить в сварочных кабинах или в зоне сварки горючие либо взрывчатые предметы и материалы;
д) допускать к сварочным работам сварщиков или учеников сварщиков, не сдавших испытаний по противопожарной безопасности при выполнении сварочных работ;
е) выполнять сварку емкостей, содержащих горючие или взрывчатые вещества, а также сварку сосудов, находящихся под давлением, сварку