Файл: Лекция 1. Неплавящиеся электроды для дуговой сварки общие сведения о неплавящихся электродах.doc
ВУЗ: Не указан
Категория: Не указан
Дисциплина: Не указана
Добавлен: 11.01.2024
Просмотров: 341
Скачиваний: 2
ВНИМАНИЕ! Если данный файл нарушает Ваши авторские права, то обязательно сообщите нам.
Просушенные шихтовые материалы хранят в расходных бункерах дозировочного отделения, причем для каждого из материалов предназначен отдельный бункер.
5) Составление и подготовка шихты. Составление шихты предусматривает выполнение следующих операций: расчет состава шихты; составление рецепта; дозировку компонентов по рецепту; смешение компонентов.
Состав шихты рассчитывают в соответствии с регламентируемым НТД химическим составом флюса марки АН-348-А и химическим составом компонентов (по результатам контрольного анализа), предназначенных для изготовления данной партии флюса.
По результатам расчета состава шихты должен быть составлен рецепт шихты на одну плавку флюса.
Расчет состава шихты, составление рецепта шихты на одну плавку и одну порцию следует выполнять в специальном рецептурном журнале. Каждый расчет должен быть подписан технологом с указанием даты, а рецепту присваивают порядковый номер.
Взвешенная по рецепту шихта на одну плавку должна быть перемешана в смесителе, обеспечивающем получение однородной по цвету и внешнему виду шихты.
6) Загрузка шихты в печь.
Подготовленную на каждую плавку шихту загружают в приемный бункер флюсоплавильной установки, откуда с помощью вибрационных, шнековых устройств или каким-либо другим механическим путем ее подают в плавильное пространство. Доза шихты, одновременно подаваемой в печь, определяется в зависимости от количества в шихте материалов, разлагающихся при нагреве с выделением значительного количества газообразных веществ и вместимостью печи. При правильной загрузке должно обеспечиваться спокойное расплавление шихты без выбросов, выплесков и образования спекшейся корки над расплавом.
7) Выплавка флюса.
Плавка флюса является наиболее ответственной операцией в технологическом процессе изготовления плавленых флюсов и предусматривает выполнение следующих операций: подготовку печи к работе; пуск печи и подбор режима выплавки; подачу шихты в ванну печи; расплавление шихты; выдержку расплава до готовности; установление готовности расплава к выпуску.
В процессе плавки может быть осуществлено рафинирование расплава с целью снижения в готовом флюсе содержания серы и фосфора.
Уменьшение содержания серы во флюсе достигается за счет ее окисления по реакции
S+O2=SO2 ↑
Повышения окислительного потенциала расплава можно добиться за счет тщательного перемешивания материалов с большим содержанием серы с материалами, имеющими высокую окислительную способность. Применение указанных мер позволяет снизить содержание серы во флюсе с 1,5 до 0,15%.
Снижение содержания фосфора во флюсе достигается за счет его восстановления из рудоминеральных материалов по реакции
2Р2О5 + 5С = 4 [Р] ↓ + 5СО2 ↑
Одновременно с фосфором происходит частичное восстановление железа, марганца, кремния, которые образуют так называемые металлические корольки, осаждающиеся на дно печи в виде металлического осадка, периодически удаляемого по мере его накопления.
Интенсификации перевода фосфора из шлака в металлический осадок способствуют перегрев расплава и его дополнительное раскисление, обеспечиваемое за счет введения раскислителей как в состав шихты, так и на зеркало расплава при его выдержке.
Строение зерен, получаемых при сливе флюса (стекловидное, пемзовидное, стекло-пемзовидное), определяется степенью перегрева флюсового расплава, его раскисленностью и технологией слива расплава в воду. Пемзовидное строение зерен получается при определенном перегреве расплава флюса, обеспечиваемом либо за счет применения повышенных параметров режима при выдержке расплава, либо за счет его дополнительного раскисления. Более интенсивно образование пемзовидного строения зерен происходит при сливе расплава в подогретую воду.
8) Выпуск флюса из печи и его грануляция.
Выпускать флюс из печи следует непрерывно равномерной струей через верхний сливной носок.
Расплав сливают в приемную корзину, установленную в грануляционный бассейн, наполненную водой до специальной отметки.
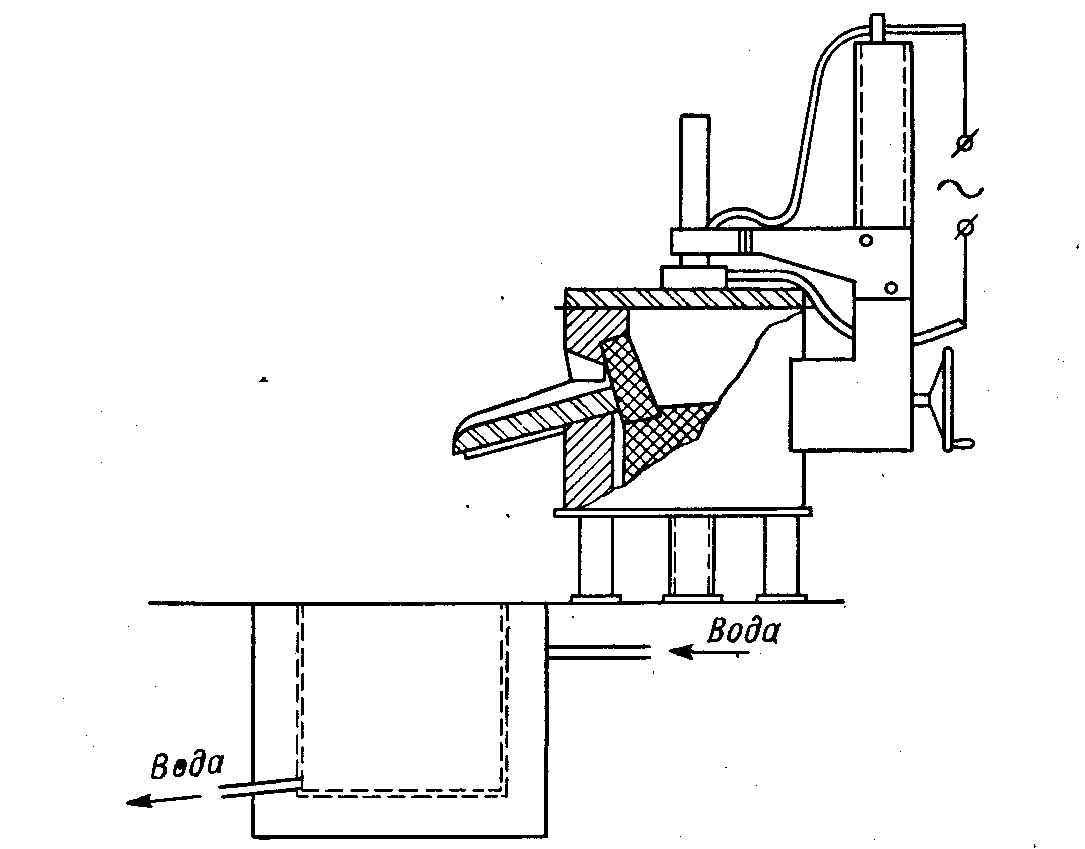
Рис. 4.1. Электрическая печь для плавки флюса с баком для грануляции по мокрому способу.
Грануляционный бассейн должен иметь объем, превышающий не менее чем в 5 раз объем флюса после слива расплава одной плавки. В состав грануляционного устройства должны входить напорный насос, обеспечивающий создание давления воды в грануляционной системе не менее 4,9·105 Па, насадка для формирования струи воды, гранулирующей флюс, и направляющее устройство, обеспечивающее изменение направления струи воды в вертикальной и горизонтальной плоскостях.
При сливе расплава струя воды должна подаваться в место встречи струи расплава с поверхностью воды в приемной корзине, но не на струю расплава.
Если при начале слива расплава пемзовидных флюсов наблюдаются единичные хлопки, представляющие собой мелкие слабые взрывы, слив расплава следует прекратить и продолжить его разогрев. Слив и выгребание разогретых осадков расплава из тигля печи в воду запрещается. Удаление осадков допускается только в специальную изложницу.
После окончания слива расплава корзину с флюсом переносят из бассейна на специальную площадку, предназначенную для стока воды.
9) Сушка флюса.
После мокрой грануляции для естественного удаления основной массы воды флюс отстаивается и высушивается в специализированном оборудовании, обеспечивающем удаление воды до влажности, не превышающей 0,05—0,1 %. Длительность операции отстоя флюса не должна превышать 8 ч.
Сушка флюса может осуществляться в камерных электропечах.
При этом флюс должен быть загружен на противни из жаростойкой стали 20Х20Н14С2, 20Х23Н18, 10Х23Н18 или других с температурой начала интенсивного окалинообразования в воздушной среде не ниже 1000 °С.
Высота слоя флюса на противнях не должна превышать 100—150 мм. Камерные электропечи должны обеспечивать нагрев стекловидных флюсов до температуры 350—400ºС и пемзовидных до 350—500°С и удаление паров воды из рабочего пространства. Печи также должны быть оборудованы приборами, регистрирующими температуру и продолжительность сушки флюсов.
Просеивают флюсы на вибрационньтх, осуществляющих частичное измельчение и сортировку зерен по размерам согласно НТД на конкретную марку флюса. Мелкую и крупную фракции, не соответствующие требованиям НТД, возвращают на переплав или доизмельчение.
Строение и цвет, размер зерен и объемная масса сварочных плавленых флюсов приведены в таблице 4.2
Таблица 4.2
Строение, цвет, размер зерен и объемная масса сварочных плавленых флюсов
Марка флюса | Строение зерен | Цвет зерен | Размер зерен, мм | Объемная масса, кг/дм3 |
АН-348-А | Стекловидное | Желтый и коричневый цвет всех оттенков | 0,35-3,0 | 1,3-1,8 |
АН-348-АМ | 0,25-1,60 | |||
ОСЦ-45 | Светло-серый, желтый и коричневый всех оттенков | 0,35-3,00 | ||
ОСЦ-45М | 1,25-1,60 | |||
ФЦ-9 | Светло-желтый и коричневый всех оттенков | 0,25-1,60 | ||
АН-60 | Пемзовидное | Белый, желтый всех оттенков и светло-коричневый | 0,35-4,00 | 0,7-1,0 |
АН-20П | Белый и светло-серый | 0,35-4,00 | ||
АН-26П | Светло-серый | 0,35-3,00 | ||
АН-8 | Стекловидное | Желтый и коричневый всех оттенков | 0,25-2,50 | 1,5-1,8 |
АН-20С | Светло-серый и светло-голубой | 0,35-3,00 | 1,2-1,7 | |
АН-20СМ | 0,25-1,60 | |||
АН-22 | Желтый всех оттенков и светло-коричневый | 0,25-2,50 | 1,5-1,8 | |
АН-26С | Серый всех оттенков и светло-зеленный | 0,25-2,50 | 1,3-1,8 | |
АН-26СП | Смесь стекловидных и пемзовидных зерен | Серый всех оттенков и светло-зеленный | 0,25-4,00 | 0,9-1,3 |
Годную фракцию для удаления металлических включений, попавших в флюс во время грануляции, сушки и рассева, подвергают магнитной сепарации. Конструкции магнитных сепараторов и место их установки должны обеспечивать удаление слабомагнитных «корольков» металла из обрабатываемого флюса.
10) Усреднение партии флюса.
После сушки, рассева и магнитной сепарации, усреднение осуществляют в специальных емкостях сегментного типа, в которых флюс собирается в количестве, необходимом для формирования партии.
11) Определение качества партии флюса.
12) Упаковка флюса. Флюс может быть упаковав в пятислойные бумажные мешки (по ГОСТ 2226—75), полиэтиленовые мешки (по ГОСТ 17811—78) из пленки толщиной не менее 0,15 мм, металлические барабаны (по ГОСТ 5044—79), ящики типов П-1 и П-2 (по ГОСТ 2991—85), в пакеты (по ГОСТ 21929—76), крепящиеся на универсальных поддонах (по ГОСТ 26381—84).
Мешки должны быть защиты машинным способом или запаяны. Масса одного грузового места при упаковке в мешки не должна превышать 20 кг. Масса флюса, упакованного в металлический барабан, не должна превышать 50 кг, в ящики типа П-1 и П-2 —60 кг и в пакеты —1 т.
Каждая партия флюса должна сопровождаться сертификатом, удостоверяющим соответствие флюса требованиям ИТД с указанием: наименования или товарного знака завода-изготовителя; марки флюса; номера НТД; номера партии и даты ее изготовления; массы нетто партии; результатов приемосдаточных испытаний; дополнительных технологических рекомендаций; гарантийного срока хранения.
4.8. Технологический процесс изготовления керамических флюсов
Керамические флюсы представляют собой механическую смесь различных природных материалов и ферросплавов. Технология изготовления керамических флюсов идентична с технологией изготовления покрытых электродов:
- Полученную массу (измельчают) гранулируют
- Сушат, (20-24 часа)
- Прокаливают при температуре 150-4000С в течение 3-4 часов.
- Просеивают для получения частиц зерен определенного размера.
Частицы сухой смеси компонентов могут скрепляться спеканием при повышенных температурах без расплавления. Полученные комки гранулируют до необходимого размера (так называемые спеченные флюсы).
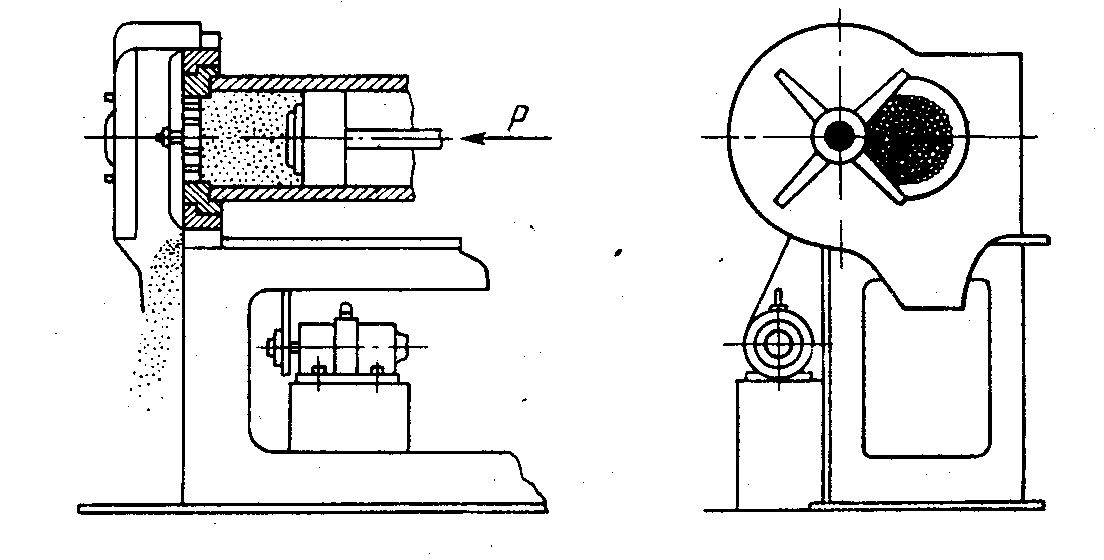
Рис. 4.2. Гранулятор для изготовления керамических флюсов
Существует несколько способов грануляции сырой массы.
-Первый способ. заключается в разливе сырой массы на металлический лист. После того как она засохнет, ее дробят и просеивают. В этом случае выход годного флюса очень низкий, получается много отходов. Этот способ применяется в лабораторных условиях.
-Второй способ. применяется в индивидуальном или мелкосерийном производстве, для получения значительно большего выхода годного флюса, сырую массу протирают через сито с определенной сеткой.
-Третий способ. применяется в массовом производстве. Для изготовле-ния гранулированной крупки из приготовленной массы применяют меха-низированные устройства (грануляторы) различных конструкций).
4.9. Технология изготовления флюс-пасты
Флюс-пасты представляют собой смесь компонентов и пастообразующей жидкости. В качестве пастообразующей жидкости используют: воду, ацетон, спирт, скипидар, растворитель и др. Чаще всего для приготовления флюс-пасты используют этиловый спирт. Так как он обладает быстрой испаряемостью, не ядовит и сравнительно доступен.
Последовательность операции изготовления флюс-пасты: прокалка компонентов; просеивание компонентов; взвешивание компонентов по рецептуре; перемешивание компонентов; замешивание компонентов на пастообразующей жидкости.
Хранение и контроль флюс-пасты. Флюс-пасты хранятся в герметично закрытой стеклянной или пластмассовой таре. На этикетках должны указываться сроки хранения и даты изготовления флюс-паст. Влажность флюса используемого при сварке не должна превышать указанного в паспорте флюса. Каждую партию флюса проверяют на химический и гранулометрический составы.
Лекция № 5.
Газы и жидкости, применяемые в сварочном производстве
План:
5.1. Кислород
5.2. Общие сведения о горючих газах
5.3. Ацетилен
5.4. Газы – заменители ацетилена
5.5. Карбид кальция
5.6. Инертные защитные газы
5.7. Активные защитные газы
5.1. Кислород
Кислород - самый распространенный на Земле элемент. Он составляет около 50 % массы Земли, где он находится в окислах различных элементов, около 86 % массы воды в соединении с водородом и 23 % массы воздуха (21 % по объему) в смеси с азотом, аргоном и с другими газами.