Файл: 1. Общая часть 7 1 Причины и износ деталей двухсекционного окорочного барабана 7 2 Методы защиты от износа деталей двухсекционного окорочного барабана 11 Специальная часть.docx
Добавлен: 11.01.2024
Просмотров: 80
Скачиваний: 3
ВНИМАНИЕ! Если данный файл нарушает Ваши авторские права, то обязательно сообщите нам.
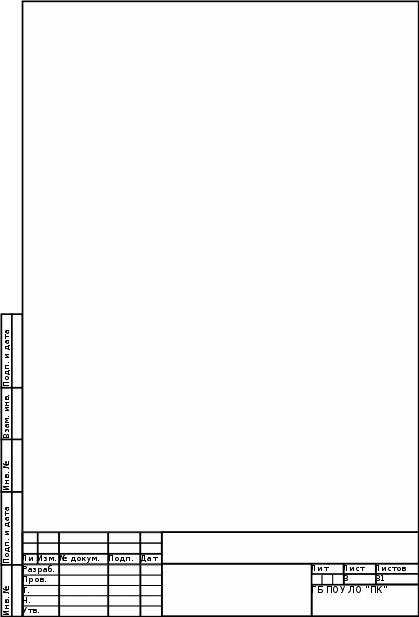
1.Общая часть 7
1.1 Причины и износ деталей двухсекционного окорочного барабана 7
1.2 Методы защиты от износа деталей двухсекционного окорочного барабана 11
2. Специальная часть 13
2.1 Назначение, устройство и принцип работы двухсекционного окорочного барабана 13
2.3 Способы восстановления деталей двухсекционного окорочного барабана 19
2.2 Работы, выполняемые при ремонте 22
3.Охрана труда при работах окорочного барабанa 26
Заключение 29
Список использованной литературы 30
Приложение 1 31
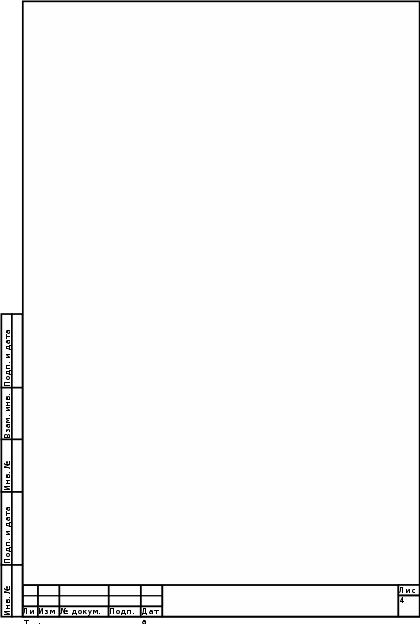
Тема данной курсовой работы является техническое обслуживание и ремонт окорочного барабана для сухой и мокрой окорки.
В общей части подробно описаны причины и виды износа деталей, а также рассмотрены некоторые методы защиты от износа окорочного барабана.
В специальной части идёт описание назначения, устройства и принцип работы окорочного барабана, рассматриваются методы восстановления и ремонта.
Охране труда отведен третий раздел работы. В ней содержится техника безопасности при ремонте.
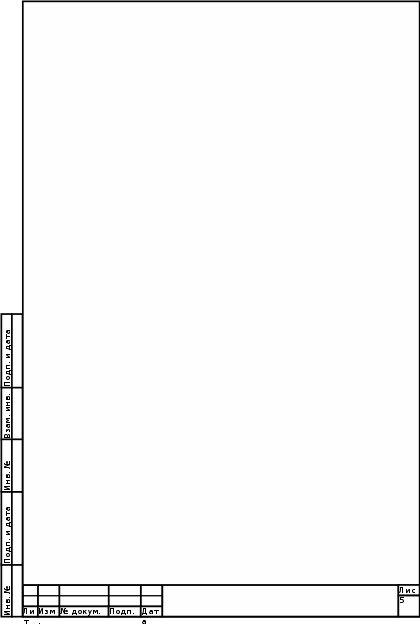
В современном целлюлозно-бумажном производстве используется более 500 типов разнообразных машин и аппаратов специального назначения. Это многообразие, с одной стороны, связано со сложностью и многоступенчатостью технологического процесса, с другой - объясняется непрерывными поисками оптимальных конструкций оборудования для осуществления каждого технологического этапа производства. Несмотря на большое многообразие, основное оборудование целлюлозно-бумажного производства может быть объединено в группы по виду выполняемой технологической операции. Ниже приведена блочная технологическая схема целлюлозно-бумажного производства и указаны основные виды оборудования, используемого на различных ступенях производства.
Технологический процесс целлюлозно-бумажного предприятия начинается со складирования и хранения исходного волокнистого сырья, основными видами которого являются балансы, щепа или макулатура. Для выполнения этих операций используется разнообразное оборудование для складирования и транспортировки указанных видов сырья (крановое оборудование, самоходные погрузчики, конвейеры, оборудование для пневмотранспорта).
Следующей технологической ступенью при переработке балансов является окорка древесины. Для окорки используются разнообразные машины, основными из которых являются окорочные станки и корообдирочные барабаны, широко используемые в ЦБП.
Актуальность темы заключается в том, что целлюлозно-бумажное производство потребляет большое количество кубометров древесины, как хвойных, так и лиственных пород. Но сначала их надо подготовить к использованию. Первичной подготовкой сырья является окорка древесины на соответствующем оборудовании. От организации данного процесса зависят не только количественные показатели сырья-щепы, но выходные показатели готовой целлюлозы, а также степень механизации труда, мероприятия по охране окружающей среды и пути утилизации отходов. Для окорки используется разнообразные машины - окорочные станки и корообдирочные барабаны.
Цель работы: ТО и Р окорочного барабана для сухой и мокрой окорки
Объект работы: промышленность
Предмет работы: окорочный барабан для сухой и мокрой окорки
Задачи исследования:
-изучить основные причины и виды износа деталей окорочного барабана;
-дать описание назначения, устройства и принципа работы окорочного барабана;
-определить ремонта конвейера;
-изучить основные положения охраны труда.
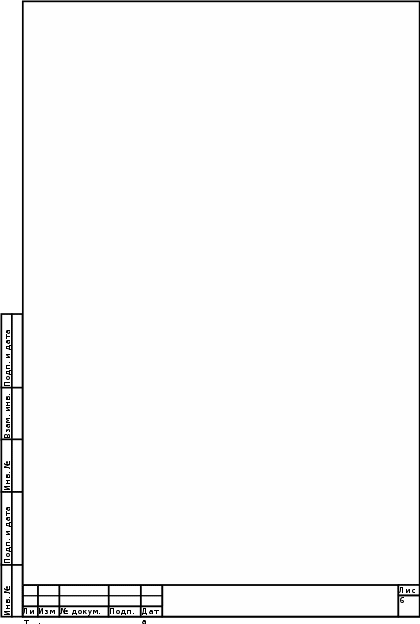
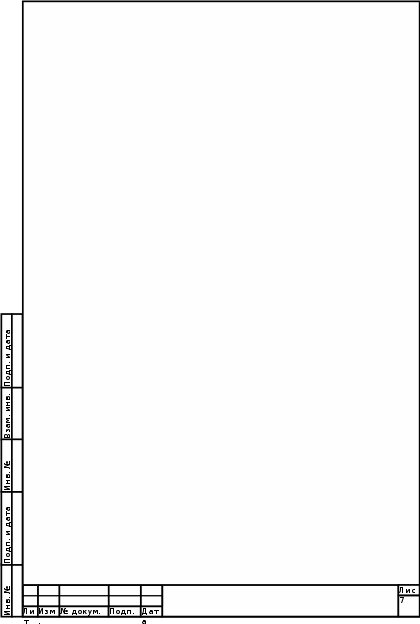
1.1 Причины и виды износа деталей двухсекционного окорочного барабана
Разрушение деталей оборудования происходит при их взаимодействии с твердыми, жидкими и газообразными средами. Наиболее часто встречают следующие виды разрушения:
-
изломы (вязкие, хрупкие, усталостные); -
деформации; -
изнашивание.
Излом — полное разрушение материала детали в результате растяжения, сжатия, изгиба или сложного напряженного состояния.
Вязкий излом происходит при напряжениях, превышающих предел текучести материала. Ему предшествует пластическая деформация материала под влиянием кручения или изгиба, а иногда вследствие растяжения или сжатия. Излом при этом виде разрушения имеет волокнистое строение со следами сдвига материала. Вязкое разрушение менее опасно, чем хрупкое, так как разрушение детали и поломка оборудования могут быть выявлены по появлению пластической деформации. Для предупреждения вязкого разрушения применяют следующие меры:
-
ограничивают перегрузку деталей во время работы с помощью муфт различных типов, срезных шпилек и др.; -
изготовляют детали из материала с повышенными механическими свойствами и термически их обрабатывают; -
увеличивают жесткость деталей; -
уменьшают рабочие напряжения в детали, используя ориентированный наклеп.
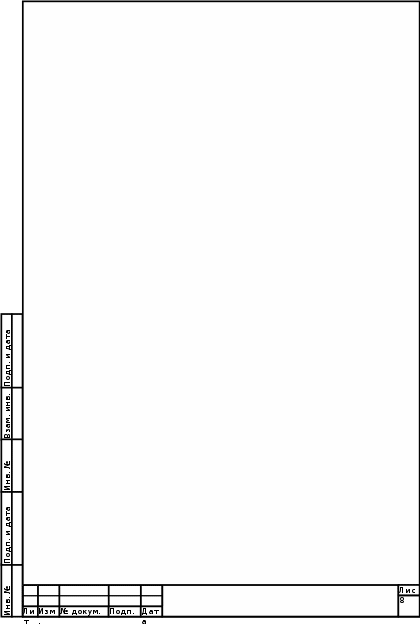
-
ограничивают перегрузку детали при работе установкой предохранительных устройств; -
уменьшают жесткость удара за счет амортизирующих устройств; -
повышают прочность и пластичность материала детали.
Усталостный излом возникает и развивается в наиболее напряженных поверхностных слоях детали вследствие длительного действия переменных по величине и знаку нагрузок. Чаще всего это происходит при тяжелом динамическом режиме работы деталей, больших перегрузках и несвоевременной замене изношенных деталей. Причиной поломки детали является усталостная трещина. Усталостный излом имеет две зоны: усталостного разрушения (мелкозернистая, блестящая или матовая поверхность) и единовременного разрушения (кристаллическое строение и другие признаки хрупкого разрушения).
Деформация материала происходит в результате приложения нагрузки и сопровождается изменением формы и размеров детали.
Во многих случаях циклическое действие контактных напряжений вызывает остаточную деформацию, которая не разрушает детали, но нарушает ее нормальную работу. Остаточная деформация появляется при взаимодействии колеса локомотива с рельсом, наблюдается на круглозвенных цепях конвейеров и др.
Контактная усталость металла проявляется в виде усталостного выкрашивания поверхности часто при трении качения со скольжением. Причина появления — пульсационное действие контактных напряжений вследствие переменного давления на поверхности.
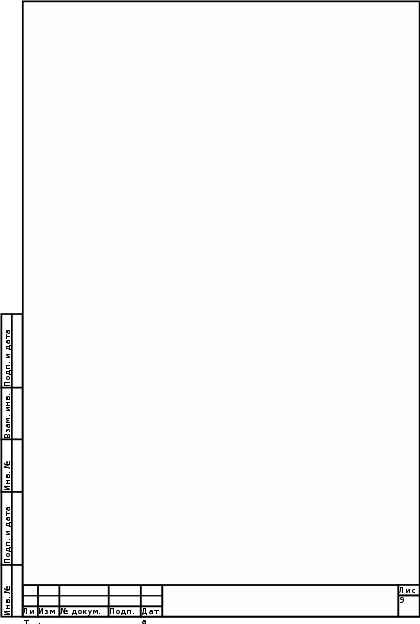
Изнашивание — процесс разрушения и отделения материала с поверхности твердого тела и (или) накопления его остаточной деформации при трении, проявляющийся в постепенном изменении размеров и (или) формы тела. В горных машинах и оборудовании встречается несколько видов изнашивания.
Механическое — изнашивание в результате механических воздействий.
Коррозионно-механическое — изнашивание в результате механического воздействия, сопровождаемого химическим и (или) электрическим взаимодействиями материала со средой.
Абразивное — механическое изнашивание материала в основном в результате режущего или царапающего действия на него твердых частиц, находящихся в свободном или закрепленном состоянии.
Эрозионное — механическое изнашивание в результате воздействия потока жидкости и (или) газа.
Гидроабразивное (газообразивное) — абразивное изнашивание в результате действия твердых частиц, взвешенных в жидкости (газе) и перемещающихся относительно изнашивающихся тел.
Усталостное — механическое изнашивание в результате усталостного разрушения при твердом деформировании микрообъемов материала поверхностного слоя.
Изнашивание при заедании — изнашивание в результате схватывания, глубинного вырывания материала, переноса его с одной поверхности трения на другую и воздействия возникающих неровностей на сопряженную поверхность.
Изнашивание при фреттинге — механическое изнашивание соприкасающихся тел при малых колебательных относительных перемещениях.
Износ детали — результат ее изнашивания.
Износ делят на моральный, обусловленный старением конструкций оборудования, и физический, связанный с длительностью и интенсивностью его использования.
Физический износ может быть нормальным (естественным) и аварийным (преждевременным). Нормальный износ происходит в результате длительной работы оборудования под действием сил трения. Аварийный износ происходит в значительно меньшие сроки и вызывается нарушением режимов работы оборудования, отсутствием смазки и неправильным ее выбором, некачественным ремонтом и несвоевременной заменой деталей, дефектами деталей (раковины, трещины и др.), усталостными явлениями в материале, неправильным монтажом оборудования и др.
Чаще всего в машинах наблюдается физический износ. Возникает он под действием сил трения и представляет собой сумму одновременно протекающих процессов истирания, смятия и окисления соприкасающихся поверхностей.
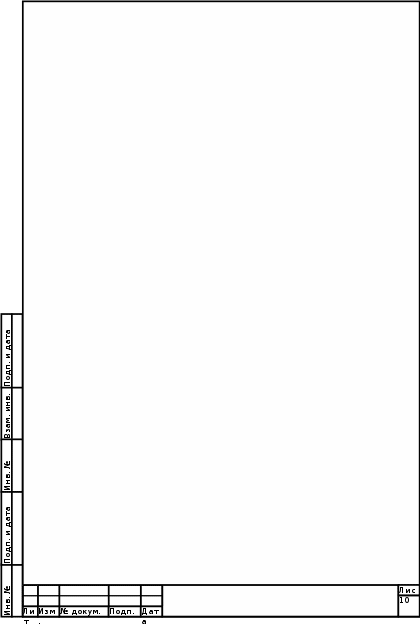
Износ может быть предельным, соответствующим предельному состоянию изнашивающегося изделия, или допустимым, при котором оно сохраняет работоспособность.
Скорость изнашивания деталей зависит от конструктивных, технологических и эксплуатационных факторов.
К конструктивным факторам относятся:
-
форма, размеры и материал сопрягаемых деталей; -
зазоры и посадки в сопряжениях; -
создание конструкций, обеспечивающих наименьший износ деталей, сборочных единиц, рациональную систему смазки;
доступность деталей, сборочных единиц для проведения технического обслуживания и ремонта.
К технологическим факторам относятся:
-
качество материала; -
механическая и термическая обработка деталей.
К эксплуатационным факторам относятся:
-
режимы работы оборудования; качество горючего и смазочных материалов; -
климатические и горно-геологические условия работы; -
качество и своевременность технического обслуживания и ремонта.
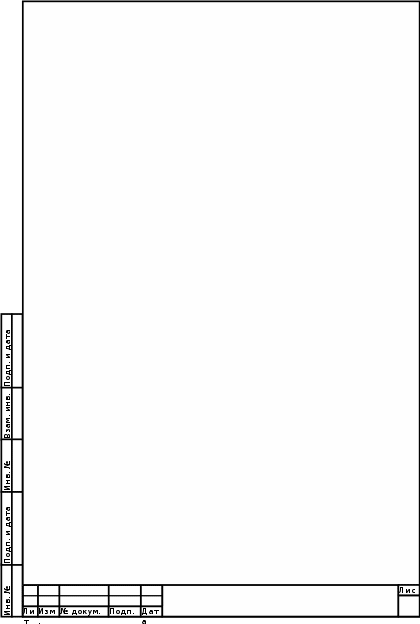
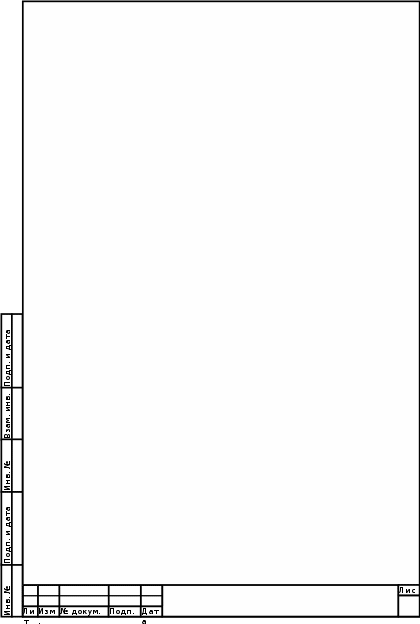
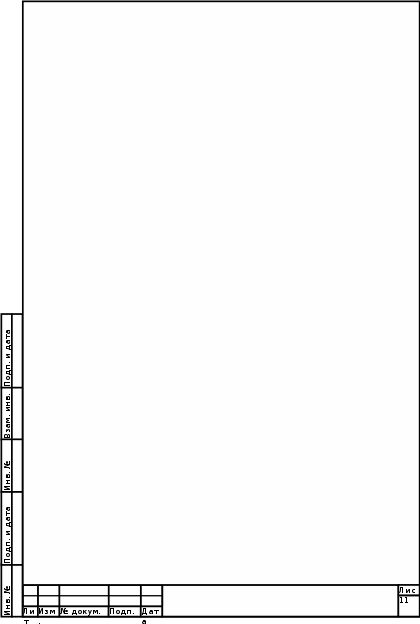
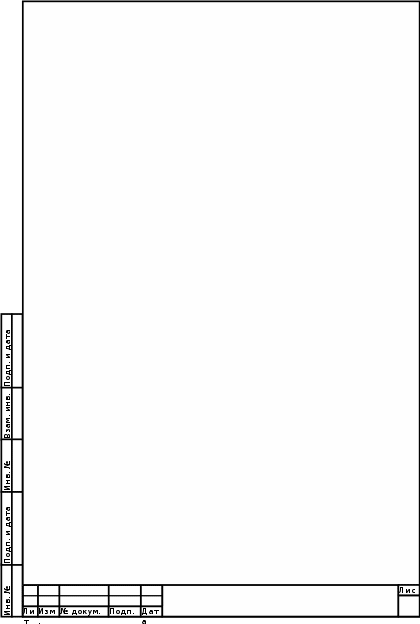
Прежде всего окорочный установка должен проходить тщательную регулировку.
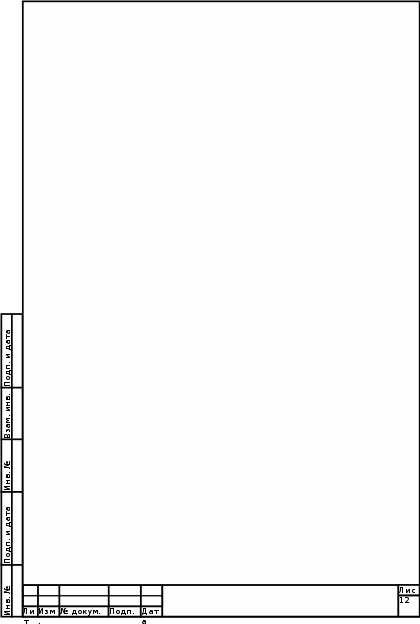