Файл: Ко второй группе относятся процессы, связанные с обработкой жидких сред.docx
Добавлен: 02.12.2023
Просмотров: 99
Скачиваний: 2
ВНИМАНИЕ! Если данный файл нарушает Ваши авторские права, то обязательно сообщите нам.
5. Регулировка тепловых циклов лазерного излучения позволяет влиять и контролировать микроструктуру получаемых сварных соединений, в том числе используя легирующие добавки в расплав.
2. Волноводы
Д16 - это сплав алюминия с магнием и медью. Такие сплавы именуются дюралями, а дюрали применяются в качестве конструкционных сплавов в авиационной и космической промышленности, благодаря их прочности и относительной лёгкости. Продажа алюминиевого проката.
В чистом виде Д16 применяется редко, так как в не закалённом состоянии обладает меньшей прочностью и твёрдостью, чем АМг6 и в то же время уступает ему по коррозионной стойкости и свариваемости. Но детали из Д16 с поперечным сечением не более 100-120 мм можно закалить и состарить уже после их изготовления. В большинстве же случаев в продаже присутствуют уже упроченные и состаренные естественным методом полуфабрикаты, маркируемые Д16Т.
Сплав классифицируется как прочный термоупрочняемый, но не предназначен для сварки. Однако, его можно сваривать точечной сваркой, хотя в большинстве случаев детали из него закрепляются с помощью креплений. Также из Д16 могут изготавливать и сами крепления в виде заклёпок с антикоррозионным покрытием. Сплав легко обрабатывается резанием.
Д16Т - это конструкционный термоупроченный и естественно состаренный сплав в заготовке, который применяется в различных областях народного хозяйства.
Его применяют и для изготовления силовых элементов конструкций в авиатехнике: деталей обшивки, каркаса, шпангоутов, нервюр, тяги управления, лонжерон.
Также из него выпускают и детали, работающие при температуре в пределах 120-230 ° C — по ГОСТу.
Он применяется и в автомобильной промышленности для изготовления кузовов, труб и других достаточно прочных деталей.
Д16Т применяют для изготовления заклёпок с высокой прочностью на срез. Эти же заклёпки применяются для крепления других более мягких алюминиевых деталей, например, из магналий АМг6.
Волновод – это специальный канал (искусственный или естественный), который может распространять волны и способный поддерживать их частоту.
Одно из набирающих обороты направлений использования волноводов является ультразвуковая сварка, которая позволяет с помощью специальной установки на базе магнитостриктора проводить сваривание изделий из пластмассы и полимеров.
На базе Государственных Университетов в лабораториях ведется работа по изучению различных волноводов, которые отличаются друг от друга не только формой и материалами, но и областями их применения.
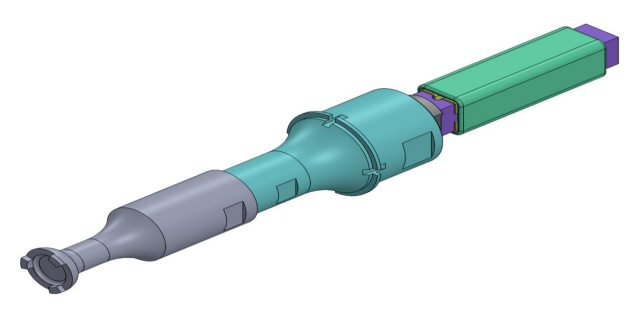
Рисунок 1 – Общий вид ультразвуковой колебательной системы
Вся УЗКС состоит из нескольких частей: магнитостриктор на котором находится обмотка подмагничивания, специальный переходник, который имеет стандартную длину в 10 мм, и сам волновод или же бустер. Бустер в свою очередь это амплитудный преобразователь. Он представляет ключевой элемент резонансной структуры. Служит для увеличения или снижения амплитуды колебаний преобразователя и передаёт их волноводу. Сама амплитуда меняется в зависимости от характеристик заготовки. На рисунках 2 и 3 представлены волноводы из алюминиевого сплава Д16Т.
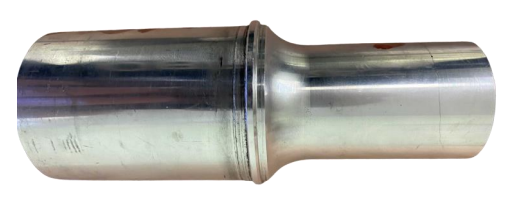
Рисунок 2 – Волновод из алюминиевого сплава Д16Т
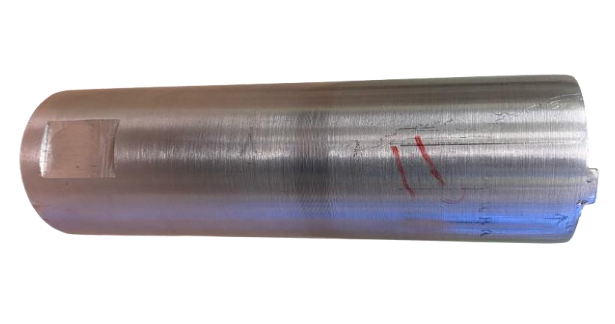
Рисунок 3 – Волновод из алюминиевого сплава Д16Т
Материалы, из которых изготавливаются волноводы довольно разные, но наиболее известны те, который изготавливаются из алюминиевых и титановых сплавов. Каждый из материалов по-своему хорош, но каждый из них имеет плюсы по сравнению с другим в отдельных моментах.
3. Материал и методики исследования
В качестве материала ультразвуковых волноводов был использован титановый сплав Д16Т (90,9-94,7 % А1; до 3,8-4,9 % Сu; 1,2-1,8 % Мg; 0,3-0,9 % Mn; до 0,5 % Fe; до 0,5 % Si; 0,25 % Zn; до 0,15 % Ti) в деформированном и литом состояниях.
Первоначально из общего списка предложенных волноводов мы выбрали несколько образцов из сплава Д16Т
Рисунок 4 – Выбранные образцы из сплава Д16Т
Общий вид волновода 1 с трещиной представлен на рисунке 5. После вскрытия трещины обнаружен излом, состоящий из нескольких отдельных фрагментах усталостного разрушения. Причем данные фрагменты расположены на разном уровне, а очаг зарождения трещины находится не только на поверхности волновода (у резьбы), но и внутри волновода.
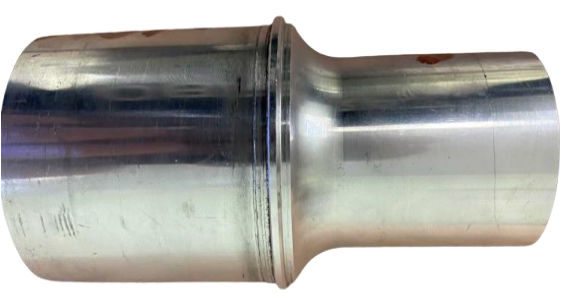
Рисунок 5 – Общий вид волновода 1
Усталостное разрушение волноводов под действием ультразвуковых колебаний можно рассматривать как мегацикловую усталость. Зарождение трещины при мегацикловой усталости происходит у дефектов металла (микропоры, неметаллические включения и так далее).
Отсюда следует вывод: к металлу, из которого изготовляют ультразвуковые волноводы должны быть предъявлены повышенные требования к качеству и чистоте металла.
Микрорельеф поверхности усталостных участков излома между макрополосами состоит из сравнительно малорельефных участков и бороздок, в основном расположенных параллельно направлению расположения усталостной трещины. Это вызывает сомнение, что они отражают положение фронта трещины за каждый цикл нагружения.
Обнаружен необычный микрорельеф поверхности усталостных изломов волноводов из алюминиевого сплава Д16Т (волновод №1), состоящий из полос, напоминающих усталостные бороздки, расположенных параллельно фронту распространения усталостной трещины. Между такими полосами и перпендикулярно к ним располагаются мелкие бороздки. Природу формирования такого микрорельефа еще предстоит выяснить.
Общий вид волновода 2 с обнаруженной трещиной представлен на рисунке 6. Участок с трещиной выделен синим цветом. После вскрытия трещины можно наблюдать излом. Как видно из рисунка 6, излом является усталостным. Очаг зарождения усталостной трещины находится под поверхностью волновода, о чем свидетельствуют концентрические макрополосы на поверхности излома. Направление распространения усталостной трещины показано красной стрелкой.
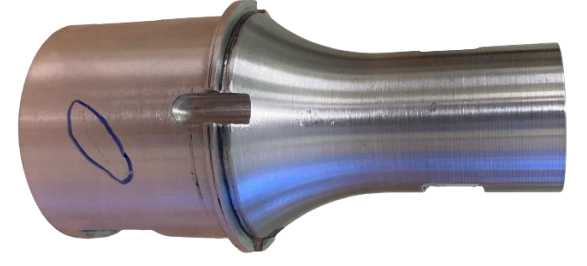
Рисунок 6 – Общий вид волновода 2 с трещиной
Вблизи очага зарождения усталостной трещины имеет место своеобразный микрорельеф, состоящий из полос, напоминающих усталостные бороздки, расположенных параллельно фронту распространения усталостной трещины. Между такими полосами и перпендикулярно к ним располагаются мелкие бороздки.
Усталостное разрушение волноводов из алюминиевого сплава Д16 в состоянии Т3 под действием ультразвуковых колебаний можно рассматривать как мегацикловую усталость. Зарождение трещины при мегацикловой усталости происходит исключительно у дефектов металла, а именно микропоры, неметаллические включения и так далее. Отсюда следует вывод о том, что к металлу, из которого изготовляют ультразвуковые колебательные системы и волноводы, которые применяются при ультразвуковой сварке в условиях массового производства должны быть предъявлены повышенные требования контроля к качеству и чистоте металла. Так как, известно, что зарождение трещины при мегацикловой усталости под действием ультразвуковых колебаний происходит у дефектов металла, а именно были обнаружены неметаллические включения в микроструктуре алюминиевого сплава Д16Т.
4. Способы упрочнения сплава Д16Т
1. Перед проведением работы включить печи и довести температуру нагрева в печи под закалку до 500 o C, а в печах для старения до 100, 200, 250 o C.
2. В печь под закалку заложить на поддоне 12 образцов сплава Д16 (1160). После 40. 50-минутной выдержки провести закалку всех образцов воде, обеспечив ускоренное перенесение образцов в закалочный бак и энергичное перемешивание воды.
3. Измерить твердость по шкале HRB оттоженного образца и 12 закаленных образцов. Перед измерением твердости зачистить торцевые поверхности образцов на наждачной бумаге. Объединить закаленные образцы по 4 штуки с приблизительно одинаковой твердостью.
4. Провести искусственное старение при температурах 100, 200, 250 o С. Заложить в соответствующую печь по 4 образца. Провести отбор образцов после 5-, 10-, 20- и 30-минутной выдержки. После остывания образцы зачистить на наждачной бумаге, измерить их твердость по шкале HRB.
Алюминиевые сплавы, имеющие переменную растворимость компонентов в твердом состоянии, можно упрочнить термической обработкой, состоящей из закалки и старения.
Цель закалки - получить в сплаве предельно неравновесное фазовое состояние - пересыщенный твердый раствор с максимально возможным содержанием легирующих элементов. Такое состояние обеспечивает, с одной стороны, повышение (по сравнению с равновесным состоянием после отжига) твердости и прочности при сохранении пластичности, а с другой - возможность дальнейшего упрочнения при старении.
Высокая пластичность сплавов после закалки позволяет подвергать полуфабрикаты формоизменению с целью изготовления деталей, пока легирующие элементы находятся в твердом растворе.
При старении структура сплавов приближается к равновесной в результате распада пересыщенного твердого раствора и образования мелкодисперсных частиц. При этом повышаются твердость, прочность, снижается пластичность, возрастает сопротивление коррозии.
Из термически упрочняемых сплавов наиболее широкое применение получили дюралюмины (система легирования Al-Cu-Mg) и высокопрочные сплавы (Al-Zn-Cu-Mg).
Рассмотрим особенности упрочнения сплавов на примере дюралюминов. Термическая обработка дюралюминов основана на переменной растворимости меди и магния в алюминии. В равновесном состоянии сплавы содержат твердый раствор и включения вторичных фаз Θ (CuAl2) и S (CuAl2Mg). Количество S-фаз возрастает с увеличением содержания Mg в сплаве.
Для наглядности примем, что основной фазой в дюралюминах является Θ, и фазовые превращения будем рассматривать по двойной диаграмме Al-Cu.
Термически упрочняемыми в системе (Al-Cu) являются сплавы с содержанием меди более 0,1%, максимальная растворимость меди в алюминии при 20 о С. Растворимость меди в твердом растворе α повышается до 5,65% при температуре 548 o C (температура эвтектического превращения).
Сплавы, содержащие не более 5,65% меди, относятся к деформируемым. После отжига эти сплавы состоят из твердого раствора на основе алюминия α, содержащего 0,1% Cu, и крупных включений Θ-фазы (фаза переменного состава с 53. 55 % Cu).
Прочность сплава после отжига минимальная.
Закалка деформируемых сплавов заключается в нагреве и выдержке при температуре, когда вторичная Θ-фаза полностью растворится в твердом растворе α, и последующем быстром охлаждении до комнатой температуры (20..25 o C). В результате закалки структура, равновесная при температуре нагрева, фиксируется при температуре 20. 25 o C, так как при быстром охлаждении не происходит распад твердого раствора (выделение Θ-фазы). После закалки получается пересыщенный твердый раствор с существенно более высоким содержанием меди по сравнению с равновесной структурой (0,1% Cu). Содержание меди в пересыщенном твердом растворе соответствует ее содержанию в сплаве.
Сплавы, содержащие более 5,65% Cu, относятся к литейным. Температура нагрева под закалку этих сплавов на 5. 15 o C ниже температуры эвтектического превращения. При закалке получается пересыщенный твердый раствор с меньшей концентрацией меди, чем содержится в сплаве. При нагреве под закалку и после закалки в сплавах присутствует не растворившаяся эвтектика (α + Θ). Сохранение не растворившейся доли Θ-фазы объясняет причину уменьшения содержания меди в пересыщенном твердом растворе.
Охлаждение при закалке производится со скоростью больше критической - минимальной скорости охлаждения, при которой не происходит распад пересыщенного твердого раствора. В промышленности большинство алюминиевых сплавов при закалке охлаждают в воде с температурой до 40 o C. Скорость охлаждения тонкостенных изделий в холодной воде (600. 800 o C/c) значительно превосходит критические скорости охлаждения сплавов (10. 120 o C/c). Такие условия охлаждения обеспечивают значительную прокаливаемость. Изделия из алюминиевых сплавов прокаливаются насквозь в сечениях 120..150 мм.
Пересыщенный твердый раствор закаленного сплава отличается повышенным уровнем свободной энергии. Распад твердого раствора, происходящий при старении, приближает фазовое состояние к равновесному.