Файл: 1 Функции и структура управления буровых работ (убр). Назначение и функции отделов, инженерных служб убр самостоятельно.doc
ВУЗ: Не указан
Категория: Не указан
Дисциплина: Не указана
Добавлен: 24.10.2023
Просмотров: 281
Скачиваний: 7
ВНИМАНИЕ! Если данный файл нарушает Ваши авторские права, то обязательно сообщите нам.
- поагрегатный метод;
- мелкоблочный метод;
- крупноблочный (индустриальный) метод;
- блочно-модульный метод.
Агрегатный способ сооружения буровых характерен для первичного монтажа. Оборудование с заводов обычно поступает в виде монтажных блоков. Только отдельные блоки, габариты или масса которых не соответствует техническим условиям грузов, перевозимых по железной дороге, поставляются агрегатами. Агрегатному способу характерны следующие основные особенности. Во-первых, длительные сроки сооружения буровых из-за трудоёмкости работ, связанных с монтажом и демонтажем оборудования, строительством и разборкой буровых укрытий, сооружением фундаментов и транспортировкой оборудования и материалов Во-вторых, многократность монтажа и демонтажа оборудования приводят к преждевременному его износу, в результате чего возрастает объем ремонтных работ, нарушается комплектность оборудования отдельные агрегаты монтируют из различных комплектов с разными сроками службы. В-третьих, при этом способе значительно снижается возврат материалов из-за периодической разборки буровых укрытий и коммуникаций. Все эти недостатки агрегатного способа приводят к низкой производительности труда и высокой себестоимости сооружения буровых.
По сравнению с агрегатным, мелкоблочный способ сооружения буровых установок позволяет ликвидировать вышеперечисленные недостатки.
Мелкоблочный метод сводится к перетаскиванию оборудования мелкими блоками. Этот метод применяется в условиях лесистой или холмистой местности, а также в целях улучшения землепользования.
При мелкоблочном сооружении вся буровая установка разбивается на 12-20 блоков в зависимости от числа узлов, кинематически связанных друг с другом. Для этих узлов изготовляют основания, которые и служат фундаментом при установке на площадке, а так же транспортным средством во время монтажа при незначительном расстоянии кустовых площадок. Основным недостатком этого способа считается большая расчленённость бурового оборудования в мелкие блоки, которая полностью не обеспечивает создание кинематически увязанных обособленных рабочих узлов.
При крупноблочном методе подготовка оснований и монтаж на них оборудования осуществляется на механизированных индустриальных базах вышкомонтажных управлений, вышкомонтажных цехов или на первой буровой. В дальнейшем вышкомонтажные работы сводятся к перетаскиванию крупных блоков и их монтажу с небольшим объемом работ. При этом методе трудоемкость вышкомонтажных работ уменьшается в 7-8 раз, а себестоимость – в 2-4 раза по сравнению с мелкоблочным методом.
Крупноблочный способ сооружения буровых перед мелкоблочным способом имеет следующие преимущества: резкое сокращение числа блоков; упрощение конструкции фундаментов; снижение за счёт этого объёма строительно-монтажных работ и сокращение сроков сооружения буровых; увеличение скорости транспортировки блоков и повышение срока службы оборудования и оснований в связи с транспортировкой их на гусеничных тяжеловозах и тяжеловозах на пневмоколесном ходу; экономия строительных материалов в результате повышения при демонтаже возврата леса, мягкой кровли и других материалов. При крупноблочном способе оборудование монтируется на двух - шести блочных основаниях, которые перевозятся на специальных транспортных средствах - тяжеловозах. Общая эффективность крупноблочного способа сооружения буровых зависит от объёмов буровых работ блоков, наличие естественных и искусственных препятствий на пути транспортировки. Большая эффективность при крупноблочном способе достигается на эксплуатационных площадках с большим объёмом буровых работ, небольшими сроками бурения скважин и расстояниями между ними, с открытым непересечённым рельефом. Эффективность крупноблочного способа снижается при транспортировке блоков на большие расстояния (особенно на лесистой, болотистой и пересечённой местности), так как в этих условиях приходится выполнять много работ по подготовке трасс. В этих случаях выгоднее оборудование полностью демонтировать, разобрать основание на мелкие секции и перевезти их на автомобильном транспорте.
Модульный способ монтажа предусматривает специальное конструктивное построение буровой установки. При этом буровая установка, включая и металлоконструкции подвышенного основания и рабочей буровой площадки, состоит из модулей полной заводской готовности, т. е. с установленными, отрегулированными и испытанными на предприятии- изготовителе узлами и механизмами, включая все их системы (охлаждения, смазки, обогрева, освещения, управления и т. д.). При этом способе практически исключаются операции по сборке каркасов при монтаже укрытий и элементов утепления. Модули соединяются друг с другом и с внешними коммуникациями (электрокабелями, трубопроводами подвода воздуха, воды, пара и т. п.), быстроразъемными соединениями. При этом время «первичного» монтажа или монтажа оборудования, поступившего на промысел непосредственно с предприятия-изготовителя, уменьшается кратно, а время «вторичных» монтажей сравнимо с крупноблочным способом, но лишено всех вышеперечисленных недостатков.
Монтаж и транспортировка модульной буровой установки осуществляются стандартной крановой и автомобильной техникой, соответствующей грузоподъемности по обычным автомобильным или промысловым дорогам.
6.1 Приспособления для обеспечения точности монтажа агрегатов
Комплект приспособлений для обеспечения точности монтажа кинематически связанных агрегатов предназначен для монтажа узлов агрегатов и блоков буровой установки, проверки центровки агрегатов, а также для проверки при эксплуатации.
Приспособление для центровки валов предназначено для проверки положения валов механизмов, между которыми устанавливаются карданные валы. Устройство его следующее: в направляющих штатива 5 установлена штанга 4. Во втулке штанги 4 установлен движок 3. Штанга 4 и движок 3 могут перемещаться вдоль своих осей. Взаимное движение штанги 4 и движка фиксируется винтами. В головке движка установлены болты 2 с контргайками. Приспособление присоединяется к валу при помощи болтов 7 с гайками. При установке приспособление должно быть ориентировано движком 3 в сторону вала, установленного в эксцентриковом стакане. Проверка центровки производится осторожным проворачиванием вала. Задевание болтов о поверхность стакана недопустимо.
12 3 4 5 6 7 8 9
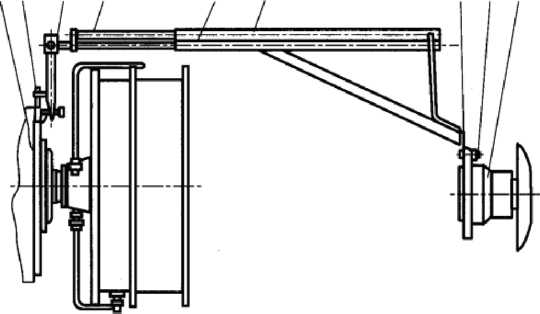
Рисунок 4 - Приспособление для центровки валов: 1, 9 — центрируемые валы; 2 — болт; 3 — движок; 4 — штанга; 5 — штатив; 6 — ребра жёсткости; 7 — болт; 8 — гайка
Приспособление для выверки торцов звездочек предназначено для проверки правильности установки звездочек цепных передач. Звездочки должны находиться в одной плоскости. Сварные кронштейны устанавливают на звездочках при помощи болтов. В кронштейны ввернуты специальные болты 5, имеющие проточку, через которую натягивается струна 6 при помощи грузов. Установка звездочек считается удовлетворительной, если по всей поверхности торцов А звездочек струна, находясь в зазоре мерного платика
7, не касается платика звездочки, т. е. ни один из размеров Б или В не равен нулю.
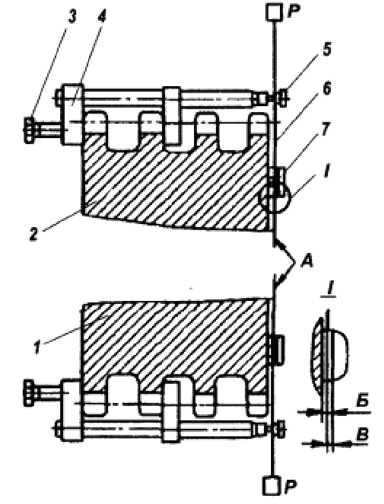
Рисунок 5 - Приспособление для выверки торцов звёздочек: 1, 2 — звёздочки; 3, 5 — болты; 4 — кронштейн; 6 — струна; 7 — мерный платик
Штихмас служит для установки межцентрового расстояния между валами. Он устанавливается во впадины шкивов или зубьев до соприкосновения с ними. Необходимое межцентровое расстояние устанавливается перемещением агрегатов и контролируется по провисанию цепи. Штихмас 2 может быть индивидуальным, т. е. предназначенным для контроля между определенными агрегатами, или раздвижным, когда необходимо знать расстояние между впадинами шкивов или зубьев 1 и 3.
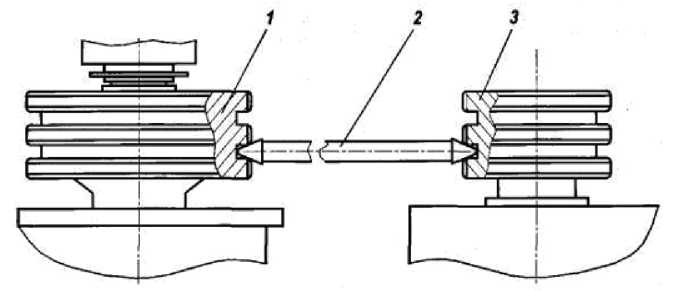
Рисунок 6 - Схема контроля межцентрового положения с помощью штихмаса: 1, 3 — шкивы (зубья); 2 — штихмас
Для стяжки цепей без перемещения агрегатов применяется специальное приспособление.
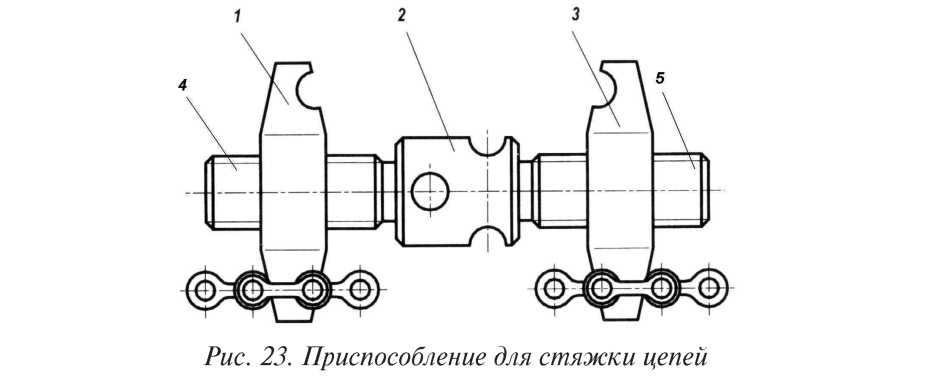
Рисунок 7– Приспособление для стяжки цепей
Ролик обводной применяется для изменения направления ходового каната при подъеме вышки или погрузке и выгрузке оборудования с передвижной платформы. Ролик обводной состоит из серьги 1, имеющей с двух сторон проушины. Одной проушиной серьга крепится к основанию вышечного блока при помощи оси 5. В другой проушине на оси 5 установлен ролик 2 с запрессованной бронзовой втулкой. Ось 5 удерживается от выпадения чекой 4 со шплинтом 3. Ролик рассчитан на максимальное усилие каната (150 кН).
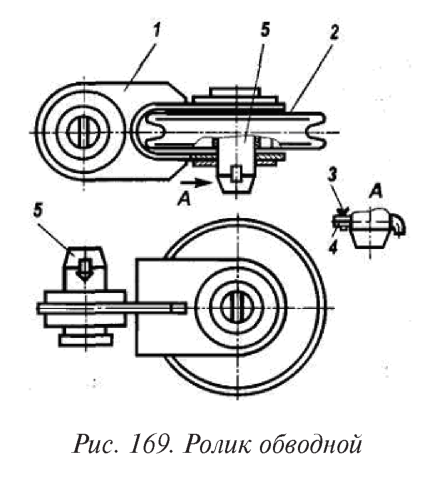
Рисунок 8 – Ролик обводной
Приспособление для центровки пальцевой муфты состоит из планки 3 с установленными в ней болтом 4 с гайкой 5. К полумуфте 2 приспособление крепится штатным болтом. Проверка центровки проводится вращением полумуфты 2 относительно полумуфты 1. Точность центровки: разность а по всему периметру должна быть не более 0,4 мм, а b — не более 0,5 мм.
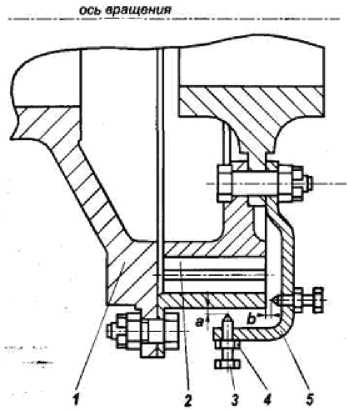
Рисунок 9- Приспособление для центровки пальцевой муфты
Приспособление для проверки параллельности осей валов состоит из двух кронштейнов 2, крепящихся к фланцам валов проверяемых узлов болтом 4. Замером расстояний между фиксированными точками проверяется параллельность валов (см. схему замеров). Максимальная разность замеров не должна превышать 5 мм.
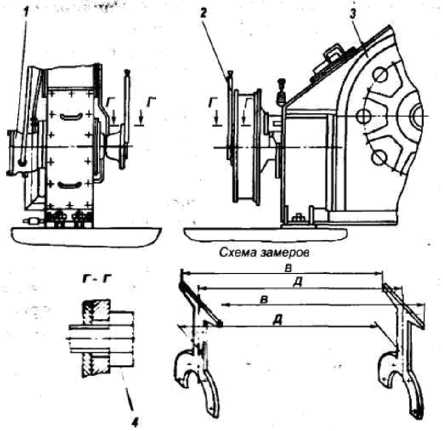
Рисунок 10 - Приспособление для проверки параллельности валов: 1 — вал передачи; 2 — кронштейн; 3 — коробка перемены передач; 4 — болт
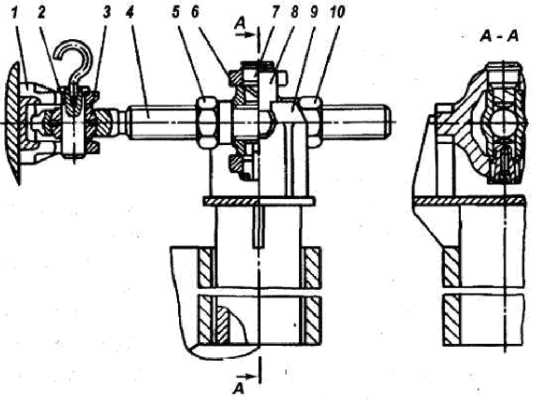
Рисунок 11 - Приспособление для центровки агрегатов: 1 — проушина; 2 — ось; 3 — опора шаровая; 4 — винт; 5,10 — гайки; 6— крестовина; 7, 8 — пробка; 9 — упор
Приспособление для центровки агрегатов предназначено для проверки соосности секций и агрегатов, установленных на этих секциях (насосы, лебедки, коробки скоростей). При центровке винт в сборе с траверсой устанавливается в пазы упора 9. Вывинчивая винт 4 из гаики, совмещаются отверстия в винте, шаровой опоре 3 и проушине 7, после чего вставляется ось 2. Центровка проводится навинчиванием одной из гаек 5 или 10, при этом другая из них не должна упираться в крестовину 6. Данное приспособление съемное и используется для центровки всех секций и агрегатов. При хранении и перед использованием его необходимо смазывать.

Рисунок 12 – Гидростатический нивелир
Гидростатический нивелир предназначен для установки направляющих рельсов горизонтально относительно друг друга. Рельсы устанавливают следующим образом. Один из сосудов устанавливают на головке рельса, а другой - на расстояние допуска и проверяют уровень жидкости в обоих сосудах. Разность уровней должна быть в пределах допуска на единицу длины. Аналогично определяют расположение рельсов в одной плоскости.
Для нивелирования различных буровых сооружений относительно друг друга и к горизонту могут применяться также оптические нивелиры.
1 2 3 4 5 6