Файл: 1. Характеристика объекта проектирования. Характеристика производственной зоны и средств механизации на объекте проектирования.docx
ВУЗ: Не указан
Категория: Не указан
Дисциплина: Не указана
Добавлен: 24.10.2023
Просмотров: 61
Скачиваний: 2
ВНИМАНИЕ! Если данный файл нарушает Ваши авторские права, то обязательно сообщите нам.
1.Характеристика объекта проектирования.
1.1.Характеристика производственной зоны и средств механизации на объекте проектирования.
Цех металлорежущих станков предназначен для резки металла разной формы и величины, так же изготовляет серийные детали под заказ.
В цеху находиться очень большое и различное оборудование, если посмотреть на план цеха, то можно увидеть станки для заточки, резьбошлифовальные и металлорежущие.
На производстве организованы не только рабочие помещения, но и для отдыха персонала, есть столовая зона, зона переодевания персонала, так есть и туалет, бытовая комната с инструментами, кладовая с запчастями для станков и дополнительным оборудование для персонала.
Размер цеха составляет 1500 кв.м, длина цеха 50м, ширина 30м. Сам же цех делиться на несколько помещений разной формы, есть 2 основных по 576 кв.м, бытовка, комната с инструментами, склад и прочее по 24 кв.м, а вот резьбошлифовальная комната занимает уже 36 кв.м. А так же все помещения кроме станочного помещения отделения, двухэтажные высотой 3,6м. Сам же цех в свою очередь сделан из блок-секции, длинна каждой такой секции от 6-8 метров.
Грунт в районе цеха состоит полностью из глины.
Количество рабочих смен на производстве равно трем так как каждая смена работает по 8 часов в день, это обеспечивает беспрерывную работу всего производства. Начало первой смены начинается в 0.00, а заканчивается в 8.00, вторая смена выходит в 8.00, заканчивает в 16.00, третья смена начинает в 16.00, заканчивает в 24.00.
На производстве класс пожар опасности категории Г, причина этого что данное производство не работает с негорючими материалами, но одновременно с веществами, которыми нагреваться в процессе работы.
На рабочих местах освещение искусственного типа, которое относиться к общему освещению, освещение работает таким образом, что его хватает для всех нужд, так же в каждой закрытой комнате есть свою собственное освещение. Авариное освещение тоже есть на производстве, включается только когда происходят аварийные ситуации на производстве или в цеху.
Перемещение грузов внутри помещения производиться несколькими способами, кран-балкой для больших, тяжёлых и не габаритных деталей, конструкции. А вот для более легких, не крупных деталей используют электротележки.
1.2 Оценка уровня электрификации и автоматизации на объекте проектирования
Трансформаторная подстанция питающая цех, находиться внутри производства, питающаяся от главной трансформаторной подстанции находящаяся на расстоянии 1.3 км.
На первичной обмотке трансформатора 10 кВ, на вторичные обмотки стандартное напряжение 0,4 кВ.
Категорию надежности электроснабжения объекта составляет 3 категория, так как на производстве отсутствуют установки которые нельзя выключать, количество человек которое работает на самом производстве одновременно меньше 50.
На производстве способ укладки питающих производств выполнен в нишах, стенах, на потолке, в трубах.
Главными условиями прокладки питающих сетей являться простота и экономность прокладки их на производстве, а также отсутствие перегрузок из-за этого тут используют прокладку магистральные схему подключения. Ее используют из-за того, что такой способ удобен для больших нагрузок и более правильного распределения ЭЭ на производстве.
Электроустановки на производстве питаются напряжением в 400В.
Применяемое заземление на производстве TN-S, данная система заземления более безопасная чем остальные, так как разделение рабочей (N) и защитного (PE) ноля реализовано сразу на подстанции, что в свою очередь дает более надёжную безопасность персонала и станков.
Таблица 1Перечень оборудования цеха
№ | Наименование оборудования | Кол-во, шт | Pном, кВт | Ku | Cos ![]() | tg ![]() |
1 | Электропривод раздвижных ворот | 1 | 4,5 | 0,12 | 0,5 | 1,73 |
2 | Универсальные заточные станки | 3 | 2,8 | 0,12 | 0,5 | 1,73 |
3 | Заточные станки для фрезерных головок | 2 | 4,2 | 0,12 | 0,5 | 1,73 |
4 | Круглошлифовальные станки | 3 | 10 | 0,12 | 0,5 | 1,73 |
5 | Токарные станки | 3 | 7,8 | 0,12 | 0,5 | 1,73 |
6 | Вентиляторы | 3 | 5 | 0,6 | 0,8 | 0,75 |
7 | Плоскошлифовальные станки | 6 | 18,5 | 0,12 | 0,5 | 1,73 |
8 | Внутришлифовальные станки | 4 | 12 | 0,12 | 0,5 | 1,73 |
9 | Кран-балка | 1 | 15 | 0,6 | 0,8 | 0,75 |
10 | Заточные станки | 4 | 3,2 | 0,12 | 0,5 | 1,73 |
2.Расчетно-конструктивная часть проекта
2.1.Расчет электрических нагрузок

где Р-мощность электродвигателя



3.Для каждого электроприемника определяют коэффициент использования Ки и коэффициент мощности cosφ (определяется по учебнику Коноваловой с 82 табл. 2.1 и заполняется таблица 1).
4.По коэффициенту мощностиcosφ определяют реактивный коэффициент мощности по формуле:
tgφ= tg(arccosφ) (2)
5.Определяем общее количество электроприемников в группе и суммарную мощность группы электроприемников
6.Для каждой группы однородных электроприемников определяют среднюю активную и реактивную нагрузку за наиболее нагруженную схему
tgφ= 1,38771(arccosφ)



Ки-коэффициент использования.






7.Для узла присоединения суммируют активные и реактивные составляющие мощностей





(6)



8.Определяем средне взвешенное значение коэффициента использования узла
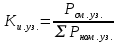



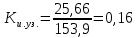
9.Определяем среднее значение реактивного коэффициента мощности узла по формуле:



10.Определяют силовой показатель в группе электроприемников.




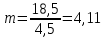
11.По одному из определения способов определяют эффективное число электро приемников в группе (Шеховцовс.25 табл.1.5.2)

Под эффективным числом принимают такое число однородных по режиму работы электро приемников одинаковой мощности, которая обеспечивает тот же расчетный максимум что и группа различных по мощности и режиму работы электро приемников.

12.Определение коэффициента максимума (Шехавцов с.26 табл.1.5.3)


13.Определить расчетную максимальную нагрузку

Где


14.Определить расчетную реактивную мощность

Где





15.Определить расчетную полную мощность




16.Определить расчетный ток





Таблица 2 «Расчет электрических нагрузок цеха»

2.2Расчет компенсирующих устройств
Правильная компенсация позволяет:
-
снизить общие расходы на электроэнергию; -
уменьшить нагрузку элементов распределительной сети (подводящих линий, трансформаторов и распределительных устройств), тем самым продлевая их срок службы; -
снизить тепловые потери тока и расходы на электроэнергию; -
снизить влияние высших гармоник; -
подавить сетевые помехи, снизить не симметрию фаз; -
добиться большей надежности и экономичности распределительных сетей.