Файл: Отчет по производственной практике по учебному курсу.docx
Добавлен: 25.10.2023
Просмотров: 252
Скачиваний: 6
ВНИМАНИЕ! Если данный файл нарушает Ваши авторские права, то обязательно сообщите нам.
Например, с применением металлорежущих станков с числовым программным управлением значительно уменьшает основное и вспомогательное время, также уменьшает число самих операций.
Заводской технологический процесс в значительной степени проигрывает с разработанным мною технологическим процессом.
2. ПРОЕКТИРОВАНИЕ ТЕХНОЛОГИЧЕСКОЙ ОСНАСТКИ
2.1 ПРОЕКТИРОВАНИЕ САНОЧНОГО ПРИСПОСОБЛЕНИЯ
Трехкулачковый самоцентрирующийся патрон выполняется со спирально-реечным механизмом и ключевым зажимом.
Проектирование 3-х кулачкового патрона ведем по наиболее нагруженному черновому переходу. Для него имеем: наружный диаметр обрабатываемой поверхности 45 мм (Dоп = 32 мм), диаметр заготовки Dп.к = 150 мм; длина заготовки Lз = 91 мм; глубина резания t =2,2 мм; подача Sст = 0,35 мм/об; частота вращения шпинделя станка n = 500 об/мин; скорость резания V=0,8 м/с; патрон 3-х кулачковый с рычажным перемещением кулачков, осуществляемый зажим от пневматического цилиндра.
Определяем силу резания Pz ,Н, на данной операции [11, с.47]:
Pz = Sур Cp txp kпр
где Ср – коэффициент силы резания; Ср = 300;
хр, yр, пр – показатели степени для тангенсальной силы резания Pz
Коэффициенты, входящие формулу силы резания определяются по [11 табл. 22 с. 273-3] и составляют xp = 1; yp = 0.75; np = -0.15
Pz = 300 3,2 0,35 0,75 6,06-0,15 = 333,4 Н
Определяем поправочный коэффициент Kp
Kp = KMp Kp Kp Krp Kp
где KMp – коэффициент, учитывающий влияние механических свойств конструкционных сталей на силы резания.
KMp = (в/75) пр = (600/75) 0,75 = 4,85
где в - временное сопротивление разрыву, Н/мм2. Для стали 35 в = 600 н/мм2;
Kp Kp Krp Kp – поправочные коэффициенты, учитывающие влияние геометрических параметров режущей части инструмента на составляющие силы резания, при обработке алюминия
Kp = 1;
Kp = 1;
Krp = 1
Kp = 1,25;
Кр=4.85 1 1.25 1 1 = 6.06.
Определяем коэффициент запаса Кзап для 3-х кулачкового патрона с пневматическим приводом зажима [2 , с 107]
Кзап = К0 К1 К2 К3 К4 К5 К6
где к0 – гарантированный коэффициент запаса при всех случаях обработки;
к1… к6 – коэффициент запаса
Кзап = 1,5 1 1,2 1,2 1 1 1,5 = 3,24
Определим силу зажима детали одним кулачком патрона Wk,Н [5,c.150]
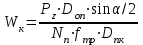
где Nn – 3 число кулачков в патроне, шт;
f Tn – 0,8 – коэффициент трения на рабочих поверхностях кулачков (с зубьями параллельно оси патрона)
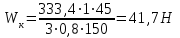
Определим силу Q ,Н, на штоке механизированного привода 3-х кулачкового патрона [11. с 49]
Qшт = Wk nk Kтр (1 + 3 ак/ nк f к ) L1 / Lk
где Ктр = 1,05 – коэффициент, учитывающий дополнительные силы трения в патроне,
ак = 40 мм – вылет кулачка от середины его опоры в пазу патрона до центра приложения силы зажима на одном кулачке;
nк – 105мм – длина направляющей части кулачка;
fк = 0,1 – коэффициент трения кулачка;
L1 и Lк – размеры короткого и длинного плеч двухплечевого рычага (конструктивно L1 = 20мм, Lк = 100 мм до оси штока).
Qшт = 41,741,05 (1 + 3 40/105 0,1) = 295,7 Н.
Определим диаметр поршня цилиндра и выберем ближайший большой стандартный размер пневматического цилиндра Dц,мм
Dц = 1,44 Qшт/р
где р = 039 Мн/м – давление сжатого воздуха
Dц = 1,44 29,57/0,39 = 12,54 мм
Принимаем диаметр пневмо – цилиндра Dц = 200 мм.
Определим действительную силу зажима

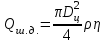
где - коэффициент полезного действия, = 0,85,

Определим время срабатывания пневмоцилиндра.
Тс = Dц Lx/d2в Vв
где Lx – длина хода поршня, см (для диаметра Dв = 20мм, Lx = 35мм); (рекомендуется dв = 8… 10мм),
вd = 10мм;
Vв = скорость перемещения сжатого воздуха, см/с (Vв = 1500 2600 см/с);
Тс = 0,25 3,5 /12 2000 = 0,0035с
принимаем Vв = 2000 см/с.
Заключение
В процессе прохождения практики изучены материалы по проектированию участка и разработки технологического процесса изготовления детали.
В отчете приведен анализ технологичности конструкции детали, даны сравнительные характеристики при выборе способа получения заготовки и ее экономическое обоснование.
Анализируя базовый технологический процесс, следует указать ряд его существенных недостатков.
Во-первых: это метод получения заготовки – прокат. Технико-экономические расчеты показали, что заготовка, полученная методом КГШП, более экономична по использованию материала и по себестоимости, чем заготовка, полученная из проката.
Анализ операций механической обработки позволяет сделать следующие выводы:
- во-первых, для сокращения вспомогательного времени на установку заготовки следует предусмотреть элементы автоматизации;
- во-вторых, заменить универсальное, неавтоматизированное оборудование токарных операций на станки с ЧПУ.
Окончательно разработанный технологический процесс механической обработки вала-шестерни будет представлен в маршрутных и маршрутно-операционных картах, в приложении к дипломному проекту. Наладки операций нового технологического процесса будут даны в графической части дипломного проекта.
СПИСОК ЛИТЕРАТУРЫ
1. Методические указания для учащихся средних специальных заведений «Курсовое проектирование по предмету «технология машиностроения» часть 1 приложения, Днепропетровск, 1990 г.;
2. ГОСТ 2009–55 – припуски и отклонения на механическую обработку отливок;
3. Горбацевич А.Ф., «Курсовое проектирование по технологии машиностроения». Минск, «Высшая школа», 1975 г., 285с.;
4. ГОСТ 7505–55 – припуски и отклонения на механическую обработку поковок и штамповок;
5. Косилова А.Г., Мещеряков Р.К. “Справочник технолога-машиностроителя”, М.: Машиностроение, 1985. 496 с. Том 1;
6. Косилова А.Г., Мещеряков Р.К. “Справочник технолога-машиностроителя”, М.: Машиностроение, 1985. 496с. Том 2;
7. ГОСТ 9324–80 – Фрезы червячные чистовые однозаходные для цилиндрических зубчатых колес с эвольвентным профилем;
8. Нефедов Н.А., Осипов К.А. Сборник задач и примеров по резанию металлов и режущему инструменту: Учебное пособие для техникумов по предмету «Основы учения о резании металлов и режущий инструмент». – 5-е изд., перераб. и доп. – М.: Машиностроение 1990., 448 с.;
9. Медовой И.А., Уманский Я.Г., Журавлев Н.М. «Исполнительные размеры калибров: Справочник» – М.: Машиностроение, 1980. – 384 с.;
10. Методические указания для учащихся средних специальных заведений «Курсовое проектирование по предмету «технология машиностроения» часть 2 приложения, Днепропетровск, 1990 г.
Приложение 1
МИНИСТЕРСТВО НАУКИ И ВЫСШЕГО ОБРАЗОВАНИЯ РОССИЙСКОЙ ФЕДЕРАЦИИ
федеральное государственное бюджетное образовательное учреждение
высшего образования
«Тольяттинский государственный университет»
__________________________
(Наименование института)
_______________________________________________________________________________________________
(Наименование кафедры, центра, департамента)
АКТ о прохождении практики
Данным актом подтверждается, что
ОБУЧАЮЩИЙСЯ ___________________________________________________
(И.О. Фамилия)
НАПРАВЛЕНИЕ ПОДГОТОВКИ
(СПЕЦИАЛЬНОСТЬ)____________________________________________
ГРУППА ___________
Проходил __________________________________________________
___________________________________________________________
(Наименование практики)
-
__________________________________________________________
(Наименование организации)
-
период с_____________________по _______________________ г.
Руководитель практики от организации (предприятия, учреждения, сообщества):
____________________________________________________________________
(фамилия, имя, отчество, должность)
РЕКОМЕНДУЕМАЯ ОЦЕНКА __________________________
__________________
________________
(дата)
М.П.
(подпись)