ВУЗ: Не указан
Категория: Не указан
Дисциплина: Не указана
Добавлен: 25.10.2023
Просмотров: 128
Скачиваний: 4
ВНИМАНИЕ! Если данный файл нарушает Ваши авторские права, то обязательно сообщите нам.
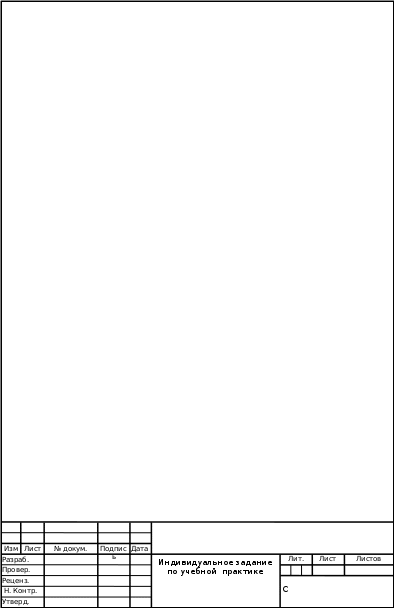
СОДЕРЖАНИЕ
| Введение | 9 | |
| 1.1 Подготовка проводов к монтажу | 11 | |
| 1.2 Соединение алюминиевых и медных проводов скруткой, | | |
внахлест, встык, желобком, косичкой, бандажное соединение | 16 | ||
| 1.3 Оконцевание проводов, наконечники, клемники и зажимы | 23 | |
| Заключение | 36 | |
| Литература | 37 |
ВВЕДЕНИЕ
За последние годы в организации и управлении производственной эксплуатацией и ремонтом оборудования на предприятиях, особенно промышленных, произошли коренные изменения. Одновременно с сокращением большинства промышленных министерств ликвидированы общеотраслевые и общесоюзные ремонтные организации (ремонтные объединения, тресты и т.д.), осуществлявшие централизацию ремонта основного энергетического оборудования. Упразднено централизованное обеспечение предприятий оборудованием, ремонтными материалами, запчастями и ремонтной оснасткой. Перестали существовать отраслевые управления главного механика и главного энергетика, осуществлявшие координацию ремонта оборудования в рамках отраслей. Большая часть энергетического оборудования (до 60 %) исчерпала свой амортизационный срок, требует замены или восстановительного капитального ремонта.
При всех недостатках и трудностях сегодняшнего времени можно быть уверенным в том, что многие организационные и технологические решения, давно научно обоснованные и поддержанные многими руководителями ремонтно-механических и энергетических служб на предприятиях различных отраслей, мучительно пробивавшие себе дорогу в течении десятилетий, в новых условиях будут быстро реализованы в силу их практической и экономической целесообразности.
В новых условиях уже больше нельзя оправдывать проведение сверхнормативных (три-четыре и более) капитальных ремонтов. Повсеместная практика проведения капитальных ремонтов путем полной разборки оборудования также обречена на быстрое саморазрушение. На смену ей должно прийти восстановление ресурса путем массовой замены неисправных узлов и агрегатов. Нынешние свободные промышленные мощности заводов-изготовителей энергооборудования в дальнейшем неизбежно будут загружены производством товарных запасных частей (сменных ремонтных элементов). Мировой опыт свидетельствует, что производство сменных ремонтных элементов- дело выгодное, цена на них всегда на 25-30 % выше, чем в собранном оборудовании. Заводы-изготовители будут заинтересованы в расширенном производстве и реализации своей продукции, и несомненно, пойдут на активное участие в ремонте своего оборудования, в результате чего агрегатно-узловой метод ремонта, который давно научно обоснован, но практически реализован лишь для 7-10 % оборудования (за рубежом подобный метод ремонта с обязательным участием предприятий-изготовителей называется фирменным), очень скоро станет обыденной практикой и в нашей стране на больший процент оборудования, чем раньше.
В сегодняшних условиях основная тенденция в планировании и организации ремонта характеризуется переносом всей ответственности за техническое состояние оборудования непосредственно на предприятия при одновременном расширении их прав в вопросах:
- применение различных систем технического обслуживания и ремонта;
- планирование технического обслуживания и ремонта;
- финансирования ремонта и его материального обеспечения;
- регулирование численности оперативного и ремонтного персонала.
1.1 Подготовка проводов к монтажу
Подготовка проводов к монтажу включает следующие операции:
– мерную резку,
– удаление изоляции и заделку концов проводов,
– маркировку,
– облуживание и свивание проводов.
Мерную резку проводов вручную выполняют ножницами, кусачками, определяя длину провода по шаблону. В мелкосерийном производстве эта операция механизируется с помощью устройств мерной резки (рисунок 1).
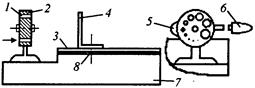
Рисунок 1 - Устройство мерной резки.
Приспособление состоит из упора 4 с закрепленной на нем стрелкой. Упор жестко крепится на столе 7 гайкой-барашком так, чтобы стрелка совпадала с делением линейки 8. Резка производится между отверстиями 1 в неподвижном 2 и подвижном 3 дисках путем поворота диска 3 вручную рукояткой 6. Диск 3 возвращается в исходное положение с помощью пружины 5. Приспособление позволяет получить точность нарезки ±0,7 мм. В других конструкциях вращение диска осуществляется электродвигателем.
Резку проводов (различных марок и сечений) длиной от 50 до 1350 мм и зачистку концов обжигом пластиковой изоляции по концам на расстоянии 5-10 мм при массовом производстве выполняют на специальных автоматах (рисунок 2).
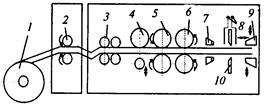
Рисунок 2 - Схема автомата подготовки провода.
Провод с катушки 1 протягивается через механизм предварительной подачи 2, роликовый механизм рихтовки 3, мерный ролик 4, механизмы подачи (ролики 5, 6), зажима 7,9, обжига 8 к устройству резки 10. При достижении заданной длины ведущие подвижные ролики 5 отходят от ведущих неподвижных роликов 6 с помощью пневмосистемы, но происходит фиксация провода зажимами 7 и 9. После этого механизм обжига 8 наджигает изоляцию провода в двух местах. Далее провод разрезается отрезным ножом 10 и выталкивается зажимом 9 с помощью пневмосистемы в тару. Производительность автомата достигает 2000 шт/ч.
Зачистка проводов от изоляции должна обеспечить технологичность монтажа и надежность контактного соединения. Для большинства соединений зачистку осуществляют на длину 7-10 мм, для многожильных проводов – 10-15 мм (рисунок 3).
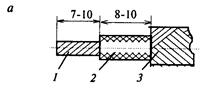
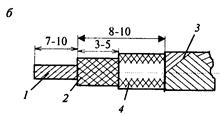
а - пластиковой, б - комбинированной, 1 - провод, 2 –пластиковая изоляция,
3 - экран, 4 - волокнистая изоляция
Рисунок 3 - Разделка концов проводов с изоляцией
Изоляцию проводов удаляют:
– МГВ, МГВЛ, МГВЛЭ, МГВСЛ электрообжигом;
– МГСЛ (с внутренней изоляцией из стекловолокна) надрезом на автомате, специальными щипцами;
– МГТФ, МГТФЛЭ (термостойкая фторопластовая изоляция) надрезом;
– ЛПЛ (хлопчатобумажная пряжа), МОГ (шелк, капрон), МГТЛ (лавсановая) электрообжигом;
– МШВ, МГШВ (пленочная и волокнистая изоляция) электрообжигом;
– эмалевую изоляцию с проводов ПЭТ, ПЭЛ шлифовальной шкуркой, шабером;
– ПЭВ и ПЭМ погружением в муравьиную кислоту и протиркой бязью;
– многожильных ЛЭШО и ЛЭШД нагревом в верхней части пламени
спиртовой горелки и погружением в спирт с последующей протиркой бязью либо погружением в расплав солей (хлористый калий) при температуре 768°С на 1-2 с.
Для зачистки изоляции применяют специальные приспособления, удаляющие изоляцию обжигом (рисунок 4) и стягиванием съемником изоляции.
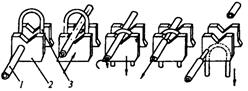
Рисунок 4 - Схема удаления изоляции обжигом
Основными рабочими органами являются нить накала 3 и губки-ножи 2. Нить прожигает изоляцию при повороте провода вокруг оси. Губки являются опорой для провода при прожигании изоляции, предохраняют ее от обугливания, обеспечивают снятие изоляции. Для исключения надрезов губки полируются и имеют радиус скругления 0,08 мм.
Термомеханический способ позволяет снимать изоляцию в один прием с проводов сечением 0,07-0,35 мм2. Рабочее место при этом должно быть оборудовано местной вентиляцией. Недостатки тепловых методов удаления изоляции: возможны пережоги провода, образование оксидной пленки, выделение вредных газов.
К механическим приспособлениям, предназначенным для снятия любой изоляции, относится устройство с механическими щетками, которые вращаются с помощью электродвигателя в противоположных направлениях. Зазор между щетками регулируется. Время зачистки изоляции 2-3 с, производительность 150-300 проводов в час, длина снимаемой изоляции 5-20 мм. К недостаткам механического способа относятся уменьшение диаметра, насечки, скручивание, трудности при обработке проводов малого диаметра (0,02-0,05 мм).
В связи с развитием более совершенных методов объемного монтажа все шире внедряется комплексная механизация и автоматизация подготовки проводов к монтажу. Примером является автомат для мерной резки, зачистки изоляции и лужения проводов марок МШВ, МГШВ, МГВ на длину от 40 до 300 мм (рисунок 5), который состоит из цепной передачи 5, укладчика провода 2, совершающего качательное движение, катушки с запасом провода, щеток 4, зоны обжига изоляции 3, зон флюсования 6, лужения 7, влагозащиты 8, ножей 9.
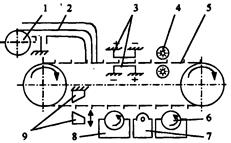
Рисунок 5 - Схема автомата для подготовки проводов.
При перемещении цепей и качании раскладчика провод, сматываясь с катушки, перемещается вместе со штырьками цепи и попадает в зону обжига изоляции 3. Затем щетками 4 снимается оксидная пленка.
Флюсование осуществляется войлочным валиком 6. Лужение происходит в волне припоя 7, влагозащита – в ванночке 8 с вращающимся войлочным роликом, а затем ножами 9 провод отрезается.
Заделку концов провода с волокнистой изоляцией осуществляют с помощью нитроклея, путем надевания полихлорвиниловых трубок или наконечников из пластмасс, нитками (оклетневка).
Оклетневка заключается в наматывании на изоляцию слоя цветных хлопчатобумажных или шелковых ниток, которые затем покрывают клеем БФ-4 или нитролаком (рисунок 6).
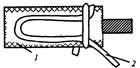
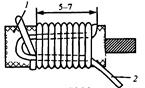
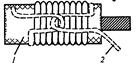
1 - провод, 2 - хлопчатобумажная нитка
Рисунок 6 - Закрепление изоляции провода ниткой
Для отрезания трубок необходимой длины применяют станки, работающие в автоматическом цикле (рисунок 7).
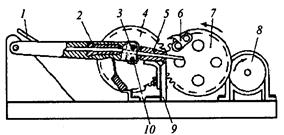
Рисунок 7 - Станок для отрезания изоляционных трубок
Трубка 1 проходит через направляющую втулку 2 и, попадая на сменный ведущий ролик 10, прижимается резиновым валиком 3. Далее вращением шестерен 4 и 7 от ведущей шестерни 8 трубка подается во вторую направляющую втулку 5 и на лезвия подвижного 6 и неподвижного 9 ножей, с помощью которых изоляционная трубка отрезается. Производительность станка 300 тыс. заготовок за смену. Он позволяет разрезать трубки диаметром 2-6 мм на отрезки длиной от 8 до 20 мм.
Для снятия экранирующей оплетки с кабеля применяется установка СЭ-1, работающая по принципу винтового среза оплетки с помощью вращающихся фрез и неподвижных, ножей (рисунок 8).
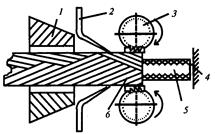
Рисунок 8 - Схема установки для снятия экранирующей оплетки
Перемещением втулки 1 устанавливают расстояние между ножами 2. Кабель 5 подается в отверстие втулки до упора 4. Фрезы 3, вращаясь навстречу движению провода, загибают экранирующую оплетку 6, которая срезается, попадая в зазор между зубьями фрез и ножами. Круговой срез обеспечивается поворотом провода вокруг оси. Установка для снятия экранирующей оплетки с концов монтажных проводов типа МГВШЭ, БПВЛЭ диаметром по оплетке 1- 5 мм имеет производительность 600 заготовок в час.
Разделку концов экранирующей оплетки, обеспечивающую подключение ее к корпусу, выполняют путем протаскивания конца провода через отверстие, сделанное в оплетке на расстоянии 20 мм от конца, и подключением свободной части оплетки к корпусу либо подпайкой к оплетке дополнительного провода. Лужение монтажных проводов осуществляют путем погружения оголенных участков в ванны с припоем ПОС61, ПОС61М при температуре 250-260°С в течение 1- 4 с, используя флюсы ФКСп, ФКТ. Для ВЧ-кабелей с нетеплостойкой изоляцией применяется припои ПОСВ 33 при температуре 170-190°С
1.2 Соединение алюминиевых и медных проводов скруткой, внахлест, встык, желобком, косичкой, бандажное соединение
Надежная и плотная скрутка уберегает от непредвиденных аварийных ситуаций. Важно выполнить ее максимально правильно. Даже малейшие нарушения техники безопасности способны стать поводом для возгорания. По этой причине правила устройства электрооборудования не предусматривают законного применения данного способа. Несмотря на запрет, он актуален как на производствах, так и в быту. Существующие виды скруток проводов можно использовать временно, когда по какой-то причине невозможно быстрое соединение более безопасными методами.