Добавлен: 29.10.2023
Просмотров: 465
Скачиваний: 7
ВНИМАНИЕ! Если данный файл нарушает Ваши авторские права, то обязательно сообщите нам.
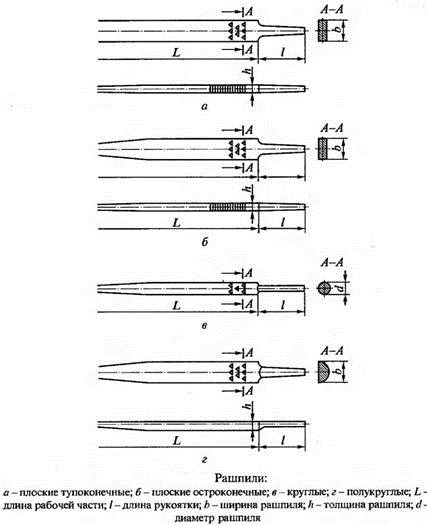
Рисунок 8 Виды рашпилей.
Для обработки мелких деталей применяют специальные напильники — надфили, имеющие малую длину (80,120 или 160 мм) и различную форму поперечного сечения (рис. 10). Надфили имеют также двойную насечку: основную — под углом 25 ° и вспомогательную — под углом 45°
Для обеспечения высокого качества опиливания необходимо правильно выбирать профиль поперечного сечения, длину и насечку напильника.
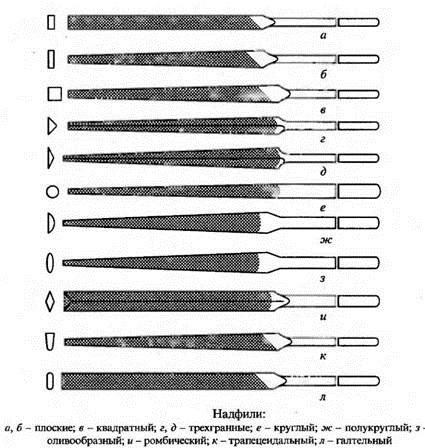
Рисунок 9. Виды надфилей
Профиль поперечного сечения напильника выбирается в зависимости от формы опиливаемой поверхности:
-
плоский, плоская сторона полукруглого — для опиливания плоских и выпуклых криволинейных поверхностей; -
квадратный, плоский — для обработки пазов, отверстий и проемов прямоугольного сечения; -
плоский, квадратный, плоская сторона полукруглого — при опиливании поверхностей, расположенных под углом 90°; -
трехгранный — при опиливании поверхностей, расположенных под углом свыше 60°; -
ножовочный, ромбический — для опиливания поверхностей, расположенных под углом свыше 10°; -
трехгранные, круглые, полукруглые, ромбические, квадратные, ножовочные — для распиливания отверстий (в зависимости от их формы).
Длина напильника зависит от вида обработки и размеров обрабатываемой поверхности и должна составлять:
-
100… 160 мм — для опиливания тонких пластин; -
160…250 мм — для опиливания поверхностей с длиной обработки до 50 мм; 250…315 мм с длиной обработки до 100 мм; 315… 400 мм — с длиной обработки более 100 мм; -
100…200 мм — для распиливания отверстий в деталях толщиной до 10 мм; -
315 …400 мм — для чернового опиливания; -
100… 160 мм — при доводке (надфили).
Номер насечки выбирается в зависимости от требований к шероховатости обработанной поверхности.
Техника безопасности при опиливании металла:
-
Заготовка должна быть прочно зажата в тисках. -
Нельзя работать напильником с расколотой ручкой. Ручка должна быть хорошо насажена на хвостовик напильника. -
Нельзя касаться ручкой инструмента детали, закрепленной в тисках, так как это нарушает прочность её насадки. -
Нельзя охватывать носок напильника левой рукой. -
Запрещается сдувать стружки, удалять их голыми руками. Для этого есть щетка-сметка.
Тема 7: «Сверление, зенкование, зенкерование и развёртывание отверстий»
Сверление, зенкерование и развертывание производится на сверлильных станках различных типов, расточных агрегатных, а также станках токарной группы. Кроме того, эти операции могут производиться с помощью ручных и механических дрелей.
Сверлением называют операцию механической обработки с целью получения отверстий в сплошном материале. Режущими инструментами для сверления служат сверла различной конструкции. Главное движение при сверлении вращательное, движение подачи — поступательное. На сверлильных станках общего назначения и расточных станках главное движение имеет сверло; на токарных станках и специальных сверлильных станках для глубокого сверления сверло имеет только поступательное движение, а заготовка — вращательное; это определяет более высокую точность обработки.
Для облегчения условий работы сверла производят подточку поперечной кромки. С этой же целью производят двойную заточку сверл, работающих по чугуну и стали, с углом 2 ф! = 75—80°. Ширина Ь задней поверхности второй заточки делается в пределах 0,18—0,22 диаметра сверла. В результате двойной заточки увеличивается ширина стружки за счет толщины, уменьшается главный угол в плане, поэтому повышается стойкость сверла.
-
Центровочные сверла применяются для сверления центровых отверстий при зацентровывании заготовок. Эти сверла делаются комбинированными и двусторонними для лучшего использования инструментальной стали. (Рис. 11) -
Перовые сверла выполняются в виде лопаток. Они применяются редко, в основном при сверлении отверстий в твердых поковках и литье. (Рис. 12) -
Сверла с пластинками из твердых сплавов изготовляются диаметром от 3 до 50 мм и применяются для сверления отбеленного чугуна, твердых сталей и т. п. (Рис. 13)
Глубокими отверстиями считаются отверстия, имеющие длину в пять раз и более превышающую их диаметр.
Сверла для глубокого сверления изготовляются диаметром от 6 до 100 мм. Сверление отверстий такими сверлами производится на специальных сверлильных станках, причем в большинстве случаев сверлу сообщается лишь движение подачи, а главное движение (вращательное) сообщается заготовке.
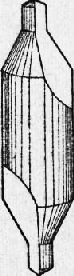
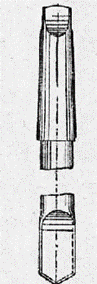
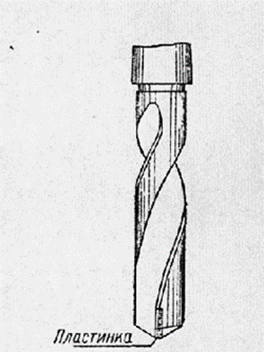
Рисунок 11. Центровочное сверло Рисунок 12. Перовое сверло Рисунок 13. Сверло с пластинкой
из твердых сплавов
Зенкованием называется обработка выходной части отверстия, например, снятие заусенцев с краев отверстий, образование углублений под потайные головки винтов и заклепок. Эта операция выполняется на сверлильных станках с помощью режущего инструмента называемого зенковками. Зенковки по форме режущей части подразделяются на конические и цилиндрические с торцевыми зубьями, снабженные цапфой.
Конические зенковки предназначены для снятия заусенцев в выходной части отверстия, получения конического углубления в отверстии под опоры конических головок винтов и заклепок и для центрования отверстий. Наибольшее распространение получили конические зенковки с углом конуса при вершине 30, 60, 90 и 120°.
Цилиндрические зенковки с торцевыми зубьями применяются для расширения выходной части цилиндрических отверстий под головки винтов, под плоские шайбы, а также для подрезания торцов, плоскостей бобышек, для выборки уступов и углов. Эти зенковки имеют направляющую цапфу, которая при обработке входит в просверленное отверстие, обеспечивая точность совпадения оси отверстия с цилиндрическим отверстием, образованным зенковкой. Цилиндрические зенковки имеют число зубьев от 4 до 8.
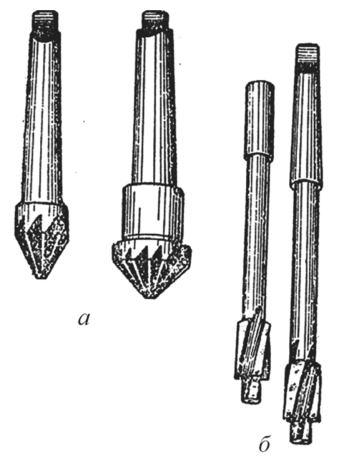
Рисунок 14. Зенковки: а) - конические, б) - цилиндрические.
Зенкерование. Зенкерованием называют операцию механической обработки резанием стенок или входной части отверстия; зенкерование производится по отверстиям, полученным при отливке или ковке (черным) или по просверленным заранее. Цель зенкерования — получение более точных размеров отверстий и положения их осей, фасонная обработка торцовой (входной) части отверстия для получения углублений под головки винтов и пр.
Процесс резания при зенкеровании подобен одновременной работе нескольких расточных резцов, которыми в данном случае можно считать зубья зенкера.
Существуют четыре основных типа зенкеров: для расширения отверстий, для получения цилиндрических углублений отверстий, для получения конических углублений отверстий, для зачистки торцовых поверхностей.
Зенкеры для расширения отверстий изготовляются трехзубыми (для отверстий до 30 мм) и четырехзубыми (для отверстий до 100 мм). На рисунке 14, а – показан трехзубый зенкер с коническим хвостовиком для крепления в шпинделе станка, а на рисунке 14, б — четырехзубый насадной зенкер. С целью повышения производительности зенкеры оснащают пластинками из твердых сплавов.
Помимо цельных зенкеров изготовляют также зенкеры со вставными ножами, изготовленными из быстрорежущей стали или армированными твердыми сплавами. Преимуществом таких зенкеров является экономия быстрорежущей стали и возможность регулирования диаметра обработки. Насадные зенкеры со вставными ножами могут иметь 6 зубьев
Обработка зенкерами обеспечивает исправление оси отверстиями, повышает точность до 4—5-го классов и чистоту поверхности до 4—6-гсг классов:
Зенкеры для получения цилиндрических углублений (рис. 14, в) имеют направляющую цапфу, которая изготовляется за одно целое с корпусом зенкера или (в других конструкциях) делается сменной.
Зенкеры для получения конических углублений — зенковки (рис. 14, г) — чаще всего имеют угол 2cf> = 60°, реже 75°, 90° и 120°. Число зубьев в зенковках колеблется от 6 до 12.
Зенкеры для зачистки торцовых поверхностей (рис. 14, д) имеют зубья только на торце. Число зубьев этих зенкеров, в зависимости от их диаметра, бывает равно 2, 4 или 6.
Кроме описанных, существуют также комбинированные зенкеры для получения ступенчатых отверстий. Эти зенкеры позволяют производить сложную обработку на простом станке, чем достигается уменьшение.
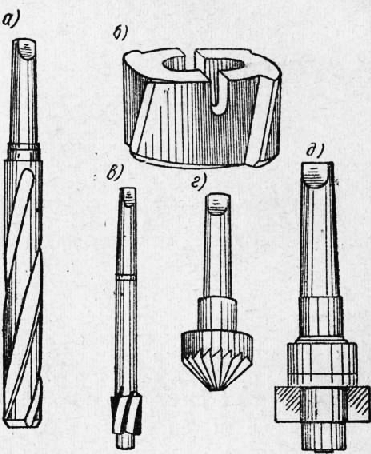
Рисунок 15. Зенкеры
Развертывание. Развертыванием называют операцию механической обработки резанием стенок отверстий с целью получения высокой точности и чистоты поверхности. При развертывании со стенок предварительно обработанных (сверлением и зенкерованием или только сверлением) отверстий снимается слой металла в несколько десятых миллиметра; отверстия получаются в пределах 1—3-го классов точности и 6—9-го классов чистоты. Для получения точных и чистых отверстий применяют последовательно черновое и чистовое развертывание.
По форме обрабатываемого отверстия развертки делятся на цилиндрические и конические.
Развертки, также как и зенкеры, делают хвостовыми и насадными.
Рабочая часть цилиндрической развертки состоит из режущей части калибрующей части и заднего конуса. Число зубьев развертки берется четным (шесть и больше) для достижения точного промера диаметра развертки. Во избежание получения граненого отверстия распределение зубьев по окружности делают неравномерным, однако с учетом того, чтобы обеспечить возможность промера диаметра по ленточке (колебание шага 1—4°).
По способу применения развертки разделяют на машинные и ручные; по конструкции — на цельные и сборные со вставными ножами. Для увеличения стойкости режущую часть зубьев армируют пластинками твердых сплавов.
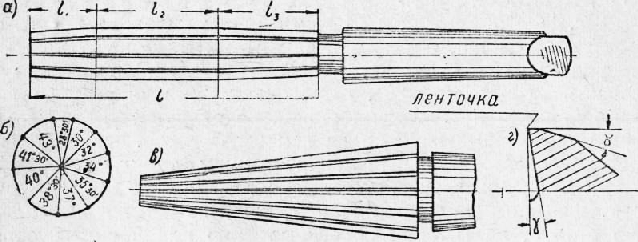
Рисунок 16. Развертки
Техника безопасности при сверлении, зенкеровании, зенковании и развертывании отверстий:
-
надев спецодежду, волосы тщательно заправить под берет; -
расположить инструменты и заготовки в определенном установленном порядке на тумбочку или специальном приспособлении, убрать все лишнее; -
проверить исправную работу станка на холостом ходу; -
не оставлять ключа в сверлильном патроне после смены режущего инструмента; -
не браться за вращающийся режущий инструмент и шпиндель; -
не вынимать рукой сломанных режущих инструментов из отверстия, пользоваться для этого специальными приспособлениями; -
постоянно следить за исправностью режущего инструмента и устройств для крепления заготовок и инструмента; -
не передавать и не принимать каких-либо предметов через работающий станок; -
не работать на станке в рукавицах; -
не оставлять работающий станок без присмотра.