Добавлен: 30.10.2023
Просмотров: 239
Скачиваний: 1
ВНИМАНИЕ! Если данный файл нарушает Ваши авторские права, то обязательно сообщите нам.
2.2 Технология диагностирования и ремонт рулевого управления
Диагностирование рулевого управления позволяет без разборки его узлов оценивать состояние рулевого механизма и рулевого привода; включает работы по определению свободного хода рулевого колеса, общей силы трения, люфта в шарнирах рулевых тяг.
Контроль технического состояния механизма рулевого управления осуществляется на диагностических стендах и с помощью специальных приборов.
Методы определения неисправностей механизма рулевого управления.
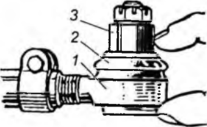
Рисунок 3 Проверка зазоров шарниров рулевых тяг на автомобилях классической компоновки: 1 — наконечник рулевой тяги; 2 — защитный чехол; 3 — рычаг
Перед проверкой механизма рулевого управления доводят до нормы давление воздуха в шинах. Проверяют и при необходимости регулируют углы установки и подшипники ступиц управляемых колес. Подтягивают крепление картера механизма рулевого управления, рулевой сошки и рычагов поворотных цапф, проверяют наличие смазочного материала в узлах механизма рулевого управления и ступицах колес, а у автомобилей с гидроусилителем руля уровень и качество масла в бачке насоса гидроусилителя.
Автомобиль устанавливают на ровную площадку, а управляемые колеса — в положение для движения прямо.
Суммарный угловой зазор рулевого колеса и усилие, необходимое для его поворота, определяют с помощью динамометра - величина углового зазора не должна превышать 20°.
Марка автомобиля, Угловой зазор рулевого колеса, автомобиль (расстояние по ободу колеса, мм)
ЗИЛ .......................................до 10
ГАЗ-5312......................................5
ГАЗ-6611....................................10
МАЗ, КрАЗ............................10-13
КамАЗ (новый)...........................15
ЛиАЗ-677....................................12
ЛАЗ-695Н............................... ....15
ЛАЗ-699Р, ЛАЗ-4202 .................12
ВАЗ-2109, ВАЗ-2105 ............................18-20 (5)
Москвич-2141, Москвич-21412...................16(5)
ЗАЗ-1102 ............................................. 25-30 (10)
ИЖ-212521................................................ 25 (10)
ГАЗ-31029 ...................................................10 (5)
Осмотр и проверка деталей механизма рулевого управления производятся, как правило, двумя механиками при установке автомобиля на эстакаду или осмотровую канаву: один покачивает рулевое колесо попеременно в разные стороны, второй в это время производит проверку креплений деталей рулевого управления и зазоров в соединениях. Сопряженные детали привода рулевого механизма должны перемещаться одновременно/7, с.158/.
В первую очередь проверяются зазоры в шарнирных соединениях рулевых тяг, которые контролируются визуально либо на пальца ощупь, приложив пальцы одновременно к наконечнику тяги и к головке рычага 3. Одновременно проверяется состояние защитных чехлов 14 (рис. 4). Затем проверяют крепление картера рулевого механизма по его перемещению при поворотах рулевого колеса, подтягивают крепление.
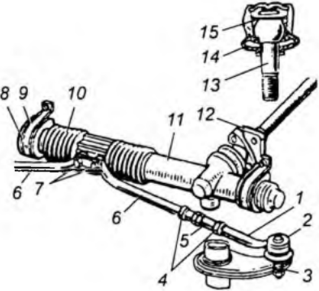
Рисунок 4 Проверка зазора шарниров рулевых тяг на автомобилях:
1 — наконечник рулевой тяги: 2 — шаровой шарнир наконечника; 3 — поворотный рычаг; 4 — гайка; 5 — регулировочная тяга; 6 — рулевые тяги; 7— болты крепления рулевых тяг к рейке; 8 — скоба крепления редуктора; 9 — опора рулевого механизма; 10 — гофрированный защитный чехол редуктора; 11 — картер редуктора;
12 — упругая муфта; 13 — папец шарового шарнира; 14 — защитный чехол шарового шарнира; 15 — вкладыш шарового
На автомобилях с классической схемой компоновки проверяют крепление и зазор маятникового рычага. Кроме того, выявляются механические повреждения деталей механизма рулевого управления, определяется надежность крепления рулевого колеса и симметричность его установки (при прямолинейном положении колес), а также отсутствие подтекания смазочного материала из картера рулевого механизма.
На переднеприводных автомобилях проверяют изнашивание резинометаллических шарниров соединений рулевых тяг 6 с рейкой рулевого механизма, креплений упругой муфты 12, а также состояние защитных чехлов 10 редуктора рулевого механизма.
Проверка свободного хода рулевого колеса автомобиля с гидроусилителем производится при работе двигателя на холостом ходу. Перед тем как приступить к регулировке свободного хода рулевого колеса, необходимо проверить состояние и регулировку рулевого механизма, зазор в карданных сочленениях и затяжку клиньев крепления карданного вала.
Чтобы проверить осевой зазор рулевого колеса, необходимо перемешать рулевое колесо в осевом направлении вверх и вниз. При наличии осевого зазора подтягивают гайку, предварительно разогнув усики ее стопорной шайбы.
После регулировки один из усиков шайбы загнуть в паз гайки и проверить момент сопротивления вращению вала механизма рулевого колеса, отсоединенного от карданного вала рулевого управления. Допустимое сопротивление вращению должно быть 0,6-0,8 Н • м.
Проверка рулевого механизма производится при отсоединенной от сошки 12 (рис. 5) продольной рулевой тяги и неработающем двигателе.
Пользуясь пружинным динамометром, измеряют усилие, приложенное к ободу рулевого колеса, в трех положениях:
первое (рис. 5, а) - рулевое колесо повернуто более чем на два оборота от среднего положения, усилие на ободе рулевого колеса 6-16 Н/10, с.67/.
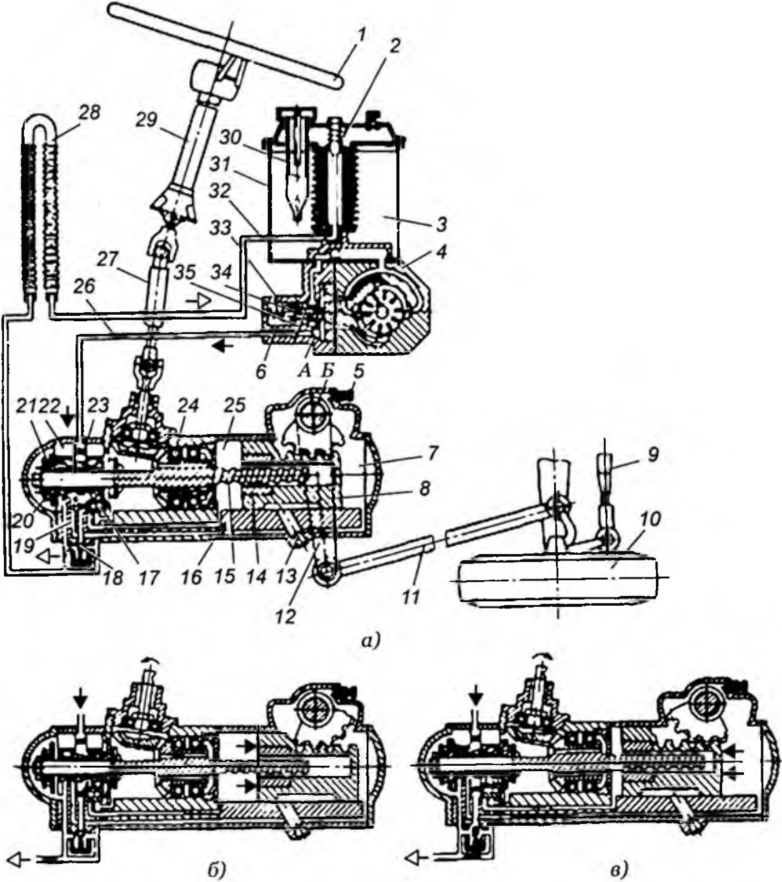
Рисунок 5 Гидроусилитель рулевого привода
автомобиля марки «КамАЗ и схемы его работы:
а - движение прямо; 6 - поворот направо; в - поворот налево; 1 - рулевое колесо;
2 - пружина предохранительного клапана фильтра гидросистемы; 3 - фильтр; 4 - насос гидроусилителя; 5 - перепускной клапан; 6 - вал сошки с зубчатым сектором; 7 - задняя рабочая полость гидроусилителя; 8 - поршень-рейка; 9 - поперечная тяга; 10 - переднее колесо; 11 - продольная тяга; 12 - сошка; 13 - сливная магнитная пробка; 14 - шариковая гайка; 15 - винт; 16 - картер рулевого механизма; 17 - обратный клапан;
18 - предохранительный клапан рулевого механизма; 19 - клапан управления гидроусилителем; 20 - золотник клапана управления; 21 - упорный подшипник;
22 - реактивный плунжер; 23 - центрирующая пружина; 24 - угловой редуктор;
25 - передняя рабочая полость гидроусилителя; 26 - линия нагнетания; 27 - карданный вал; 28 - радиатор; 29 - рулевая колонка; 30 - фильтр заливной горловины; 31 - бачок гидросистемы; 32 - линия слива; 33 - пружина перепускного клапана насоса;
34 - предохранительный клапан насоса;
35 - перепускной клапан; А, Б - дросселирующие отверстия
- второе (рис. 5, б) — рулевое колесо повернуто на 3/4— 1 оборот от среднего положения, усилие, приложенное к ободу рулевого колеса, не должно превышать 22 Н;
- третье (рис. 5, в) — рулевое колесо проходит среднее положение, усилие, приложенное к ободу рулевого колеса, не должно превышать на 4—6 Н усилия, полученного при замере во втором положении рулевого колеса, и не должно превышать 27 Н.
У автомобилей марки «ЗИЛ» усилие на ободе рулевого колеса проверяют так же в трех положениях рулевого колеса при работающем двигателе:
- первое — рулевое колесо повернуто более чем на два оборота от среднего положения, усилие 5,5—13,5 Н;
- второе — рулевое колесо поворачивают на 3/4 — 1 оборот от среднего положения, усилие не должно превышать 23 Н;
- третье — усилие должно быть больше на 8—12,5 Н, чем во втором положении, но не более 28 Н.
Начинают регулирование рулевого механизма с установления величины усилия в третьем положении, пользуясь регулировочным винтом и предварительно ослабив его контргайку (при этом рулевой механизм не требует разборки).
При вращении регулировочного винта по часовой стрелке усилие увеличивается, а против часовой стрелки — уменьшается. Момент затяжки контргайки 60—65 Н м. После затяжки контргайки следует вторично проверить регулировку. Несоответствие усилия на ободе рулевого колеса при первом и втором положениях указанным выше данным свидетельствует о неправильной регулировке упорных подшипников винта рулевого механизма, повреждении деталей узла шарнирной гайки.
Поворот вала сошки с одного крайнего положения в другое требует приложения усилия 98 Н.
Разборка рулевого механизма должна выполняться только квалифицированным механиком.
Давление насоса гидроусилителя проверяют при частоте вращения коленчатого вала на режиме холостого хода 600 мин'1 с помощью специального устройства (рис. 6). Устройство включают между насосом и шлангом высокого давления усилителя механизма рулевого управления. Открывают вентиль, проворачивая колеса автомобиля в крайнее левое или правое положение до упора. При этом давление, развиваемое насосом, должно быть не менее 5,5 МПа. Если давление не достигает этого значения, надо медленно ввертывать вентиль, наблюдая за увеличением давления по показаниям манометра (рис. 6).
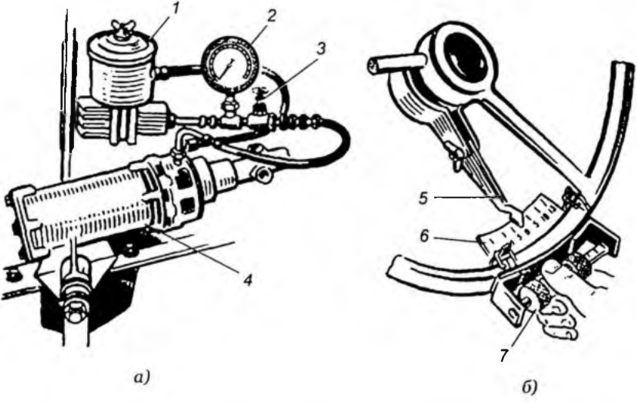
Рисунок 6 Устройство для измерения давления насоса гидроусилителя (а) и прибор для измерения зазоров в рулевом колесе (б):
1 - бачок; 2 - манометр; 3 - вентиль; 4 - гидроусилитель руля; 5 - указатель; 6 - шкала;
7 – манометр
Отсутствие повышения давления свидетельствует о неисправности в рулевом механизме — неправильной регулировке предохранительного клапана или больших внутренних утечках масла.
Если давление насоса при закрытом вентиле больше, чем при открытом, но ниже 6 МПа, то неисправны оба узла.
Чтобы проверить правильность работы клапана управления гидроусилителя рулевого привода надо отсоединить продольную рулевую тягу, открыть вентиль и приложить дополнительное усилие на рулевое колесо — не менее 98 Н при частоте вращения коленчатого вала 1000 мин-1. При снятии усилия с рулевого колеса давление должно упасть до 0,3—0,5 МПа (не более).
Данную проверку выполняют в обоих крайних положениях. Недостаточное падение давления показывает на заедание в клапане. При проверке нельзя держать вентиль закрытым более 5 с. Температура в бачке 1 насоса должна составлять 65—75 °С. При необходимости повышения температуры масла следует поворачивать колеса от одного крайнего положения до другого, удерживая их каждый раз в указанных положениях не более 15 с /9, с.45/.
3 Охрана труда
От организации рабочего места зависят производительность труда и обеспечение безопасности работы. Необходимо, чтобы слесарь регулярно убирал своё рабочее место, оборудование и инструменты, не разбрасывал обтирочные материалы, не проливал масло, топливо, воду.
На автотранспортных предприятиях рабочие места снабжают технологическими картами, содержащими:
- перечень операций в технологической последовательности;
- перечень оборудования и инструментов;
- указание о месте выполнения работы (сверху, снизу, сбоку автомобиля);
- количество одновременных мест обслуживания;
- норму времени и технические условия выполнения работы.
Предусматривается связь рабочих мест с мастером, работниками вспомогательных служб, доставка запасных частей и материалов непосредственно на рабочее место.
Рабочие, занятые техническим обслуживанием и ремонтом автомобилей, могут входить в специализированную или комплексную бригаду.
Для большинства авторемонтных заводов характерны специализированные производственные бригады, обеспечивающие наиболее полную загрузку рабочих и эффективное использование оборудования, что достигается специализацией каждого члена бригады по выполнению технологически однородных операций, но в необходимых случаях исполнители могут быть заменены любым другим членом бригады.
Замену агрегатов и их ремонт без снятия с автомобиля производят на осмотровых канавах, ремонт агрегатов, снятых с автомобиля, - на специализированных участках по ремонту.
Выполняя работы по техническому обслуживанию непосредственно на автомобиле или на верстаке, слесарь - авторемонтник должен соблюдать требования техники безопасности, одним из основных условий которого является порядок на рабочем месте.
Для защиты от ожогов при работе с расплавленным свинцом рабочий должен надевать защитный резиновый фартук, резиновые перчатки, резиновые полусапоги и защитные очки. При замене пластин одежда и руки рабочего постоянно загрязняются соединениями свинца, поэтому следует работать в хлопчатобумажном костюме с кислостойкой пропиткой, резиновом фартуке и перчатках. При приготовлении свинцово-сурьмянистого сплава для отливки деталей необходимо засыпать его поверхность древесным углем для уменьшения выделения паров свинца. При этом следует особенно тщательно следить за исправностью вытяжной вентиляции или местного отсоса над верстаком. Особенно активно выделяются пары при расплавлении свинца электрической дугой. В этом случае необходимо работать в респираторе.