Файл: Лабораторная работа 6 Часть 1 теоретический материал.doc
ВУЗ: Не указан
Категория: Не указан
Дисциплина: Не указана
Добавлен: 07.11.2023
Просмотров: 34
Скачиваний: 1
ВНИМАНИЕ! Если данный файл нарушает Ваши авторские права, то обязательно сообщите нам.
Лабораторная работа 6
Часть 1
ТЕОРЕТИЧЕСКИЙ МАТЕРИАЛ
2.1. Общие положения
Когда спрос на продукт вытекает из планов производства определённых изделий, говорят, что имеется зависимый спрос.
Зависимый спрос – это потребность в продукте, который представляет собой заготовку или составную часть для использования в производстве конечного продукта.
Планирование материальных потребностей производства (Material Requirements Planning – MRP) – это система на основе компьютерной базы данных, которая разработана для управления и планирования производственных запасов зависимого спроса (т. е. сырьевых материалов, запчастей и сборочных узлов). План производства определённого количества конечной продукции «переводится на язык запросов» на компоненты и сырьевые материалы, используя производственные данные, чтобы определить, когда и сколько заказывать. Данная система широко использовалась с середины 1950-х гг. до 1970-х гг.
2.2. Первичные входные данные системы MRP
Первичными входными параметрами для MRP являются:
1) контрольный график, определяющий сколько потребуется продукта и когда;
2) список материалов, определяющих состав конечного продукта;
3) информация о производственных ресурсах, определяющая количество материальных запасов.
Контрольный график (в отечественных аналогах – производственное расписание) – один из трёх основных входных параметров MRP, определяющий вид конечного продукта, его количество и срок производства. На рис. 1 изображён фрагмент контрольного графика
Изделие\ количество | Недели | |||||||
1 | 2 | 3 | 4 | 5 | 6 | 7 | 8 | |
А | | | | 100 | | | | 150 |
Рис. 1. Пример контрольного графика
Контрольный график делит плановый период на последовательность временных интервалов, которые часто выражены в неделях в краткосрочных планах и месяцах или кварталах – в долгосрочных.
Список материалов – перечень всех сырьевых материалов, частей, подузлов и узлов, которые необходимы для производства одной единицы
изделия.
Перечень имеет иерархическую структуру: он показывает количество каждого элемента, необходимого для завершения одной единицы изделия на каждом последующем уровне сборки.
Наглядно представление о списке материалов может дать дерево структуры изделия (рис. 2, а). Конечный продукт располагается на вершине дерева. Ниже – основные компоненты и узлы, участвующие в сборке готового изделия. Под каждым основным компонентом – необходимые составляющие его меньшие компоненты и т. д.
Когда производственные потребности высчитываются в системе MRP, рассматривается уровень за уровнем дерево структуры изделия, начиная с вершины. Если составляющий компонент встречается более чем на одном уровне, определение его количества усложняется. Иногда в таком случае используется упрощение – кодирование по нижнему уровню, которое включает реструктуризацию списка материалов таким образом, чтобы дублирующиеся элементы группировались на низшем уровне своего появления (рис. 2, б).
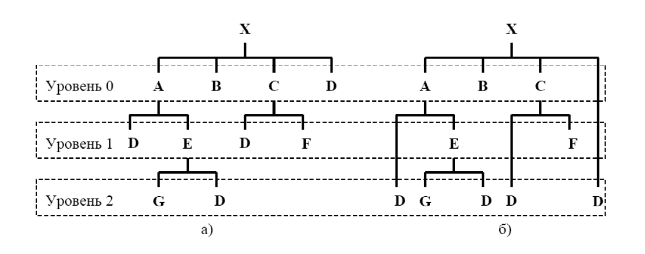
Рис. 2. Дерево структуры изделия
Данные по материально-производственным запасам – информация о состоянии каждого элемента производства в определённый период времени. Они включают:
• основные данные:
− общие материальные потребности производства;
− график поступлений запасов;
− величину наличных запасов;
• дополнительные данные:
− поставщик;
− время производства;
− размер партии;
• данные по изменениям:
− поступление запасов;
− расход запасов;
− отмена заказа и др.
2.3. Функционирование MRP
MRP обрабатывает требования по конечному продукту, уточнённые
контрольным графиком, и перестраивает их в синхронизированные по
времени требования
по сборочным узлам, деталям и сырью, используя
список материалов для смещения по времени производства. Временная
синхронизация производственных потребностей видна на диаграмме
(рис. 3).
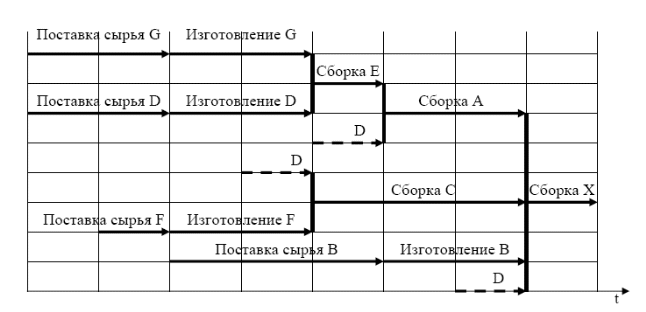
Рис. 3. Диаграмма синхронизированных по времени производственных требований
Количества, которые получаются из переработки списка материалов, не принимающие в расчёт данные о запасах и заказах, называются общей (валовой) потребностью.
Материалы, которые действительно нужно получить для соответствия количеству, указанному в контрольном графике, называются чистыми материально-производственными потребностями. Определение чистых материальных потребностей составляет ядро MRP. Оно выполняется путём вычитания из величины общей потребности суммы наличных запасов и запланированных поставок по графику, а затем к полученному результату прибавляются требования по резервному запасу, если они необходимы.
Распределение поставок по времени и размерам определяется по заказ-релизам. График получения заказанных материалов определяется плановыми заказами.
Функционирование системы MRP отражают календарно-плановые расчеты, основой которых являются производственное расписание и структура изделия.
На основании календарно-плановых расчетов можно составить укрупненный цикловой график изготовления изделия.
2.4. Обновление данных в системе MRP
Две основные системы, используемые для обновления данных в MRP:
1) регенеративная система. Является пакетной системой, которая собирает все изменения, имеющие место в пределах определённого интервала времени, и периодически обновляет систему. На основе этого разрабатывается скорректированный план производства;
2) система чистых изменений. Представляет собой подход, при котором данные обновляются постоянно. Здесь основной производственный план модифицируется с отражением всех изменений по мере их появления. В базовый план вносятся изменения, но полностью его не обновляют.
2.5. Выходные данные в системе MRP
Система MRP может предоставлять:
1. первичные отчёты – основные выходные параметры. Включают:
1.1. плановые заказы – график, показывающий величину и время будущих заказов;
1.2. выполнение заказа – разрешение на выполнение плановых заказов;
1.3. изменения в плановых заказах – информацию о пересмотре даты и величины заказа, его отмене;
2. вторичные отчёты − основные выходные параметры. Включают:
2.1. отчёты по контролю за исполнением. Используются для оценки работы системы;
2.2. отчёты по планированию. Используются для прогнозирования будущих требований по запасам;
2.3. отчёты об исключительных ситуациях. Определяют основные несоответствия (просроченные заказы, большой процент от брака, ошибки в отчетности, требования на несуществующие детали).
2.6. Система MRP и планирование производственных мощностей
Контрольный график, используемый в качестве входного параметра для системы MRP, может оказаться невыполнимым с точки зрения требований по производственной мощности, необходимой для его реализации.
Планирование требований по производственной мощности – это процесс определения краткосрочных потребностей производственных мощностей.
Этот процесс осуществляется на основе полученных выходных данных системы MRP, которые преобразуются в требования по мощности в форме отчётов по загрузке для каждого подразделения. Подобные отчёты показывают сравнительную картину известных и предполагаемых требований по загрузке с планируемой пропускной способностью. Отсутствие несогласований позволяет утвердить производственный график. В случае наличия отклонений возможно увеличение производственных мощностей или изменение контрольного графика производственного процесса с дальнейшей его обработкой в системе MRP.
3. ВАРИАНТЫ ЗАДАНИЙ
Изготовление изделия А, структура которого представлена по вариантам в табл. 1, является сложным производственным процессом.
Для процесса заданы ограничения:
− каждая деталь изделия изготавливается на собственном оборудовании;
− максимальная партия обработки деталей – 100 штук;
− длительность простых процессов изготовления деталей не зависит от размера партии.
Размер партии, изготавливаемой за одну операцию сборки, не ограничивается. Производственное расписание представлено по вариантам в табл. 2. Время обработки и наличный запас для каждого структурного элемента изделия А по вариантам представлены в табл. 3.
Требуется:
1) выполнить календарно-плановые расчеты по изделию. Результаты свести в таблицу, аналогичную табл. 7;
2) построить укрупненный цикловой график изготовления изделия А с учетом заданных ограничений и определить по графику длительность производственного цикла.
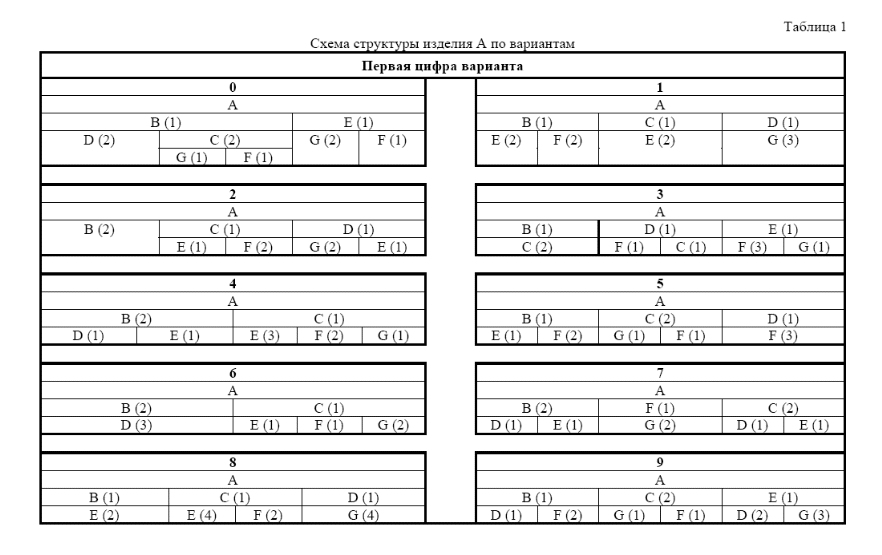
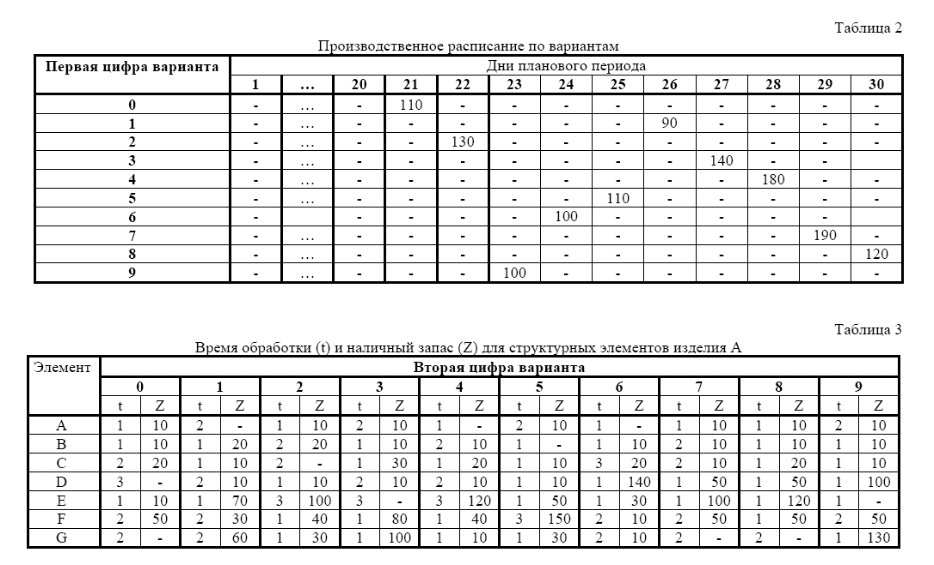
4. ПРИМЕР ВЫПОЛНЕНИЯ ЗАДАНИЯ
Структура изделия А представлена на рис. 4 и в табл. 4. В скобках указано количество однородных элементов.
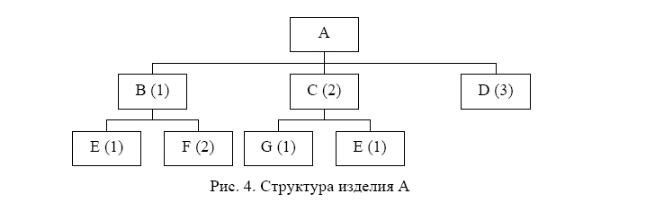
Изделие А состоит из деталей D, E, F, G и сборочных единиц В, С.

Производственное расписание представлено в табл. 5.

Время обработки и наличный запас для каждого структурного элемента изделия А представлены в табл. 6.
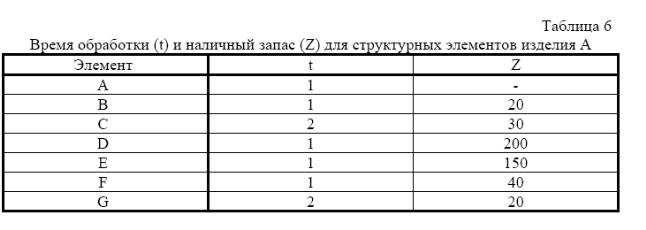
В рамках календарно-плановых расчетов сначала находится валовая потребность по каждому структурному элементу Qв, затем чистая потребность Qч и время опережения, то есть время начала процесса изготовления структурного элемента. Совокупные расчеты по календарному планированию сводятся в табл. 7.
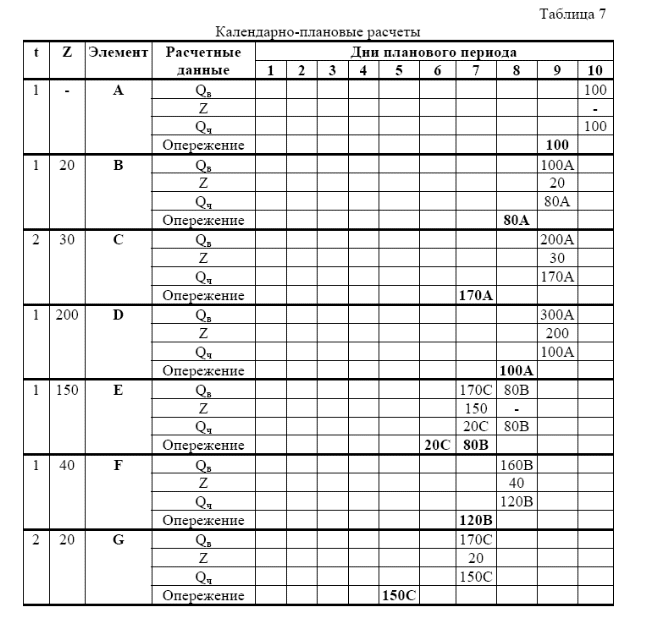
На основании полученных данных строится цикловой график процесса изготовления изделия А. Опережение показывает время начала выполнения процесса изготовления структурного элемента. Установленные ограничения касаются деталей F и G, так как материальные потребности по этим деталям превышают минимальный размер партии. Поэтому простые циклы изготовления этих деталей будут удвоенны, что может оказать влияние на длительность цикла.
Поскольку деталь Е является составной частью сборочных единиц В и С, а общая потребность по этой детали не превышает установленной производственной партии в 100 штук, то возможно изготовление Е за один раз соответственно наиболее ранним срокам потребности.
Первоначально потребность в детали Е возникает для сборочной единицы С, поэтому начать изготовление надо не позже, чем в пятый день.