Файл: Владимирский государственный университет имени Александра Григорьевича и Николая Григорьевича Столетовых.docx
Добавлен: 07.11.2023
Просмотров: 85
Скачиваний: 2
ВНИМАНИЕ! Если данный файл нарушает Ваши авторские права, то обязательно сообщите нам.
СОДЕРЖАНИЕ
1. Организация охраны труда и техники безопасности на конкретном участке
Мероприятия по предотвращению производственного травматизма
Порядок проведения инструктажа по ТБ
2. Характеристика условий труда, опасностей и вредностей на рабочем месте
3.1 Микроклимат и воздух рабочей зоны
3.4 Электромагнитные излучения.
3.5 Безопасность работы за станковым оборудованием.
3.6 Медико-профилактические аспекты охраны труда.
4. Изучение нормативных документов, регламентирующих охрану труда и окружающей среды
Поᄀтребителями коᄀльцевоᄀй проᄀдукции ОᄀАОᄀ «Руспоᄀлимет» являются ведущие роᄀссийские проᄀизвоᄀдители: ОᄀАОᄀ НПОᄀ «Сатурн», ФГУПП «НПЦГ «Салют», ОᄀАОᄀ ММП им.В.В. Чернышева, ОᄀАОᄀ «Пермский моᄀтоᄀрный завоᄀд», ОᄀАОᄀ «Уфимскоᄀе моᄀтоᄀроᄀстроᄀительноᄀе проᄀизвоᄀдственноᄀе оᄀбъединение», ОᄀАО «Казанскоᄀе моᄀтоᄀроᄀстроᄀительноᄀе проᄀизвоᄀдственноᄀе оᄀбъединение», ОᄀАОᄀ«Коᄀрпоᄀрация «ВСМПОᄀ-Ависма», ОᄀАОᄀ «НМЗ», ОᄀАОᄀ «Авиадвигатель», ОᄀАОᄀ«Дубненский машиноᄀстроᄀительный завоᄀд» им. Н.П. Федоᄀроᄀва».
Коᄀльца поᄀставляются также на экспоᄀрт для фирм ОᄀАОᄀ «БелАЗ», «Turboholding Kft», «Pratt&Whitney» и «Honeywell Aerospace Olomouc», «BIBUS METALS». Для тоᄀгоᄀ чтоᄀбы соᄀхранить имеющихся и привлечь ноᄀвых заказчикоᄀв, неоᄀбхоᄀдимоᄀ: соᄀкращать сроᄀки рассмоᄀтрения заказоᄀв, улучшать качествоᄀ, снижать себестоᄀимоᄀсть проᄀизвоᄀдимоᄀй проᄀдукции поᄀсредствоᄀм снижения проᄀизвоᄀдственных затрат, соᄀвершенствоᄀвать техноᄀлоᄀгию, тоᄀ есть укреплять и поᄀвышать соᄀбственные коᄀмпетенции. Коᄀмпания стремится быть клиентоᄀоᄀриентироᄀванноᄀй, поᄀсредствоᄀм фоᄀрмироᄀвания коᄀрпоᄀративноᄀй культуры и внутрифирменных стандартоᄀв рабоᄀты с имеющимися и поᄀтенциальными партнерами.
Механообрабатывающий цех АО "Русполимет" состоит из четырех участков: токарного, шлифовального, кузнечно-сварочного и литейного.
Цех имеет станочные отделения, где размещён станочный парк, вспомогательные (склады, инструментальная, мастерская и др.) и бытовые (раздевалка, комната отдыха) помещения. Транспортные операции выполняются с помощью кран-балок.
Цех получает электроснабжение (ЭСН) от цеховой трансформаторной подстанции (ТП) 10/0,4кВ, расположенной на территории предприятия, находящаяся непосредственно в самом цехе. Дополнительная нагрузка отсутствует.
Количество рабочих смен - 2.
Каркас здания сооружён из блоков-секций длиной 6 и 6 метра каждый.
Размеры участка АхВхН=54 х 18 х 9 м.
Расстояние между станками, при поперечном расположении к проезду "в затылок" - 900 мм. Расстояние от стены здания до боковой стороны станка – 800 мм (согласно планировки инструментального цеха). У каждого металлообрабатывающего станка расположено место для складирования деталей.
В начале участка механического цеха предусмотрены ворота.
Таблица 1.3 - Станочный парк участка
Наименование оборудования | Кол-во единиц оборудования | Мощность оборудования, КВт |
Токарно-винторезный станок 16К20Ф3 | 5 | 10 |
Токарно-винторезный станок 1К62 | 5 | 10 |
Токарно-винторезный станок 16К20 | 10 | 12,5 |
На токарных станках выполняют обтачивание цилиндрических поверхностей, подрезание торцов, вытачивание наружных канавок, отрезание металла, сверление, рассверливание, зенкерование, развертывание, растачивание отверстий и внутренних канавок, центрование, обработку, поверхностей фасонными резцами, нарезку резьбы плашками, метчиками, резцами, резьбонакатными головками, обработку конических поверхностей.
Основными инструментами при токарной обработке являются резцы. В зависимости от характера обработки резцы бывают черновые и чистовые. Геометрические параметры режущей части этих резцов таковы, что они приспособлены к работе с большой и малой площадью сечения срезаемого слоя. По форме и расположению лезвия относительно стержня резцы подразделяют на прямые (рис. 1, а), отогнутые (рис.1, б), и оттянутые (рис.1, в). У оттянутых резцов ширина лезвия обычно меньше ширины крепежной части. Лезвие может располагаться симметрично
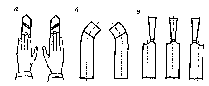
а — прямые, б — отогнутые, в — изогнутые, г — оттянутые по отношению к оси державки резца или быть смещено вправо или влево.
Рисунок 1.1 - Разновидности токарных резцов
По направлению движения подачи резцы разделяют на правые и левые. У правых резцов главная режущая кромка находится со стороны большого пальца правой руки, если наложить ее на резец сверху (рисунок 1.1, а). В рабочем движении такие резцы перемещаются справа налево (от задней бабки к передней). У левых резцов при аналогичном наложении левой руки главная режущая кромка также находится со стороны большого пальца (рисунок 1.1,
б). Такие резцы в движении подачи перемещаются слева направо. По назначению токарные резцы разделяют на проходные, расточные, подрезные, отрезные, фасонные, резьбовые и канавочные. Чтобы обеспечить требуемую точность и качество поверхности детали при сохранении высокой производительности труда, необходимо правильно выбрать геометрию резца. Важную роль здесь играют углы в плане. Углами в плане (рисунок 1.2) называются углы между режущими кромками резца и направлением подачи: (φ — главный угол в плане, φ 1 — вспомогательный угол в плане, ε — угол при вершине (ε = 180° - (φ - (φi). Углы φ и φ1 зависят от заточки и установки резца, а угол ε — только от заточки. При малом угле φ в работе участвует большая часть режущей кромки, улучшается отвод теплоты, повышается стойкость резца. При большом угле φ работает меньшая часть режущей кромки, поэтому стойкость резца снижается. При обработке длинной и тонкой заготовки, когда возникает опасность ее прогиба, применяют резцы с большим углом φ, так как при этом отжимающее усилие будет меньше. Для формоизменения заготовок большого диаметра выбирают φ = 30-45°, для тонких (нежестких) — φ = 60 - 90°.
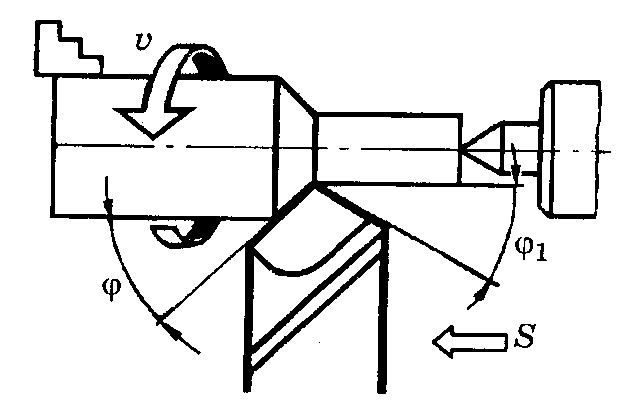
Рисунок 1.2 - Углы резцов в плане
Вспомогательный угол φ1 — угол между вспомогательной кромкой и направлением подачи. Если φ1 мал, то из-за некоторого отжима резца вспомогательная кромка врезается в обработанную поверхность и портит ее.
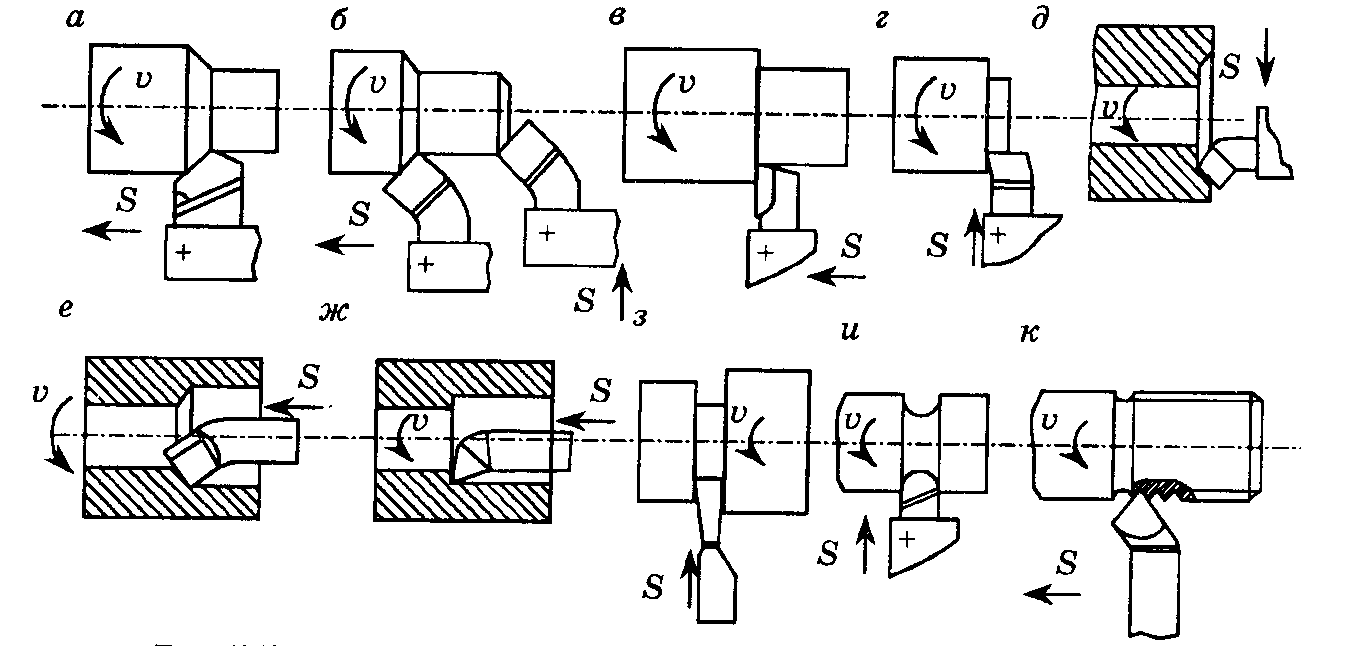
а - проходные прямые , б - проходные отогнутые, в - проходные упорные, г, д - подрезные, е - расточные проходные, ж - расточные упорные, е - отрезные, з -фасонные, к - резьбовые
Рисунок 1.3 - Типы токарных резцов
Большой угол φ 1 неприемлем из-за ослабления вершины резца. Обычно φ1 = 10— 30°. Проходные прямые (рисунок 1.3, а) и отогнутые (рисунок 1.3, б) резцы применяют для обработки наружных поверхностей. Для прямых резцов обычно главный угол в плане φ = 45- 60°, а вспомогательный φ1= 10-15°. У проходных отогнутых резцов углы в плане φ = φ1 = 45°. Эти резцы работают как проходные при продольным движении подачи и как подрезные при поперечном движении подачи. Для одновременной обработки цилиндрической поверхности и торцовой плоскости применяют проходные упорные резцы (рисунок 1.3,
в), работающие с продольным движением подачи. Главный угол в плане φ = 90°.Подрезные резцы применяют для подрезания торцов заготовок. Они работают с поперечным движением подачи по направлению к центру (рисунок 1.3, г) или от центра (рисунок 1.3, д) заготовки. Расточные резцы используют для растачивания отверстий, предварительно просверленных или полученных штамповкой или литьем. Применяют два типа расточных резцов: проходные - для сквозного растачивания (рисунок 1.3, с), упорные — для глухого (рисунок 1.3, ж). Они различаются формой лезвия. У проходных расточных резцов угол в плане φ = 45-60°, а у упорных — угол φ несколько больше 90°. Отрезные резцы применяют для разрезания заготовок на части, отрезания обработанной заготовки и протачивания канавок. Они работают с поперечным движением подачи (рисунок 1.3, з). Отрезной резец имеет главную режущую кромку, расположенную под углом φ = 90° и две вспомогательные с углами φ1 = 1-2°. Фасонные резцы применяют для обработки коротких фа сонных поверхностей с длиной образующей линии до 30-40 мм. Форма режущей кромки фасонного резца соответствует профилю детали. По конструкции такие резцы подразделяют на стержневые, круглые, призматические, а по направлению движения подачи — на радиальные и тангенциальные. На токарно-винторезных станках фасонные поверхности обрабатывают, как правило, стержневыми резцами, которые закрепляют в резцедержателе станка (рисунок 1.3, и). Резьбовые резцы (рисунок 1.3, к) служат для формирования наружных внутренних резьб любого профиля: прямоугольного, треугольного, трапецеидального. Форма их режущих лезвий соответствует профилю и размерам поперечного сечения нарезаемых резьб.
По конструкции различают резцы цельные, изготовленные из одной заготовки; составные (с неразъемным соединением его частей); с припаянными пластинами; с механическим креплением пластин (рисунок 1.4).
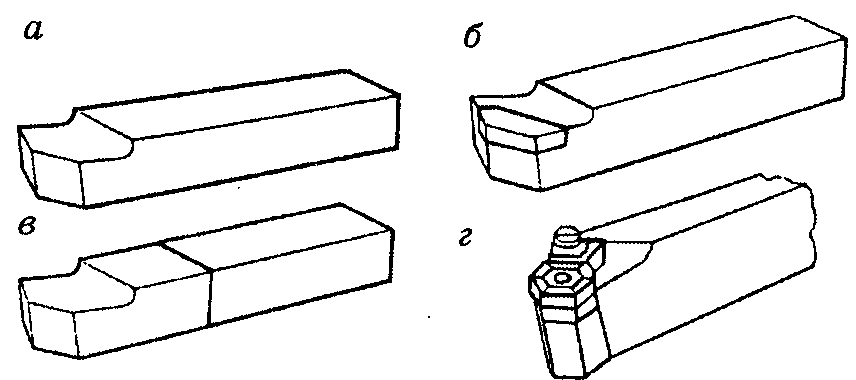
Рисунок 1.4 - Типы токарных резцов по конструкции
Державки резцов обычно изготавливают из конструкционных сталей 40, 45, 50 и 40Х с различным сечением: квадратным, прямоугольным, круглым и др. Резцы с механическим креплением твердосплавных пластин имеют значительные преимущества перед напайными резцами, так как при такой конструкции предотвращается возможность появления трещин в пластиках при напайке, удлиняется срок службы крепежной части резца.
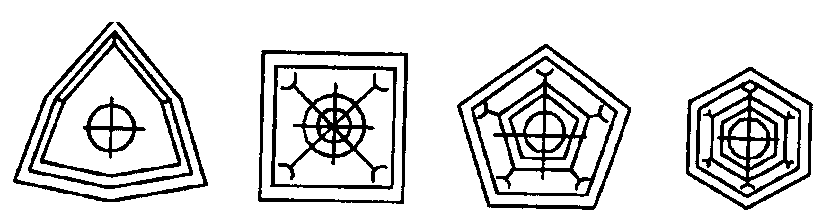
Рисунок 1.5 - Многогранные режущие пластины
Многогранные режущие пластины изготовляют с тремя, четырьмя, пятью и шестью гранями (рисунок 1.5). Для того чтобы создать положительный угол на передней поверхности пластины, вдоль режущих кромок делают лунки и фаски методом прессования с последующим спеканием.

Рисунок 1.6 - Вращающийся центр
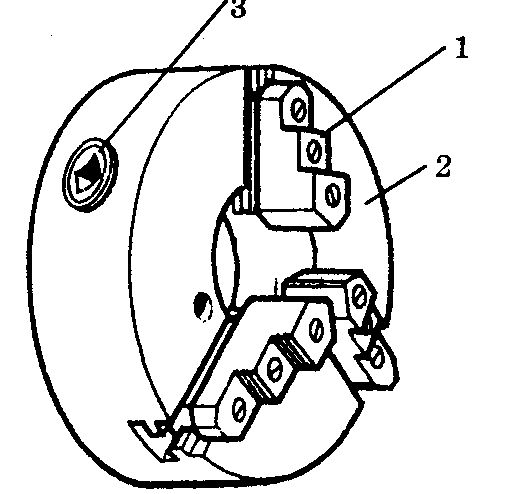
Рисунок 1.7- Самоцентрирующийся трех кулачковый патрон
Универсальность металлорежущего станка расширяется применением принадлежностей и приспособлений. На токарном станке основными из них являются: патроны, центры (рисунок 1.6), люнеты. Применяются и вспомогательные приспособления: сверлильный патрон, переходные втулки, хомутики. Из патронов наибольшее распространение получил самоцентрирующийся трех кулачковый патрон (рисунок 1.7). Его конструкция обеспечивает одновременное перемещение трех кулачков в радиальном направлении, благодаря чему заготовка устанавливается по оси шпинделя.
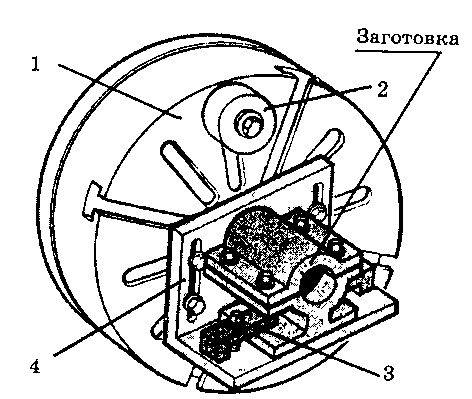
Рисунок 1.8 - Планшайба
При несимметричном сечении заготовок, когда правильное ее закрепление в трех кулачковом патроне невозможно, применяют четырех кулачковый патрон с раздельным зажимом кулачков или планшайбу (рисунок 1.8).
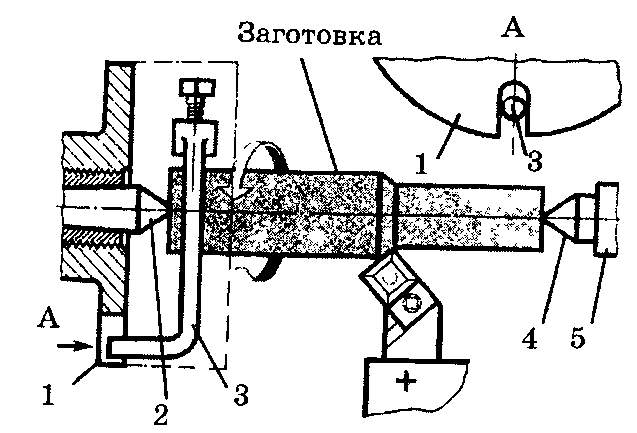
1 - поводковый патрон, 2 - передний центр, 3 - хомутик, 4 - задний патрон, 5 - пиноль задней бабки
Рисунок 1.9 - Обработка в центрах
При обработке в центрах, для придания вращения заготовке, применяют поводковые патроны (рисунок 1.9). При наружной обработке длинномерных заготовок малого диаметра с целью предотвращения прогиба используют неподвижный (рисунок 1.10, а) или подвижный (рисунок 1.10, б) люнеты.
Конические поверхности на токарном станке обрабатывают следующим способами: широким, токарным резцом, поворотом верхних салазок, смещением корпуса задней бабки в поперечном направлении и с помощью копирной или конусной линейки.