Добавлен: 22.11.2023
Просмотров: 80
Скачиваний: 2
ВНИМАНИЕ! Если данный файл нарушает Ваши авторские права, то обязательно сообщите нам.
в)Испытание аммиаком. Полые изделия заполняют сжатым воздухом с добавлением 1% аммиака, а швы закрывают бумагой, пропитанной 50% раствором азотнокислой ртути. При наличии неплотностей на бумаге появляются черные пятна.
г) Люминесцентный метод. Деталь погружают на 20…30 мин в смесь керосина и масла, а затем вытирают насухо и погружают в порошок магнезии, прилипающей в местах появления масла (над трещинами).
д) Испытание поливом. Подвергают громоздкие изделия, у которых есть доступ к швам с двух сторон. Одну сторону изделия поливают водой из шланга под давлением и проверяют герметичность швов с другой стороны.
е) При гидравлическом испытаниис давлением сосуд наполняют водой и создают избыточное давление, превышающее в 1,2 —2 раза рабочее давление. В таком состоянии изделие выдерживают в течение 5-10 минут. Герметичность проверяют по наличию влаги наливах и величине снижения давления. Все виды гидравлических испытаний проводят при положительных температурах.
3. Методы обнаружения внутренних дефектов. Для обнаружения внутренних дефектов сварного соединения – пор, трещин, непровара, вольфрамовых и шлаковых включений – используются различные виды неразрушающего контроля, основанные на различных физических явлениях, из которых в строительстве наиболее часто применяют: рентгено – и гаммаграфирование, ультразвуковая и магнитная дефектоскопия.
Рентгенографический метод контроля сварных соединений. Это наиболее совершенный метод определения качества сварных швов без их разрушения. Наиболее распространенные промышленные рентгеновские установки позволяют контролировать листовую сталь толщиной до 100 мм.
Рентгенографирование проводится в специальном помещении со свинцовой защитой обслуживающего персонала. Рентгеновские лучи явля-ются электромагнитными колебаниями с длиной волны 2х10-8…6х10-11 см. При просвечивании пучок рентгеновских лучей из трубки направляется на сварное соединение и, проходя через него, воздействует на фотопленку,
размещенную в кассете. Контроль швов основан на способности этих лучей проникать сквозь тела, поглощаясь в различной степени в зависимости от толщины и свойств материала.
1 – рентгеновская трубка;
2 – сварное соединение;
3 – кассета;
4 - фотопленка
Рис. 2. Рентгенографический контроль сварных соединений
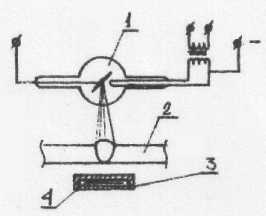
После проявления негативной пленки на ней видны
- сварной шов, более светлый, чем остальное поле пленки;
- трещины в виде резких, извилистых или зигзагообразных темных линий вдоль или поперек шва;
- непровар в виде резких прямых или пунктирных линий вдоль шва;
- поры, в виде округлых или вытянутых темных пятен или точек;
- шлаковые включения, в виде серых пятен неправильной формы;
- вольфрамовые включения в виде белых пятен неправильной формы или точек.
Дешифровка рентгенографических снимков производится на негатоскопе– фонаре с регулировкой силы и площади света и с местом для установки снимков.В заключении, составляемом по каждому снимку, указываются обнаруженные дефекты с помощью условных обозначений.
Гамма-излучатели обладают значительной интенсивностью и позволяют контролировать металл большей толщины. Но гамма-излучение представляет большую опасность при неосторожном обращении, поэтому пользоваться этим методом можно только после соответствующего обучения.
К недостаткам радиографического контроля относят тот факт, что просвечивание не позволяет выявить трещины, расположенные не по направлению основного луча.
Магнитные методы. Основаны на рассеивании магнитных потоков в дефектных местах изделия и позволяют выявлять мелкие трещины и поры шва. Для этого к изделию подключают сердечник электромагнита. На поверхность намагниченного соединения наносят железные опилки, окалину и т.д., реагирующие на магнитное поле. В местах дефектов на поверхности изделия образуются скопления порошка. Чтобы порошок легко перемещался под воздействием магнитного поля, изделие слегка постукивают, придавая мельчайшим крупинкам подвижность. Поле магнитного рассеивания можно фиксировать специальным прибором, называемым магнитографическим дефектоскопом. Качество соединения определяют методом сравнивания с эталонным образцом. Простота, надежность и дешевизна метода, а главное его высокая производительность и чувствительность позволяют использовать его при монтаже ответственных трубопроводов.
Ультразвуковой метод Ультразвуковой метод основан на использовании ультразвуковых колебаний, которые представляют собой колебания упругой среды со сверхвысокими частотами. Ультразвуковые волны способны проникать в металл на большую глубину и отражаться от неметаллических включений, находящихся в нем. | |
| |
![]() Рис. 3. Схема ультразвукового контроля: 1 - генератор ультразвуковых колебаний; 2 —пьезоэлектрический щуп; 3 — усилитель; 4 — экран дефектоскопа. ![]() Рис.4. Теневой и эхо-импульсный метод контроля. При теневом методе (рис. 4, а) ультразвуковые волны, идущие через сварной шов от источника ультразвуковых колебаний (щупа-излучателя), при встрече с дефектом не проникают через него, так как граница дефекта является границей двух разнородных сред (металл — шлак или металл — газ). За дефектом образуется область так называемой «звуковой тени». Интенсивность ультразвуковых колебаний, принятых щупом-приемником, резко падает, а изменение величины импульсов на экране электронно-лучевой трубки дефектоскопа указывает на наличие дефектов. Этот метод имеет ограниченное применение, так как необходим двусторонний доступ к шву. В ряде случаев требуется снимать усиление шва. При эхо-импульсном методе (рис. 4,б) щуп-излучатель посылает черезсварной шов импульсы ультразвуковых волн, которые при встрече с дефектом отражаются от него и улавливаются щупом-приемником. Эти импульсы фиксируются на экране электронно-луче- вой трубки дефектоскопа в виде пиков, свидетельствующих о наличии дефекта. Измеряя время от момента посылки импульса до приема обратного сигнала, можно определить и глубину залегания дефектов. Основное достоинство этого метода состоит в том, что контроль можно проводить при одностороннем доступе к сварному шву без снятия усиления или предварительной обработки шва. Этот метод получил наибольшее применение при ультразвуковой дефектоскопии сварных швов. | |
| |
Содержание отчета.
1.Зарисовать эскизы расположения внутренних и внешних
дефектов, объяснить причины их появления и сделать указания по
исправлению этих дефектов.
2.Ознакомиться со свойствами ультразвука и основами ультразвуковой дефектоскопии; зарисовать схемы проведения ультразвуковой дефектоскопии.
.
Контрольные вопросы.
1. Какие дефекты сварных соединений являются внешними и внутренними?
2. Что называют непроваром, наплывом, подрезом, шлаковым включением, пористостью, трещиной?
3. Какими методами контроля проверяют качество сварных швов?
4. Каковы причины образования разных видов дефектов?
5. Какие цели преследуются при разных способах контроля сварных швов?