Файл: Эксплуатационные повреждения и технология ремонта гребных винтов судов проекта Сормовский 488.docx
ВУЗ: Не указан
Категория: Не указан
Дисциплина: Не указана
Добавлен: 23.11.2023
Просмотров: 288
Скачиваний: 5
ВНИМАНИЕ! Если данный файл нарушает Ваши авторские права, то обязательно сообщите нам.
Обработка лопастей и статическая балансировка винтов. После сварки и наплавки поверхности лопастей гребного винта зачищают от брызг и шлака в районе трещин и раковин.
Усиление валиков фрезеруют заподлицо с поверхностью лопасти с помощью сменных фрез стенда ЭБП-М, как показано на рисунке 4.9. Сменив режущий инструмент на шлифовальные круги с зернистостью 46, производят черновую шлифовку наплавленной поверхности лопасти в районе трещин и кавитационных раковин.
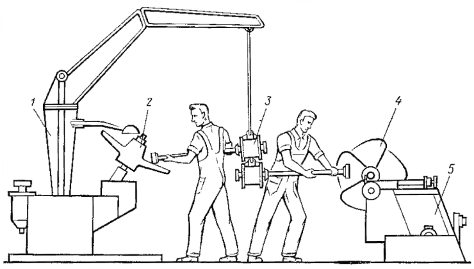
Рисунок 2.9 - Обработка лопастей и статическая балансировка винта на стенде ЭБП-М:1 - стенд ЭБП-М; 2 - обрабатываемый винт; 3 - электроборштанга; 4 - балансируемый винт; 5 - стенд БВ-100
По шаблонам, снятым с поврежденной лопасти, размечают контур лопастей, у которых кромки наплавлялись или на которых устанавливались наделки. С помощью цилиндрической фрезы такие лопасти обрезают по контуру; затем грушевидной фрезой и наждачным кругом кромкам лопастей придают нужный профиль. Контролируют его посредством кромочных шаблонов. На данном этапе обработки гребного винта проводят предварительную статическую балансировку его. Для этой цели винт переставляют с помощью тележки ТПВ-200 на вибростенд БВ-100 (Рисунок 4.10, а).
Установив винт на платформе стенда, приподнятой в верхнее крайнее положение, вставляют и закрепляют оправку в ступице. Платформу вибростенда опускают так, чтобы оправка легла на поверхность нерабочей пасти параллелей.

Рисунок 2.10. Использование тележки ТПВ-200 для транспортировки и установки винтов
Винт перекатывают на контрольные валики параллелей и поворотом его на 60 - 90° выводят из состояния равновесия. Затем, дав ему возможность остановиться, фиксируют «легкое место». Повторив эту операцию с поворотом винта в противоположную сторону, принимают средний угол и подбирают уравновешивающий груз (методом пробных грузов). Величина уравновешивающего груза составляет величину дисбаланса. Методом шлифовки или пневматической рубки дисбаланс в «тяжелом месте» снимают со ступицы или лопасти винта (на всасывающей поверхности), соблюдая плавность перехода поверхностей.
Обработанный винт должен находиться в состоянии безразличного равновесия. Допускаемый дисбаланс в соответствии с ГОСТ 8054 - 72 проверяют контрольным грузом массой 10 - 13 г.
Предварительно отбалансированный винт снимают с вибростенда и снова устанавливают на стенд ЭБП-М, где производят чистовую шлифовку и полировку поверхностей лопастей в районе ремонта. При этом обработку ведут войлочными или фетровыми кругами с наклеенными на них шлифзерном или шлифпорошком в такой последовательности: шлифзерном 80 - 125; шлифзерном 40 - 60; шлифпорошком 6 - 12; пастой ГОН.
После полировки лопастей винт переставляют на приспособление для развертки конусных отверстий (Рисунок 4.10, б) и проверяют конусность отверстия в ступице и шпоночного гнезда по калибрам. При наличии дефектов развертывают конусное отверстие с помощью пневматической машинки для вращения развертки и ручного винтового привода для вертикальной подачи. Шпоночное гнездо исправляют шабровкой по калибру или по штатной шпонке.
Выполнив все операции по слесарной обработке винта после наплавки и сварки, необходимо проверить геометрические параметры лопастей способами, применяемыми при дефектовании. При обнаружении отклонений, вызванных сварочными деформациями, винт повторно правят и затем направляют на окончательную статическую балансировку. Ее выполняют в той же последовательности, что и предварительную балансировку на вибростенде БВ-100, с той только разницей, что уравновешенность проверяют при включенном вибраторе. Это позволяет повысить чувствительность стенда и обеспечить применение нормы уравновешенности с массой контрольного грузика в 2 г на радиусе 305 мм.
Правка лопастей гребных винтов. Погнутость лопастей устраняют ручной или механической правкой с подогревом и в холодном состоянии. Подогрев значительно упрощает процесс правки, однако сопровождается остаточными деформациями после полного остывания винта. Эти деформации особенно заметны при местном нагреве лопасти газовой горелкой. Вследствие неравномерности нагрева в теле лопасти образуются остаточные напряжения, которые в период охлаждения приводят к деформациям.
Сильно загнутые кромки лопасти латунных винтов подогревают до 250 - 300 °С и с помощью специальных вилок, медной или свинцовой кувалды, струбцин и скоб выправляют вручную. Затем подают винт на холодную правку агрегатом АПВ-2.
Подбирают соответствующий данному винту блок штампов и устанавливают его на стол агрегата с помощью тележки ТПВ-200 (Рисунок 4.11).
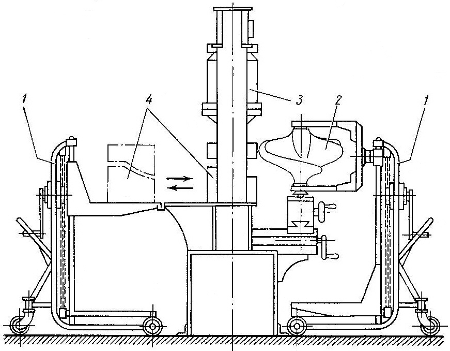
Рисунок 2.11 - Схема установки винтов и штампов на агрегат АПВ-2: 1 - тележка ТПВ-200; 2 - винт; 3 - агрегат; 4 - блок штампов
Установка винта на колонку суппорта показана на рисунке 4.11 справа.
Холодная правка винтов СПК на агрегате АПВ-2 выполняется в таком порядке:
перемещают каретку суппорта с гребным винтом до совпадения указателя с риской «поперечная подача»;
перемещают суппорт с винтом в сторону штампа до совпадения указателя с риской «продольная подача»; при этом для захода лопасти в штамп необходимо опустить пуансон с помощью плунжера пресса, наклонить или поднять винт, а также вращать его вокруг оси;
предварительно обжимают лопасть, добиваясь положения ее в штампе, как показано на рисунке 4.12, а;
включают в действие силовую установку и обжимают лопасть при усилии 50 - 60 тс, останавливают подачу масла в цилиндр и проверяют положение лопасти в штампе;
при правильном положении лопасти обжимают ее при полном усилии пресса 100 тс (стрелки манометра на красной черте);
поднимают плунжер в верхнее положение (пуансон под действием пружин также поднимается вверх) и выводят винт из штампа, пользуясь суппортом механизма подачи;
поворачивают на зажимной колонке винт вокруг своей оси и заводят следующую лопасть в штамп, соблюдая порядок, указанный выше;
правят следующую лопасть и т.д.
Если лопасть имеет местные вмятины, то ее правят с применением специальных прокладок (Рисунок 4.12, б), которые позволяют сосредоточить усилие пресса на площади вмятины.
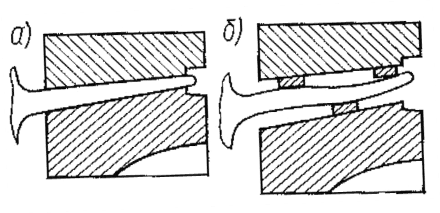
Рисунок 2.12 - Положение лопасти в штампе
Снятие и постановка гребного винта.
Для демонтажа гребного винта с вала вначале отгибают усы стопорной шайбы и свертывают гайку-обтекатель. Затем в гнездо ступицы винта ввертывают захват винтового или гидравлического съемников (Рисунок 4.13, а, б).
Гребные винты скоростных судов крепят на валу конусным соединением со шпонкой. Это соединение имеет ряд недостатков, и целесообразно было бы перейти к гидропрессовым бесшпоночным. Однако последние внедряются крайне медленно.
Для правильной работы шпоночного соединения у конусных сопрягаемых поверхностей необходимо создать натяг, эквивалентный примерно среднему значению легкопрессовой посадки. Подгонка конусов винта и гребного вала должна обеспечить посадку в пять-восемь пятен на площади 2525 мм; щуп 0,03 мм не должен проходить более чем на 10 мм между телом ступицы и конусом вала. Во время ремонта очень трудно выполнить качественную подгонку из-за расхождений размеров конусных поверхностей вала и винта при их замене, из-за провала шпонки и отсутствия средств контроля натяга.
При большой частоте вращения винта открытые и контактные конусные поверхности интенсивно изнашиваются в потоке воды с взвешенными в ней частицами. Происходит ослабление посадки, что приводит к необходимости частого контроля и восстановления натяга за счет более глубокой насадки винта на конус вала.
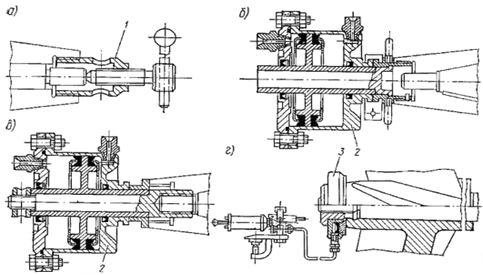
Рисунок 2.13 - Снятие гребного винта с вала и посадка его на вал: 1 - винтовой съемник; 2 - универсальный гидравлический съемник-домкрат; 3 - кольцевой гидравлический домкрат
Жидкая смола заполняет все зазоры между винтом и валом, после отверждения создает монолитность соединения и повышение запаса прочности по вращающему моменту до 20%. В таком соединении полностью исключается подтекание и циркуляция воды на контактных поверхностях.
Технология сборки включает операцию нанесения смолы, которую готовят в таком соотношении с отвердителем, чтобы ее живучесть была не более 1 ч. Поверхности вала и винта перед нанесением слоя смолы должны быть обезжирены уайт-спиритом. Шпоночный паз располагают во время сборки винта с валом вверху, чтобы улучшить условия заполнения неплотностей выхода шпоночного паза.
Для съема винта, насаженного на эпоксидной смоле, нагревают ступицу винта до температуры, при которой смола частично плавится и размягчается. При нагреве двумя горелками винт снимают без особых затруднений за 15 мин. Применение эпоксидной смолы позволяет собирать детали без взаимной подгонки. Это особенно важно в период навигационных ремонтов, когда гребной вал не демонтируют.
Наиболее распространенным способом обеспечения натяга при посадке винта является затяжка его посредством гайки-обтекателя с применением рычагов большой длины и ударов кувалды. Этот способ является не только малопроизводительным и физически тяжелым, но и может привести к нарушению прямолинейности вала, изгибу в районе большого конуса и даже к смещениям концевого кронштейна. Поэтому рекомендуется применять затяжку винтов с помощью гидравлических домкратов.
Маршрутная карта на восстановление гребного винта
Результаты испытаний
Расчет экономической эффективности
Прогнозирование долговечности гребных валов
Заключение
В работе была рассмотрена проблема эксплуатационных повреждений гребных винтов судов проекта Сормовский 488. Была представлена технология ремонта гребных винтов, а также был произведен анализ эксплуатационных повреждений и причин их возникновения. Исходя из результатов работы, можно сделать вывод о том, что для предотвращения повреждений гребных винтов необходимо проводить регулярный контроль и техническое обслуживание судна, а также выбирать оптимальные условия для его эксплуатации. Технология ремонта гребных винтов также является важным аспектом, и необходимо выбирать оптимальные методы восстановления гребного винта для повышения его эксплуатационных характеристик и удлинения срока службы.