Файл: Министерство образования российской федерации уральская государственная горногеологическая академия.rtf
Добавлен: 23.11.2023
Просмотров: 241
Скачиваний: 3
ВНИМАНИЕ! Если данный файл нарушает Ваши авторские права, то обязательно сообщите нам.
Слив гидроциклона, работающего на медном промпродукте, поступает на сгущение в девятиметровом сгустителе до 22-28% твёрдого, после чего подвергается дофлотации с выделением в пенный продукт медных минералов, а в хвосты - цинковых и пирита. Пенный продукт вместе с медным грубым концентратом направляется на первую медную перечистку. Хвосты флотации поступают вместе с грубым цинковым концентратом на его перечистку.
По схеме представленной на рис. 2.2. на фабрике получают медные концентраты с содержанием Cu-14,8%; Zn-5,8%; при извлечении меди -88%; цинковые концентраты с содержанием Cu -1,4%, Zn-50,4% при извлечении Zn-52,5%; в пиритном концентрате содержится меди -0,26%, цинка -0,53%, серы -44,8%, при извлечении серы -50%.
Схема переработки вкрапленной руды на Кировоградской фабрике
Руда
Складирование
Измельчение I
Классификация I
Классификация II
Измельчение II Классификация в
гидроциклонах
Коллективная флотация
Сгущение
Перечистная Грубая Cu флотация
Контрольная Измельчение
отвальные Классификация
хвосты
Основная Cu флотация
Грубая Cu флотация
Контрольная I Перечистная
Основная Zn флотация II Перечистная
I Перечистная
II, III Перечистная
пиритный к-т цинковый к-т медный к-т
Рис. 2.2
Месторождения медно-цинковых руд за рубежом сосредоточены в основном в Канаде, Финляндии, Норвегии, Швеции и Японии. Медно-цинковые руды Канады в основном вкрапленные. Соотношение меди и цинка в них составляет в них от 1:1,5 до 1:6, что является благоприятным для их извлечения. Сульфидные минералы - халькопирит; сфалерит и пирит - крупно и равномерно вкраплены в пустой породе, поэтому они освобождаются при измельчении дол 70-80% класса -0,074 мм.
Зарубежный опыт переработки вкрапленных медно-цинковых руд представлен обогатительной фабрикой “Квемонт” (Канада). Руда поступающая на фабрику содержит 1,5% Cu; 2,7% Zn; 25% S; 5 г/т Au; 26 г/т Ag. Схема и технологический режим на фабрике весьма своеобразен. Руда после первой стадии измельчения и классификации направляется в аэратор. Слив аэратора крупностью 9,3% +0,3 мм и 44,9% класса -0,074 мм поступает в основную медную флотацию. При этом стремятся получить готовый медный концентрат с максимально возможным извлечением золота. Пески аэратора направляют во вторую стадию измельчения. Медный промпродукт в виде песков из аэратора возвращается не в шаровую мельницу второго цикла, а в стержневую первого цикла. В этом случае при наличии рудных солей в пульпе лучше депрессируется цинковая обманка. Эта струя песков, насыщенная кислородом, создаёт благоприятные условия подготовки пульпы к флотации, т.к. количество кислорода в пульпе стержневой мельницы меньше, чем в шаровой. Аэрация медного грубого концентрата перед перечисткой введена для повышения извлечения: при аэрации флотируемость цинковой обманки (сростков) с халькопиритом повышается и увеличивается извлечении меди. На фабрике используют следующие реагенты: в измельчении (стержневая мельница) - сода 1 кг/т, сульфит натрия - 500 г/т (делится между стержневой и шаровой мельницей), цианид 35г/т (частично в аэратор), пентазоламиловый ксантогетат 30 г/т (в аэратор 10 г/т аэрофлота); в медной флотации - вспениватель (сосновое масло) по ходу процесса 235 г/т; в цинковой флотации медный купорос 350 г/т, известь 400 г/т (в перечистку), сульфат аммония 300 г/т, цианид 10 г/т (в аэратор), аэрофлот 10 г/т, пентазоламиловый ксантогенат 10 г/т, вторичный бутиловый спирт 30 г/т; в медно-пиритной флотации - этиловый ксантогенат; в промпродуктовой (золото пиритной) флотации - медный купорос 100 г/т, амиловый ксантогенат 400 г/т, изопропиловый ксантогенат 20 г/т, вторичный бутиловый спирт 20 г/т, реагент № 242 60 г/т (нейтра-лизовнный аммиаком аэрофлот).
По схеме представленной на рис. 2.3. на фабрике получают: медные концентраты с содержанием Cu-19,1%; Zn-3,65%; Au-28 г/т; Ag-168 г/т; цинковые концентраты с содержанием Zn51%; Cu-1.61%; Au-3 г/т; Ag-45 г/т; при извлечении Zn-75%; Cu-2%; Au-2,2%; Ag-5%.
Схема обогащения на фабрике “Квемонт” Канада
Руда
Измельчение
Классификация
Аэроклассификация
I Cu флотация Измельчение
II Cu флотация
Аэрация III Cu флотация
Флотация Аэроклассификация
Аэрация
Флотация Классификация
Zn флотация
Классификация Zn флотация
Измельчение
Cu и FeS2 флотация
На цианирование
Измельчение
Аэрация FeS2 и Au флотация
Перечистная
Медный к-т Цинковый к-т Хвосты
Рис. 2.3
3. ТЕХНОЛОГИЧЕСКАЯ ЧАСТЬ
.1 ВЫБОР И ОБОСНОВАНИЕ ТЕХНОЛОГИЧЕЧСКОЙ СХЕМЫ ОБОГАЩЕНИЯ
При обогащении руды, она подвергается механической обработке, при которой не изменяет основных химических качеств, в отличие от металлургических процессов. Исходя из различных физико-химических свойств минералов, применяют различные методы обогащения. Основными в переработке многих типов полезных ископаемых являются флотационные методы. Они используются при обогащении более 95% руд цветных металлов. Возрастающее значение флотационных методов обогащения в настоящее время обусловлено вовлечением в переработку бедных, тонковкрапленных и труднообогатимых руд. Руда Гайского месторождения является тонковкрапленной и другого технологического процесса обогащения, который был бы в состоянии конкурировать с флотацией, нет.
Флотация - процесс универсальный, так как не существует принципиальных ограничений в отношении возможности ее применения для разделения любых минералов, поскольку все они имеют разные значения удельной свободной поверхностной энергии. Универсальность обеспечивается и тем, что если природная разница в значениях удельной поверхностной энергии у разделяемых минералов невелика и недостаточна для разделения, то она может быть увеличена с помощью флотационных реагентов, избирательное закрепление которых на поверхности определенных минералов изменяет их поверхностную энергию в заданном направлении.
При выборе, обосновании и разработке схемы обогащения учитываем характер и размер вкрапленности полезных минералов, их содержание в руде и флотируемость, наличие и характер шламов, требование к качеству концентратов, необходимость комплексного использования сырья при минимальных затратах на обогащение.
.1.1 Выбор и обоснование схемы дробления
Операции дробления применяются для подготовки полезного ископаемого к измельчению в мельницах. Схемы дробления включают одну, две, три и более стадии дробления.
Для выбора рациональной схемы дробления из большого числа возможных схем необходимо решить следующие вопросы: о числе стадий дробления; о необходимости операций предварительного и поверочного грохочения в отдельных стадиях дробления.
Число стадий дробления определяется начальной и конечной крупностью дробимого материала. При заданных размерах максимальных кусков в руде и в дробленом продукте предел общей степени дробления будет

Степень дробления i = 61,5 не может быть достигнуто в одну стадию, поэтому число стадий должно быть не менее двух. Но две стадии дробления могут обеспечить только молотовые дробилки, а не щековые и конусные. Учитывая нормы технологического проектирования флотационных фабрик, разработанных институтом "Механобр", а также практику, работу отечественных фабрик, принимаем три стадии дробления.
Операции предварительного грохочения применяются для сокращения количества материала, поступающего в дробление, за счет отсева мелочи и увеличения поверхности материала в рабочей зоне дробилки.
Принимая во внимание, что построенные в последние годы крупные отечественные фабрики цветной металлургии отказались от предварительного грохочения перед первой стадией дробления, и исходный материал относительно сухой, предварительное грохочение предусматривать не будем. Этим самым уменьшим капитальные затраты на строительство фабрики и упростим эксплуатацию отделения крупного дробления.
Если дробилки среднего дробления, связанные с дробилками мелкого дробления, имеют большой запас производительности по сравнению с последними и обеспечивают производительность без отсева мелочи, то предварительное грохочение не предусматривается. В остальных случаях применение грохочения обязательно. В последней стадии дробления при малых выходных щелях предварительное грохочение должно применяться.
Операции поверочного грохочения имеют целью возвратить в дробилку избыточный продукт. Крупность продукта 13 мм, оптимальная для измельчения в шаровых и стержневых мельницах, может быть получена на конусных дробилках мелкого дробления только в замкнутом цикле с грохотом. Поэтому в последней стадии дробления необходимо включить операцию поверочного грохочения. Замкнутый цикл дробления с грохочением, конечно, сложнее открытого с предварительным грохочением. Включение поверочного грохочения вызывает необходимость установки грохотов, конвейеров. В цехе появляются дополнительные перегрузки. Все это приводит к увеличению затрат. Но отказаться от замкнутого цикла возможно лишь при условии увеличения крупности питания мельниц, а при этом общая стоимость дробления и измельчения на фабрике возрастает.
Из вышесказанного видно, что более рациональной в экономическом отношении и эксплуатации будет схема, представленная на рис.3.1. Это подтверждается и практикой дробления на Учалинской, Башкирской, Гайской фабриках, где предварительное грохочение перед второй стадией дробления не предусматривается, а в третьей стадии дробления используется совмещенное предварительное и поверочное грохочение.
Вещественный состав, физико-химические свойства и обогатимость руд различных участков месторождения значительно отличаются. Усреднение руды позволяет повысить извлечение металлов. Для усреднения руды строят склады дробленой руды, применяя при этом усреднительные машины.
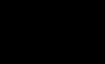
Рис.3.1
3.1.2 Выбор и обоснование схемы измельчения
Для флотации важно раскрыть ценные минералы, освободить основную их часть от сростков с минералами пустой породы, и в то же время не переизмельчать ценные минералы, так как образование шламов может резко ухудшить технологический процесс и снизить его показатели. Получение класса минус 0,071мм с содержанием его до 90% представляется трудно возможным при двухстадиальной схеме измельчения. Учитывая практику работы отделений измельчения Башкирской, Гайской фабрик [2], перерабатывающих аналогичную руду, принимаем трехстадиальное измельчение.
Измельчение руды перед флотацией проводится в сочетании с классификацией. Предварительная классификация исходного материала перед измельчением применяется для выделения из него уже готового по крупности продукта, если его значение не менее 15%. В руде, поступающей на измельчение, содержание класса минус 0,071 мм незначительное, поэтому предварительную классификацию в первой стадии измельчения не предусматриваем.
Во второй и третьей стадии предусматриваем поверочную классификацию в замкнутом цикле. Она применяется для контроля крупности измельченного продукта, повышения производительности мельницы, уменьшения ошламования продукта при измельчении. При наличии поверочной классификации некондиционный продукт возвращается обратно в мельницу, в питании мельницы увеличивается содержание класса, вследствие чего возрастает ее производительность по готовому классу. Важнейшим условием достижения высокой производительности мельниц при измельчении является правильное распределение работы измельчения между мельницами предыдущей и последующей стадий. Если на мельницу предыдущей стадии будет выдаваться слишком мелкий материал, то мельница следующей стадии окажется недогруженной, а общая производительность мельниц понизится. Выдача из предыдущей стадии измельчения слишком крупного материала тоже вызовет снижение общей производительности, вследствие перегрузки мельницы последующей и недогрузки предыдущей стадии измельчения.
Максимальная производительность мельниц достигается только при определенной крупности слива гидроциклонов (классификаторов) второй стадии измельчения, которая на практике регулируется изменением его плотности. Работа гидроциклонов при очень плотных сливах неустойчива, так как небольшое измельчение в количестве подаваемой воды значительно отражается на крупности материала, уходящего в слив, и нарушает правильное распределение работы измельчения между стадиями. Операции предварительной и поверочной классификации в третьей стадии измельчения совмещены в схеме, изображенной на рисунке 3.2. и разделены на рис. 3.3.