Файл: Методы окончательной обработки отверстий в деталях типа тел вращения. Эскизы базирования и наладки.odt
ВУЗ: Не указан
Категория: Не указан
Дисциплина: Не указана
Добавлен: 23.11.2023
Просмотров: 17
Скачиваний: 2
ВНИМАНИЕ! Если данный файл нарушает Ваши авторские права, то обязательно сообщите нам.
Задание: Методы окончательной обработки отверстий в деталях типа тел вращения. Эскизы базирования и наладки.
В машиностроении обычно для соединения деталей между собой применяются различные детали с отверстиями. Отверстия по форме бывают цилиндрические, конические, квадратные, прямоугольные, центровые, ступенчатые, глубокие, глухие, шлицевые и пазовые.
Ступенчатые - это отверстия с общей осью и разными последовательно рас-положенными диаметрами. Глубокими называются отверстия, у которых диаметр значительно меньше длины, приблизительно в 5 раз и более. Отверстия, открытые с одной стороны, называются глухими, а с трех - пазами . Фасонные отверстия бывают квадратными, шестигранными, многогранными, шлицевыми и т. д.
К обработке отверстий предъявляют следующие технические требования: а) размеры должны удовлетворять заданным классу точности и шероховатости; б) ось внутренних поверхностей должна быть прямолинейной; в) поверхность должна соответствовать чертежу по всей длине; г) должна быть соблюдена соосность поверхностей; д) расстояния между осями поверхностей и от заданных баз должны быть выдержаны в пределах допусков.
Сверление, зенкерование, развертывание и зенкование отверстий.
Сверление. Наиболее распространенным способом образования отверстий является сверление с помощью специального инструмента - сверла. Сверло, как и другие режущие инструменты, работает по принципу клина. Для осуществления процесса резания ему необходимо сообщать одновременно два движения: вращательное - относительно его геометрической оси, которое является главным движением ,и поступательное - вдоль оси, являющееся подачей (рис. 1,а).
Точность сверления отверстий невысока и равна для небольших диаметров приблизительно 0,1 мм, а для больших - около 0,25 мм. Чтобы просверленные отверстия были более точными, а также, чтобы придать им специальную форму, применяют дополнительную обработку - зенкерование, развертывание и зенкование.
Зенкерование выполняют с помощью специальных многолезвийных инструментов - зенкеров (рис. 1,б), в результате чего образуется углубление необходимо формы и размеров. Обычно углубления делают конической или цилиндрической формы для размещения в них головок болтов, заклепок и других деталей. Зенкование выполняют с помощью многолезвийного режущего инструмента - конической зенковки (рис. 1, б).
Цекование выполняют торцовым зенкером (насадным или специальным) нековкой поверхности отверстия под головку болта или гайку.
Развертывание. Развертыванием называется чистовая обработка резанием отверстий для придания им высокой точности и низкой шероховатости. Развертыванием обрабатывают обычно цилиндрические отверстия и реже конические. Выполняют развертывание с помощью специальных инструментов - разверток. По форме развертка напоминает зенкер.
Характер ее работы такой же, как и зенкера, но точность обработки получается намного выше благодаря наличию большого числа режущих кромок.
Зенкование. Зенкование - получение конических или цилиндрических углублений вокруг отверстий, снятие фасок по краям отверстий (обычно под головки винтов или шурупов). Зенкование применяют также для удаления острых кромок (гратов) на краях отверстий.
Растачивание отверстий. Растачивание отверстий выполняют расточными резцами на токарных и расточных станках. На рис. 2 показаны установка резца и последовательность растачивания отверстия. Необходимо помнить, что после растачивания отверстия резец следует перемещать к центру отверстия, чтобы между вершиной резца и обрабатываемой поверхностью образовался зазор. Это необходимо для того, чтобы не поцарапать резцом обработанную поверхность. Продольное перемещение суппорта при обработке глубоких отверстий можно определить, помечая мелом на стержне резца длину растачиваемого отверстия. Продольное перемещение резца прекращают при совпадении метки с торцом заготовки. Глубину резания при растачивании определяют также, как и при обработке наружных поверхностей.
Протягивание отверстий. Протягивание - производительный метод обработки отверстий с помощью протяжки или прошивки. Протяжки и прошивки - это многорезцовые инструменты в виде стержней или полос, на поверхности которых располагаются зубья с постепенно увеличивающейся их высотой от зуба к зубу. При прямолинейном движении протяжки припуск снимается каждым зубом равномерными слоями за один ход или оборот.
Название инструменты получили от способа воздействия на них при обработке. Так, протяжку протягивают через отверстие (рис. 3, а) а прошивкой (рис. 3, б) как бы пробивают отверстие.
Протягиванием обрабатывают отверстия различных профилей (рис. 4) на горизонтально - и вертикально протяжных станках. Производительность процесса обработки в 8-9 раз выше, чем при развертывании отверстий. К недостаткам протягивания относятся высокая стоимость протяжек, значительная сила резания, деформирующая тонкостенные детали, невозможность обработки деталей значительных размеров, трудность точно координировать положение оси обрабатываемого отверстия относительно других поверхностей.
Внутреннее круглое шлифование. Шлифование применяют в основном для окончательной обработки отверстий в закаленных деталях и деталях с поверхностями неравномерной твердости, когда отверстие нельзя обработать другим способом (тонкостенных деталях, глухих отверстиях, шлицевых и шпоночных канавках и т. п.).
Различается шлифование отверстий во вращающейся (рис. 5, а, б), в неподвижной (рис. 5, в) деталях и бесцентровое шлифование. Сущность процесса ясна из рисунка и заключается в относительном перемещении детали или вращающегося шлифовального круга в продольном и поперечном направлениях и снятии при этом слоя стружки с внутренней поверхности обрабатываемой детали.
В случаях, когда по техническим условиям требуется высокая точность обрабатываемой поверхности, когда ее невозможно достичь шлифованием, прибегают к отделочно-доводочным операциям: притирке, хонингованию, полированию и т. п.
Притирка и доводка отверстий. Притиркой называется доводочная опера-ция, применяя которую, можно получить шероховатость поверхности Rz = 0,025 мкм и точность 1-го класса. Сущность процесса заключается в удалении шерохо-ватостей притиром при наличии абразивного материала. Притир - это чугунные или медные бруски, насаженные на оправку. Бруски могут разжиматься с помощью пружин или конусов. При подготовке притира к работе рабочие поверхности брусков «насыщаются» абразивным мелким порошком, смешанным со смазкой (масло, керосин и др.). Можно также наносить слой абразива в виде пасты (60-70% карбида бора и 30-40% парафина). Для окончательной доводки применяют пасты ГОИ, состоящие из окиси хрома (74-81%).
Оправку с подготовленными к притирке брусками помещают в обрабатываемое отверстие, сообщая ей вращательное и возвратно-поступательное движение. Процесс резания осуществляется на доводочных станках и сходится к истиранию слоя металла отверстия зернами притира. Притирка отверстий в результате низкой производительности применяется редко.
Хонингование. Для окончательной обработки отверстий в точном машиностроении применяют производительный способ - хонингование. Это отделочная обработка отверстий на хонинговальных станках раздвижными абразивными брусками, встроенными в хон. Хон состоит из стального корпуса с механизмом для подачи абразивных брусков. Хон может быть с ручной, механической и гидравлической подачей. Несколько брусков
находятся в разжимной головке в колодках, которые принудительно раздвигаются двумя конусами с помощью пластин. Процесс хонингования заключается в том, что хон вводят в отверстие. Хон, вращаясь, производит перекрестно возвратно-поступательное винтовое движение резания, обеспечивая высокую точность обработки и требуемую шероховатость. Хонингование применяют для получения высокой точности отверстий, что способствует повышению надежности и долговечности деталей машин.
Для предохранения поверхностей от ржавления, повышения долговечности, придания блеска и красоты внешнему виду производят полирование вращающимися мягкими полировальными кругами или лентами на полировальных станках.
Понятие о центровании отверстий. При изготовлении разнообразных деталей типа валов базой для крепления заготовки при обтачивании, нарезании резьбы, шлифовании, нарезании шлицев, контроля правильности изготовления детали служат центровые отверстия. Эти отверстия также являются базами при выполнении ремонта (обтачиванием), например, таких деталей, как оси транспортных машин. Кроме того, их используют не только при обработке сверл, зенкеров, метчиков и т. д., но и для проверки заточки и переточки режущих инструментов. Поэтому центровые отверстия следует выполнять весьма тщательно в соответствии с требованиями ГОСТ 14034-74.
Отверстия типа А должны иметь цилиндрическую часть малого диаметра d и коническую поверхность большего диаметра D с углом перехода на конус, равным 60°, а отверстия типа Б должны дополнительно еще иметь вторую коническую поверхность с большим диаметром D0 и углом конуса при вершине 120°. ГОСТ 14034-74 предусматривает центровые отверстия с выпуклыми дуговыми образующими несущего конуса, которые обеспечивают снижение погрешности установки детали в центрах.
Центровые отверстия получают обработкой резанием на вертикально - и горизонтально-сверлильных, токарных и револьверных станах, на специальных фрезерно-центровочных и одно - или двусторонних центровочных станках. Для получения при центровке цилиндрических отверстий применяют спиральные сверла, а для конических - зенковки, но чаще применяют специальные центровочные сверла, которые обрабатывают одновременно цилиндрическую и коническую поверхности.
Возможны и другие варианты обработки центровых отверстий, из которых наиболее приемлемые - это применение специальной инструментальной головки. Наиболее высокопроизводительным и точным методом центрования отверстий является обработка на агрегатном двустороннем станке.
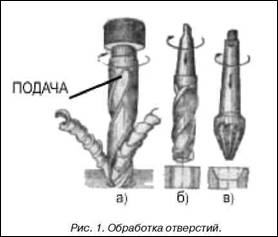
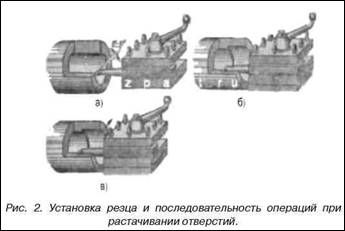
а - установка резца; б - растачивание отверстия; в - подрезка уступа
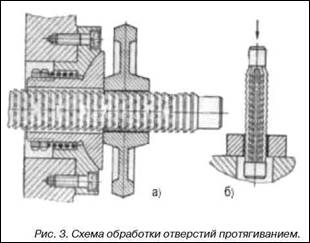
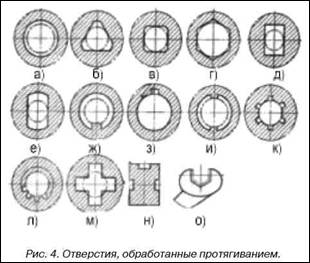
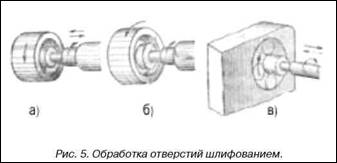
Номенклатура мерных инструментов весьма разнообразна. На рисунке 6. приведена классификация мерных инструментов по следующим признакам:
- по способу взаимодействия инструмента с обрабатываемой заготовкой;
- относительной глубине обрабатываемых отверстий (L/D);
- способу базирования инструмента в обрабатываемом или обработанном отверстиях.
- на режуще-деформирующие;
- на деформирующие.
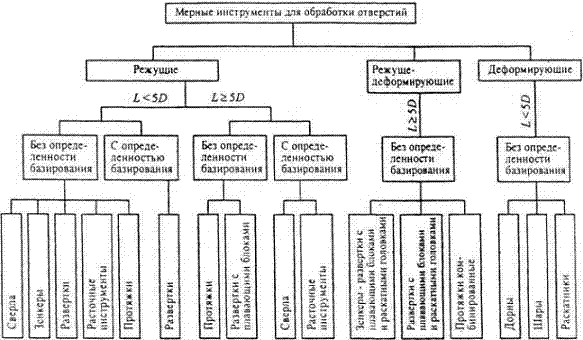
Рис. 6. Классификация мерных инструментов для обработки отверстий
Основным отличием в этом разделении является то, что обработка отверстий режущими инструментами происходит со стружкообразованием, а деформирующих – без снятия стружки.