Файл: азастан республикасыны ауыл шаруашылыы министрлігі.docx
ВУЗ: Не указан
Категория: Не указан
Дисциплина: Не указана
Добавлен: 04.12.2023
Просмотров: 51
Скачиваний: 1
ВНИМАНИЕ! Если данный файл нарушает Ваши авторские права, то обязательно сообщите нам.
Станокты бос жүрісте сынау кезінде бірқатар элементтердің паспорттық деректерге сәйкестігін тексеру қажет. Оларға мыналар жатады:
а) машинаның негізгі өлшемдері;
б) Электр қозғалтқыштарының, гидравликалық сорғылардың, гидравликалық қозғалтқыштардың және пневматикалық жабдықтардың сипаттамалары;
в) айналым, Қос жүріс және беріліс сандары;
г) гидравликалық механизмдердегі қысым;
д) жетек белдігінің мөлшері мен Материалы;
е) станокқа керек-жарақтардың болуы және т. б.
Станокты бос жүрісте сынамас бұрын барлық жобалық циклдарды, негізгі қозғалыстың барлық жылдамдықтарын, негізгі қозғалыс жылдамдықтарының біріндегі барлық жылдамдықтарды және жылдам қозғалыстарды дәйекті қосу арқылы оның барлық басқару органдары сынақтан өткізілуі керек. Станокты сынау кезінде станок механизмдерінің өзара әрекеттесуінің дұрыстығы тексеріліп, одан әрі сынақтарды апатсыз жүргізу мүмкіндігі анықталуы керек. Станокты бос жүрісте сынау оның барлық жұмыс жылдамдықтарын — ең төменнен ең үлкенге дейін дәйекті түрде қосу арқылы жүзеге асырылады. Ең жоғары жылдамдықта машина кем дегенде екі сағат бойы үздіксіз жұмыс істеуі керек. Барлық жұмыс иннингтері қосылған кезде, сондай-ақ бар болса, жылдам беру кезінде иннинг механизмі бос тұрғанда сыналуы керек. Шпиндель мойынтіректерінің температурасы оның ең көп айналымы кезінде 60-тан аспауы керек.Слайд мойынтіректері үшін °С және барлық машиналарда домалау мойынтіректері үшін 70°С. Сырғанау мойынтіректеріне орнатылған шпиндельдері бар тегістеу станоктарында 70°C дейін қыздыруға рұқсат етіледі. басқа механизмдерде мойынтіректердің температурасы 50°C-тан жоғары көтерілмеуі керек. Осыдан кейін олар машинаны статикалық күйде тексере бастайды.
Қаттылық-тұрақты жұмыс режимінде жүктеме кезінде машинаның дәлдігін анықтайтын машинаның жұмысының негізгі өлшемдерінің бірі. Станоктың қаттылығын статикалық әдіспен анықтауға болады, яғни жұмыс істемейтін станоктың тораптарын жүктеу және өндірістік әдіс - жұмыс істейтін станоктың қаттылығын сынау арқылы.
4.2 Сынақ жүргізуге арналған жабдықтар мен аспаптар. Өлшеу құралдары
Қаттылықты сынау үшін арнайы құрылғылар қолданылады. Әр құрылғының негізгі бөліктері-жүктеме құрылғысы (жүктеме индикаторы бар алдын-ала безендірілген динамометр) және қозғалыс индикаторлары (сурет.4).
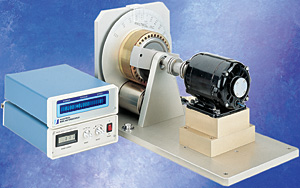
Сурет 4 – Динамометр HD-700-1 [9]
Тексеру кезінде, әдетте, берілген жүктеме күшімен оның құрал-саймандары мен өңделетін дайындаманың салыстырмалымещысуымен сипатталатын машинаның жалпы икемділігі өлшенеді. Ең үлкен рұқсат етілген орын ауыстыруды қалыпқа келтіріңіз (яғни қаттылықтың төменгі шегі). Тек жалпы сәйкестікті білу әрдайым жеткіліксіз. Сондықтан машинаның прототипін сынау кезінде серпімді қозғалыстардың тепе-теңдігі жасалуы мүмкін. Ол үшін статикалық жүктеме кезінде өлшенеді, содан кейін қолдану нүктесіне қайта есептеледі: машинаның серпімді жүйесі элементтерінің қозғалу күштері.
4.3 Үлгiлердi сынауға дайындау
Қабылдау сынақтарының алдында станоктар арнайы іргетасқа орнатылады. Реттеу сыналары мен аяқ киімдердің көмегімен бойлық және көлденең бағытта деңгей бойынша салыстыру жүргізіледі, бірақ іргетас болттары қатаймайды.
4.4 Өнiмдi сынау әдістемесі
Статикалық әдіс станоктың тораптарын деформацияларды өлшеу өндірісімен станоктың жұмыс процесінде пайда болатын күштерге сәйкес келетін күштермен біртіндеп жүктеуден тұрады. Өндірістік әдіспен қаттылықты сынау әр түрлі кесу тереңдігімен және кесу режимінің өзгермейтін басқа параметрлерімен дайындаманы өңдеу процесінде жүзеге асырылады. Өңдеу қысқа учаскелерде жүзеге асырылады, содан кейін өңделген беттегі жиектің биіктігі өлшенеді. Жиектердің мөлшерінің айырмашылығы кесу тереңдігіне байланысты дайындаманың әр түрлі қысылуының салдары болып табылады. Бөлшектің қысылуы неғұрлым аз болса, қателік соғұрлым аз болады, машинаның қаттылығы немесе техно-логикалық жүйенің қаттылығы соғұрлым жоғары болады (сынақ кезінде дайындаманың деформациясы ескерілмейді).
Қаттылықты тексеру нәтижелері жеткілікті сенімді және объективті болуы үшін, мүмкін болса, сынақтардың қарапайымдылығы үшін машинаның статикалық жүктемесін қолдана отырып, өңдеудің ең типтік нақты жағдайларына жақындау қажет. Жүктеме күшінің қолдану нүктесінің басқару элементтері мен координаттары әдеттегі өңдеу жағдайында кесу күшінің қолдану бағыты мен нүктесіне сәйкес келуі керек. Жүктеме күші 0,01 мм бөлу бағасымен қалыпты индикатор арқылы дәл бекітуге болатын қозғалыстарды тудыру үшін жеткілікті болуы керек, бірақ ол сыналатын машина үшін рұқсат етілген жүктемеден аспауы керек. Станокта қозғалатын түйіндердің белгілі бір типтік орналасуы ұсынылады. Буындарды реттеудің сапасын бағалау үшін жүктеменің бастапқы талаптары сақталуы керек (станок тораптарын берілген позицияларға орнатқаннан кейін бірден жүктеме Туралы) [9].
Машинаның жұмыс қабілеттілігінің маңызды критерийлерінің бірі-оның дірілге төзімділігі, оны машинаның кесу кезінде автоматты тербелістердің пайда болуына қарсы тұру қабілеті деп түсінуге болады. Станоктарды сынау бағдарламасы жұмыс кезінде кесу процесінің тұрақтылығының шекараларын бағалауды қамтамасыз етеді. Сынақ tnp шекті чиптерін анықтауға дейін азаяды. Шекті чиптер деп дірілсіз жұмыс кезінде алынатын максималды кесу тереңдігі түсініледі. Станоктың прототиптері үшін өңдеудің барлық түрлеріне және бірнеше берілістерге тән шпиндельдің айналу жиілігіне байланысты шекті чиптер анықталады. Мысалы, токарлық станоктарға тән өңдеу түрлері-орталықтардағы біліктің бойлық бұралуы, консольмен бекітілген біліктің өңделуі және сақинаның соңы.
Сынақтардың басында машинаның геометриялық дәлдігін тексеру машинада өңдеу дәлдігіне жанама кепілдік береді. Сондықтан өңделген беттің өңдеу дәлдігі мен кедір – бұдырлығын тікелей бағалау үшін станокты сынау бағдарламасы бақылау үлгісін өңдеуді қарастырады (CNC станоктары үшін-үлгілер партиясы). Үлгінің түрі, оның материалы, өңдеу сипаты мен режимі, құралды бекіту және т. б. машинаның сапасына тікелей қатысы жоқ факторлардың әсерін азайту және өңдеудің ең жоғары дәлдігін алу үшін осындай есептеумен тағайындалады. Үлгінің нақты өлшемдері мен пішінінің, сондай-ақ оның бетінің микрогеометриясының параметрлерінің ауытқулары тиісті МЕМСТе көрсетілген шамалардан аспауы тиіс.
Тексерулердің үшінші тобына жоғарыда сипатталғандай жүктеме кезінде машинаның Шу өнімділігін тексеру кіреді. Шу өнімділігін тексерудің мақсаты-машинаның шу деңгейі рұқсат етілген мәннен аспайтындығын анықтау. Рұқсат етілген мәндер 15 адам құлағының әртүрлі жиілік диапазонындағы шуларға сезімталдығына байланысты белгіленеді (90 дБ дейін – 350 Гц – тен төмен жиіліктер үшін, 75 дБ дейін-4 кГц-тен жоғары жиіліктер үшін). Шуды бағалау үшін адамның құлағы сияқты дыбысқа жауап беретін Шу өлшегіштер қолданылады. Шу әдетте шпиндельдің ең жоғары жылдамдығымен өлшенеді.
4.5 Сынау нәтижелерін өңдеу
Станоктарды сынау және сапасын бақылау әдістемесін жасау сынау мен бақылаудың негізі болды. Тест және бақылау нәтижелері төменде берілген. Бірінші кезең станоктарды бос тұрып сынау, механизмдердің жұмысын тексеру және төлқұжат деректерін бақылау болды. Бағалау нәтижелері 3 және 4 кестелерде көрсетілген.
Кесте 3 – Бос жүр
iсте машиналарды сынау
Көрсеткiш | MQ291A станок | Станок PFA станок |
Бос жүрiс | Сынақтан өттi | Сынақтан өттi |
Кесте 4 – Механизмдердің жұмысын тексеру
Көрсеткiш | MQ291A станок | PFA14 станок |
Механизмдердің жұмысын | Сынақтан өттi | Сынақтан өттi |
Паспорт деректерін бақылау екі машинада да талаптарға сай толық ақпарат бар екенін көрсетті. Келесі қадам өнімділік үшін жүктеме кезінде жұмыс істейтін машинаны сынау болды. Бағалау нәтижелері 5-кестеде келтірілген.
Кесте 5 – Жүктемедегі жұмыстағы машиналарды сынау
Көрсеткiш | MQ291A станок | PFA14 станок |
Механизмдердің жұмысын | Сынақтан өттi | Сынақтан өттi |
Келесі қадам станоктарды геометриялық дәлдікке, дайындаманың дәлдігіне және кедір-бұдырлық параметріне сынау болды. Сынақ нәтижелері 6-кестеде келтірілген.
Кесте 6 – Станоктарды дәлдікке сынау
Көрсеткiш | Станок MQ291A | Станок PFA14 |
Геометриялық дәлдігi | Сынақтан өттi | Сынақтан өттi |
Беттік дәлдігi | Сынақтан өттi | Сынақтан өттi |
Кедір-бұдырлығы | Сынақтан өттi | Сынақтан өттi |
Келесі қадам кесу кезінде станоктардың қаттылығы мен дірілге төзімділігін тексеру болды. Бағалау нәтижелері 7-кестеде келтірілген.
Кесте 7 – Машиналарды қаттылық пен дірілге төзімділікке сынау
Көрсеткiш | MQ291A станок | PFA14 станок |
Қаттылығы | Сынақтан өттi | Сынақтан өттi |
Дірілге төзімділігi | Сынақтан өттi | Сынақтан өттi |
Осылайша, екі өндіруші кәсіпорынның станоктарын сынау және сапасын бақылау жүргізілді.
ҚОРЫТЫНДЫ
Металл кескішті технологиялық жүйе ретінде сипаттайтын өңдеу сапасының көрсеткіштері өңделетін беттердің өлшемдерінің, пішінінің және салыстырмалы орналасуының дәлдігі, ал кейбір жағдайларда беткі қабаттың физикалық және механикалық сипаттамалары болып табылады.
Машинаның технологиялық сенімділігі-бұл белгілі бір уақыт аралығында технологиялық процестің сапалық көрсеткіштерін (өңдеу дәлдігі мен бетінің сапасы) сақтау мүмкіндігі. Ол үшін станоктарды технологиялық сенімділікке сынау керек. Бұл сынақтар, біріншіден, берілген машинаның өңдеу дәлдігі бойынша қорды белгілеуі керек, екіншіден, машинаның осы дәлдік қорын жұмсау ұзақтығына болжам жасауы керек. Пайдаланудағы станоктардың жағдайын бағалау үшін параметрлерінің өзгеруі станоктың техникалық сипаттамаларына әсер ететін механизмдерді анықтауға мүмкіндік беретін диагностикалық әдістер қолданылады.
ПАЙДАЛАНҒАН ӘДЕБИЕТТЕР ТІЗІМІ
1.Утенков В. М. Прогнозирование потери точности металлорежущих станков // Машиностроение и компьютерные технологии. - №5. – 2013.
2. Svoboda O., Bach P., Liotto G., Wang C. Machine Tool 3D Volumetric Positioning Error Measurement under Various Thermal Conditions // Proceeding of the ISPMM 2006Conference. Urumgi, Xinjiang, China, August 2-6, 2006.
3. Kaiji Sato. Trend of precision positioning technology // ABCM Symposium Series inMechatronics. 2006. Vol. 2. P. 739-750.
4. Schmitz T.L., Ziegert J.C., Zapata R., Canning J.S. Part Accuracy in High-Speed
Machining: Preliminary Results // Proceedings of MSEC2006. 2006 ASME International Conference on Manufacturing Science and Engineering (October 8-11, 2006). Ypsilanti, MI. 2006. P. 1-8.
5. Zhang H., Yang J., Shen J., Wang C. Measurement and compensation for volumetric positioning errors of CNC machine tools considering thermal effect // The International 10.7463/0513.0574593 8 Journal of Advanced Manufacturing Technology. 2011. Vol. 55, no. 1-4. P. 275-283.
6. Кузнецов А.П. Тепловое поведение и точность металлорежущих станков. МГТУ Станкин; Янус-К, 2011. 256 с.
7. Проников А.С. Параметрическая надёжность машин. М.: Изд-во МГТУ им.Н.Э. Баумана, 2002. 560 с.
8. Утенков В.М. Математическое моделирование процесса изнашивания направляющих скольжения металлорежущих станков // Наука и образование.МГТУ им. Н.Э. Баумана. Электрон. журн. 2013. No 4. DOI: 10.7463/0413.0574580.