Файл: Учебное пособие по дисциплине Геология и геохимия нефти и газа.doc
ВУЗ: Не указан
Категория: Не указан
Дисциплина: Не указана
Добавлен: 04.12.2023
Просмотров: 886
Скачиваний: 2
ВНИМАНИЕ! Если данный файл нарушает Ваши авторские права, то обязательно сообщите нам.
СОДЕРЖАНИЕ
по дисциплине «Геология и геохимия нефти и газа»
2.10.3. Контроль знаний модуля 2_10
Контроль знаний модуля Введение
Таблица 2. Состав нефти (В.В. Доценко; 2007)
1.3.8. Контроль знаний модуля 1_3
5.1 Круговорот углерода в природе, его энергетические
источники и значение для образования нефти и газа
2.7.3 Факторы вторичной миграции нефти и газа
2.7.9. Контроль знаний модуля 1_7
Производство малосернистых котельных топлив базируется главным образом на использовании малосернистых нефтей, а также на применении процессов прямого и косвенного гидрообессеривания. Косвенный метод заключается в разделении мазута на вакуумный дистиллят и гудрон с последующим гидрообессериванием дистиллята по стандартной технологии при давлении 5-10 МПа. Смешением гидроочищенного дистиллята с, гудроном получают котельное топливо с содержанием серы менее 1%. При этом в зависимости от качества мазута достигаемая глубина обессеривания составляет от 30 до 40%.
В конце 60-х годов косвенный метод гидрообессеривания получил распространение в Японии и США, где потребление высокосернистых котельных топлив в плотнонаселенкых и промышленно развитых районах обусловило особую актуальность сероочистки котельных топлив.
Получение малосернистого (с содержанием серы менее 1%) котельного топлива из любых, включая высокосернистые, нефтей возможно только в процессе прямого каталитического гидрообессеривания всего остатка. Основные отличия прямого обессеривания от косвенного заключаются в следующем;
— повышенный расход водорода — в 5-10 раз выше, чем при гидроочистке средних дистиллятов. Следствием этого является необходимость ввода установки по производству водорода;
— быстрое отравление катализатора примесями, содержащимися в остатках в больших концентрациях, чем в дистиллятном
сырье, поэтому необходима более частая замена отработанного катализатора;
— более жесткие технологические условия;
— плохой массообмен, вследствие протекания процесса в двухфазной системе жидкое сырье-газообразный водород;
— необходимость использования реакторов из высококачественных материалов.-
Косвенный способ гидрообессеривания мазута .по сравнению с прямым требует меньшего расхода водорода. Однако при выборе варианта получения котельного топлива следует учитывать наличие установок вакуумной перегонки к другие технико-экономические условия. Косвенный метод относительно легче осуществлять в условиях существующих схем НПЗ.
В 70-е годы в большинстве стран мира наметилась тенденция к вовлечению в переработку тяжелых нефтей, что привело к резкому увеличению выхода остатков. Одновременно с этим увеличивался спрос на дистиллятные топлива — бензин и дизельное. В связи с этим процессам гидропереработки остатков отводилась новая роль предварительной подготовки тяжелого сырья для последующих деструктивных процессов. Наибольшее распространение нашло комбинирование процесса гидрообессеривания остатков и каталитического крекинга или коксования.
Основными зарубежными лицензиарами процессов гидрообессеривания остатков с технологией в стационарном, движущемся и кипящем слое катализатора являются фирмы: "Галф", "Шеврон", ЮОП, "Экссон", "Юникал" — стационарный слой; "Шелл" — движущийся слой; "Луммус", "Хайдрокарбон рисерч" — кипящий слой. Итогом многолетних исследований различных фирм в области гидрооблагораживания тяжелого сырья явилось создание различных модификаций промышленных процессов гкдробессеривания мазута и гудрона на основе технологии со стационарным, движущимся и кипящим слоями. Наибольшее распространение ввиду относительной простоты аппаратного оформления и относительной дешевизны получили процессы со стационарным слоем катализатора. Установки гидрообессеривания в движущемся и кипящем слоях, как правило, эксплуатируются в режиме гидрокрекинга и предназначены для конверсии наиболее неблагоприятного сырья — тяжелых и синтетических нефтей, а также остатков, полученных из этих нефтей, в светлые нефтепродукты.
За рубежом выпускается значительное число марок промышленных катализаторов для процессов гидрометаллизации, гидро- обессеривания, гидродеазотирования и гидроконверсии остатков. Широкий спектр свойств этих катализаторов служит основой для создания эффективных многослойных каталитических систем, с помощью которых подбором оптимальных по размеру и форме частиц катализаторов с соответствующей пористой структурой, активностью и селективностью достигается глубокая очистка исходного сырья при минимальном снижении давления в реакторе и максимально возможном сроке службы каталитической системы в делом.
Значительный интерес представляют процессы гидрообессери-вания остатков в стационарном слое. Процессы гидрообессеривания остатков в стационарном слое катализатора получили наибольшее распространение вследствие относительной простоты технологического и аппаратного оформления. Принципиальные схемы всех модификаций процессов гидрообессеривания в стационарном слое приблизительно одинаковы, и главные их различия заключаются в использовании каталитических систем. Процессы гидрообессеривания могут проводиться как в одну, так и внесколько ступеней (стадий). Число ступеней зависит от качества исходного сырья и требований к качеству конечных продуктов.
Подбором оптимального соотношения различных катализаторов гидрообессеривания достигается максимальный эффект. При анализе поведения катализаторов гидр обессеривания и гидродеметаллизации становится очевидным, что сочетание катализаторов или ступенчатых катализаторных систем будут более эффективны при переработке сырья с высоким содержанием металлов по сравнению с единичным катализатором. При этом необходимо обеспечивать сочетание высокой стойкости катализатора к металлам с хорошей конверсионной активностью, так как диапазон примесей, содержащихся в перерабатываемых остатках, очень широк: содержание серы может изменяться от 0,2 до 6%, металлов — от 20 до 1000 мг/кг.
Длительный опыт эксплуатации промышленных установок гидрообессеривания остатков свидетельствует о том, что в стационарном слое в течение длительного времени можно, перерабатывать сырье без предварительной подготовки с содержанием металлов не более 50 мг/кг, а с предварительной подготовкой (деметаллизация, деасфальтизация) — не более 150 мг/кг.
Фирмой "Шелл" накоплен многолетний опыт создания процессов гидропереработки нефтяных остатков в движущемся слое. Для технологии гидрообесееривания и гидрокрекинга в стационарном слое фирмой разработана серия уникальных катализаторов, в том числе деметаллизирующего широкопористого катализатора с высокой емкостью по металлам. Предложен ряд мер для предотвращения слипания катализатора гидрообессеривания остатков:
— двухступенчатое обессоливание исходной нефти,
— фильтрация гидроочищаемого мазута или гудрона,
— очистка циркулирующего водорода,
— установка фильтров над верхним слоем катализатора, которые могут быть заменены без его выгрузки.
Недостаток процесса — ухудшение распределения поступающего в реактор сырья. Аналогичные меры по повышению эффективности гидрообессеривания остатков используются в процессах
других фирм.
Осуществление деметаллизации в отдельном реакторе и необходимость его отключения для замены отравленного катализатора деметаллизации (при сохранении работоспособности последующих реакторов гидрообессеривания) ускорило создание реакторов с быстрой заменой катализатора бункерного типа.
Созданы реакторы, в которых замена катализатора осуществлялась без остановки реактора. Это система с движущимся слоем, из которой непрерывно выводится отработанный катализатор и вводится свежий. В подобном реакторе с системой непрерывной замены катализатора обеспечивается движение катализатора как монолитной массы так, что он удаляется с низа реактора в том же порядке, в каком вводится вверху.
Дальнейшим этапом развития этой технологии явилось создание комплекса "Хаккон" для переработки тяжелого гудрона. В состав комплекса входила система двух параллельных линий, состоящих из трех бункерных реакторов деметаллизации и двух 'реакторов гидроконверсии со стационарным слоем катализатора. Комплекс "Хайкон" дает возможность превращать гудрон с высоким содержанием металлов и серы в дистиллятные продукты, а также в малосернистый гудрон с низким содержанием металлов, который направляется в топливную сеть или в суммарный фонд
котельного топлива.
Фирма "Хайдрокарбон рисерч" запатентовала способ создания трехфазного кипящего слоя, с помощью которого достигается
более совершенный контакт паровой и жидкой фаз за счет их пря-
моточного движения в реакторе снизу вверх (гидрообессеривание остатков в трехфазном кипящем слое). Частицы катализатора, заполняющие реактор, находятся в движении, образуя расширенный слой, который поддерживается движущимися потоками газа и жидкости.
Преимущества процесса в кипящем слое: — возможность переработки сырья с высоким содержанием металлов (до 500 мг/кг) путем постоянного замещения отработанного катализатора свежим;
—высокое качество продуктов гидрообессеривания;
— изотермичность процесса;
— достижение любой глубины обессеривания сырья, практически любого качества.
Недостатками процесса с кипящим слоем являются:
— большой расход катализатора;
— высокая энергоемкость из-за необходимости затрат энергии на рециркуляцию жидкой фазы;
— наличие сложных по конструкции горячего насоса и устройств по загрузке и выгрузке катализаторов.
При извлечении катализатора в процессе вместе с отработанными катализаторами уходит часть свежего, что дополнительно удорожает процесс. С повышением концентрации металлов в сырье эксплуатационные затраты становятся высокими, и в этих случаях предлагается использовать защитный реактор, заполненный дешевым деметаллизирующим катализатором, в котором удаляется
часть отравляющих примесей.
Наибольший выход малосернистого топочного мазута на сырье (до 80%) достигается в схеме с гидрообессериванием мазута. Проблема получения малосернистого котельного топлива с содержанием серы менее 1%, применение которого позволит значительно улучшить экологическую обстановку, может быть решена за счет углубления переработки нефти путем облагораживанияудронов и удаления из них серы.
Комплексная схема процессов, которая предназначается для глубокой переработки сернистого гудрона или мазута с получением малосернистого ДТ, бензина и облагороженного котельного топлива с пониженным содержанием серы и металлов, представлена на рис. 4.6. При переработке гудрона по такой схеме количество серы в котельном топливе составляет 18-20% масс, от количества серы в исходном гудроне, выбросы диоксида серы при сжигании топлива снижаются в 5,5 раза.
Положительным отличием рассматриваемой схемы является также получение из гудрона до 45% моторных топлив, что позволяет значительно увеличить глубину переработки нефти.
2.11.6.1 Улучшение присадками качества котельных топлив. Ассортимент присадок для котельных топлив менее обширен, чем для моторных. Типы применяемых присадок и их концентрация (мг/кг) приведены ниже.
Депрессорные 100 - 200
Антикоррозионные 10 - 500
Детергентно-диспергирующие (стабилизирующие) 100 - 200
Модификаторы горения (улучшающие горение топлив) —
Деэмульгаторы до 0,01%
Преобладают полифункционалъные присадки, представляющие собой композиции соединений, обеспечивающие набор различных свойств, например, моюще-диспергирующих, антикоррозионных, улучшающих полноту сгорания.
Присадки, улучшающие полноту сгорания остаточных топлив, позволяют получить положительный эффект за счет снижения расхода
топлива и уменьшения токсичности продуктов сгорания.
По принципу действия их разделяют на катализаторы сгорания, ПАВ, окислители. В остаточных топливах наиболее эффективны соединения, улучшающие поверхностное натяжение топлива. Эффективность действия ПАВ и катализаторов горения увеличивается при их сочетании в различных композициях.
Важное значение для улучшения качества котельных топлив имеют присадки, предотвращающие высокотемпературную коррозию продуктов их сгорания.
Образование серного ангидрида при сгорании котельных топлив уменьшается при введении в сернистое топливо аминов, хотя кислотность сажи при этом не снижается. Более эффективны присадки на основе композиции аминов и оксидов магния в этом случае при сгорании топлива, содержащего 0,25% азота, уменьшалась не только эмиссия оксидов серы, но и азота.
Для борьбы с химической газовой коррозией выпускают присадки, лучшими из которых являются следующие соединения магния:
— маслорастворимые органические соединения (алкилсульфонаты, магниевая соль окисленного петролатума);
— водорастворимые (соли магния и неорганических кислот);
— дисперсии оксида и гидроксида магния в. воде и углеводородах.
Наиболее удобны для введения в топливо маслорастворимые присадки. Перспективны многофункциональные присадки, сочетающие (наряду с антикоррозионными) антидымные и диспергирующие свойства.
Диспергирующие присадки добавляются к котельным топли-вам для улучшения их стабильности при хранении, а также при их распылении при подаче в топку, что увеличивает полноту сгорания.
Для улучшения эксплуатационных свойств тяжелых (судовых, газотурбинных, котельных) топлив помимо присадок, улучшающих полноту сгорания, добавляют также стабилизаторы — диспер-санты, функции которых:
— улучшение стабильности к совместимости,компонентов мазутов;
— разрушение водно-мазутных эмульсий;
— предотвращение сернокислотной коррозии поверхностей котлов.
Деэмульгаторы — присадки, облегчающие выделение воды из тяжелых топлив, содержащих природные эмульгаторы. Отделение воды осуществляется ка центрифугах, при этом часть топлива уходит со шламом и водой в виде устойчивой эмульсии. Потери могут достигать 5%, но их можно уменьшить, применяя деэмульгаторы (поверхностно-активные вещества — ПАВ). На практике обычно применяют неионногенные ПАВ — оксизтилированные жирные кислоты и амины. Иногда в состав присадки входят ингибиторы и другие компоненты. — рекомендуемые концентрации: 0,005-0,01%.
Среднедистиллятные и особенно котельные топлива — сравнительно дешевые нефтепродукты, и применение присадок удорожает их стоимость. Однако преимущества, реализуемые за счет улучшения потребительских свойств и удовлетворения требований по охране окружающей среды, обеспечивают растущий спрос на облагороженные присадками топлива.
2.11.7.Рациональные направления переработки углеводородных газообразных систем.
Рассмотрим некоторые направления переработки газообразных углеводородных систем — пропан-пропиленовой и бутан-бутиленовой фракций, которые образуются на установках каталитического крекинга и риформинга, первичной переработки нефти, вторичной перегонки и стабилизации бензинов, разделения и очистки жирных газов. Обычно эти газы поступают в топливную сеть завода, но существуют и более эффективные пути их переработки (рис. 58).
Эти направления включают производство пропилена и полимерных материалов и изделий на его основе, а так же метил-трет-бутилового эфира.
Далее рассмотрены основные достижении по разработке указанных выше технологических процессов. Внедрение этих производств позволяет не только снизить экологическую напряженность, но и значительно повысить технико-экономическую эффективность производства.
Производство полипропилена (МП). Основными исследованиями, направленными на повышение эффективности технологического процесса производства полипропилена явились: перевод процесса поликеризации на непрерывный режим работы, повышение интенсивности теплосъема; использование более эффективных каталитических систем.
Существующие в настоящее время технологии производства ПП основаны на использовании следующих способов полимеризации;
— полимеризация в "тяжелом" растворителе;
— полимеризация в "легком" растворителе-мономере;
— газофазная полимеризация.
Во всех способах используются металлооргакические каталитические системы, основным компонентом которых является трех-хлористый титан или нанесенный титан-магниевый катализатор (ТМК), а сокатализаторами являются диэтилалюминийхлорид (Al(C2H5)2Cl) или триэтилалюминий (Al(C2H5)3.
Наиболее перспективной является полимеризация пропилена в среде сжиженного мономера из газовой фазы. В промышлен-
ности реализована технология полимеризации пропилена в среде жидкого мономера с использованием реактора с газовой фазой. В основу технологии заложен периодический процесс полимеризации пропилена на катализаторах Циглера-Натта TiCl3+Al(C2H5)2Cl. Преимуществом этого процесса являлась высокая концентрация мономера в зоне реакции, отсутствие растворителя и установок, связанных с его очисткой и регенерацией. Недостатки процесса; отложение
полимера на стенках реактора; необходимость сохранения стадии обеззоливания полимера; относительно низкое качество продукции.
Использование высокоактивного микросферического ТiС1з позволило увеличить выход ПП в 4-5 раз по сравнению с выходом на обычном катализаторе, увеличить стереоспецифичность с 90% до 97%, снизить долю атактической фракции с 6-8% до 0,5-1,5%, почти в 3 раза уменьшить зольность ПП и улучшить дисперсность полимера.
Проведены исследования по использованию данных катализаторов в процессе полимеризации пропилена в среде жидкого мономера. Исследование проводилось с использованием ТМК и заключалось в: изучении влияния условий полимеризации и способов формирования каталитической системы на ее активность; исследовании закономерности процесса полимеризации пропилена в массе на ТМК в присутствии водорода; изучении свойств полученного ПП; разработке математической модели непрерывного процесса получения ПП в среде сжиженного пропилена в реакторах идеального смешения.
Изучена каталитическая активность при полимеризации пропилена в массе в интервале температур 30-800С при концентрации Н2 — 2-10-2 моль/г. При использовании ТМК и осуществлении процесса в среде жидкого мономера выход ПП достигает 1400-1550 кг
ПП/г Тi (33-36 кг ПП/г кат.). Увеличение температуры полимеризации от 30 до 800С привело к изменению фракционного состава образующегося ПП. Максимальная степень изотактичиости ПП, полученного при температурах 70-80С, достигает 97-98%.
Исследована активация ТМК введением водорода. Установлено, что при концентрациях водорода (
0,5-10-3 моль/л) наблюдается существенное (в 3-5 раз) увеличение каталитической активности, но при этом система менее стабильна во времени. Полипропилен, синтезированный на ТМК, характеризуется высокими физикомеханическими показателями (табл. 42).
Результаты исследования кинетических закономерностей полимеризаций пропилена и разработанная на их основе математики, включающих стадии: смешения в холодном смесителе и гранулирование смеси в экструдере. Разработана' рецептура и технология для получения эластичного и морозостойкого материала на основе ПП — "Элпона", содержащего в качестве добавки дивинил-стирольный термоэластопласт ДСТ-30 в виде гранул.
Для расширения температурного интервала эксплуатации изделий при сохранении высоких прочностных показателей проведены исследования по модификации полипропилена различными силоксановыми каучуками: СКТ — диметилсилоксановый каучук; ОКТВ, СКТВ-1, СКТВ-2, СКТВ-2Т - метилвинилсилоксановые каучуки, отличающиеся содержанием винильных групп; СКТФВ-803, СКТФВ-2101, СКТФВ-2001 — метилфенилвинилсилоксановые каучуки, отличающиеся содержанием фенильных и винильных заместителей; СКТФТ-50 — термостойкий фторсодержащий каучук с улучшенными диэлектрическими свойствами. Для промышленного
использования рекомендованы силоксановые каучуки, введение которых обеспечивает получение морозостойких композиций различного применения (табл. 4.62).
Изменение прочностных показателей от содержания силокса-новых каучуков аналогично введению добавок других каучуков
ря хорошей совместимости силоксановых каучуков с полипропиленом, достигаемой тонким измельчением, а также обусловленной химическим строением силоксановых каучуков, композиции обладают более низкой температурой хрупкости, чем, например, композиции полипропилен-термозластопласт.
Введение силоксановых каучуков изменяет не только физико-механические, но и электрофизические свойства полипропилена.
Таблица 43
часть отравляющих примесей.
Наибольший выход малосернистого топочного мазута на сырье (до 80%) достигается в схеме с гидрообессериванием мазута. Проблема получения малосернистого котельного топлива с содержанием серы менее 1%, применение которого позволит значительно улучшить экологическую обстановку, может быть решена за счет углубления переработки нефти путем облагораживанияудронов и удаления из них серы.
Комплексная схема процессов, которая предназначается для глубокой переработки сернистого гудрона или мазута с получением малосернистого ДТ, бензина и облагороженного котельного топлива с пониженным содержанием серы и металлов, представлена на рис. 4.6. При переработке гудрона по такой схеме количество серы в котельном топливе составляет 18-20% масс, от количества серы в исходном гудроне, выбросы диоксида серы при сжигании топлива снижаются в 5,5 раза.
Положительным отличием рассматриваемой схемы является также получение из гудрона до 45% моторных топлив, что позволяет значительно увеличить глубину переработки нефти.
2.11.6.1 Улучшение присадками качества котельных топлив. Ассортимент присадок для котельных топлив менее обширен, чем для моторных. Типы применяемых присадок и их концентрация (мг/кг) приведены ниже.
Депрессорные 100 - 200
Антикоррозионные 10 - 500
Детергентно-диспергирующие (стабилизирующие) 100 - 200
Модификаторы горения (улучшающие горение топлив) —
Деэмульгаторы до 0,01%
Преобладают полифункционалъные присадки, представляющие собой композиции соединений, обеспечивающие набор различных свойств, например, моюще-диспергирующих, антикоррозионных, улучшающих полноту сгорания.
Присадки, улучшающие полноту сгорания остаточных топлив, позволяют получить положительный эффект за счет снижения расхода
топлива и уменьшения токсичности продуктов сгорания.
По принципу действия их разделяют на катализаторы сгорания, ПАВ, окислители. В остаточных топливах наиболее эффективны соединения, улучшающие поверхностное натяжение топлива. Эффективность действия ПАВ и катализаторов горения увеличивается при их сочетании в различных композициях.
Важное значение для улучшения качества котельных топлив имеют присадки, предотвращающие высокотемпературную коррозию продуктов их сгорания.
Образование серного ангидрида при сгорании котельных топлив уменьшается при введении в сернистое топливо аминов, хотя кислотность сажи при этом не снижается. Более эффективны присадки на основе композиции аминов и оксидов магния в этом случае при сгорании топлива, содержащего 0,25% азота, уменьшалась не только эмиссия оксидов серы, но и азота.
Для борьбы с химической газовой коррозией выпускают присадки, лучшими из которых являются следующие соединения магния:
— маслорастворимые органические соединения (алкилсульфонаты, магниевая соль окисленного петролатума);
— водорастворимые (соли магния и неорганических кислот);
— дисперсии оксида и гидроксида магния в. воде и углеводородах.
Наиболее удобны для введения в топливо маслорастворимые присадки. Перспективны многофункциональные присадки, сочетающие (наряду с антикоррозионными) антидымные и диспергирующие свойства.
Диспергирующие присадки добавляются к котельным топли-вам для улучшения их стабильности при хранении, а также при их распылении при подаче в топку, что увеличивает полноту сгорания.
Для улучшения эксплуатационных свойств тяжелых (судовых, газотурбинных, котельных) топлив помимо присадок, улучшающих полноту сгорания, добавляют также стабилизаторы — диспер-санты, функции которых:
— улучшение стабильности к совместимости,компонентов мазутов;
— разрушение водно-мазутных эмульсий;
— предотвращение сернокислотной коррозии поверхностей котлов.
Деэмульгаторы — присадки, облегчающие выделение воды из тяжелых топлив, содержащих природные эмульгаторы. Отделение воды осуществляется ка центрифугах, при этом часть топлива уходит со шламом и водой в виде устойчивой эмульсии. Потери могут достигать 5%, но их можно уменьшить, применяя деэмульгаторы (поверхностно-активные вещества — ПАВ). На практике обычно применяют неионногенные ПАВ — оксизтилированные жирные кислоты и амины. Иногда в состав присадки входят ингибиторы и другие компоненты. — рекомендуемые концентрации: 0,005-0,01%.
Среднедистиллятные и особенно котельные топлива — сравнительно дешевые нефтепродукты, и применение присадок удорожает их стоимость. Однако преимущества, реализуемые за счет улучшения потребительских свойств и удовлетворения требований по охране окружающей среды, обеспечивают растущий спрос на облагороженные присадками топлива.
2.11.7.Рациональные направления переработки углеводородных газообразных систем.
Рассмотрим некоторые направления переработки газообразных углеводородных систем — пропан-пропиленовой и бутан-бутиленовой фракций, которые образуются на установках каталитического крекинга и риформинга, первичной переработки нефти, вторичной перегонки и стабилизации бензинов, разделения и очистки жирных газов. Обычно эти газы поступают в топливную сеть завода, но существуют и более эффективные пути их переработки (рис. 58).
Эти направления включают производство пропилена и полимерных материалов и изделий на его основе, а так же метил-трет-бутилового эфира.
Далее рассмотрены основные достижении по разработке указанных выше технологических процессов. Внедрение этих производств позволяет не только снизить экологическую напряженность, но и значительно повысить технико-экономическую эффективность производства.
Производство полипропилена (МП). Основными исследованиями, направленными на повышение эффективности технологического процесса производства полипропилена явились: перевод процесса поликеризации на непрерывный режим работы, повышение интенсивности теплосъема; использование более эффективных каталитических систем.
Существующие в настоящее время технологии производства ПП основаны на использовании следующих способов полимеризации;
— полимеризация в "тяжелом" растворителе;
— полимеризация в "легком" растворителе-мономере;
— газофазная полимеризация.
Во всех способах используются металлооргакические каталитические системы, основным компонентом которых является трех-хлористый титан или нанесенный титан-магниевый катализатор (ТМК), а сокатализаторами являются диэтилалюминийхлорид (Al(C2H5)2Cl) или триэтилалюминий (Al(C2H5)3.
Наиболее перспективной является полимеризация пропилена в среде сжиженного мономера из газовой фазы. В промышлен-
ности реализована технология полимеризации пропилена в среде жидкого мономера с использованием реактора с газовой фазой. В основу технологии заложен периодический процесс полимеризации пропилена на катализаторах Циглера-Натта TiCl3+Al(C2H5)2Cl. Преимуществом этого процесса являлась высокая концентрация мономера в зоне реакции, отсутствие растворителя и установок, связанных с его очисткой и регенерацией. Недостатки процесса; отложение
полимера на стенках реактора; необходимость сохранения стадии обеззоливания полимера; относительно низкое качество продукции.
Использование высокоактивного микросферического ТiС1з позволило увеличить выход ПП в 4-5 раз по сравнению с выходом на обычном катализаторе, увеличить стереоспецифичность с 90% до 97%, снизить долю атактической фракции с 6-8% до 0,5-1,5%, почти в 3 раза уменьшить зольность ПП и улучшить дисперсность полимера.
Проведены исследования по использованию данных катализаторов в процессе полимеризации пропилена в среде жидкого мономера. Исследование проводилось с использованием ТМК и заключалось в: изучении влияния условий полимеризации и способов формирования каталитической системы на ее активность; исследовании закономерности процесса полимеризации пропилена в массе на ТМК в присутствии водорода; изучении свойств полученного ПП; разработке математической модели непрерывного процесса получения ПП в среде сжиженного пропилена в реакторах идеального смешения.
Изучена каталитическая активность при полимеризации пропилена в массе в интервале температур 30-800С при концентрации Н2 — 2-10-2 моль/г. При использовании ТМК и осуществлении процесса в среде жидкого мономера выход ПП достигает 1400-1550 кг
ПП/г Тi (33-36 кг ПП/г кат.). Увеличение температуры полимеризации от 30 до 800С привело к изменению фракционного состава образующегося ПП. Максимальная степень изотактичиости ПП, полученного при температурах 70-80С, достигает 97-98%.
Исследована активация ТМК введением водорода. Установлено, что при концентрациях водорода (
0,5-10-3 моль/л) наблюдается существенное (в 3-5 раз) увеличение каталитической активности, но при этом система менее стабильна во времени. Полипропилен, синтезированный на ТМК, характеризуется высокими физикомеханическими показателями (табл. 42).
Результаты исследования кинетических закономерностей полимеризаций пропилена и разработанная на их основе математики, включающих стадии: смешения в холодном смесителе и гранулирование смеси в экструдере. Разработана' рецептура и технология для получения эластичного и морозостойкого материала на основе ПП — "Элпона", содержащего в качестве добавки дивинил-стирольный термоэластопласт ДСТ-30 в виде гранул.
Для расширения температурного интервала эксплуатации изделий при сохранении высоких прочностных показателей проведены исследования по модификации полипропилена различными силоксановыми каучуками: СКТ — диметилсилоксановый каучук; ОКТВ, СКТВ-1, СКТВ-2, СКТВ-2Т - метилвинилсилоксановые каучуки, отличающиеся содержанием винильных групп; СКТФВ-803, СКТФВ-2101, СКТФВ-2001 — метилфенилвинилсилоксановые каучуки, отличающиеся содержанием фенильных и винильных заместителей; СКТФТ-50 — термостойкий фторсодержащий каучук с улучшенными диэлектрическими свойствами. Для промышленного
использования рекомендованы силоксановые каучуки, введение которых обеспечивает получение морозостойких композиций различного применения (табл. 4.62).
Изменение прочностных показателей от содержания силокса-новых каучуков аналогично введению добавок других каучуков
ря хорошей совместимости силоксановых каучуков с полипропиленом, достигаемой тонким измельчением, а также обусловленной химическим строением силоксановых каучуков, композиции обладают более низкой температурой хрупкости, чем, например, композиции полипропилен-термозластопласт.
Введение силоксановых каучуков изменяет не только физико-механические, но и электрофизические свойства полипропилена.
Таблица 43
Наибольший выход малосернистого топочного мазута на сырье (до 80%) достигается в схеме с гидрообессериванием мазута. Проблема получения малосернистого котельного топлива с содержанием серы менее 1%, применение которого позволит значительно улучшить экологическую обстановку, может быть решена за счет углубления переработки нефти путем облагораживанияудронов и удаления из них серы.
Комплексная схема процессов, которая предназначается для глубокой переработки сернистого гудрона или мазута с получением малосернистого ДТ, бензина и облагороженного котельного топлива с пониженным содержанием серы и металлов, представлена на рис. 4.6. При переработке гудрона по такой схеме количество серы в котельном топливе составляет 18-20% масс, от количества серы в исходном гудроне, выбросы диоксида серы при сжигании топлива снижаются в 5,5 раза.
Положительным отличием рассматриваемой схемы является также получение из гудрона до 45% моторных топлив, что позволяет значительно увеличить глубину переработки нефти.
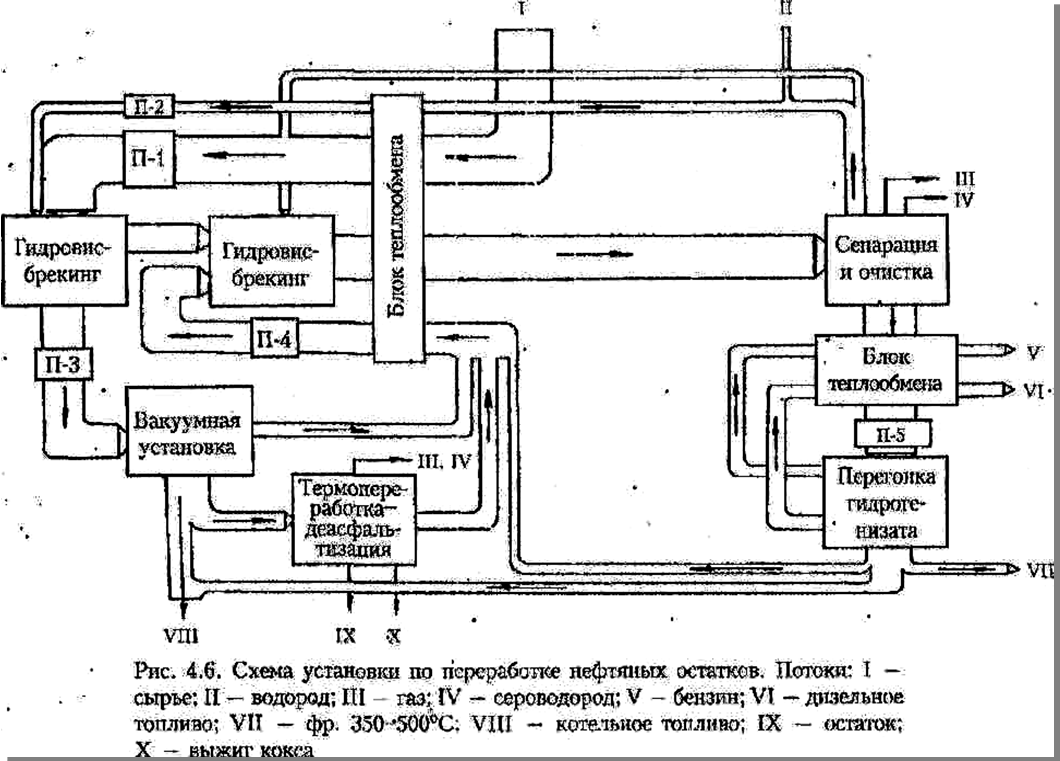
2.11.6.1 Улучшение присадками качества котельных топлив. Ассортимент присадок для котельных топлив менее обширен, чем для моторных. Типы применяемых присадок и их концентрация (мг/кг) приведены ниже.
Депрессорные 100 - 200
Антикоррозионные 10 - 500
Детергентно-диспергирующие (стабилизирующие) 100 - 200
Модификаторы горения (улучшающие горение топлив) —
Деэмульгаторы до 0,01%
Преобладают полифункционалъные присадки, представляющие собой композиции соединений, обеспечивающие набор различных свойств, например, моюще-диспергирующих, антикоррозионных, улучшающих полноту сгорания.
Присадки, улучшающие полноту сгорания остаточных топлив, позволяют получить положительный эффект за счет снижения расхода
топлива и уменьшения токсичности продуктов сгорания.
По принципу действия их разделяют на катализаторы сгорания, ПАВ, окислители. В остаточных топливах наиболее эффективны соединения, улучшающие поверхностное натяжение топлива. Эффективность действия ПАВ и катализаторов горения увеличивается при их сочетании в различных композициях.
Важное значение для улучшения качества котельных топлив имеют присадки, предотвращающие высокотемпературную коррозию продуктов их сгорания.
Образование серного ангидрида при сгорании котельных топлив уменьшается при введении в сернистое топливо аминов, хотя кислотность сажи при этом не снижается. Более эффективны присадки на основе композиции аминов и оксидов магния в этом случае при сгорании топлива, содержащего 0,25% азота, уменьшалась не только эмиссия оксидов серы, но и азота.
Для борьбы с химической газовой коррозией выпускают присадки, лучшими из которых являются следующие соединения магния:
— маслорастворимые органические соединения (алкилсульфонаты, магниевая соль окисленного петролатума);
— водорастворимые (соли магния и неорганических кислот);
— дисперсии оксида и гидроксида магния в. воде и углеводородах.
Наиболее удобны для введения в топливо маслорастворимые присадки. Перспективны многофункциональные присадки, сочетающие (наряду с антикоррозионными) антидымные и диспергирующие свойства.
Диспергирующие присадки добавляются к котельным топли-вам для улучшения их стабильности при хранении, а также при их распылении при подаче в топку, что увеличивает полноту сгорания.
Для улучшения эксплуатационных свойств тяжелых (судовых, газотурбинных, котельных) топлив помимо присадок, улучшающих полноту сгорания, добавляют также стабилизаторы — диспер-санты, функции которых:
— улучшение стабильности к совместимости,компонентов мазутов;
— разрушение водно-мазутных эмульсий;
— предотвращение сернокислотной коррозии поверхностей котлов.
Деэмульгаторы — присадки, облегчающие выделение воды из тяжелых топлив, содержащих природные эмульгаторы. Отделение воды осуществляется ка центрифугах, при этом часть топлива уходит со шламом и водой в виде устойчивой эмульсии. Потери могут достигать 5%, но их можно уменьшить, применяя деэмульгаторы (поверхностно-активные вещества — ПАВ). На практике обычно применяют неионногенные ПАВ — оксизтилированные жирные кислоты и амины. Иногда в состав присадки входят ингибиторы и другие компоненты. — рекомендуемые концентрации: 0,005-0,01%.
Среднедистиллятные и особенно котельные топлива — сравнительно дешевые нефтепродукты, и применение присадок удорожает их стоимость. Однако преимущества, реализуемые за счет улучшения потребительских свойств и удовлетворения требований по охране окружающей среды, обеспечивают растущий спрос на облагороженные присадками топлива.
2.11.7.Рациональные направления переработки углеводородных газообразных систем.
Рассмотрим некоторые направления переработки газообразных углеводородных систем — пропан-пропиленовой и бутан-бутиленовой фракций, которые образуются на установках каталитического крекинга и риформинга, первичной переработки нефти, вторичной перегонки и стабилизации бензинов, разделения и очистки жирных газов. Обычно эти газы поступают в топливную сеть завода, но существуют и более эффективные пути их переработки (рис. 58).
Эти направления включают производство пропилена и полимерных материалов и изделий на его основе, а так же метил-трет-бутилового эфира.
Далее рассмотрены основные достижении по разработке указанных выше технологических процессов. Внедрение этих производств позволяет не только снизить экологическую напряженность, но и значительно повысить технико-экономическую эффективность производства.
Производство полипропилена (МП). Основными исследованиями, направленными на повышение эффективности технологического процесса производства полипропилена явились: перевод процесса поликеризации на непрерывный режим работы, повышение интенсивности теплосъема; использование более эффективных каталитических систем.
Существующие в настоящее время технологии производства ПП основаны на использовании следующих способов полимеризации;
— полимеризация в "тяжелом" растворителе;
— полимеризация в "легком" растворителе-мономере;
— газофазная полимеризация.
Во всех способах используются металлооргакические каталитические системы, основным компонентом которых является трех-хлористый титан или нанесенный титан-магниевый катализатор (ТМК), а сокатализаторами являются диэтилалюминийхлорид (Al(C2H5)2Cl) или триэтилалюминий (Al(C2H5)3.
Наиболее перспективной является полимеризация пропилена в среде сжиженного мономера из газовой фазы. В промышлен-
ности реализована технология полимеризации пропилена в среде жидкого мономера с использованием реактора с газовой фазой. В основу технологии заложен периодический процесс полимеризации пропилена на катализаторах Циглера-Натта TiCl3+Al(C2H5)2Cl. Преимуществом этого процесса являлась высокая концентрация мономера в зоне реакции, отсутствие растворителя и установок, связанных с его очисткой и регенерацией. Недостатки процесса; отложение
полимера на стенках реактора; необходимость сохранения стадии обеззоливания полимера; относительно низкое качество продукции.
Использование высокоактивного микросферического ТiС1з позволило увеличить выход ПП в 4-5 раз по сравнению с выходом на обычном катализаторе, увеличить стереоспецифичность с 90% до 97%, снизить долю атактической фракции с 6-8% до 0,5-1,5%, почти в 3 раза уменьшить зольность ПП и улучшить дисперсность полимера.
Проведены исследования по использованию данных катализаторов в процессе полимеризации пропилена в среде жидкого мономера. Исследование проводилось с использованием ТМК и заключалось в: изучении влияния условий полимеризации и способов формирования каталитической системы на ее активность; исследовании закономерности процесса полимеризации пропилена в массе на ТМК в присутствии водорода; изучении свойств полученного ПП; разработке математической модели непрерывного процесса получения ПП в среде сжиженного пропилена в реакторах идеального смешения.
Изучена каталитическая активность при полимеризации пропилена в массе в интервале температур 30-800С при концентрации Н2 — 2-10-2 моль/г. При использовании ТМК и осуществлении процесса в среде жидкого мономера выход ПП достигает 1400-1550 кг
ПП/г Тi (33-36 кг ПП/г кат.). Увеличение температуры полимеризации от 30 до 800С привело к изменению фракционного состава образующегося ПП. Максимальная степень изотактичиости ПП, полученного при температурах 70-80С, достигает 97-98%.
Исследована активация ТМК введением водорода. Установлено, что при концентрациях водорода (
Вид каучука | Содержание каучука, % | Предел текучести, н/м2 | Относительное удлинение, % | Теплостойкость Вика, % | Температура хрупкости, 0С |
СКТ | 5 | 270 | 500 | 135 | -70 |
СКВ | 5 | 270 | 500 | 135 | -70 |
СКТФВ-803 | 5 | 270 | 500 | 135 | -80 |
СКТН | 1-2 | 280 | 500 | 150 | -60 |
ДСТ-30 | 10 | 250 | 300 | 130 | -50 |