Файл: Очистка сточных вод производства экстракционной фосфорной кислоты.docx
ВУЗ: Не указан
Категория: Не указан
Дисциплина: Не указана
Добавлен: 04.12.2023
Просмотров: 82
Скачиваний: 1
ВНИМАНИЕ! Если данный файл нарушает Ваши авторские права, то обязательно сообщите нам.
«Очистка сточных вод производства экстракционной фосфорной кислоты»
Содержание
Введение
Глава 1.Особенности процесса производства ЭФК
Глава 2.Модернизация АСУТП производства ЭФК ОАО «Аммофос»
Глава 3. Очистка сточных вод производства ЭФК
Заключение
Литература
Введение
Производство экстракционной фосфорной кислоты связано с расходом значительных количеств воды. В процессе производства эта вода загрязняется многочисленными примесями, среди которых наиболее токсичными являются: желтый фосфор, фтористые и цианистые соединения, фенолы, фосфин. Организация работы фосфорного завода без выпуска сточных вод является наиболее целесообразной. Такая организация использования воды основана на наличии взаимосвязанных замкнутых циклов, с промежуточной очисткой воды до установленных норм. Главным звеном в этой организации является цех очистки сточных вод. Принимая химически загрязненную воду завода, он должен переработать ее и выдать воду установленного регламентом качества для снабжения технологических процессов, систем мокрой пыле-газоочистки и других потребителей.
Глава 1. Особенности процесса производства экстракционной фосфорной кислоты
Аппаратура для производства экстракционной фосфорной кислоты в основном не зависит от способа выделения сульфата кальция. Различие технологических режимов сказывается главным образом на соотношениях между отдельными аппаратурными элементами, а также и на выборе конструкционных материалов, защите от коррозии и величине образования потоков.
Наиболее распространен дигидратный режим, усовершенствование которого позволяет получать из апатитового концентрата или высококачественных фосфоритов при 65-80°С фосфорную кислоту с содержанием P


Фосфорную кислоту с содержанием более 30-32% P


получают по высокотемпературному режиму (90-100°С) с выделением в твердую фазу полугидрата или ангидрита. Полугидратный процесс в настоящее время широко используется в промышленности.
Ангидритный процесс, протекающий при температуре выше 100°С с применением концентрированной кислоты осложняется сильной коррозией аппаратуры, трудностью отделения мелких кристаллов; кроме того, для поддержания автотермичности процесса из-за недостаточной экзотермичности его необходим подогрев реагентов. Помимо этого возникают большие трудности при отмывке фосфорной кислоты из осадка. Поэтому ангидритный процесс до сих пор не вышел из стадии небольших опытных масштабов.
Производство экстракционной фосфорной кислоты состоит из следующих основных стадий: дозирования фосфатного сырья серной кислотой, разложение фосфата смесью серной и фосфорной кислот (экстракции), охлаждение циркулирующей пульпы, фильтрования экстракционной пульпы, абсорбции фторсодержащих газов и концентрирования фосфорной кислоты.
В зависимости от температуры и концентрации фосфорная кислота в системе CaSO4-H3PO4-H2O сульфат Ca осаждается в виде дигидрата (гипса), гемигидрата или ангидрита. В реальных условиях осадок загрязнен примесями P2O5 в виде неразложенных природных фосфатов, недоотмытой H3PO4, сокристаллизованных фосфатов различных металлов и др., поэтому образующиеся сульфаты Ca называют соответствующе фосфогипс, фосфогемигидрат и фосфо-ангидрит. В зависимости от типа осаждаемого сульфата различают три прямых способа производства экстракционной фосфорной кислоты: дигидратный, полугидратный (гемигидратный) и ангидритный, а также комбинированные: полугидратно-дигидратный и дигидратно-полугидратный.
В СНГ наиболее отработан в промышленности дигидратный способ, который отличается высоким выходом P2O5 (93-96,5%) в продукционную кислоту; однако относительно низкая концентрация фосфорной кислоты требует ее последующего упаривания. Основные стадии процесса: экстракция с внешней или внутренней циркуляцией и вакуумным или воздушным охлаждением экстракционной пульпы, дозревание пульпы после экстрактора, отделение фосфорной кислоты на наливных вакуум-фильтрах. Эффективность процесса определяют в основном экстрагирование P2O5 и фильтрование пульпы. Аппаратурное оформление должно обеспечить полноту разложения сырья и кристаллизацию сульфата Ca в условиях минимального пересыщения им жидкой фазы. Оптимальная форма и размеры кристаллов сульфата Ca обусловливают хорошую фильтруемость пульпы и эффективную отмывку от фосфорной кислоты минимальным количеством воды (для получения концентрированной продукционной фосфорной кислоты). Типовая схема дигидратного способа (рис. 1) реализуется при непрерывном дозировании в экстрактор фосфатного сырья, 75-93%-ной H
2SO4 и оборотной H3PO4. Температура процесса 72-750C, продолжительность 4-6 ч. Использование 93%-ной H2SO4 (при переработке апатитового концентрата) позволяет увеличить подачу воды для промывки фосфогипса на вакуум-фильтре. Поступающая на фильтр фосфорная кислота отделяется, осадок фосфогипса промывается на фильтре по противоточной схеме водой с возвратом образующейся слабой фосфорной кислоты в экстрактор. Фосфорную кислоту, полученную из апатитового концентрата (28-32% P2O5), обычно упаривают до содержания P2O5 52-54%. Концентрирование фосфорной кислоты, полученной из фосфоритов (20-24% P2O5), неосуществимо без предварительной очистки от примесей и не используется в промышленности.
Гемигидратный процесс позволяет получить более концентрированную фосфорную кислоту (в отдельных случаях до 50% P2O5 без дополнительного упаривания). Фосфорную кислоту, содержащую 36-38% P2O5, можно получить из апатитового концентрата практически на том же оборудовании, что и в типовом дигидратном процессе с воздушным охлаждением пульпы. Фосфориты Каратау по этому методу не перерабатывают. Широкого распространения гемигидратные процессы пока не получили из-за повышенной температуры (80-100 0C), выделения HF в газовую фазу, более низкого выхода P2O5 в кислоту, чем в дигидратном методе. В усовершенствованных промышленных схемах предусмотрено предварительное смачивание апатитового сырья в скоростном смесителе, разделение зон разложения и кристаллизации и др. Проведение процесса при содержании H2SO4 в жидкой фазе пульпы 0,2-1,0% в первом реакторе и 2,0-3,0% во втором позволяет снизить количество растворенного сульфата Ca в продукционной фосфорной кислоте, значительно уменьшить зарастание оборудования и трубопроводов, существенно интенсифицировать работу основных технологических узлов.
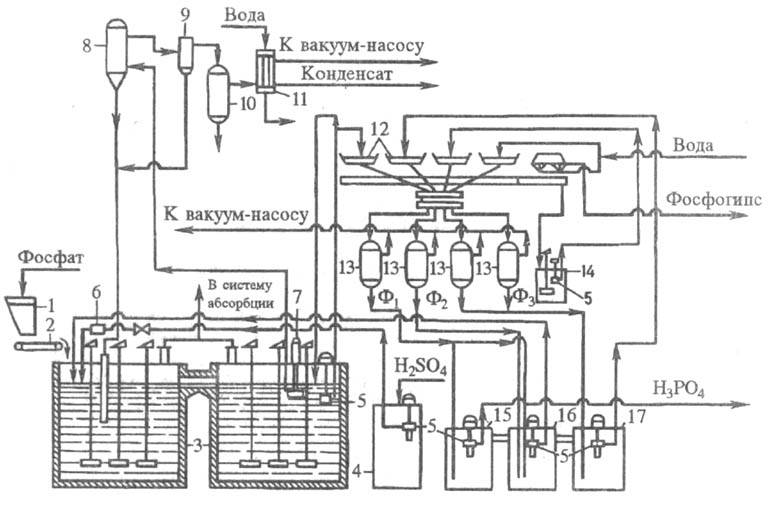
Рис. 1. Технологическая схема типового производства экстракционной H3PO4 в дигидратном процессе из апатитового концентрата, мощность 110 тыс. т P2O5 в год: 1 - бункер для фосфатного сырья; 2 - ленточный весовой дозатор; 3 - двухбаковый экстрактор; 4 -хранилище серной кислоты; 5 - погружной насос; 6 -расходомер серной кислоты; 7 - циркуляционный погружной насос; 8 - испаритель; 9 - брызгоуловитель; 10 -барботажный нейтрализатор; 11 - конденсатор; 12 -лотки карусельного вакуум-фильтра; 13 - сепараторы (ресиверы); 14 - промежуточный сборник образующейся при регенерации фильтровальной ткани; 15, 16, 17 - барометрические сборники: для первого (основного) фильтра (15), для оборотной фосфорной кислоты (16), для промывного фильтрата (17).
Содержание P2O5 в фильтратах: Ф1 - 28-32%, Ф2 - 22-25%, Ф3 - 5-10% .
Ангидритный способ имеет ряд преимуществ перед дигидратным и полугидратным: позволяет без упаривания получать кислоту, содержащую до 50% P2O5; при экстракции в газовую фазу выделяется большая часть фтора; получаемая кислота меньше загрязнена сульфатом Ca. Использование метода в промышленности сдерживают: жесткие коррозионные условия (высокие температуры и концентрации фосфорной кислоты), образование мелких кристаллов и необходимость большого числа ступеней противоточной промывки.
Комбинированные способы получения экстракционной фосфорной кислоты - гемигидратно-дигидратный и дигидратно-гемигид-ратный - более технологичны и экономичны, чем одностадийные. Обеспечивают повышение степени использования фосфатного сырья (за счет снижения технологических потерь P2O5), увеличение концентрации продукционной фосфорной кислоты, получение более чистого сульфата Ca с целью его дальнейшей переработки.
За рубежом широко распространены гемигидратно-дигидратные схемы, внедрен также дигидратно-гемигидратный способ. Однако комбинированные процессы иногда усложнены двойным фильтрованием или нетехнологичны из-за высокой продолжительности стадии перекристаллизации в гемигидратно-дигидратном методе (общая продолжительность процесса 10-16 ч в зависимости от сырья). Из усовершенствованных комбинированных технологий наибольший интерес представляет отечественный дигидратно-гемигидратный процесс с промежуточным фильтрованием. Метод позволяет получать из апатитового концентрата фосфорную кислоту, содержащую 33-34% P2O5, из фосфоритов Каратау - фосфорную кислоту, содержащую 28-30% P2O5. Степень извлечения P2O5 из сырья около 99%. Продолжительность процесса не превышает 6 ч. Фосфополугидрат (фосфогемигидрат) содержит менее 0,5% P2O5 и0,15% F и применен как вяжущее средство в строительных материалах [1].
Глава 2. Модернизация АСУТП производства экстракционной фосфорной кислоты ОАО «Аммофос»
Открытое акционерное общество "Аммофос", входящее в холдинг «ФосАгро», на сегодня представляет собой большой технологический комплекс по производству минеральных удобрений, реализуемых как на внутреннем, так и на внешнем рынках. В состав этого комплекса входят три основных производства: серной кислоты, фосфорной и производство минеральных удобрений. В настоящее время ОАО «Аммофос» выпускает как двойные марки удобрений, содержащие азот и фосфор, так и трехкомпонентные, в состав которых входят три основных питательных элемента: азот, фосфор, калий.
Автоматизированные системы управления процессами (АСУТП) на предприятии внедрялись практически с пуском технологического производства. Сначала это были АСУТП на базе ЭВМ М6000, затем - на базе СМ-2М, ТВСО, и уже более десяти лет – на базе микропроцессорной техники и персональных компьютеров. Это достаточно большой срок для средств автоматизации. И в настоящее время по целому ряду причин мы столкнулись, как и другие предприятия отрасли, с необходимостью модернизации АСУТП. Это связано с тем, что поддержка работоспособности систем на базе ПЛК Ломиконт-110,-112, Ремиконт-110 и программного обеспечения, эксплуатируемого с начала 90-х годов становится все более трудоёмкой и продолжительной по времени. Например, мы начали сталкиваться с тем, что при замене вышедшей из строя вычислительной техники приходилось искать и использовать устаревшие, снятые с производства персональные компьютеры и компоненты. И конечно это не могло не сказаться на надежности системы, и соответственно, на самом производстве. Кроме того, существующие АСУТП имели ограничения вычислительных ресурсов, средств обработки и представления информации, имели и ограничения по расширению под постоянно растущие требования производства. В результате довольно длительного изучения доступных HMI/SCADA-пакетов мы остановили свой выбор на ПО HMI/SCADA iFIX компании GE Fanuc, представленном на российском рынке компанией “ИндаСофт”. Кроме того, в пользу выбора iFIX сыграло наличие у компании GE Fanuc интегрированных решений для автоматизации производства, в составе которых (помимо iFIX) имеются масштабируемая и высокопроизводительная система архивирования Proficy Historian и другие средства автоматизации. Что же касается iFIX, то этот пакет обладает многими достоинствами, среди которых возможности базы данных реального времени, распределенная сетевая архитектура, возможности масштабирования и резервирования, встроенный язык VBA, возможность обмена информацией с существующей у нас системой диспетчерского управления, наличие драйверов к отечественным контроллерам Ломиконт.
Модернизация АСУТП началась с производства экстракционной фосфорной кислоты в августе 2004 года. В период капитального ремонта одного из корпусов (5.58) производства, длившегося около 2-х месяцев, была проведена и реконструкция АСУТП. На 2005 год запланирована реконструкция АСУТП участка ЭФК-1. А в 2006 году – закончить реконструкцию АСУТП ПЭФК (SCADA-системы).