Добавлен: 05.12.2023
Просмотров: 2312
Скачиваний: 50
ВНИМАНИЕ! Если данный файл нарушает Ваши авторские права, то обязательно сообщите нам.
СОДЕРЖАНИЕ
1. Безопасные условия труда слесаря и противопожарные мероприятия.
Тема 1: «Плоскостная разметка»
Тема 3: «Правка и рихтовка металла»
Тема 7: «Сверление, зенкование, зенкерование и развёртывание отверстий»
Тема 10: «Пространственная разметка»
Тема 12: «Распиливание и припасовка»
Восстанавливают изношенные притиры точным строганием, шабрением, обтачиванием и шлифованием.
Рисунок 23. Притиры для обработки плоскостей: а – плита с канавками для грубой притирки; б – плита для чистовой притирки
Притирка (доводка) плоских поверхностей. Эту операцию обычно выполняют с применением минерального масла, технического сала, керосина, бензина. Притирать или доводить всухую не рекомендуется, так как абразивный порошок при этом распределяется неравномерно и, кроме того, детали нагреваются и может произойти их коробление.
Различные притиры требуют различной смазки. Для притиров из чугуна в качестве смазки берут керосин или бензин, из мягкой стали – машинное масло, из меди – машинное масло, спирт и содовую воду. Стальные детали притирают с применением машинного масла и технического сала, бронзовые сала, чугунные-керосина. При особо высоких требованиях к качеству стальной поверхности применяют венскую известь, разведенную в спирте, или крокус в вазелине. Алюминий притирают трепелом, разведенным в толуоле со стеариновой кислотой или в деревянном масле.
Плоские несопрягаемые поверхности чаще всего притирают вручную на неподвижных притирочных плитах.
Притирочные плиты для предварительной притирки снабжают продольными и поперечными канавками. Эти канавки выполняют шириной и глубиной 1–2 мм на расстоянии 15–20 мм друг друга. Канавки предназначены для сбора снимаемой стружки металла и выпадающих из поверхности плиты зерен абразива. Плиты для окончательной притирки канавок не имеют. Притирка на плитах дает очень точные результаты, поэтому на них притирают детали, требующие особо высокой точности, в частности, лекальные линейки, шаблоны, калибры, плитки.
Для притирки деталей плиту шаржируют абразивом или наносят на нее тонким равномерным слоем смешанный с маслом абразивный порошок.
Поверхность под притирку тщательно готовят. Лучшие результаты дает предварительное шлифование. Припуск на притирку оставляют не более 0,02 мм (большие припуски увеличивают трудоемкость).
Обрабатываемое изделие кладут притираемой поверхностью на плиту и с легким нажимом перемещают его круговыми в сочетаниями с прямолинейными движениями по всей поверхности плиты. При этом выступающие острые ребра частиц абразива, находящиеся на притире, срезают с изделия очень тонкий слой металла. Нажим на изделие должен быть равномерным и несильным. Необходимо следить, чтобы не было сильного нагрева детали. Если деталь нагрелась, то притирку приостанавливают и дают изделию остыть.
Узкие поверхности и тонкие изделия (шаблоны, угольники, линейки) притирают при помощи металлического бруска, который прижимают к детали сбоку и вместе с ней перемещают по притиру. Такие бруски служат направляющими, без них трудно удержать изделие в вертикальном положении.
Притирку со сменой слоя абразивной массы повторяют несколько раз, пока обрабатываемая поверхность не достигнет необходимого качества.
Окончательную притирку для придания поверхности блеска производят на одном масле с прибавлением остатков абразивного порошка от предварительной притирки.
Для притирки плоских поверхностей, кроме плит, применяют различные приспособления.
Например, ряд плоских изделий притирают при помощи медных и чугунных вращающихся дисков. На плоскости диска имеются радиальные канавки, расположенные на расстоянии 30– 50 мм одна от другой. Для притирки на вращающихся дисках существуют специальные станки. Иногда диск закрепляют на шпинделе шлифовального станка. Притирка при помощи вращающегося диска менее точна, чем притирка на плите. Поэтому чаще применяют ее лишь для предварительной обработки. Весьма высокую точность дает притирка на стеклянных плитах, которые применяют для окончательной доводки калибров, плиток и т.п. В этом случае часто притирку ведут на одном масле, а порошком служат остатки порошковой пыли на плоскостях изделия от предварительной притирки или паста ГОИ. Механизированную притирку с успехом применяют при ремонте направляющих станины вместо окончательного шабрения (чаще всего при ремонте продольно-строгальных станков). На предварительно пришабренные направляющие наносят слой пасты ГОИ (грубой), накладывают стол станка, являющийся в данном случае притиром, и приводят его в движение от редуктора станка. Через 8–10 двойных ходов изношенную пасту удаляют и направляющие промывают керосином. По мере притирки на направляющих появляются матовые пятна, характеризующие снятие металла в этих местах. К концу притирки (через 5–7 ч) поверхность направляющих станины получает на 90% матовый оттенок с проблесками редких светящихся пятен. На этом притирку заканчивают, тщательно промывают и разбивают пятна шабером, что предохраняет направляющие от задиров при работе станка.
Техника безопасности при притирке и доводке:
Тема 14: «Лужение и пайка»
Пайка – это процесс создания неразъемного соединения металлов с помощью присадочного связующего материала, называемого припоем, причем припой в процессе пайки доводится до жидкого состояния. Температура плавления припоя значительно ниже, чем соединяемых металлов.
Неразъемное соединение металлов пайкой может быть выполнено паяльником, в газовом пламени, пайкой в печах, в ванне, химическим способом, автогенной пайкой и др.
Для пайки припоем необходимы паяльники, припои, а также очищающие, травящие и предупреждающие окисление поверхности во время пайки средства.
Паяльник – это ручной инструмент различной формы и массы. Часть паяльника, которой непосредственно паяют, выполняется из меди. Нагрев медной части паяльника можно производить с помощью электричества (электрический паяльник), над газовым пламенем (газовый паяльник) или в горне.
Для нагрева паяльников и некоторого прогрева соединяемых металлов могут применяться паяльные бензиновые лампы.
Рисунок24. Паяльники:
а – обычный, нагреваемый пламенем; б – электрический; в – паяльная лампа
Мягкими припоями являются оловянно-свинцовые (с добавлением или без добавления сурьмы). Температура плавления этих припоев от 183 до 305 °C.
Твердость припоя определяется маркой и химическим составом применяемых для припоя металлов. Припои делаются на основе меди, латуни, серебра, никеля и алюминия. Кроме того, различают жаропрочные и нержавеющие припои на основе никеля, марганца, серебра, золота, палладия, кобальта и железа. Температура плавления твердых припоев составляет от 600 до 1450 °C
К химическим очищающим и травящим средствам относятся: соляная кислота, хлорид цинка, бура, борная кислота, нашатырь. Можно очистить поверхность механическими средствами, абразивным материалом или напильником либо металлическими щетками. Во время пайки поверхность предохраняется от окисления такими средствами, как стеарин, скипидар и канифоль.
Хлорид цинка – это химическое соединение соляной кислоты с цинком. Получают его путем помещения в разбавленную соляную кислоту кусочков цинка. После окончания реакции (прекращение выделения водорода) хлорид цинка следует слить в другую посуду, оставив осадок в прежней посуде. Разбавлять кислоту следует путем добавления в нее воды, а не наоборот.
Мягкие припои применяются для неразъемного соединения и уплотнения металлов при незначительных требованиях к прочности и выносливости соединения на растяжение и удар, твердые припои – для неразъемных и герметичных соединений большой прочности и выносливости на растяжение и удары.
Припои выпускаются в виде листа, ленты, прутков, проволоки, сеток, блоков, фольги, зерен, порошков и паяльной пасты.
Лужением называется покрытие поверхности металлических изделий тонким слоем олова или сплавом на основе олова. Цинкование производится способом холодного электролитического или горячего покрытия металлических изделий тонким слоем цинка.
Лужение и цинкование применяются, например, в слесарном деле при производстве бытовых изделий, в пищевой промышленности, в строительстве как средство для защиты от коррозии, окисления и образования химических соединений, вредных для здоровья и разрушающих металл.
Для лужения и цинкования в зависимости от детали и ее назначения нужно иметь чистое олово, цинк или их сплавы, паяльную лампу либо газовую горелку, очищающие средства, необходимые для обезжиривания и очистки поверхностей, подвергающихся лужению или цинкованию, ванны для плавки олова или цинка, обтирочный материал и клещи.
Подшипниковый сплав – это сплав металлов (олова, свинца, меди, сурьмы и др.), служащий для изготовления вкладышей подшипников скольжения заливкой. Во вкладышах из подшипникового сплава при вращении в них валов возникает очень незначительное трение.
Подбор наиболее соответствующих заданным условиям подшипниковых сплавов производят с учетом их физико-механических свойств, в частности антифрикционных свойств, способности выдерживать определенные давления и температуры, твердости, вязкости, литейных качеств и др.
Свойства подшипникового сплава определяет его главный компонент.
Различают подшипниковые сплавы на оловянной, свинцовой, алюминиевой, кадмиевой, цинковой, медной (бронза, латунь) и других основах. Чаще всего используют подшипниковые сплавы на основе олова, свинца или меди.
Жидкий подшипниковый сплав получают в графитовом или чугунном тигле. Тигель подогревают паяльной лампой, на кузнечном горне или пламенем газовых горелок.
Температура отливки подшипниковых сплавов на основе олова или свинца составляет от 450 до 600 °C. Температура плавления бронзы составляет от 940 до 1090 °C. На расплавленный подшипниковый сплав перед разливкой насыпается измельченный древесный уголь, который предохраняет сплав от окисления.
Металлизация напылением – это нанесение металлического покрытия на поверхность изделия путем разбрызгивания под давлением расплавленного металла.
Эта операция выполняется с помощью специальных пистолетов. Металлизация применяется с целью предохранения изделий от коррозии, а также для ремонта изношенных деталей машин, для исправления дефектных отливок, а также для исправления дефектов, возникающих в результате обработки резанием.
Склеиванием называют неразъемное соединение деталей изделий путем обмазки соединяемых поверхностей изделия веществом (или смесью веществ), называемым клеем, их соединения и выдерживания под некоторой нагрузкой до затвердения клея. В ряде случаев применяется подогрев склеенных деталей.
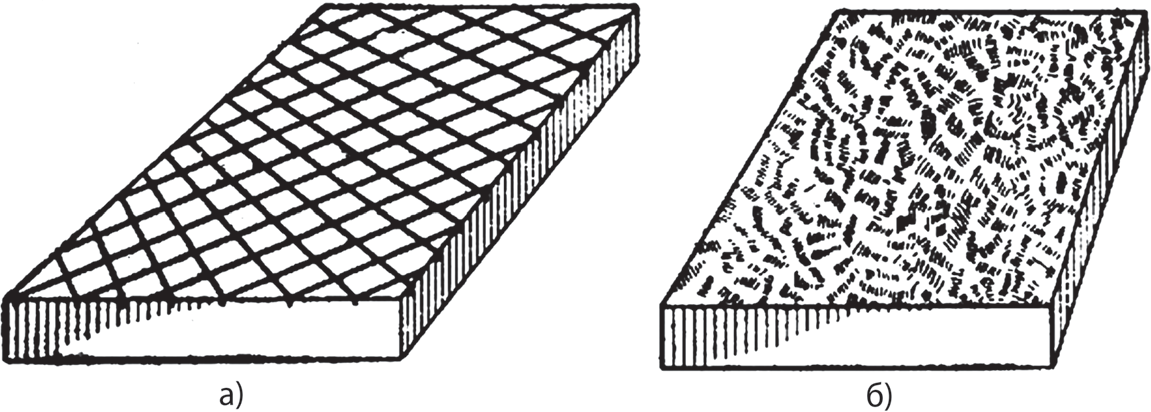
Рисунок 23. Притиры для обработки плоскостей: а – плита с канавками для грубой притирки; б – плита для чистовой притирки
Притирка (доводка) плоских поверхностей. Эту операцию обычно выполняют с применением минерального масла, технического сала, керосина, бензина. Притирать или доводить всухую не рекомендуется, так как абразивный порошок при этом распределяется неравномерно и, кроме того, детали нагреваются и может произойти их коробление.
Различные притиры требуют различной смазки. Для притиров из чугуна в качестве смазки берут керосин или бензин, из мягкой стали – машинное масло, из меди – машинное масло, спирт и содовую воду. Стальные детали притирают с применением машинного масла и технического сала, бронзовые сала, чугунные-керосина. При особо высоких требованиях к качеству стальной поверхности применяют венскую известь, разведенную в спирте, или крокус в вазелине. Алюминий притирают трепелом, разведенным в толуоле со стеариновой кислотой или в деревянном масле.
Плоские несопрягаемые поверхности чаще всего притирают вручную на неподвижных притирочных плитах.
Притирочные плиты для предварительной притирки снабжают продольными и поперечными канавками. Эти канавки выполняют шириной и глубиной 1–2 мм на расстоянии 15–20 мм друг друга. Канавки предназначены для сбора снимаемой стружки металла и выпадающих из поверхности плиты зерен абразива. Плиты для окончательной притирки канавок не имеют. Притирка на плитах дает очень точные результаты, поэтому на них притирают детали, требующие особо высокой точности, в частности, лекальные линейки, шаблоны, калибры, плитки.
Для притирки деталей плиту шаржируют абразивом или наносят на нее тонким равномерным слоем смешанный с маслом абразивный порошок.
Поверхность под притирку тщательно готовят. Лучшие результаты дает предварительное шлифование. Припуск на притирку оставляют не более 0,02 мм (большие припуски увеличивают трудоемкость).
Обрабатываемое изделие кладут притираемой поверхностью на плиту и с легким нажимом перемещают его круговыми в сочетаниями с прямолинейными движениями по всей поверхности плиты. При этом выступающие острые ребра частиц абразива, находящиеся на притире, срезают с изделия очень тонкий слой металла. Нажим на изделие должен быть равномерным и несильным. Необходимо следить, чтобы не было сильного нагрева детали. Если деталь нагрелась, то притирку приостанавливают и дают изделию остыть.
Узкие поверхности и тонкие изделия (шаблоны, угольники, линейки) притирают при помощи металлического бруска, который прижимают к детали сбоку и вместе с ней перемещают по притиру. Такие бруски служат направляющими, без них трудно удержать изделие в вертикальном положении.
Притирку со сменой слоя абразивной массы повторяют несколько раз, пока обрабатываемая поверхность не достигнет необходимого качества.
Окончательную притирку для придания поверхности блеска производят на одном масле с прибавлением остатков абразивного порошка от предварительной притирки.
Для притирки плоских поверхностей, кроме плит, применяют различные приспособления.
Например, ряд плоских изделий притирают при помощи медных и чугунных вращающихся дисков. На плоскости диска имеются радиальные канавки, расположенные на расстоянии 30– 50 мм одна от другой. Для притирки на вращающихся дисках существуют специальные станки. Иногда диск закрепляют на шпинделе шлифовального станка. Притирка при помощи вращающегося диска менее точна, чем притирка на плите. Поэтому чаще применяют ее лишь для предварительной обработки. Весьма высокую точность дает притирка на стеклянных плитах, которые применяют для окончательной доводки калибров, плиток и т.п. В этом случае часто притирку ведут на одном масле, а порошком служат остатки порошковой пыли на плоскостях изделия от предварительной притирки или паста ГОИ. Механизированную притирку с успехом применяют при ремонте направляющих станины вместо окончательного шабрения (чаще всего при ремонте продольно-строгальных станков). На предварительно пришабренные направляющие наносят слой пасты ГОИ (грубой), накладывают стол станка, являющийся в данном случае притиром, и приводят его в движение от редуктора станка. Через 8–10 двойных ходов изношенную пасту удаляют и направляющие промывают керосином. По мере притирки на направляющих появляются матовые пятна, характеризующие снятие металла в этих местах. К концу притирки (через 5–7 ч) поверхность направляющих станины получает на 90% матовый оттенок с проблесками редких светящихся пятен. На этом притирку заканчивают, тщательно промывают и разбивают пятна шабером, что предохраняет направляющие от задиров при работе станка.
Техника безопасности при притирке и доводке:
-
В процессе ручной и механизированной притирки, как и при выполнении других слесарных операций, необходимо строго соблюдать правила техники безопасности. Так, при ручной притирке не следует слишком быстро перемещать деталь, так как она может упасть и травмировать работающего. Притираемую деталь в закрепленном в тисках притире нельзя ударять о губки тисков, в противном случае возможны ущемления пальцев и порча детали.
-
При выполнении притирки ручным механизированным инструментом электрического и пневматического действия нужно соблюдать ранее описанные правила пользования этими инструментами. -
Не разрешается держать руки вблизи вращающегося притира. Нажим на притираемую поверхность нужно осуществлять плавным последовательным усилием. При работе притиром, укрепленным в механизированном инструменте, нужно следить за тем, чтобы не было биения притира. Кроме того, он не должен иметь трещин, неравномерных выработок и других неисправностей. -
Обрабатываемые детали или притиры необходимо крепить в механизированном инструменте правильно и устойчиво, чтобы исключалось их смещение во время работы. Нельзя очищать притираемую поверхность голыми руками; для этого нужно пользоваться чистыми тряпками и ветошью. -
Следует помнить, что сухая обработка деталей притирами сопряжена с образованием большого количества пыли, поэтому рекомендуется работать в предохранительных очках, пользоваться защитными устройствами для отсасывания пыли и т. д.
Тема 14: «Лужение и пайка»
Пайка – это процесс создания неразъемного соединения металлов с помощью присадочного связующего материала, называемого припоем, причем припой в процессе пайки доводится до жидкого состояния. Температура плавления припоя значительно ниже, чем соединяемых металлов.
Неразъемное соединение металлов пайкой может быть выполнено паяльником, в газовом пламени, пайкой в печах, в ванне, химическим способом, автогенной пайкой и др.
Для пайки припоем необходимы паяльники, припои, а также очищающие, травящие и предупреждающие окисление поверхности во время пайки средства.
Паяльник – это ручной инструмент различной формы и массы. Часть паяльника, которой непосредственно паяют, выполняется из меди. Нагрев медной части паяльника можно производить с помощью электричества (электрический паяльник), над газовым пламенем (газовый паяльник) или в горне.
Для нагрева паяльников и некоторого прогрева соединяемых металлов могут применяться паяльные бензиновые лампы.
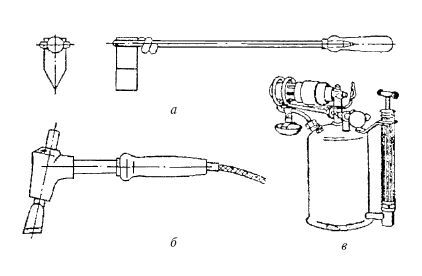
Рисунок24. Паяльники:
а – обычный, нагреваемый пламенем; б – электрический; в – паяльная лампа
Мягкими припоями являются оловянно-свинцовые (с добавлением или без добавления сурьмы). Температура плавления этих припоев от 183 до 305 °C.
Твердость припоя определяется маркой и химическим составом применяемых для припоя металлов. Припои делаются на основе меди, латуни, серебра, никеля и алюминия. Кроме того, различают жаропрочные и нержавеющие припои на основе никеля, марганца, серебра, золота, палладия, кобальта и железа. Температура плавления твердых припоев составляет от 600 до 1450 °C
К химическим очищающим и травящим средствам относятся: соляная кислота, хлорид цинка, бура, борная кислота, нашатырь. Можно очистить поверхность механическими средствами, абразивным материалом или напильником либо металлическими щетками. Во время пайки поверхность предохраняется от окисления такими средствами, как стеарин, скипидар и канифоль.
Хлорид цинка – это химическое соединение соляной кислоты с цинком. Получают его путем помещения в разбавленную соляную кислоту кусочков цинка. После окончания реакции (прекращение выделения водорода) хлорид цинка следует слить в другую посуду, оставив осадок в прежней посуде. Разбавлять кислоту следует путем добавления в нее воды, а не наоборот.
Мягкие припои применяются для неразъемного соединения и уплотнения металлов при незначительных требованиях к прочности и выносливости соединения на растяжение и удар, твердые припои – для неразъемных и герметичных соединений большой прочности и выносливости на растяжение и удары.
Припои выпускаются в виде листа, ленты, прутков, проволоки, сеток, блоков, фольги, зерен, порошков и паяльной пасты.
Лужением называется покрытие поверхности металлических изделий тонким слоем олова или сплавом на основе олова. Цинкование производится способом холодного электролитического или горячего покрытия металлических изделий тонким слоем цинка.
Лужение и цинкование применяются, например, в слесарном деле при производстве бытовых изделий, в пищевой промышленности, в строительстве как средство для защиты от коррозии, окисления и образования химических соединений, вредных для здоровья и разрушающих металл.
Для лужения и цинкования в зависимости от детали и ее назначения нужно иметь чистое олово, цинк или их сплавы, паяльную лампу либо газовую горелку, очищающие средства, необходимые для обезжиривания и очистки поверхностей, подвергающихся лужению или цинкованию, ванны для плавки олова или цинка, обтирочный материал и клещи.
Подшипниковый сплав – это сплав металлов (олова, свинца, меди, сурьмы и др.), служащий для изготовления вкладышей подшипников скольжения заливкой. Во вкладышах из подшипникового сплава при вращении в них валов возникает очень незначительное трение.
Подбор наиболее соответствующих заданным условиям подшипниковых сплавов производят с учетом их физико-механических свойств, в частности антифрикционных свойств, способности выдерживать определенные давления и температуры, твердости, вязкости, литейных качеств и др.
Свойства подшипникового сплава определяет его главный компонент.
Различают подшипниковые сплавы на оловянной, свинцовой, алюминиевой, кадмиевой, цинковой, медной (бронза, латунь) и других основах. Чаще всего используют подшипниковые сплавы на основе олова, свинца или меди.
Жидкий подшипниковый сплав получают в графитовом или чугунном тигле. Тигель подогревают паяльной лампой, на кузнечном горне или пламенем газовых горелок.
Температура отливки подшипниковых сплавов на основе олова или свинца составляет от 450 до 600 °C. Температура плавления бронзы составляет от 940 до 1090 °C. На расплавленный подшипниковый сплав перед разливкой насыпается измельченный древесный уголь, который предохраняет сплав от окисления.
Металлизация напылением – это нанесение металлического покрытия на поверхность изделия путем разбрызгивания под давлением расплавленного металла.
Эта операция выполняется с помощью специальных пистолетов. Металлизация применяется с целью предохранения изделий от коррозии, а также для ремонта изношенных деталей машин, для исправления дефектных отливок, а также для исправления дефектов, возникающих в результате обработки резанием.
Склеиванием называют неразъемное соединение деталей изделий путем обмазки соединяемых поверхностей изделия веществом (или смесью веществ), называемым клеем, их соединения и выдерживания под некоторой нагрузкой до затвердения клея. В ряде случаев применяется подогрев склеенных деталей.