Файл: Учебный курс для студентов очной и заочной форм обучения.doc
ВУЗ: Не указан
Категория: Не указан
Дисциплина: Не указана
Добавлен: 11.12.2023
Просмотров: 876
Скачиваний: 6
ВНИМАНИЕ! Если данный файл нарушает Ваши авторские права, то обязательно сообщите нам.
, то есть сжатие витка от единичной силы, ;
G – модуль сдвига.
Потребное число рабочих витков определяют по условию, по которому при возрастании нагрузки от установочной (начальной) Fmin до максимальной Fmax пружина должна получить заданное упругое перемещение
. (5)
Откуда вычисляют число витков
. (6)
Полная длина ненагруженной пружины составляет
, (7)
где Н3 – длина пружины, сжатой до соприкосновения соседних рабочих витков, , полное число витков уменьшено на 0,5 из-за шлифовки каждого конца пружины на 0,25d для образования плоского опорного торца.
i1 – полное число витков, , дополнительные 1,5…2,0 витка идут на поджатие для создания опорных поверхностей пружин.
Максимальная осадка пружины, т. е. перемещение торца пружины до полного соприкосновения витков составляет,
. (8)
Шаг пружины определяется по зависимости
. (9)
Длину проволоки для изготовления пружины рассчитывают из соотношения
. (10)
Зависимость между нагрузкой и осадкой пружины сжатия показана на рис. 7.
Рис.7. Диаграмма пружины сжатия
Вопросы для самопроверки
- По какому признаку в конструкции машины можно найти упругие элементы ?
- Для каких задач применяются упругие элементы ?
- Какая характеристика упругого элемента считается главной ?
- Из каких материалов следует изготавливать упругие элементы ?
Раздел 13. Методы повышения конструкционной прочности деталей машин
Характеристики механических свойств конструкционных материалов для изготовления деталей машин (характеристики упругости, прочности, пластичности и др.) определяют путем испытаний стандартных образцов в стандартных условиях. В реальных конструкциях эти свойства не всегда проявляются в полной мере. Особенно заметно это
несоответствие между характеристиками прочности, полученными при испытании лабораторных образцов, и конструкционной прочностью как максимальным сопротивлением материала, реализуемым в деталях машин.
Особый характер проявления механических свойств материала, воплощенного в деталь или конструкцию, связан с влиянием трех групп факторов: эксплуатационных, технологических и конструкционных.
Эксплуатационные факторы.
Эксплуатационные факторы определяются назначением детали и условиями его эксплуатации (температурой, видом и характером нагружения, окружающей средой и т.п.); они определяют выбор материала для проектируемого изделия и конструкции.
Большой эффективности в повышении конструкционной прочности и снижении материалоемкости изделий можно достичь за счет технологических факторов, связанных с предысторией металлургической, механической и термической переработки материала.
Технологические методы.
Известно, что прочность – это свойство материала, зависящее от его природы (химического состава) и структурного состояния. Прочность реальных конструкционных материалов из-за наличия дефектов структуры на два-три порядка ниже теоретической, характеризуемой сопротивлением разрыву межатомных связей. Поэтому практически все технологические методы повышения конструкционной прочности материалов основаны на создании такого структурного состояния, при котором обеспечивалось бы сведение к минимуму влияние имеющихся дефектов, в том числе, на субмикроуровне (дислокаций). Это осуществляется путем легирования, предварительной пластической деформации, термической, термомеханической, химико-термической обработок. Необходимые характеристики физико-механических свойств достигаются и повышением чистоты выплавляемого металла. Для этого в промышленности все более широко внедряется вакуумно-дуговой, электронно-лучевой и другие виды переплавов.
За счет применения выше перечисленных технологических методов удается достичь высоких уровней прочности материалов: для сталей - =1600...2000 МПа, для титановых сплавов - =1000...1250 МПа, для алюминиевых сплавов - =550...600 МПа и т.п.
Для повышения циклической прочности и износостойкости применяют технологические методы поверхностного упрочнения, поверхностную закалку, химико-термическую обработку (азотирование, цементацию), поверхностное пластическое деформирование (обдувку дробью, обкатку роликами и др.).
Следует иметь в виду, что повышение характеристик прочности материала путем использования различных технологических приемов, как правило, сопровождается снижением характеристик пластичности и вязкости разрушения. Показателен в этом отношении характер зависимости конструкционной прочности от взаимного сопротивления материала . Наличие на этой зависимости максимума свидетельствует о том, что повышение за счет термообработки или иными способами имеет смысл только до определенных пределов, так как снижение при этом пластичности препятствует перераспределению напряжений в зонах концентрации, а снижение вязкости повышает вероятность хрупкого разрушения. Отметим, если деталь изготовлена из пластичных материалов, то к эффективным способам оптимизации распределения напряжений можно отнести тренировку изготовленного изделия с перегрузками (автофретирование). Этот способ упрочнения деталей применим только в том случае, если в процессе эксплуатации нагрузка не изменяет знак.
В настоящее время для достижения высокой конструкционной прочности широко используются композиционные материалы, состоящие из мягкой матрицы и высокопрочных волокон, оптимально ориентированных по отношению к действующему в детали полю напряжений. Композиционные материалы позволяют рационально согласовать «поля напряжений» с «полями сопротивлений» материала. Они отличаются высокой трещиностойкостью, так как при образовании трещин, например, из-за разрушения волокна, ее распределение тормозится мягкой матрицей. Недостатком композиционных материалов на неметаллической основе является их интенсивное старение, сопровождающееся охрупчиванием.
Конструкционные методы.
Принцип равнопрочности всех высоконапряженных деталей, составляющих изделие, осуществить практически невозможно. Тем не менее, использование более достоверных расчетных схем в сочетании с приемами оптимального конструирования является важным резервом повышения несущей способности изделия, более полного использования свойств материала в детали. Высокие показатели использования резерва прочности материала не всегда адекватны экономическим показателям в части стоимости изделия.
К основным правилам конструирования относятся следующие:
Необходимо избегать резких концентраторов напряжений – больших перепадов жесткостей, глубоких канавок, галтелей малого радиуса и т.п. Концентрация напряжений может быть вызвана дефектами материала (микротрещины, раковины, включения), а также действием сопряженной детали, например, при использовании посадок с гарантированным натягом. Циклическая прочность может резко снижаться при наличии царапин на поверхности, повреждений поверхностного слоя при грубой механической обработке, кислотном травлении. Поэтому при проектировании изделий следует предусматривать специальные меры по обеспечению и сохранению в процессе работы хорошего состояния поверхности деталей. Для этого используют различного рода покрытия, предупреждающие коррозию металла, водородное и другие виды охрупчивания. Однако некоторые виды покрытий, например, гальванические, могут способствовать снижению циклической прочности.
В местах резких изменений размеров ступенчатых деталей лучше использовать конические переходы, эллиптические или поднутренные галтели, а также декомпенсаторы в виде канавок на поверхности большого размера. Кромки отверстий подвергают обжатию или обчеканке. Благоприятное расположение пятна контакта в зонах приложения сосредоточенных нагрузок достигается приданием поверхности бочкообразной формы (бомбинированием), применением смазок, изготовлением контактируемых поверхностей с кривизной одинакового знака, заменой точечного контракта линейным, введением самоустанавливающихся башмаков.
Уровень остаточных напряжений в деталях машин
, в том числе монтажных напряжений, должен быть сведен до минимума. Необходимую несущую способность соединений с гарантированным натягом лучше обеспечивать не за счет натяга, а за счет длины контактируемых поверхностей. При этом соединяемые детали должны обладать приблизительно одинаковой жесткостью в радиальном направлении. Для уменьшения деформаций при сварке и снижения сварочных напряжений применяют конструкции с симметричным расположением швов, избегают их пересечения, делают сварные швы прерывистыми, не располагают их вблизи элементов жесткости.
Коэффициент использования металла по критериям прочности и жесткости можно значительно повысить применением рациональных сечений с усилениями наиболее нагруженных зон (двутавровой балки), полых деталей в виде труб, коробок, тонкостенных элементов других форм, подкрепленных поперечными и диагональными связями (раскосами), ребрами или гофрами, а также ячеистых и сотовых деталей. Эффективными могут оказаться конструкции, в которых несущие элементы, работающие при высоких градиентах напряжений (на изгиб, кручение), заменены элементами, работающими на растяжение и сжатие. Иногда остаточные напряжения сжатия различными способами формируются в локальных зонах для «смягчения» концентрации напряжений.
Конструкции деталей машин, работающих при высоких или низких температурах, особенно в неизотермических условиях, должна исключать возможность возникновения высоких температурных градиентов, приводящих к термическим напряжениям. С этой целью в каждом узле следует использовать материалы с близкими коэффициентами линейного расширения и одинаковой теплопроводностью.
Понижение температуры эксплуатации изделия сопровождается ростом вероятности хрупкого разрушения несущих элементов, особенно в зонах сварных швов. В этих случаях очень важно избегать высоких концентраций напряжений любой природы, использовать геометрические формы деталей, исключающие работу материала при двух- и трехосном растяжении, обеспечивать низкие запасы упругой энергии в силовых элементах. В отдельных случаях необходимо предусматривать специальные «ловушки», останавливающие развивающуюся трещину.
Статистика и анализ отказов машин свидетельствует о том
G – модуль сдвига.
Потребное число рабочих витков определяют по условию, по которому при возрастании нагрузки от установочной (начальной) Fmin до максимальной Fmax пружина должна получить заданное упругое перемещение
. (5)
Откуда вычисляют число витков
. (6)
Полная длина ненагруженной пружины составляет
, (7)
где Н3 – длина пружины, сжатой до соприкосновения соседних рабочих витков, , полное число витков уменьшено на 0,5 из-за шлифовки каждого конца пружины на 0,25d для образования плоского опорного торца.
i1 – полное число витков, , дополнительные 1,5…2,0 витка идут на поджатие для создания опорных поверхностей пружин.
Максимальная осадка пружины, т. е. перемещение торца пружины до полного соприкосновения витков составляет,
. (8)
Шаг пружины определяется по зависимости
. (9)
Длину проволоки для изготовления пружины рассчитывают из соотношения
. (10)
Зависимость между нагрузкой и осадкой пружины сжатия показана на рис. 7.
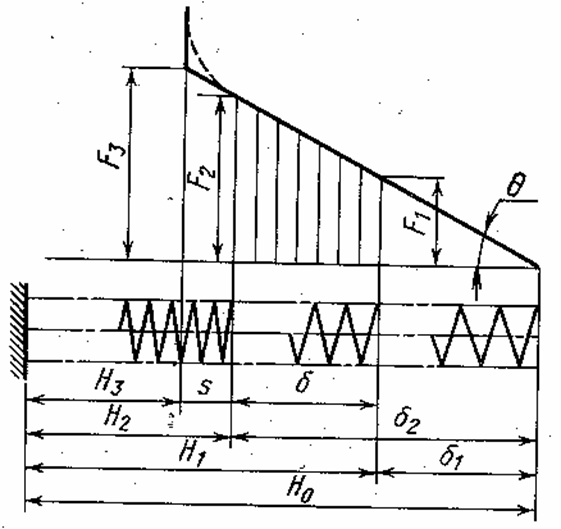
Рис.7. Диаграмма пружины сжатия
Вопросы для самопроверки
- По какому признаку в конструкции машины можно найти упругие элементы ?
- Для каких задач применяются упругие элементы ?
- Какая характеристика упругого элемента считается главной ?
- Из каких материалов следует изготавливать упругие элементы ?
Раздел 13. Методы повышения конструкционной прочности деталей машин
Характеристики механических свойств конструкционных материалов для изготовления деталей машин (характеристики упругости, прочности, пластичности и др.) определяют путем испытаний стандартных образцов в стандартных условиях. В реальных конструкциях эти свойства не всегда проявляются в полной мере. Особенно заметно это
несоответствие между характеристиками прочности, полученными при испытании лабораторных образцов, и конструкционной прочностью как максимальным сопротивлением материала, реализуемым в деталях машин.
Особый характер проявления механических свойств материала, воплощенного в деталь или конструкцию, связан с влиянием трех групп факторов: эксплуатационных, технологических и конструкционных.
Эксплуатационные факторы.
Эксплуатационные факторы определяются назначением детали и условиями его эксплуатации (температурой, видом и характером нагружения, окружающей средой и т.п.); они определяют выбор материала для проектируемого изделия и конструкции.
Большой эффективности в повышении конструкционной прочности и снижении материалоемкости изделий можно достичь за счет технологических факторов, связанных с предысторией металлургической, механической и термической переработки материала.
Технологические методы.
Известно, что прочность – это свойство материала, зависящее от его природы (химического состава) и структурного состояния. Прочность реальных конструкционных материалов из-за наличия дефектов структуры на два-три порядка ниже теоретической, характеризуемой сопротивлением разрыву межатомных связей. Поэтому практически все технологические методы повышения конструкционной прочности материалов основаны на создании такого структурного состояния, при котором обеспечивалось бы сведение к минимуму влияние имеющихся дефектов, в том числе, на субмикроуровне (дислокаций). Это осуществляется путем легирования, предварительной пластической деформации, термической, термомеханической, химико-термической обработок. Необходимые характеристики физико-механических свойств достигаются и повышением чистоты выплавляемого металла. Для этого в промышленности все более широко внедряется вакуумно-дуговой, электронно-лучевой и другие виды переплавов.
За счет применения выше перечисленных технологических методов удается достичь высоких уровней прочности материалов: для сталей - =1600...2000 МПа, для титановых сплавов - =1000...1250 МПа, для алюминиевых сплавов - =550...600 МПа и т.п.
Для повышения циклической прочности и износостойкости применяют технологические методы поверхностного упрочнения, поверхностную закалку, химико-термическую обработку (азотирование, цементацию), поверхностное пластическое деформирование (обдувку дробью, обкатку роликами и др.).
Следует иметь в виду, что повышение характеристик прочности материала путем использования различных технологических приемов, как правило, сопровождается снижением характеристик пластичности и вязкости разрушения. Показателен в этом отношении характер зависимости конструкционной прочности от взаимного сопротивления материала . Наличие на этой зависимости максимума свидетельствует о том, что повышение за счет термообработки или иными способами имеет смысл только до определенных пределов, так как снижение при этом пластичности препятствует перераспределению напряжений в зонах концентрации, а снижение вязкости повышает вероятность хрупкого разрушения. Отметим, если деталь изготовлена из пластичных материалов, то к эффективным способам оптимизации распределения напряжений можно отнести тренировку изготовленного изделия с перегрузками (автофретирование). Этот способ упрочнения деталей применим только в том случае, если в процессе эксплуатации нагрузка не изменяет знак.
В настоящее время для достижения высокой конструкционной прочности широко используются композиционные материалы, состоящие из мягкой матрицы и высокопрочных волокон, оптимально ориентированных по отношению к действующему в детали полю напряжений. Композиционные материалы позволяют рационально согласовать «поля напряжений» с «полями сопротивлений» материала. Они отличаются высокой трещиностойкостью, так как при образовании трещин, например, из-за разрушения волокна, ее распределение тормозится мягкой матрицей. Недостатком композиционных материалов на неметаллической основе является их интенсивное старение, сопровождающееся охрупчиванием.
Конструкционные методы.
Принцип равнопрочности всех высоконапряженных деталей, составляющих изделие, осуществить практически невозможно. Тем не менее, использование более достоверных расчетных схем в сочетании с приемами оптимального конструирования является важным резервом повышения несущей способности изделия, более полного использования свойств материала в детали. Высокие показатели использования резерва прочности материала не всегда адекватны экономическим показателям в части стоимости изделия.
К основным правилам конструирования относятся следующие:
Необходимо избегать резких концентраторов напряжений – больших перепадов жесткостей, глубоких канавок, галтелей малого радиуса и т.п. Концентрация напряжений может быть вызвана дефектами материала (микротрещины, раковины, включения), а также действием сопряженной детали, например, при использовании посадок с гарантированным натягом. Циклическая прочность может резко снижаться при наличии царапин на поверхности, повреждений поверхностного слоя при грубой механической обработке, кислотном травлении. Поэтому при проектировании изделий следует предусматривать специальные меры по обеспечению и сохранению в процессе работы хорошего состояния поверхности деталей. Для этого используют различного рода покрытия, предупреждающие коррозию металла, водородное и другие виды охрупчивания. Однако некоторые виды покрытий, например, гальванические, могут способствовать снижению циклической прочности.
В местах резких изменений размеров ступенчатых деталей лучше использовать конические переходы, эллиптические или поднутренные галтели, а также декомпенсаторы в виде канавок на поверхности большого размера. Кромки отверстий подвергают обжатию или обчеканке. Благоприятное расположение пятна контакта в зонах приложения сосредоточенных нагрузок достигается приданием поверхности бочкообразной формы (бомбинированием), применением смазок, изготовлением контактируемых поверхностей с кривизной одинакового знака, заменой точечного контракта линейным, введением самоустанавливающихся башмаков.
Уровень остаточных напряжений в деталях машин
, в том числе монтажных напряжений, должен быть сведен до минимума. Необходимую несущую способность соединений с гарантированным натягом лучше обеспечивать не за счет натяга, а за счет длины контактируемых поверхностей. При этом соединяемые детали должны обладать приблизительно одинаковой жесткостью в радиальном направлении. Для уменьшения деформаций при сварке и снижения сварочных напряжений применяют конструкции с симметричным расположением швов, избегают их пересечения, делают сварные швы прерывистыми, не располагают их вблизи элементов жесткости.
Коэффициент использования металла по критериям прочности и жесткости можно значительно повысить применением рациональных сечений с усилениями наиболее нагруженных зон (двутавровой балки), полых деталей в виде труб, коробок, тонкостенных элементов других форм, подкрепленных поперечными и диагональными связями (раскосами), ребрами или гофрами, а также ячеистых и сотовых деталей. Эффективными могут оказаться конструкции, в которых несущие элементы, работающие при высоких градиентах напряжений (на изгиб, кручение), заменены элементами, работающими на растяжение и сжатие. Иногда остаточные напряжения сжатия различными способами формируются в локальных зонах для «смягчения» концентрации напряжений.
Конструкции деталей машин, работающих при высоких или низких температурах, особенно в неизотермических условиях, должна исключать возможность возникновения высоких температурных градиентов, приводящих к термическим напряжениям. С этой целью в каждом узле следует использовать материалы с близкими коэффициентами линейного расширения и одинаковой теплопроводностью.
Понижение температуры эксплуатации изделия сопровождается ростом вероятности хрупкого разрушения несущих элементов, особенно в зонах сварных швов. В этих случаях очень важно избегать высоких концентраций напряжений любой природы, использовать геометрические формы деталей, исключающие работу материала при двух- и трехосном растяжении, обеспечивать низкие запасы упругой энергии в силовых элементах. В отдельных случаях необходимо предусматривать специальные «ловушки», останавливающие развивающуюся трещину.
Статистика и анализ отказов машин свидетельствует о том