Файл: В настоящее время на промышленных предприятиях применяют несколько способов получения заготовок из металла.docx
ВУЗ: Не указан
Категория: Не указан
Дисциплина: Не указана
Добавлен: 12.12.2023
Просмотров: 35
Скачиваний: 1
ВНИМАНИЕ! Если данный файл нарушает Ваши авторские права, то обязательно сообщите нам.

Введение.
В настоящее время на промышленных предприятиях применяют несколько способов получения заготовок из металла:
1) снятие слоя металла с заготовки;
2) дутьё под давлением;
3) штамповка.
На большинстве предприятий используют метод снятия слоя металла на металлорежущих станках. Металлорежущие станки предназначены для механической обработки заготовок из металла режущими инструментами путём снятия стружки с заготовки, придавая ей требуемые форму, размеры и чистоту поверхности.
Металлорежущие станки по количеству типов и потребляемой ими электроэнергии занимают одно из основных мест среди электрифицированных машин и агрегатов. Электрооборудование и автоматика станков оснащаются современными типами электроприводов и средствами автоматического управления, что обеспечивает высокую производительность и точность обработки, безопасность и удобства управления и обслуживания их.
В соответствии с действующей документацией, в зависимости от характера выполняемых работ, вида применяемых инструментов и формы образуемой поверхности металлорежущие станки подразделяются на следующие группы:
1) токарные;
2) сверлильные и расточные;
3) шлифовальные;
4) комбинированные;
5) зубо- и резьбообрабатывающие;
6) фрезерные;
7) строгальные и долбёжные;
8) отрезные.
Рассмотрим токарно-винторезный станок на 1М61П.
-
Назначение станка.
Токарно-винторезные станки модели 1М61П предназначены для выполнения разнообразных токарных работ в механических цехах в условиях мелкосерийного и единичного производства. Станок позволяет производить следующие виды токарных работ: проточку и расточку цилиндрических и конических поверхностей, подрезку торцов, отрезку, нарезание метрических резьб, дюймовой, модульной, питчевой, сверление и ряд других работ.
-
Устройство станка.
Основные узлы станка: 1 – станина, 2 - коробка скоростей, 3 - коробка передач, 4 - коробка подач, 5 – фартук, 6 – суппорт, 7 - задняя бабка, 8 – электрооборудование, 9 - защитный экран, 10 - система охлаждения.
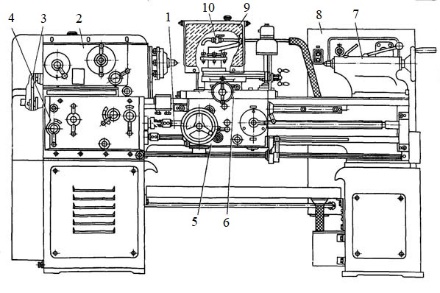
-
Принцип действия станка.
Электродвигатель через клиноременную передачу передает движение на коробку скоростей, которая обеспечивает 24 скорости вращения шпинделя. Изменение скорости вращения шпинделя производится рукоятками 1 и 3. Коробка передач (гитара) служит для передачи движения от коробки скоростей коробке подач и для настройки подач на тип нарезаемой резьбы. При нарезании метрических и модульных резьб движение передается от вала через зубчатую муфту на ходовой винт. При нарезании дюймовых и питчевых резьб движение на ходовой винт передается через шестерни. Для более точных резьб ходовой винт имеет прямое включение, без механизма цепи подач. Это достигается соответствующей наладкой шестерен гитары, поставляемых по особому заказу. Установка величины резьбы осуществляется рукоятками 5. Установка типа резьбы, включение ходового винта или ходового валика производится при помощи рукоятки 4. Фартук передает движение суппорту от ходового винта или ходового валика. Подачи суппорта при обтачивании осуществляются исключительно при помощи ходового валика ходовой винт применяется только при нарезании резьбы. Для включения продольной подачи суппорта рукоятку 13 необходимо вытянуть на себя и затем повернуть вправо влево в зависимости от требуемого направления движения суппорта.
-
Требования к электроприводу и системе управления станка.
В станке предусмотрены следующие приводы: главный привод и привод подачи охлаждающей жидкости.
К главному приводу предъявляются следующие требования, т.е. он должен:
1) обеспечивать различные режимы обработки: черновую, получистовую, чистовую;
2) быть реверсивным, т.к. на станке производятся операции по нарезанию резьбы;
3) обеспечивать точную и быструю остановку;
4) быть надёжным в эксплуатации и простым в обслуживании;
5) обеспечивать требуемую скорость обработки, а также её плавное регулирование.
Регулирование частоты вращения двигателя главного привода производится переключением шестерён коробки скоростей при помощи рукоятки. В схеме предусмотрено электродинамическое торможение этого двигателя.
Система управления предусматривает надёжную и безопасную работу на станке, т.к. она имеет все необходимые аппараты защиты и питается пониженным напряжением. Применение пониженного напряжения необходимо для обеспечения пожаробезопасности; оно подводится через трансформатор. В систему управления входят магнитные пускатели, реле, кнопки управления, выключатели и тепловые реле.
К системе управления предъявляют следующие требования:
1) безопасность и удобство управления;
2) быстрота управления;
3) защита двигателей от длительных перегрузок.
-
Расчет и выбор электродвигателей.
5.1 Расчёт мощности двигателя главного привода (М1).
Процесс обработки деталей на токарных станках происходит при определённых значениях величин, характеризующих режим резания. Режимами резания являются: глубина резания t, подача S, скорость резания U.
Назначаемая скорость резания зависит от свойств обрабатываемого материала, материала резца, вида обработки, условий охлаждения резца детали.
Определяем необходимое значение скорости резания по формуле

где Cv – коэффициент, характеризующий свойства обрабатываемого материала, резца, а также вид токарной обработки;
T – стойкость резца, мин;
t – глубина резания, мм;
S – подача, мм/об;
Xv, Yv – показатели степени зависящие от свойств обрабатываемого материла, резца и вида обработки.
Глубину резания устанавливают исходя из припуска на обработку. Так, как расчёт мощности двигателя производим при черновой обработке, глубина резания t = 5 мм. Для точения серого чугуна с твёрдостью 150НВ резцом при черновой обработке подача S = 0,23 мм/об. Принимаем подачу S=0,3 мм/об. Стойкость резца Т = 60 мин. Коэффициент и показатели степени также выбираем Cv=55; Xv=0,25; Yv=0,6; m=0,125.

Определяем усилие резания, преодолеваемое шпинделем станка по формуле:

где CF – коэффициент, характеризующий обрабатываемый материал, материал резца и вид токарной обработки;
XF, YF, nF – показатели степени, зависящие от свойств обрабатываемого материала, резца и вида обработки.
Выбираем коэффициент и показатели степени
CF=200; XF=1,0; YF=0,75; nF=0

Определяем мощность резания по формуле


Определяем мощность на валу главного двигателя в установившемся режиме с учётом потерь в передачах по формуле

где


По произведённым расчётам, скорости и ближайшей мощности выбираем по таблице Д.1 (1) асинхронный двигатель с короткозамкнутым ротором серии АИР100L4. Данные данного двигателя приведены в таблице 1.
5.2 Расчёт мощности двигателя системы охлаждения (М2).
В станке используется охлаждение режущего инструмента, для этого используется центробежный насос. В качестве охлаждающей жидкости используется СОЖ. В зону охлаждения жидкость подаётся под давлением, которое создаёт насос.
Определяем мощность двигателя насоса по формуле:
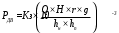
где Рдв - мощность двигателя, кВт;
ρ – плотность перекачиваемой жидкости, кг/м3;
Q – производительность насоса, м/с;
Н – статический напор, полная высота подачи жидкости, м;


Кз – коэффициент запаса;

Выбираем двигатель АИР50B2 исходя из расчётной мощности насоса из таблицы Д.1(1). Данные данного двигателя приведены в таблице 1.
Таблица 1.
Тип двигателя | Рном, кВт | КПД % | cos ![]() ![]() | Sном % | Кп | Кmax | Kmin | K1 | Момент инерции, кг∙м2 | Масса, кг |
АИР100L4 | 4 | 85 | 0,84 | 6 | 2 | 2,2 | 1,6 | 7 | 0,011 | 27,3 |
АИР50B2 | 0,12 | 63 | 0,75 | 11,5 | 2,2 | 2,2 | 1,8 | 4,5 | 0,000028 | 2,8 |
-
Описание принципиально электрической схемы токарно-винторезного станка модели 1М61П.
Управление электродвигателем M1 главного привода осуществляется рукояткой управления путевыми выключателями SQ1 и SQ2, фиксируемой в трех положениях, в нейтральном положении рукоятки размыкающие контакты путевых выключателей SQ1 и SQ2 (10-1) замкнуты.
Включением автоматического выключателя QF1 через размыкающие контакты SQ1 и SQ2 промежуточное реле KL1 получает питание и через свой замыкающий контакт переходит на самопитание. Замкнувшиеся силовые контакты реле KL1 подготавливают цепь электронасоса охлаждения. Получает питание также реле времени KT1. Размыкающий контакт реле KT с выдержкой времени 3-4 с отключает электромагнитную муфту торможения ЭМТ.
Отключение электромагнитной муфты торможения в исходном положении необходимо для свободного проворота шпинделя. Пуск электродвигателя M1 в направлении в направлении "вперед".
Для пуска электродвигателя M1 в направлении "вперед рукоятку 14 поворачивают вверх. При этом размыкается размыкающий контакт путевого выключателя SQ1 и замыкается замыкающий контакт SQ1, срабатывает контактор KM1 и включает электродвигатель M1 на вращение "вперед". Размыкающий контакт KM1 размыкается, обесточивается реле времени KT1, размыкая замыкающий контакт KT1 и замыкая размыкающий контакт KT1.
Отключение электродвигателя M1 производится переводом рукоятки 14 в нейтральное положение. При этом размыкается нормально разомкнутый контакт SQ1 и замыкается нормально замкнутый контакт SQ1. Контактор KM1 обесточивается, реле времени KT1 через контакт KM1 получает питание и замыкает свой замыкающий контакт KT1. Срабатывает электромагнитная муфта ЭМТ, получая постоянный ток от селенового выпрямителя VD, и затормаживает механизм коробки скоростей и
шпиндель. Несколько позже, с выдержкой времени 3-4 с, размыкается размыкающий контакт KT1, электромагнитная муфта отключается и система возвращается в исходное положение.
Пуск электродвигателя M1 в направлении "назад" производится переводом рукоятки 14 в нижнее положение. Работа электросхемы аналогична работе при пуске электродвигателя М1 в направлении "вперед", только в этом случае срабатывает контактор KM2.
Электронасос охлаждения М2 включается и выключается выключателем QF2 и пускателем KL1.
-
Расчет и выбор аппаратов защиты и управления.