Добавлен: 09.01.2024
Просмотров: 119
Скачиваний: 6
ВНИМАНИЕ! Если данный файл нарушает Ваши авторские права, то обязательно сообщите нам.
По окончании работ изделие рекомендуется сначала отверждать при температуре, немного превышающей комнатную. В течение 23 часов происходит т.н. отверждение «до отлипания» (первичная полимеризация), после чего изделие можно сильно нагреть, что позволит закончить процесс отверждения за 56 часов. При комнатной же температуре полная полимеризация может продлиться несколько суток (до 7 дней, согласно литературе), а при использовании ТЭТА поверхность может остаться липкой.
Заметим, что несколько граммов клея ЭДП прекрасно смешиваются и отверждаются при комнатной температуре, но когда в работе используется большое количество смолы, технология должна быть другая.
Если необходима большая толщина (больше 2 мм), то материал обычно накладывают слоями, дожидаясь первичной полимеризации предыдущего слоя перед нанесением следующего. Процесс несколько усложняется, если необходимо изготовить объёмное изделие из смолы (стеклопластик).
Эпоксидную смолу можно отливать в форму. Для обеспечения возможности отделения готового изделия от формы она смазывается жиром (например, техническим вазелином). Добавляя в смолу порошковый краситель, можно придать изделию любой цвет. Отлитое из эпоксидной смолы изделие можно в дальнейшем подвергать механической обработке (резать, шлифовать).
Для отливки объёмного изделия отечественная эпоксидная смола малопригодна, т.к. из-за неравномерности свойств изделие может неравномерно отвердиться в толще.
. Достаточно часто эпоксидные смолы применяют для ремонта бетона, железобетонных конструкций, фундаментов, а также для их усиления. Например, с помощью эпоксидного полимерраствора произведён ремонт бетонных бордюров на существующих мостах, а также увеличение их высоты.
.1 Известно, что от высоты бордюров в значительной мере зависит безопасность движения по мосту, так как они препятствуют выезду автомобилей с проезжей части на тротуары. Обследование показало, что высота бордюров на многих существующих мостах не превышает 15 см, и в случае скопления мусора и грязи, а зимой наледи вдоль бордюра автомобили беспрепятственно выезжают за пределы проезжей части. Имели место и обрушения автомобилей с мостов.
Выполнено увеличение высоты бетонных бордюров до 40 см. Проектом производства работ предусматривалось наращивание их на 25 см монолитным бетоном, для чего требовалось обнажить арматуру плиты проезжей части, установить арматурный каркас, опалубку и т.д. Технологически сложный, многодельный и трудоёмкий метод производства работ был заменён клеевым способом прикрепления готовых бордюрных блоков. Бетонные блоки ограждения длиной 1,5 м были изготовлены из бетона класса В 22,5 (марки М300). Основание блока ограждения тщательно очищалось с помощью металлических щеток от цементной корки и прогрунтовывалось. Затем раскладывался полимерраствор и на него устанавливался блок ограждения. Все работы были выполнены за 5 рабочих смен без ограничения движения транспорта по мосту. Было приклеено 225 м блоков. Несмотря на наличие следов наезда автомобилей на бордюр, за 5 лет эксплуатации моста нарушений в клеевых швах не зафиксировано.
.2 Полимербетоны и полимеррастворы использованы также для ремонта бетонных опор моста через Свиягу на автотрассе Казань-Ульяновск. Опоры моста имели значительные повреждения: раковины, сколы бетона с обнажением защитной металлической сетки, вызванные ледоходом.
В неглубокие раковины полимерраствор укладывался без опалубки, во всех остальных случаях использована инвентарная металлическая опалубка с резиновыми уплотнителями по краям. Смесь укладывалась через загрузочные воронки. Через 1,5-2 ч после укладки полимерраствора опалубка перемещалась на следующий участок. Ввиду довольно низкой температуры окружающего воздуха (810°С) опалубка предварительно прогревалась. Дефекты большого объёма заделывались обычным цементным мелкозернистым бетоном с промазкой контактной зоны старый - новый бетон эпоксидным составом. Увеличение адгезии нового бетона к старому было необходимо ввиду сложных условий эксплуатации (воздействие воды, мороза) опор.
Восстановление опор с помощью полимерраствора позволило значительно сэкономить опалубочный материал, снизить трудоёмкость, упростить технологию и сократить сроки производства работ. Надёжность защиты опор от повреждений подтвердилась пропуском льда в течение 5 лет.
.3 Широкое применение сборных железобетонных конструкций в промышленном и жилищно-гражданском строительстве вызвало необходимость выполнения большого количества стыков сборных элементов. Клеевые стыки, как показали многочисленные исследования, характеризуются значительными технико-экономическими достоинствами. Известны также попытки стыкования железобетонных свай, которые по производственным причинам не могли быть изготовлены или погружены в грунт целиком. Модифицированные эпоксидные составы применены для ремонта свай, получивших повреждения при погрузочно-разгрузочных и транспортных работах, а также при забивке (разрушении головы сваи); стыковании обрубков свай для их последующего использования по прямому назначению и наращивания железобетонных свай в процессе забивки. Склеивание свай представляет интерес и как наглядный, жёсткий метод испытания эпоксидного клея в натурных условиях, так как в процессе забивки в грунт клееный стык испытывает значительные динамические нагрузки. Железобетонные сваи имели следующие типы стыков (рис.1): 1, 2 - арматурные; 3, 4 - безарматурные; 5 - со сваркой стыковыми накладками и последующим омоноличиванием эпоксидным составом.
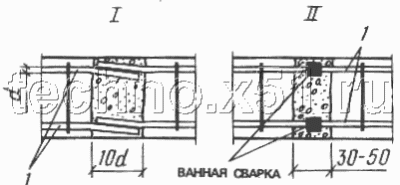
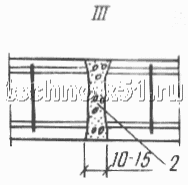
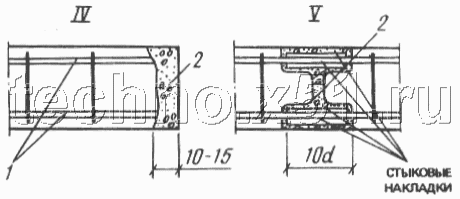
Рисунок 1. Типы клеевых стыков с применением модифицированных эпоксидных полимербетонов и полимеррастворов: 1− основная арматура; 2 - полимерраствор
Общая длина клееных свай сечением 0,3x0,3 м, состыкованных из обрубков, составляла 6-7 м, а количество стыков на одной свае - 13. Подготовка обрубков свай к склеиванию заключалась в оголении арматуры на необходимую длину; выравнивании торца (с помощью отбойного молотка) и очистке поверхности от снега, грязи и слабых трещиноватых мест. Подготовленные обрубки подбирались по длине и раскладывались с помощью крана на стеллажах. Арматура соединялась (связывалась или сваривалась), на стык устанавливалась несложная металлическая опалубка. Разделительным слоем служила суспензия воска в бензине. Использованы полимербетоны и эпоксидные составы, частей (по массе): I - эпоксидная смола Э40 − 70; фенольная смесь - 30; полиэтиленполиамин - 1020; цемент − 200-400; щебень − 100200; II − эпоксидная смола ЭД20 − 23; фенольная смесь − 23; полиэтиленполиамин − 6; цемент или молотый кварцевый песок - 48. Наибольшая крупность зерен щебня составляла 15 мм. Эпоксидная полимерная смесь готовилась вручную в полиэтиленовой емкости. Сваи склеивались и омоноличивались в горизонтальном положении (за исключением типа II, который был выполнен в вертикальном проектном положении). Отверждение эпоксидной смеси осуществлялось в естественных условиях при температуре наружного воздуха + 1020°С в состав вводился ускоритель (хлорное железо) в количестве 1-3 ч. по массе на 100 ч. по массе связующего. Такие смеси при температуре наружного воздуха 15°С набирают прочность 40 МПа. Количество отвердителя варьировалось в зависимости от температуры окружающей среды, а количество наполнителя лимитировалось необходимой удобоукладываемостью смеси.
Клееные сваи погружались в грунт сваебойным копром. Все типы стыков выдержали испытания, связанные с транспортированием и погружением в грунт. Нарушений в клеевых швах не обнаружено. Установлено, что наилучшими техникоэкономическими показателями обладают стыки с ванной сваркой арматуры.
Использование эпоксиднофенольных клеящих составов взамен сварки при наращивании свай в процессе погружения позволило снизить стоимость, трудоёмкость и материалоёмкость. Внедрение клеевого способа наращивания железобетонных свай было проведено на объектах треста "Татгражданстрой". Шестнадцатиметровые сваи состояли из нижней (l = 12 м) и верхней (l = 4 м) частей. На торец нижней части сваи, погружённой в грунт на глубину 11 м, разливалась полимеррастворная смесь, которая заполняла анкерные отверстия и покрывала торец (рис. 2).
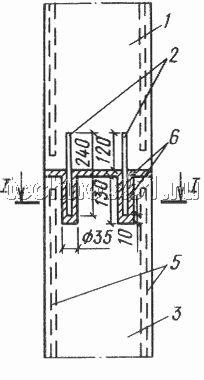
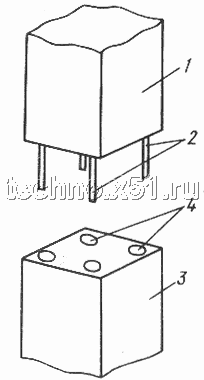
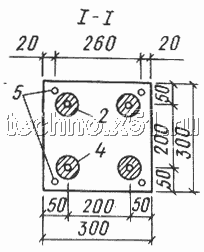
Рисунок 2. Полимеррастворы при наращивании железобетонных свай: 1 − верхняя часть сваи; 2 - выпуски арматуры диаметром 16 мм; 3 − нижняя часть сваи; 4 анкерные отверстия диаметром 35 мм; 5 − основная арматура диаметром 16 мм; 6 − полимерраствор
После установки верхней части и дальнейшем погружении торцы свай соприкасаются и склеиваются. Эпоксидный состав надёжно соединяет бетон и арматуру. Положение верхней сваи фиксировалось на период отверждения смеси с помощью кондуктора. Дальнейшее погружение свай проводилось через сутки после стыкования. Вес ударной части сваебойного копра составлял 3,2 т, высота подъема - 1 м. Осмотр погруженных свай путем откапывания до клеевого стыка показал отсутствие повреждений клеевого шва.
Эпоксидные композиции применяют для соединения железобетонных колонн, элементов сборных куполов, балок и др. При этом для круглогодичного производства строительных работ созданы композиции, отверждающиеся при отрицательных температурах до 20°С и ниже. С этой целью в эпоксидное связующее вводят ускоритель: хлорное железо или солянокислый анилин в сочетании с фуриловым спиртом или изготавливают клеи в виде плёнокпрокладок, способных склеивать и отверждаться при прогреве.
.4 Ремонт фундамента включает в себя замоноличивание пустот, каверн и трещин. Для ремонта бетонных фундаментов под технологическим оборудованием на участке ёмкостного парка производства фенола и ацетона в Казанском производственном объединении "Органический синтез" был применён эпоксиднофенольный пенопласт с повышенной плотностью, обеспечивающий высокую прочность и малое водопоглощение.
Возможность регулирования в широких пределах прочностных показателей, простота получения эпоксиднофенольных пенопластов (ЭФП) создали предпосылки для их применения в качестве эффективных расширяющихся композиций для замоноличивания трещин, заполнения пустот в бетонных и железобетонных конструкциях. Вспенивание композиции заливочного эпоксиднофенольного пеннопласта позволяет при сохранении требуемых свойств (достаточная прочность и небольшое водопоглощение) повысить качество выполнения работ, поскольку вспенивание композиции пенопласта непосредственно в трещинах и пустотах обеспечивает их наилучшее заполнение и наименьшую проницаемость конструкции.
Для заливки была использована композиция эпоксиднофенольного пенопласта следующего состава, частей по массе:
Эпоксидная смола ЭД16 100
Фенольная смесь (смола) 50
Поверхностноактивное вещество ОП10 3
Кремнийорганическая жидкость ГКЖ94 1
Полиэтиленполиамин 15
Заливочный эпоксиднофенольный пенопласт вышеуказанного состава в отверждённом состоянии имеет следующие показатели:
Плотность пенопласта, кг/м3 630650
Прочность при сжатии, МПа 29,530
Водопоглощение за 24 ч, % по объёму 0,3 0,35
Заливка композиций пенопласта осуществлялась шприцеванием. Подготовка поверхности бетона ремонтируемых участков под заливку состояла в удалении слабых трещиноватых мест и обезжиривании их ацетоном. Для предотвращения вытекания заливочной смеси на вертикальных поверхностях устраивалась несложная опалубка.
Как показал опыт, заливочная композиция эпоксиднофенольного пенопласта после отверждения обеспечивает восстановление монолитности конструкции и полное заполнение всех пустот и трещин фундамента. Ремонт фундамента проходил без прекращения эксплуатации ёмкостей.
.5 В настоящее время железобетонные конструкции очень широко применяются в гражданском и промышленном строительстве. С течением времени возникает вопрос о ремонте и усилении железобетонных конструкций. Оздоровление и ремонт мостов играет важную роль для обеспечения бесперебойного движения автотранспорта без ограничения скорости и массы. Эксплуатационным службам приходится выполнять большой объём работ: ремонт и смену гидроизоляции, заделку сколов и раковин, затирку трещин, инъекцию цементного раствора и т.д., а в некоторых случаях (при недостаточной несущей способности) и усиление железобетонных конструкций. Так, ряд мостов, построенных в 19001912 гг., не имеет гидроизоляции и водоотводных устройств, в результате чего вода с проезжей части стекает по фасадным поверхностям главных балок, смачивая их. При обследовании железобетонного моста на дороге Казань - Пермь, построенного в 1912 г., было установлено, что толщина слоя коррозии арматуры главных балок достигала 45 мм и вызвала ослабление площади сечения рабочей арматуры до 2025%. Коррозия сопровождалась разрушением бетона по нижним поясам балок и образованием продольных трещин раскрытием до 2 мм. Поверочный расчёт с целью определения грузоподъёмности моста выявил, что несущая способность главных балок недостаточна для восприятия современных нормативных нагрузок и мост нуждается в усилении.