Файл: Содержание Введение 2 Способы защиты резервуаров от коррозии 3 Виды коррозий и коррозионных разрушений резервуаров 9 Классификация видов коррозии 9 2 Типы коррозии .rtf
Добавлен: 09.01.2024
Просмотров: 87
Скачиваний: 3
ВНИМАНИЕ! Если данный файл нарушает Ваши авторские права, то обязательно сообщите нам.
Содержание
Введение 2
1. Способы защиты резервуаров от коррозии 3
2. Виды коррозий и коррозионных разрушений резервуаров 9
2.1. Классификация видов коррозии 9
2.2 Типы коррозии 11
3. Выбор способа защиты резервуара от коррозии 13
4. Зоны наиболее подверженные коррозии 14
5. Выбор способа защиты резервуара от коррозии 19
Заключение 21
Список использованных источников 22
Введение
Коррозия металлов наносит огромный ущерб, который в промышленно развитых странах, некоторые источники выявляют статистику, согласно которой до 10% производимого за год металла идет на восполнение коррозионных потерь.
Cоздание промышленных объектов из металла в перспективе может оказаться мало эффективным, если не предпринимать действенных мер к продлению сроков службы сооружений и изделий из стали, которая была и остается основным конструкционным материалом в промышленности, на транспорте и в строительстве.
Огромная доля производственных фондов нефтеперерабатывающей промышленности состоит из стальных резервуаров для хранения нефти и нефтепродуктов, по отношению к которым выдвинутая ныне задача повышения качества решается в форме поддержания их в состоянии нормального (безаварийного) функционирования в течение возможно более длительного периода при существенном снижений эксплуатационных расходов. Одним из определяющих факторов решения поставленной задачи является проблема защиты резервуаров от коррозионного воздействия нефтяных сред.
Коррозионный износ основных несущих элементов стальных резервуаров приводит к дополнительным расходам металла. Средний межремонтный срок службы незащищенных резервуаров составляет 6 лет, а отдельные коррозионные воздействия — особенно кровель — появляются уже через 18 месяцев. На восполнение ущерба от коррозии расходуется до 25% металла, требуемого для постройки нового резервуара.
Коррозионные повреждения резко снижают степень эксплуатационной надежности резервуаров. Имевшие место в нашей стране аварии были вызваны именно коррозионными поражениями, приведшими к разрушению ответственных элементов конструкций резервуаров.
1. Способы защиты резервуаров от коррозии
Коррозия приводит ежегодно к миллиардным убыткам, и решение этой проблемы является важной задачей. Основной ущерб, причиняемый коррозией, заключается не в потере металла как такового, а в огромной стоимости изделий, разрушаемых коррозией. Вот почему ежегодные потери от неё в промышленно развитых странах столь велики. Истинные убытки от неё нельзя определить, оценив только прямые потери, к которым относятся стоимость разрушившейся конструкции, стоимость замены оборудования, затраты на мероприятия по защите от коррозии. Не малый ущерб составляют косвенные проблемы, например, простои оборудования при замене прокорродировавших деталей и узлов, утечка продуктов, нарушение технологических процессов.
Хорошая защита от коррозии на 80% зависит от правильной подготовки поверхности, и только на 20% от качества используемых лакокрасочных материалов и технологии их нанесения. Наиболее производительным и эффективным методом подготовки поверхности перед дальнейшей защитой субстрата является абразивоструйная очистка.
Обычно выделяют три направления методов защиты от коррозии:
-
Конструкционный; -
Активный; -
Пассивный.
Активные методы борьбы с коррозией направлены на изменение структуры двойного электрического слоя. Применяется наложение постоянного электрического поля с помощью источника постоянного тока, напряжение выбирается с целью повышения электродного потенциала защищаемого металла.
Активный метод – изменение электрических параметров системы, частью которой является защищаемый элемент, с помощью источника тока. При этом система подвергается наложению электрического поля с постоянными характеристиками. Смысл этих манипуляций – повысить электродный потенциал защищаемого металла. Другой активный метод – использование в системе специального анода, процесс разрушения которого гарантирует целостность защищаемым элементам.
Пассивный метод – это классический вариант, использующийся с давних времён. В качестве покрытия используют другие металлы (цинк, олово, никель, хром), эмали, краски или полимеры. Примечательно, что если повреждение эмалированного слоя или краски вызывает коррозию основного металла под ним со «стандартной» скоростью, то поврежденный защитный слой из металла может как ускорять процесс, так и мешать ему (в этом случае начинают работать принципы активной защиты, которые описывались выше).
Так, повреждённое цинковое покрытие всё равно защищает основной металл, т.к. цинк обладает большим отрицательным потенциалом, чем сталь и цинк выступает в качестве анода. Каким материалом защитить поверхность, зависит от предполагаемой эксплуатации изделия. Например, оловянное покрытие допустимо при контакте с пищевыми продуктами, тогда как ионы цинка, образующиеся при повреждении цинкового слоя, токсичны для живых организмов.
Попытки защиты днищ резервуаров одними эпоксидными смолами пока не дают желаемых результатов. Более надежной является комплексная защита днищ от коррозии: нанесение покрытия из эпоксидных смол и устройство протекторной защиты.
Пассивную защиту внутренней поверхности резервуаров осуществляют покрытиями на основе лакокрасочных и полимерных материалов, цинка и других.
Лакокрасочные материалы (ЛКМ) - это поверхностные пленкообразующие покрытия способные при нанесении их на какую-либо поверхность высыхать или полимеризоваться с образованием твердой и прочной пленки. Их широко применяют для зашиты от коррозии наружной и внутренней поверхности подземных, надземных и подводных газонефтепроводов, резервуаров, различных строительных конструкций и т. д.
Нанесение ЛКМ — это один из самых распространенных и надежных способов защиты надземных конструкций от коррозии.
Они относительно недорогие, имеют несложную технологию нанесения, легко восстанавливаются в случае повреждения, отличаются разнообразием внешнего вида и цвета.
Виды лакокрасочных материалов:
Лаки – это растворы пленкообразующих веществ в органических растворителях. Тонкие слои лаков высыхают с образованием твердых блестящих и прозрачных покрытий, назначение которых защита изделий от агрессивных агентов и декоративная отделка поверхности. Они служат также основой эмалевых красок, грунтовок, шпатлевок.
Краски представляют собой однородные суспензии пигментов и других добавок в пленкообразующих веществах, образующие при высыхании непрозрачные покрытия.
В зависимости от применяемого пленкообразователя краски подразделяют на:
-
масляные (на основе высыхающих масел и олиф); -
эмалевые (на основе лаков); -
клеевые (на основе водных растворов некоторых органических полимеров); -
силикатные (на основе жидкого стекла); -
эмульсионные или водоэмульсионные (на основе водных дисперсий полимеров); -
битумные (на основе битумов) и др.
Для окраски резервуаров необходимо предварительно тщательно очистить от осадка нефтепродукта (нефти) и коррозии поверхности металла методом пескоструйной обработки. Кроме того, окраска затрудняется тем, что многие растворители лаков и красок токсичны, горючи и взрывоопасны. Практика эксплуатации перхлорвиниловых покрытий показала, что они не обладают достаточной адгезией к металлической поверхности, поэтому через небольшой период работы происходит их отслоение и разрушение.
К пассивным методам относится также защита от коррозии внутренней поверхности кровли, днища и обечайки, контактирующим с газовым пространством резервуара и подтоварной водой, с помощью ингибиторов - веществ, добавление которых в малом количестве в коррозионную среду тормозит или значительно подавляет коррозионный процесс. В газовое пространство вводятся летучие ингибиторы, а подтоварную воду – водорастворимые. Применение ингибиторов не дает большого эффекта в слизи с регулярным дренированием подтоварной воды и постоянными «дыханиями» резервуаров.
Метод защиты резервуаров добавками ингибиторов коррозии применим лишь для длительного хранения нефтепродуктов. Однако при большой оборачиваемости резервуаров происходит частая смена подтоварной воды, что вызывает необходимость постоянного ввода ингибитора коррозии для поддержания заданной концентрации в агрессивной среде, что значительно усложняет его применение.
Электрохимическая защита. Скорость электрохимической коррозии можно значительно уменьшить, если металлическую конструкцию подвергнуть поляризации. В зависимости от вида поляризации различают катодную и анодную защиту. Электрохимическую защиту применяют в том случае, если потенциал свободной коррозии конструкционного материала располагается в области активного растворения или перепассивации, то есть материал растворяется с высокой скоростью.
Катодная защита - наиболее распространенный вид электрохимической защиты. Она применяется в тех случаях, когда металл не склонен к пассивации, то есть имеет протяженную область активного растворения, узкую пассивную область, высокие значения тока пассивации и потенциала пассивации.
Катодную поляризацию можно осуществлять путем присоединения защищаемой конструкции к отрицательному полюсу внешнего источника тока или к металлу, имеющему более электроотрицательный электродный потенциал. В последнем случае нет надобности во внешнем источнике тока, так как образуется гальванический элемент с тем же направлением тока, т. е. защищаемая деталь становится катодом, а более электроотрицательный металл, называемый протектором, — анодом.
Катодная защита внешним током. Катодную защиту с использованием поляризации от внешнего источника тока применяют для защиты оборудования из углеродистых, низко- и высоколегированных и высокохромистых сталей, олова, цинка, медных и медно-никелевых сплавов, алюминия и его сплавов, свинца, титана и его сплавов. Как правило, это подземные сооружения (трубопроводы и кабели различных назначений, фундаменты, буровое оборудование), оборудование, эксплуатируемое в контакте с морской водой (корпуса судов, металлические части береговых сооружений, морских буровых платформ), внутренние поверхности аппаратов и резервуаров химической промышленности. Часто катодную защиту применяют одновременно с нанесением защитных покрытий. Уменьшение скорости саморастворения металла при его внешней поляризации называют защитным эффектом.
Основным критерием катодной защиты является защитный потенциал. Защитным потенциалом называется потенциал, при котором скорость растворения металла принимает предельно низкое значение, допустимое для данных условий эксплуатации.
2. Виды коррозий и коррозионных разрушений резервуаров
Коррозия - это самопроизвольное разрушение металлов, в результате химического или физико-химического взаимодействия с окружающей средой. В общем случае это разрушение любого материала, будь то металл или керамика, дерево или полимер. Причиной коррозии служит термодинамическая неустойчивость конструктивных материалов к воздействию веществ, находящихся в контактирующей с ними среде.
В повседневной жизни для сплавов железа чаще используют термин «ржавление». Менее известны случаи коррозии полимеров. Применительно к ним существует понятие «старение», аналогичное термину «коррозия» для металлов. Например, старение резины из-за взаимодействия с кислородом воздуха или разрушение некоторых пластиков под воздействием атмосферных осадков, а также биологическая коррозия. Скорость коррозии, как и всякой химической реакции, очень сильно зависит от температуры. Повышение температуры на 100 градусов может увеличить скорость коррозии на несколько порядков.
2.1. Классификация видов коррозии
Коррозионные процессы отличаются широким распространением и разнообразием условий и сред, в которых они протекают. Поэтому пока нет единой и всеобъемлющей классификации встречающихся случаев коррозии.
По типу агрессивных сред, в которых протекает процесс разрушения, коррозия может быть следующих видов:
-
газовая коррозия; -
атмосферная коррозия; -
коррозия в не электролитах; -
коррозия в электролитах; -
подземная коррозия; -
коррозия под воздействием блуждающих токов.
По условиям протекания коррозионного процесса различаются следующие виды:
-
контактная коррозия; -
щелевая коррозия; -
коррозия при неполном погружении; -
коррозия при полном погружении; -
коррозия при переменном погружении; -
коррозия при трении; -
межкристаллическая коррозия; -
коррозия под напряжением.
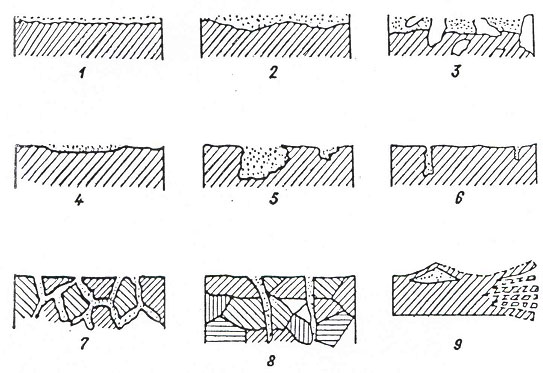
Рис. 1. Виды коррозии по характеру разрушения.
1-равномерная; 2-неравномерная; 3-избыточная; 4-пятнами; 5-язвенная; 6- точечная; 7-межкристалическая; 8-коррозионное растрескивание; 9-подповерхностная.