ВУЗ: Не указан
Категория: Не указан
Дисциплина: Не указана
Добавлен: 12.01.2024
Просмотров: 117
Скачиваний: 1
ВНИМАНИЕ! Если данный файл нарушает Ваши авторские права, то обязательно сообщите нам.
, которое выполняется цельнолитым и представляет собой как бы два колеса с односторонним входом, сложенные основными дисками. Это колесо имеет один основной и два передних диска. Основное достоинство таких рабочих колес – их хорошая осевая уравновешенность.
Вращение от ротора электродвигателя к насосу передаётся с помощью зубчатой муфты и торцевых уплотнений обеспечивается без снятия крышки корпуса и электродвигателя.
Чтобы повысить экономичность работы насосов, в период поэтапного освоения нефтепровода предусматривается применение сменных роторов с рабочим колёсами на подачу 0,5 и 0,7 от номинальной. Для расширения области применения насоса НМ 10000-210 до подачи 12000 м3/ч в нем предусмотрено применение сменного ротора на подачу 1,25 от номинальной.
Разборка насосного оборудования и прилегающих к нему агрегатов необходима при нарушениях связанных с неисправностью его трубопроводной обвязкой (пропуски во фланцевых соединениях, забивка труб, плохое закрепление, вибрация и т.п.).
Разборка центробежных насосов проводится в следующей последовательности:
Перед началом демонтажа насоса бригада ремонтников должна быть обеспечена безопасными условиями работы, полным комплектом необходимых инструментов, а также местом для проведения разборки. Задвижки на приёмной и напорной линиях насоса должны быть закрыты.
После снятия сальниковых или отсоединение торцовых уплотнений проверяют положение ротора (путём измерения расстояния между валом и расточкой сальниковой коробки), отклонение не должно превышать 0,1 мм.
Также проверяют осевой разбег ротора (не более 0,1-0,15 мм) в корпусе насоса путём подачи его в переднее и заднее крайние положения. Увеличенный разбег ротора возможен неправильной установки в корпусе подшипников качения.
Разборка секционных центробежных насосов НМ с подачей 210м3/ч имеет отличительные особенности, так как эти насосы имеют вертикальный разъем секций корпуса. Разбор насоса представлен на рисунке 6.
Рисунок 6 – Схема разбора центробежного насоса
Соединительные муфты. В насосных агрегатах чаще используют зубчатые (компенсирующие) и реже пальцевые муфты. Зубья втулок и обойм имеют обычный эвольвентный профиль. Полость зубчатой муфты заполняют маслом. Передача происходит через зубчатое зацепление.
Наибольшему износу в этих муфтах подвергаются зубья (появляются заусенцы, вмятины). После восстановления поверхности зубьев проверяют на качество сопряжения, биение муфты. Если есть биение, то детали муфты протачивают на станке относительно посадочного отверстия до устранения дефектов.
Пальцевые муфты относятся к типу упруго демпфирующих, поскольку за счёт применения упругих деталей, допускают смещение одного вала относительно другого и обеспечивают смягчение толчков.
Наиболее быстро изнашиваются у пальцевых муфт соединительные пальцы. Поэтому их подвергают тщательной ревизии. Не допускается зазор между эластичными элементами и пальцами. Эластичные шайбы подлежат замене при выработке более чем два миллиметра по диаметру. При обнаружении дефектов на полумуфтах их подвергают такому же ремонту, что и полумуфты зубчатой муфты.
До начала монтажа перекачивающего агрегата заканчивают общестроительные работы, обеспечивающие необходимый фронт ведения монтажных работ. В частности, до начала монтажа перекачивающего агрегата необходимо закончить работы нулевого цикла, то есть монтаж и устройство фундамента, обратную засыпку и уплотнение грунтов по всем элементам нулевого цикла, обустройство внеплощадочных и внутриплощадочных дорог и площадок для укрупнительной сборки оборудования, подлежащего монтажу.
Организации, ведущие монтаж, принимают от заказчика технологическое оборудование и перекачивающий агрегат.
Особое место в период подготовки монтажных работ занимают приёмка и подготовка фундамента под монтаж. В соответствии со сроками, установленными календарными и сетевыми графиками, строительные организации передают монтажным организациям фундамент под перекачивающий агрегат и технологическое оборудование. Приёмку фундамента представители монтажных организации проводят в соответствии с требованиями. На рисунке 7 представлена схема проверки перпендикулярности разбивочных осей на фундаменте.
Рисунок 7 – Схема проверки перпендикулярности разбивочных осей на фундаменте
Строительная организация (генподрядчик) предъявляет монтажной организации (субподрядчику) акты готовности каждого из элементов нулевого цикла под монтаж оборудования. Этот акт подписывают представители строительной организации (генподрядчика), монтажной организации (субподрядчика) и заказчика. После окончательной приёмки монтажной организацией фундамента и других элементов нулевого цикла составляют акт готовности нулевого цикла в соответствии с проектом. Акт готовности подписывают те же представители.
Приёмку фундамента под перекачивающий агрегат и оборудование насосных станций начинают с их внешнего осмотра и обмера. При внешнем осмотре обращают внимание на отсутствие трещин, отколов и других дефектов в теле фундамента, ростверка и стоек. При обмере фундамента с помощью рулетки проверяют соответствие его габаритов проектным размерам. Далее, проверяют правильность нанесения на фундамент разбивочных осей и их взаимную перпендикулярность при помощи струн (стальных проволок) и отвесов. Перпендикулярность разбивочных осей проверяют следующим образом. Путём натяжения одной из струн обозначают поперечную ось. На концах струны навешивают отвесы, позволяющие перенести поперечную ось на боковые грани фундамента. Затем второй струной обозначают продольную ось и навешивают на её концах отвесы. От точки пересечения осей О на струне, имитирующей поперечную ось, откладывают равные отрезки ОС и 0В произвольной длины. От точки 0 на продольной оси откладывают отрезок ОА произвольной длины. Продольная и поперечная оси будут перпендикулярны в том случае, если боковые стороны АС и АВ треугольника АСВ будут равны, то есть если треугольник АСВ будет равнобедренным.
Проверяют также соответствие отклонений реальных размеров фундамента от проектных и допустимых отклонений. Допустимые отклонения обычно указывают в приведённых выше нормативных документах. Так, для монтажа сборных элементов объектов нулевого цикла установлены следующие допустимые отклонения:
Допустимые отклонения (в мм) монолитных железобетонных конструкций объектов нулевого цикла принимают по ОСТ 102-50 — 79 «Объекты в комплектно-блочном исполнении. Приёмка работ нулевого цикла».
Контроль высотных отметок опорных частей фундамента осуществляют геодезическим нивелированием. Привязку колодцев для фундаментных болтов в монолитных железобетонных фундаментах к продольной и поперечным осям проверяют с помощью струн и отвесов, с применением измерительного инструмента — рулетки.
При обнаружении каких-либо дефектов в принимаемом фундаменте или других объектах нулевого цикла монтажная организация не имеет права самостоятельно вести работы по исправлению фундамента. Работы по исправлению фундамента и их усовершенствованию выполняет только строительная организация, ведущая общестроительные работы и имеющая письменное разрешение проектной организации.
После приёмки фундамента монтажная организация проводит его подготовку к монтажу оборудования, которая заключается в получении на обрезе фундамента строго горизонтальной опорной площадки на необходимой проектной высотной отметке. Причём характер и объем подготовки опорных поверхностей фундамента целиком зависит от выбранного способа опирания перекачивающих агрегатов и оборудования на фундаменты. Выбранным способом опирания перекачивающего агрегата и оборудования на опорную поверхность массивного фундамента является – опирание на парные монтажные клиновые подкладки. На рисунке 8 представлена схема установки оборудования на фундаментах с помощью клиновых подкладок.
1— основание машины, 5 — фундамент, 9 — бетонная подливка, 10 — шайбы, 11 — крепёжная гайка, 12 — опорная установочная гайка
Рисунок 8 – Схема установки оборудования на фундаментах с помощью клиновых подкладках
При опирании оборудования на парные клиновые подкладки и особенно— на установочные болты, требуется наименьшая подготовка фундамента. Парные клиновые подкладки состоят из двух клинообразных пластин длиной 500 мм и шириной 150 мм. Толщина пластин на противоположных концах соответственно 5 и 20 мм (уклон i = 0,03). Клинообразные пластины складывают попарно по наклонным плоскостям, что дает возможность при их взаимном перемещении получать пластины с параллельными плоскостями толщиной от 25 мм и менее. Установочные болты ввинчивают в резьбовые гнезда опорных. частей монтируемого оборудования. Концы болтов опираются на опорные пластины, установленные на поверхности фундамента. Путём поочередного ввинчивания и вывинчивания установочных болтов добиваются точной установки оборудования в горизонтальном положении на проектной отметке.
Подготовка фундамента в этом случае сводится к установке на поверхность фундамента опорных пластин. Причём отклонения вертикальных отметок опорных пластин исправляют за счёт предварительной установки клиновых парных подкладок или регулирования по высоте установочных болтов.
Насосный агрегат для насосной станции магистрального нефтепровода и нефтепродуктопровода в блочном исполнении поступает с завода-изготовителя в виде готовых блоков, полностью подготовленных к монтажу без необходимости проведения разборки и ревизии их узлов на месте монтажа. Насосный агрегат поставляют в виде двух основных блоков, устанавливаемых на раздельные рамы: центробежного одноступенчатого магистрального насоса и электродвигателя. В комплект блока центробежного насоса входят собственно насос с фундаментной рамой, поставляемой отдельно от насоса, зубчатая соединительная муфта и фундаментные болты. Блок электродвигателя включает синхронный электродвигатель, возбудитель, фундаментную раму в виде двух направляющих из стального проката, поставляемую отдельно от электродвигателя, и фундаментные болты. Монтаж перекачивающего агрегата и сложного оборудования выполняют при участии представителей заводов-изготовителей, а о начале монтажа монтажная организация письменно извещает завод-изготовитель.
Организация и технология монтажа насосного агрегата блочной поставки происходят в готовом здании. При монтаже насосного агрегата в готовом здании насосного цеха условия монтажа ухудшаются по сравнению с условиями монтажа насосного агрегата до начала строительства здания насосного цеха из-за стеснённости пространства, но при этом сам процесс монтажа не зависит от погодных условий.
Монтаж центробежного горизонтального магистрального насоса НМ 10000-210 начинают с установки плит или рам на фундамент и выверки их в плане, по высоте и горизонтали. Допускаются отклонения плиты (рамы) в плане и по высоте до десяти миллиметров, а по горизонтали до 0,1 мм на один метр длины плиты. Узел насосного агрегата устанавливают на общей раме или на отдельных рамах.
Фундаментные рамы устанавливают на прокладки и крепят к фундаменту с помощью фундаментных болтов. Прокладки помещают по обе стороны каждого болта и по всему периметру рамы через 300—1000 мм в зависимости от ее жёсткости. Число прокладок по высоте не должно превышать пяти, включая тонколистовые, применяемые для окончательной выверки. После подливки рамы бетоном и затвердевания его до проектной прочности выполняют затяжку болтов. Окончательная центровка насоса производится с помощью прокладок, помещённых между опорной поверхностью рамы и лапами двигателя. Установка прокладок под опорные поверхности гидромуфт и редукторов, а также под опорные поверхности насоса в агрегатах без гидромуфт и редукторов не разрешается и допускается только при наличии указаний завода-изготовителя. Плотность прилегания поверхностей прокладок друг к другу, а также к опорным поверхностям фундаментных рам (плит) и
Вращение от ротора электродвигателя к насосу передаётся с помощью зубчатой муфты и торцевых уплотнений обеспечивается без снятия крышки корпуса и электродвигателя.
Чтобы повысить экономичность работы насосов, в период поэтапного освоения нефтепровода предусматривается применение сменных роторов с рабочим колёсами на подачу 0,5 и 0,7 от номинальной. Для расширения области применения насоса НМ 10000-210 до подачи 12000 м3/ч в нем предусмотрено применение сменного ротора на подачу 1,25 от номинальной.
-
Демонтаж насоса и силового оборудования
Разборка насосного оборудования и прилегающих к нему агрегатов необходима при нарушениях связанных с неисправностью его трубопроводной обвязкой (пропуски во фланцевых соединениях, забивка труб, плохое закрепление, вибрация и т.п.).
Разборка центробежных насосов проводится в следующей последовательности:
-
разболчивают и разбирают соединения с всасывающим и нагнетательным трубопроводами; -
снимают заднюю крышку у насосов консольного типа, либо верхнюю крышку у насосов с горизонтальным разъёмом; -
отвинчивают гайки нажимной втулки сальника, сдвигают её, извлекают сальниковую набивку; -
разбирают муфтовое соединение и снимают полумуфту, насаженную на вал насоса; -
извлекают из корпуса вал с рабочим колесом и осторожно укладывают на доски. -
выпрессовка подшипников из корпуса может быть произведена осторожными ударами по свободному концу вала, для предохранения которого на конец навёртывается гайка; -
отвинчивают стопорную гайку и снимают с вала рабочее колесо насоса.
Перед началом демонтажа насоса бригада ремонтников должна быть обеспечена безопасными условиями работы, полным комплектом необходимых инструментов, а также местом для проведения разборки. Задвижки на приёмной и напорной линиях насоса должны быть закрыты.
После снятия сальниковых или отсоединение торцовых уплотнений проверяют положение ротора (путём измерения расстояния между валом и расточкой сальниковой коробки), отклонение не должно превышать 0,1 мм.
Также проверяют осевой разбег ротора (не более 0,1-0,15 мм) в корпусе насоса путём подачи его в переднее и заднее крайние положения. Увеличенный разбег ротора возможен неправильной установки в корпусе подшипников качения.
Разборка секционных центробежных насосов НМ с подачей 210м3/ч имеет отличительные особенности, так как эти насосы имеют вертикальный разъем секций корпуса. Разбор насоса представлен на рисунке 6.
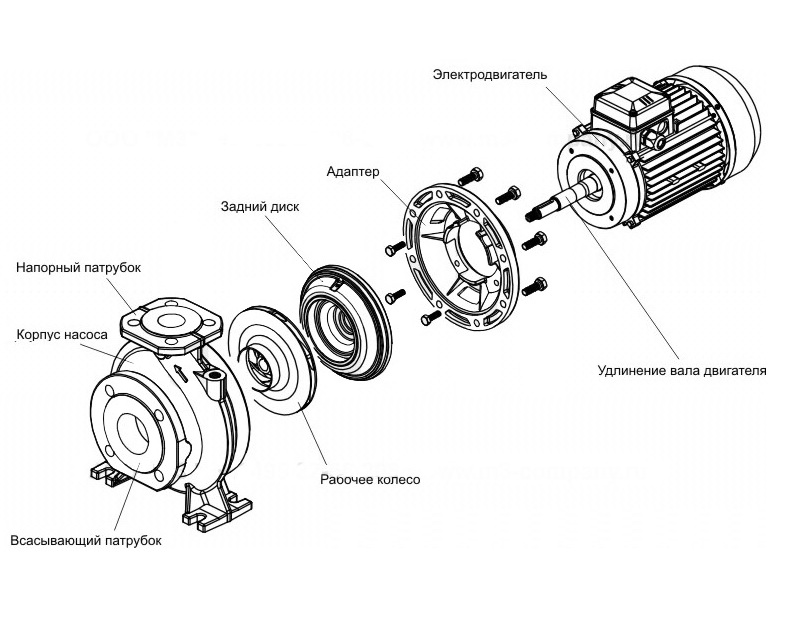
Рисунок 6 – Схема разбора центробежного насоса
Соединительные муфты. В насосных агрегатах чаще используют зубчатые (компенсирующие) и реже пальцевые муфты. Зубья втулок и обойм имеют обычный эвольвентный профиль. Полость зубчатой муфты заполняют маслом. Передача происходит через зубчатое зацепление.
Наибольшему износу в этих муфтах подвергаются зубья (появляются заусенцы, вмятины). После восстановления поверхности зубьев проверяют на качество сопряжения, биение муфты. Если есть биение, то детали муфты протачивают на станке относительно посадочного отверстия до устранения дефектов.
Пальцевые муфты относятся к типу упруго демпфирующих, поскольку за счёт применения упругих деталей, допускают смещение одного вала относительно другого и обеспечивают смягчение толчков.
Наиболее быстро изнашиваются у пальцевых муфт соединительные пальцы. Поэтому их подвергают тщательной ревизии. Не допускается зазор между эластичными элементами и пальцами. Эластичные шайбы подлежат замене при выработке более чем два миллиметра по диаметру. При обнаружении дефектов на полумуфтах их подвергают такому же ремонту, что и полумуфты зубчатой муфты.
-
Монтаж насоса и силового оборудования
До начала монтажа перекачивающего агрегата заканчивают общестроительные работы, обеспечивающие необходимый фронт ведения монтажных работ. В частности, до начала монтажа перекачивающего агрегата необходимо закончить работы нулевого цикла, то есть монтаж и устройство фундамента, обратную засыпку и уплотнение грунтов по всем элементам нулевого цикла, обустройство внеплощадочных и внутриплощадочных дорог и площадок для укрупнительной сборки оборудования, подлежащего монтажу.
Организации, ведущие монтаж, принимают от заказчика технологическое оборудование и перекачивающий агрегат.
Особое место в период подготовки монтажных работ занимают приёмка и подготовка фундамента под монтаж. В соответствии со сроками, установленными календарными и сетевыми графиками, строительные организации передают монтажным организациям фундамент под перекачивающий агрегат и технологическое оборудование. Приёмку фундамента представители монтажных организации проводят в соответствии с требованиями. На рисунке 7 представлена схема проверки перпендикулярности разбивочных осей на фундаменте.
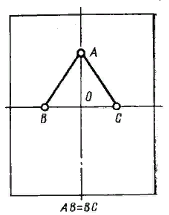
Рисунок 7 – Схема проверки перпендикулярности разбивочных осей на фундаменте
Строительная организация (генподрядчик) предъявляет монтажной организации (субподрядчику) акты готовности каждого из элементов нулевого цикла под монтаж оборудования. Этот акт подписывают представители строительной организации (генподрядчика), монтажной организации (субподрядчика) и заказчика. После окончательной приёмки монтажной организацией фундамента и других элементов нулевого цикла составляют акт готовности нулевого цикла в соответствии с проектом. Акт готовности подписывают те же представители.
Приёмку фундамента под перекачивающий агрегат и оборудование насосных станций начинают с их внешнего осмотра и обмера. При внешнем осмотре обращают внимание на отсутствие трещин, отколов и других дефектов в теле фундамента, ростверка и стоек. При обмере фундамента с помощью рулетки проверяют соответствие его габаритов проектным размерам. Далее, проверяют правильность нанесения на фундамент разбивочных осей и их взаимную перпендикулярность при помощи струн (стальных проволок) и отвесов. Перпендикулярность разбивочных осей проверяют следующим образом. Путём натяжения одной из струн обозначают поперечную ось. На концах струны навешивают отвесы, позволяющие перенести поперечную ось на боковые грани фундамента. Затем второй струной обозначают продольную ось и навешивают на её концах отвесы. От точки пересечения осей О на струне, имитирующей поперечную ось, откладывают равные отрезки ОС и 0В произвольной длины. От точки 0 на продольной оси откладывают отрезок ОА произвольной длины. Продольная и поперечная оси будут перпендикулярны в том случае, если боковые стороны АС и АВ треугольника АСВ будут равны, то есть если треугольник АСВ будет равнобедренным.
Проверяют также соответствие отклонений реальных размеров фундамента от проектных и допустимых отклонений. Допустимые отклонения обычно указывают в приведённых выше нормативных документах. Так, для монтажа сборных элементов объектов нулевого цикла установлены следующие допустимые отклонения:
-
смещение осей фундаментных блоков и стаканов фундамента относительно разбивочных осей ±10 мм; -
отклонение отметок верхних опорных поверхностей элементов фундамента —10 мм; -
отклонение отметок дна стаканов фундамента —20 мм.
Допустимые отклонения (в мм) монолитных железобетонных конструкций объектов нулевого цикла принимают по ОСТ 102-50 — 79 «Объекты в комплектно-блочном исполнении. Приёмка работ нулевого цикла».
Контроль высотных отметок опорных частей фундамента осуществляют геодезическим нивелированием. Привязку колодцев для фундаментных болтов в монолитных железобетонных фундаментах к продольной и поперечным осям проверяют с помощью струн и отвесов, с применением измерительного инструмента — рулетки.
При обнаружении каких-либо дефектов в принимаемом фундаменте или других объектах нулевого цикла монтажная организация не имеет права самостоятельно вести работы по исправлению фундамента. Работы по исправлению фундамента и их усовершенствованию выполняет только строительная организация, ведущая общестроительные работы и имеющая письменное разрешение проектной организации.
После приёмки фундамента монтажная организация проводит его подготовку к монтажу оборудования, которая заключается в получении на обрезе фундамента строго горизонтальной опорной площадки на необходимой проектной высотной отметке. Причём характер и объем подготовки опорных поверхностей фундамента целиком зависит от выбранного способа опирания перекачивающих агрегатов и оборудования на фундаменты. Выбранным способом опирания перекачивающего агрегата и оборудования на опорную поверхность массивного фундамента является – опирание на парные монтажные клиновые подкладки. На рисунке 8 представлена схема установки оборудования на фундаментах с помощью клиновых подкладок.
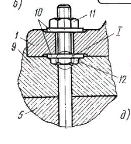
1— основание машины, 5 — фундамент, 9 — бетонная подливка, 10 — шайбы, 11 — крепёжная гайка, 12 — опорная установочная гайка
Рисунок 8 – Схема установки оборудования на фундаментах с помощью клиновых подкладках
При опирании оборудования на парные клиновые подкладки и особенно— на установочные болты, требуется наименьшая подготовка фундамента. Парные клиновые подкладки состоят из двух клинообразных пластин длиной 500 мм и шириной 150 мм. Толщина пластин на противоположных концах соответственно 5 и 20 мм (уклон i = 0,03). Клинообразные пластины складывают попарно по наклонным плоскостям, что дает возможность при их взаимном перемещении получать пластины с параллельными плоскостями толщиной от 25 мм и менее. Установочные болты ввинчивают в резьбовые гнезда опорных. частей монтируемого оборудования. Концы болтов опираются на опорные пластины, установленные на поверхности фундамента. Путём поочередного ввинчивания и вывинчивания установочных болтов добиваются точной установки оборудования в горизонтальном положении на проектной отметке.
Подготовка фундамента в этом случае сводится к установке на поверхность фундамента опорных пластин. Причём отклонения вертикальных отметок опорных пластин исправляют за счёт предварительной установки клиновых парных подкладок или регулирования по высоте установочных болтов.
Насосный агрегат для насосной станции магистрального нефтепровода и нефтепродуктопровода в блочном исполнении поступает с завода-изготовителя в виде готовых блоков, полностью подготовленных к монтажу без необходимости проведения разборки и ревизии их узлов на месте монтажа. Насосный агрегат поставляют в виде двух основных блоков, устанавливаемых на раздельные рамы: центробежного одноступенчатого магистрального насоса и электродвигателя. В комплект блока центробежного насоса входят собственно насос с фундаментной рамой, поставляемой отдельно от насоса, зубчатая соединительная муфта и фундаментные болты. Блок электродвигателя включает синхронный электродвигатель, возбудитель, фундаментную раму в виде двух направляющих из стального проката, поставляемую отдельно от электродвигателя, и фундаментные болты. Монтаж перекачивающего агрегата и сложного оборудования выполняют при участии представителей заводов-изготовителей, а о начале монтажа монтажная организация письменно извещает завод-изготовитель.
Организация и технология монтажа насосного агрегата блочной поставки происходят в готовом здании. При монтаже насосного агрегата в готовом здании насосного цеха условия монтажа ухудшаются по сравнению с условиями монтажа насосного агрегата до начала строительства здания насосного цеха из-за стеснённости пространства, но при этом сам процесс монтажа не зависит от погодных условий.
Монтаж центробежного горизонтального магистрального насоса НМ 10000-210 начинают с установки плит или рам на фундамент и выверки их в плане, по высоте и горизонтали. Допускаются отклонения плиты (рамы) в плане и по высоте до десяти миллиметров, а по горизонтали до 0,1 мм на один метр длины плиты. Узел насосного агрегата устанавливают на общей раме или на отдельных рамах.
Фундаментные рамы устанавливают на прокладки и крепят к фундаменту с помощью фундаментных болтов. Прокладки помещают по обе стороны каждого болта и по всему периметру рамы через 300—1000 мм в зависимости от ее жёсткости. Число прокладок по высоте не должно превышать пяти, включая тонколистовые, применяемые для окончательной выверки. После подливки рамы бетоном и затвердевания его до проектной прочности выполняют затяжку болтов. Окончательная центровка насоса производится с помощью прокладок, помещённых между опорной поверхностью рамы и лапами двигателя. Установка прокладок под опорные поверхности гидромуфт и редукторов, а также под опорные поверхности насоса в агрегатах без гидромуфт и редукторов не разрешается и допускается только при наличии указаний завода-изготовителя. Плотность прилегания поверхностей прокладок друг к другу, а также к опорным поверхностям фундаментных рам (плит) и